What is Calcination?
Rotary Calciners (Kilns) Various types of equipment are available for carrying out the calcining process, with rotary kilns being one of the most commonly employed types. Calcination can be carried out in either a direct-fired or indirect-fired rotary kiln, both often referred to as calciners in this setting. Direct-Fired Rotary Calciners
اقرأ أكثر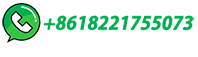
Fundamentals of Cement Chemistry, Operations, and Quality …
This chapter provides relevant understanding and inputs on different aspects related to subjects such as cement chemistry, laboratory evaluations, thermal energy, and kiln operational aspects. ... These raw materials are mixed in certain proportions and burnt at 1400 to 1450 °C in a rotary kiln to form a clinker which is subsequently ground to ...
اقرأ أكثر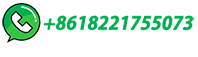
Advanced Process Control for Clinker Rotary Kiln and Grate …
The cement industry includes energy-intensive processes, e.g., clinker rotary kilns and clinker grate coolers. Clinker is obtained through chemical and physical reactions in a rotary kiln from raw meal; these reactions also involve combustion processes. The grate cooler is located downstream of the clinker rotary kiln with the purpose of suitably cooling the clinker. …
اقرأ أكثر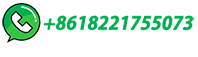
Manufacturing
The original rotary cement kilns were called 'wet process' kilns. In their basic form they were relatively simple compared with modern developments. The raw meal was supplied at ambient temperature in the form of a slurry. A wet process kiln may be up to 200m long and 6m in diameter. It has to be long because a lot …
اقرأ أكثر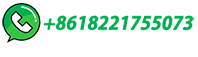
Clinkerization
Rotary kiln is a rotating cylinder, installed at an inclination of 3.5 to 4 % to facilitate material movement. Length and diameter of kiln is decided for the required capacity throughput. Main factors dictating size of kiln are the retention time (25-30 minutes) ...
اقرأ أكثر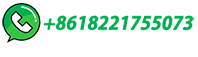
The Role and Importance of Rotary Kilns in Industrial …
Rotary kilns are essential devices in a variety of industrial processes, playing a crucial role in the thermal treatment of raw materials. These cylindrical, rotating vessels are used to heat solids to high temperatures, …
اقرأ أكثر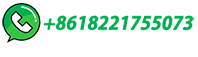
An Efficient Numerical Model for Fast Simulation of the …
This work proposes a one-dimensional numerical model of a cement production rotary kiln using combustion data of petroleum coke and Refused Derived Fuels from previously performed Computational Fluid Dynamics simulations, coupled with a black-box cyclone tower model. A 64 m long rotary kiln is discretized into one-dimensional slices in which both clinker …
اقرأ أكثر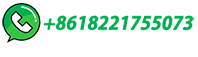
Experimental And Economic Comparison Of Fuels Used In …
Rotary kilns can have certain lengths according to the material to be sintered. After this process, the waste heat goes to the boiler. After the processes carried out here, it is released into the atmosphere at flue gas ... They are used in many areas such as ceramics, chemistry and mining in the industry [1]. Sintering process in rotary kilns ...
اقرأ أكثر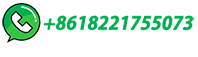
How Do Rotary Kilns Work? A Complete Guide To …
A rotary kiln is a cylindrical vessel, slightly inclined from the horizontal, that rotates slowly around its longitudinal axis. The inclination allows materials to move downward as the kiln rotates, ensuring continuous processing.
اقرأ أكثر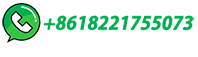
Rotary Kilns: Frequently Asked Questions (FAQs)
The rotary kiln is an advanced thermal processing device used in an extensive number of applications, with new uses constantly being developed.. As a cornerstone technique in engineering the raw materials and products our constantly evolving society depends on, the advanced thermal processing carried out in rotary kilns is an integral component of modern …
اقرأ أكثر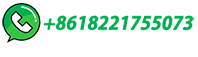
What is Rotary Kiln Refractory?
The cement-like mixture is then pumped into the rotary kiln lining and is cured for several days. ... In general, the refractory selection is dependent on the kiln temperature, material chemistry, and how abrasive the material is. For more information on refractory, download our e-book, or contact a FEECO expert today! About the Author . . .
اقرأ أكثر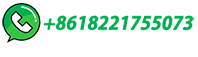
Deep Learning Techniques for Enhanced Flame Monitoring in Cement Rotary
The experiments were carried out on a rotary kiln installed in the Maceira-Liz (Portugal) cement production plant of the cement producer SECIL. Figure 4 shows the scheme of a rotary kiln for cement production, similar to the kiln where the experiments were conducted. During the cement production process, the raw material is introduced into a ...
اقرأ أكثر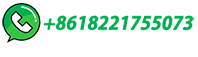
Rotary kiln | PDF
4. 4 The history of the rotary kiln: About 1900, various metallurgists were experimenting with the rotary kiln for nodulizing flue-dust, fine iron ores, etc. Edison conducted experiments, for example, on the fine concentrates obtained from his magnetic separators. Within a few years plants were established for this purpose. The rotary kiln also furnished a simple …
اقرأ أكثر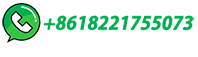
EVERYTHING YOU NEED TO KNOW ABOUT REACTIONS ZONES IN THE ROTARY KILN
THE SEMIDRY (LEPOL) KILN. The drying, the dissociation of the chemical water, the preheating to calcining temperature, and even partial calcination in this system takes place outside the rotary kiln, i.e, in the grate preheater.Hence, the rotary kiln proper has only to complete the calcination and form the clinker com· pounds. The length of the zones in the Lepol kiln are thus quite …
اقرأ أكثر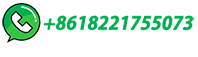
Material and energy flows in rotary kiln-electric furnace smelting of
The rotary kiln-electric furnace process is the one of the most widely adopted technological process for ferronickel smelting production. A schematic of the RKEF process with rotary dryer, rotary kiln and electric furnace is shown in Fig. 1. As depicted, the RKFF process involves three main processes: the dehydration process in rotary dryer ...
اقرأ أكثر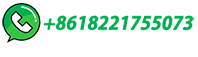
Mean residence time and hold-up of solids in rotary kilns
The influence of operational variables on the mean residence time (MRT) and hold-up of the solids in rotary kilns has been investigated by many researchers. However, their reports on the influence of the feed rate on MRT, for example, are not consistent with one another. In this study, experiments are conducted on a 400 mm ID pilot kiln with a cylindrical discharge dam. Sand is …
اقرأ أكثر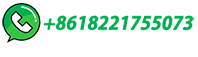
Everything you need to know about Cement Kiln Dust …
To prevent or limit operational problems, insufflation methods that use an oxygen-enriched air stream to recycle dust to the rotary kilns have been developed. Mayotte and Eleazer (1991) suggested increasing the oxygen concentration in …
اقرأ أكثر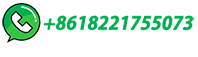
Rotary kiln process: An overview of physical mechanisms, models and applications
Rotary Kiln
A rotary kiln is a physically large process unit used in cement production where limestone is decomposed into calcium oxide which forms the basis of cement clinker particles under high …
اقرأ أكثر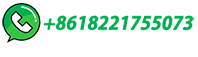
Rotary Kiln Construction | PPT
4. While rotary kilns are engineered around the material to be processed in order to yield optimal processing conditions, the basis of a rotary kiln can be somewhat standard. The following information offers an explanation on some of the standard components of a rotary kiln, as well as available customizations.
اقرأ أكثر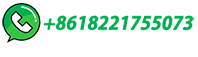
rotary kiln meaning in chemistry
Rotary kiln definition and meaning Collins English . In rolling through the rotary kiln the edges of the limestone particles are rounded off. The rotary kiln is a sloping and rotating tube into which the material enters and flows counter to the hot gases produced by a flame at the lower end. A rotary kiln is a kiln in which a sloping cylinder ...
اقرأ أكثر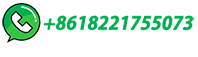
Rotary Kiln | Design, Cement & Lime Manufacturing
A rotary kiln is a crucial component used in the production of cement and lime, serving as the heart of cement manufacturing plants and lime kilns. This cylindrical vessel slowly rotates on its axis and plays a key role in the chemical processes involved. The design and operational characteristics of rotary kilns directly influence the quality ...
اقرأ أكثر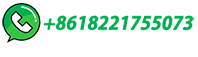
What is a Rotary Kiln?
A rotary kiln is a device that supplies tremendous amounts of heat in order to change the chemical composition of an object.
اقرأ أكثر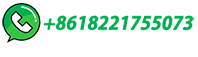
Operating Key Factor Analysis of a Rotary Kiln Using a
The global smelting business of nickel using rotary kilns and electric furnaces is expanding due to the growth of the secondary battery market. Efficient operation of electric furnaces requires consistent calcine temperature in rotary kilns. Direct measurement of calcine temperature in rotary kilns presents challenges due to inaccuracies and operational limitations, …
اقرأ أكثر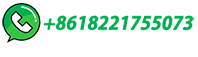
Manufacturing
However, new cement kilns are of the 'dry process' type. Dry process kilns. In a modern works, the blended raw material enters the kiln via the pre-heater tower. Here, hot gases from the kiln, and probably the cooled clinker at the far end of …
اقرأ أكثر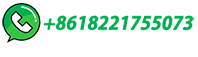
Modeling of cement clinker production in a rotary kiln …
Cement clinker is produced in rotary kilns operating at high temperature. The harsh internal conditions in the kiln prevent direct measurements of key process variables. Digital twins that use mathematical models to mimic and emulate the process in real time are viable alternatives to track equipment performance and product quality. Building on the past …
اقرأ أكثر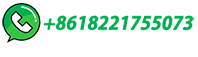
Rotary Kilns: Working Principles & History
A rotary kiln is a lengthy cylindrical structure that rotates around its axis while processing various materials. Commonly used in the manufacturing industry, it plays a pivotal …
اقرأ أكثر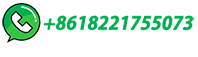
Rotary Kiln Meaning In Chemistry
A simple step-change method to determine mean residence time in rotary kiln and a predictive model at low inclination. ... Chemistry. 2013; Rotary calcination is widely used in catalyst manufacturing and many other …
اقرأ أكثر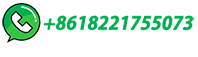
Rotary Kilns: Working Principles & History
Functionality of Rotary Kilns. Rotary kilns serve a significant role in processing raw materials into final products. Here's how they function: Rotation: The shell's rotation enables the material to tumble and mix, promoting even heating. Temperature Control: Temperatures in the rotary kiln can reach extraordinarily high levels, necessary for initiating chemical reactions or …
اقرأ أكثر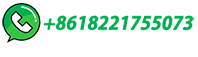
Novel method for temperature prediction in rotary kiln process …
Given the predominantly symmetrical nature of the rotary kiln's surface, this study focused on a symmetrically subdivided grid configuration of around 20,000 in the calculation domain, leading to a significant reduction in grid quantity and enhancement in calculation precision and speed. The maximum density of acquired information was 0.03m.
اقرأ أكثر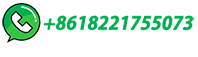
EFFECT OF SPEED AND SKEWING ANGLE IN CONTROLLING AXIAL THRUST OF ROTARY
Presently rotary kilns particularly in our country which have axial lengths up to 66m are given nearly from 3 to 3.5% inclination with the combination of rotational motion of kiln to allow material flowing out in one direction. The rotary kiln consists of …
اقرأ أكثر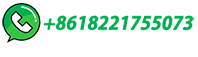