Recent Trends in the Technologies of the Direct Reduction and …
The blast furnace and direct reduction processes have been the major iron production routes for various iron ores (i.e. goethite, hematite, magnetite, maghemite, siderite, etc.) in the past few decades, but the challenges of maintaining the iron and steel-making processes are enormous. The challenges, such as cumbersome production routes, scarcity of …
اقرأ أكثر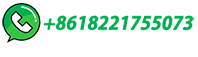
(PDF) Sticking and Swelling of Iron Ore Pellets: Mechanisms and
The sticking and breakage of iron ore pellets during high-temperature reduction pose significant challenges in shaft furnace ironmaking. As the steel industry transitions towards …
اقرأ أكثر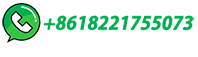
Influence of Mixing Coal Composite Iron Ore Hot Briquettes …
Blast Furnace Simulated Reaction Behavior in a Packed Mixed Bed Hiroyuki MIZOGUCHI,1) Hironori SUZUKI1) ... Chemical composition of iron ore mini pellet (mass%). Chemical composition of pellet T.Fe FeO CaO SiO2 Al2O3 MgO S P 66.23 0.07 1.57 1.56 0.75 0.85 0.007 0.047 Fig. 1. Experimental apparatus.
اقرأ أكثر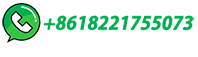
Cold compressive strength of iron ore pellets in distinct reduction
The experiments were performed for commercial acid iron ore pellets with basicity B2 of 0.10 (ratio of CaO and SiO 2). Pellets can be considered acid when B2 basicity is below 0.5 [8]. Niiniskorpi [21] has reported that the magnetic cores inside iron ore pellets vary in size. In order to improve the uniformity of the examined sample batch, the ...
اقرأ أكثر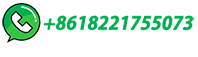
A New Approach of Pelletizing: Use of Low-Grade Ore as a
The mechanical strength of mixed pellets during reduction suggests their potential to withstand the stack layer in blast furnace operations. These findings could suggest the …
اقرأ أكثر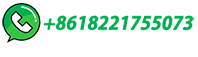
Effect of adding limestone on the metallurgical properties of iron ore
The reducibility test in CO–CO 2 –N 2 gas showed that limestone enhances the reduction reactions in the acid iron ore pellets. One reason for this is the higher porosity of the fluxed pellets compared to the non-fluxed ones. ... Iron Ore Pellets for Blast Furnace and Direct Reduction Feedstocks. Determination of the Crushing Strength. ISO ...
اقرأ أكثر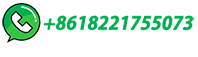
Iron Ore Pelletizing Process: An Overview
In the blast furnace, iron is reduced and melted and the most common ... melting, chemical reaction, hardening binders, recrystallization of ... The final use of iron ore pellets in ironmaking ...
اقرأ أكثر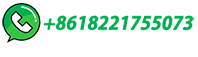
Multiscale modeling of non-catalytic gas-solid reactions applied to …
Incorporating the shift reaction improved the model's agreement with data obtained from a pilot plant scale reactor. Alamsari et al. [25] expanded the scope of reactions involved by incorporating the steam reforming reaction into the reduction of iron ore pellets and simulating the shaft furnace cooling zone.
اقرأ أكثر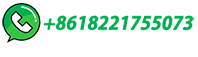
Formulating iron ore pellet induration process in an industrial
Iron ore pellets play an important role as a feedstock to the blast furnace in hot metal production as they improve the blast furnace productivity and decrease the fuel consumption rate [1], [2].For producing the pellets, there is typically a three-stage mechanism involved: blend preparation, formation of green pellets, and finally heat hardening of those …
اقرأ أكثر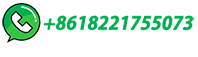
(PDF) Sticking and Swelling of Iron Ore Pellets: Mechanisms and
The sticking and breakage of iron ore pellets during high-temperature reduction pose significant challenges in shaft furnace ironmaking. As the steel industry transitions towards decarbonization ...
اقرأ أكثر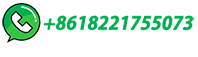
Iron Ore Pellets
Iron Ore Pellets. satyendra; December 28, 2013; ... Maximum allowable swelling of pellets for the blast furnace ranges from 16 % to 18 %. Acid pellets (DRI pellets) and MgO free pellets exhibit higher swelling. ... (MgO.Fe2O3) by solid state reaction at temperature which is higher than 700 deg C. In the dolomite fluxed pellets, after ...
اقرأ أكثر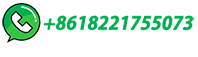
Isothermal reduction kinetics and reduction prediction for iron ore pellets
Iron ore pellets, as one of the main charges of blast furnaces, have a greater impact on the CO2 emission reduction and stable operation of blast furnaces. The isothermal reduction behavior of the pellets obtained from a Chinese steel plant was studied in the gas mixtures of CO and N2. The results showed the reduction process is divided into two stages. …
اقرأ أكثر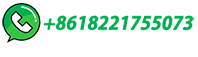
Hydrogen reduction of iron ore pellets: A surface study using …
Macroscopic investigations offer insights into transport phenomena and reaction kinetics within shaft furnaces, while the mesoscopic scale is apt for exploring the structural evolution of iron ore pellets during the reduction process. However, it is at the microscopic scale that we gain access to invaluable information pertaining to crystal ...
اقرأ أكثر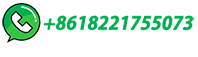
OneTunnel | Understanding Reactions in Iron Ore Pellets
The induration furnace for iron ore pellets was originally designed to process concentrates with high contents of magnetite. To support the use of haematite concentrates, …
اقرأ أكثر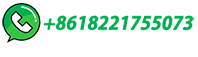
A comparative study of pellets, sinter and mixed ferrous burden
Raw materials. Commercially supplied iron ore pellets and sinter of size range 10–13 mm are utilised in the present study. Comparable to the utilisation in the industrial blast furnace, two types of olivine fluxed pellets (types 1 and 2) and one type of iron ore sinter are mixed in 40:20:40 ratio to form a ferrous raw material bed.
اقرأ أكثر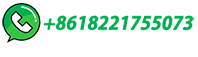
Review on Reduction Kinetics of Iron Ore–Coal Composite Pellet …
The use of iron ore–coal composite pellet as a raw material for iron making is an ongoing area of research. ... (11.44 × 10 –3 s −1), E r is the activation energy for the reduction reaction of iron ore by CO (33 kJ/mol), f is the degree of ... Ripke J (2008) Rotary hearth furnace technologies for iron ore and recycling applications. Arch ...
اقرأ أكثر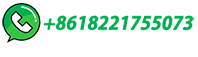
Experimental and numerical investigation of iron ore pellet firing
Iron ore pellets are the main feedstock in ironmaking processes. While extensive research has addressed numerical modeling of the iron ore pellet induration process, little effort has been made to describe the intricate thermochemical processes occurring within the reactor starting from the pellet and particularly at the intra-particle scale.
اقرأ أكثر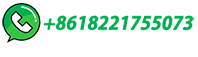
Iron Ore Pelletizing Process: An Overview
In the blast furnace, iron is reduced and melted and the most common product is liquid iron called hot metal. In direct reduction, iron …
اقرأ أكثر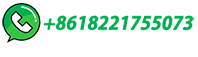
Optimization of the Iron Ore Direct Reduction Process through
Evolution of pellet structure along with reaction: (a) Unreacted Shrinking Core Model; (b) Grain Model.The porous structure evolution (b) was determined from experimental observations [].3. Shaft Furnace Model 3.1. Previous Works. The shaft furnace is the core of the DR process.Iron ore pellets are charged at the top, descend due to gravity, and encounter an upward counter …
اقرأ أكثر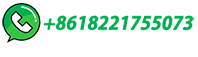
A Comparison Between the Reduction Behavior of DRI and BF …
The reduction behavior of two different iron ore pellets that are used in blast furnace (BF) and direct reduction (DRI) was investigated in this research. Single pellets …
اقرأ أكثر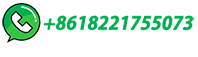
Iron Ore Reactions and Phenomena in a Blast …
While descending, the ferrous burden materials encounter different kinds of reactions and phenomena inside the blast furnace, including reduction reactions, softening and melting, disintegration as well as pellet swelling and cracking.
اقرأ أكثر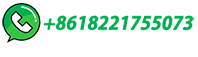
Understanding reactions in iron ore pellets
Understanding Reactions in Iron Ore Pellets
The induration furnace for iron ore pellets was originally designed to process concentrates with high contents of magnetite. To support the use of haematite concentrates, internal fuel was …
اقرأ أكثر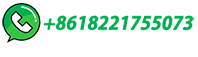
Ore Pellet
Describes the iron ore burden materials charged to the blast furnace (BF): lump ore, sinter, and pellets. 2. Gives an overview of the iron ore minerals used and the related processing techniques. 3. Compares the physical and chemical properties of the iron ore charge materials, as well as their impact on the BF operation. 4.
اقرأ أكثر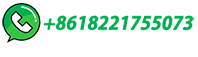
A techno-economic approach for magnetising roasting of iron ore
Microwave-assisted magnetisation roasting is widely recognised as the most effective technology for iron recovery from low-grade iron ore, as reported by [[11], [12], [13], [14]]].A comparative study between microwave and conventional magnetising roasting has become increasingly important in recent years due to the superiority of microwave-assisted …
اقرأ أكثر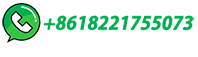
Iron Ore Pellet
The Direct Reduction of Iron. Thomas Battle, ... James McClelland, in Treatise on Process Metallurgy: Industrial Processes, 2014. 1.2.2.2 Agglomeration of Iron Ore. The three major forms of iron used in ironmaking are pellets, lump, and sinter. The major change in the past 50 years has been the development of cost-effective pelletization technology allowing pellets to be a …
اقرأ أكثر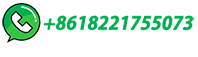
Results of Hydrogen Reduction of Iron Ore Pellets at …
degree of reduction of iron ore pellets is controlled by tempera-ture, reducing gas composition, pellet porosity, iron oxide grain size, and gangue content in iron ore pellets. These parameters canaffect the reduction rateofpellets and have been investigated by many researchers. El-Geassy et al.[25] investigated the impact
اقرأ أكثر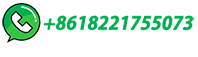
Numerical investigation on hydrogen reduction of iron oxide pellets …
Szekely et al. [11] were among the first who carried out multi-scale modeling of the direct reduction process in a shaft furnace (arrangement) using carbon monoxide-hydrogen mixture as the feed gas.In their pioneering work, the reduction behavior of a single iron oxide pellet was characterized based on the unreacted shrinking core model (USCM), while a one …
اقرأ أكثر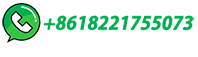
Reduction of Acid Iron Ore Pellets under Simulated …
The operational conditions, including temperature and gas composition, vary along the radial position in a blast furnace. Nevertheless, very few studies can be found in the literature that discuss how the reduction …
اقرأ أكثر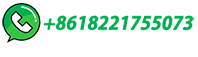
Direct reduction of iron ore pellets by H2-CO mixture: An in-situ
The iron and steel metallurgy industry faces the question of how to replace carbon in iron ore reduction to reduce CO 2 emission in basic industries and achieve the expectation of "double carbon". This study investigates the reduction swelling of individual iron ore pellet under mixed H 2-CO atmospheres and at temperatures of 800–1000 ℃ by in-situ observation.
اقرأ أكثر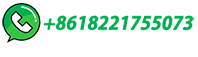
Introduction to Iron ore Pellets and Pelletizing processes
Advantages of pellets. The various advantages of iron ore pellets are given below. Iron ore pellet is a kind of agglomerated fines which has better tumbling index when compared with the iron ore and it can be used as a substitute for the iron ore lumps both in the BF and for DRI production.
اقرأ أكثر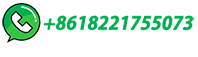