Effect of Iron Ore Pellet Size on its Properties and Microstructure
Schematic diagram of iron ore pelletization process. FZ Wood temp profile Fuel Cooloing zone - 2 Green pellets DDD WB draft FZ draft Cold air flow CZ-2 Outlet gas flow Figure 2. Schematic diagram of the induration process for iron ore pellets (UDD: updraft drying; DDD: downdraft drying). cooling zone 1.
اقرأ أكثر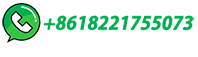
Of Proposal For 2.4 MTPA Pellet Plant Over an Area of …
3.5.1 Process Description- Iron Ore Pellet Plant 17 3.6 Resource Optimization/ Recycling and Reuse 30 . Envisaged in the Project 3.7 Availability of Water Its Source, Energy Power ... Figure 3.5.1 Pellet Plant Process Flow Diagram 18 Fig. No 3.5.2 Pellet Plant Material Flow Diagram 29
اقرأ أكثر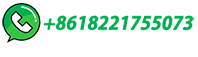
Optimization of the Iron Ore Direct Reduction Process …
Evolution of pellet structure along with reaction: (a) Unreacted Shrinking Core Model; (b) Grain Model.The porous structure evolution (b) was determined from experimental observations [].3. Shaft Furnace Model 3.1. Previous Works. The …
اقرأ أكثر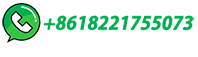
CARBON FORMATION IN DIRECT REDUCED IRON AND …
iii ABSTRACT Carbon formation in the MIDREX© reduction shaft at voestalpine Texas LLC was investigated with computational simulations and physical examination of hot briquetted iron and direct reduced iron.
اقرأ أكثر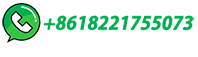
Study of slag formation behavior in iron ore pellets based on
Iron ore pellets can be classified according to their silica content. Pellets with 0%–3% SiO 2 are categorized as low-silica pellets, those with 3%–6% SiO 2 are classified as medium-silica pellets, and those with more than 6 % SiO 2 are classified as high-silica pellets [29, 30].Thermodynamic calculations and experiments laid the foundation for the industrial …
اقرأ أكثر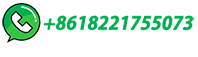
Production of iron ore pellets, process overview to the left, and
This paper summarizes more than a decade of systematic studies of the flow field in an iron ore pelletizing rotary kiln using computational fluid dynamics (CFD) on simplified models of a...
اقرأ أكثر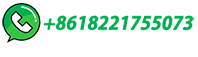
Schematic of typical process flow sheet for magnetite pelletization
Download scientific diagram | Schematic of typical process flow sheet for magnetite pelletization from publication: Investigation of Sintering Kinetics of Magnetite pellets during Induration | One ...
اقرأ أكثر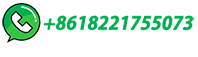
Process flow sheet of pellet making process
The iron and steel manufacturing sector directly accounts for 7–9% of global CO2 emissions. Raw material preparation, such as iron ore sintering, pelletizing, and cock making, is the major CO2 ...
اقرأ أكثر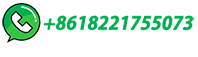
Schematic diagram of the iron ore pelletization process.
The three main pellet types for iron making purposes are: acid pellets (B2 < 0.5); basic or fluxed pellets (0.9 < B2 < 1.3), which use limestone (CaCO 3 ) or dolomite (Ca,Mg(CO 3 ) 2 ) as an ...
اقرأ أكثر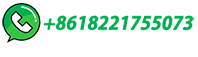
Scheme of gas flow among the pellets distributed in the furnace …
The process for pelletizing iron ore fines is an important operation unit for producing high quality of raw materials for the subsequent reduction processes such as blast furnace or direct reduction.
اقرأ أكثر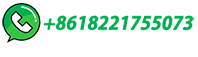
Flow diagram for composite pellet making.
Download scientific diagram | Flow diagram for composite pellet making. from publication: Effects of Binder on the Properties of Iron Ore-Coal Composite Pellets | Large amounts of fines and ...
اقرأ أكثر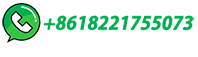
Process flow chart of preparation of pellets | Download Scientific …
The present study deals with the utilization of fines generated from comminution process (crushing, grinding and screening) of the Run of Mines into value added products i.e. fluxed …
اقرأ أكثر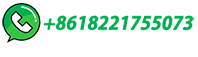
Process flow diagram of pelletization unit
There are two main technologies/processes for producing iron ore pellets: The Grate-Kiln System and the Straight Grate System. The First Grate Kiln System pellet plant was installed in...
اقرأ أكثر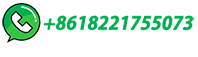
Three-dimensional characterization of porosity in iron ore pellets: …
Iron ore pellets, alongside lump ore and sinter, are fundamental raw materials for steel production, generated through the pelletizing process (Singh et al., 2023). The porosity developed during pellet manufacturing is a critical attribute. It enables internal gas flow, enhancing reducibility and process efficiency (Kim and Sohn, 2023 ...
اقرأ أكثر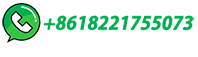
The Deposit Formation Mechanism in Coal-Fired Rotary Kiln for Iron Ore
The deposit-forming problem is one of the main bottlenecks restricting the yield and production benefit of iron ore pellets produced by coal-fired rotary kilns. In order to implement measures to ensure the efficient production of pellets by coal-fired rotary kilns, the mechanism and influencing factors on the deposit formation were reviewed. The pellet powder and coal …
اقرأ أكثر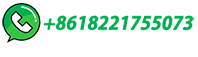
Iron Ore Pelletizing Process: An Overview
Pellets are obtained by adding an appropriate amount of water to the iron ore concentrate; this is a fundamental factor in the formation and …
اقرأ أكثر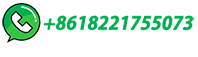
Iron Ore Pelletizing Process: An Overview
The iron ore production has significantly expanded in recent years, owing to increasing steel demands in developing countries. However, the content of iron in ore deposits has deteriorated and low-grade iron ore has been processed. The fines resulting from the concentration process must be agglomerated for use in iron and steelmaking. This chapter …
اقرأ أكثر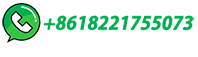
A Comparison Between the Reduction Behavior of DRI and BF Pellets …
The reduction behavior of two different iron ore pellets that are used in blast furnace (BF) and direct reduction (DRI) was investigated in this research. Single pellets reduction experiments were conducted isothermally using pure CO and H2 as reducing agent in the temperature range 700 °C to 1100 °C. Reduction by H2 was significantly faster than reduction …
اقرأ أكثر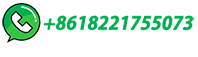
What is Iron Ore Pelletizing? How It Worked? An In …
Iron ore pelletizing is an essential industrial process that transforms powdery iron ore into uniform, robust pellets, serving as a premium feedstock for blast furnaces and direct reduction reactors.
اقرأ أكثر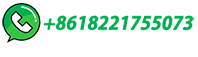
Understanding Pellets and Pellet Plant Operations
Iron ore pellets. The iron ore pellets may be acid or basic pellets. Acid pellets are also called as DRI (direct reduced iron) grade pellets while basic pellets are also known as BF grade or fluxed pellets. ... In any case, …
اقرأ أكثر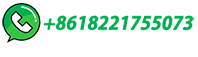
What Are Iron Ore Pellets and How to Make Them?
Iron ore pellets are spheres of typically 8-16 mm to be used as feedstock for blast furnaces. They contain 64-72% iron and additional materials, which can adjust the chemical composition and metallurgical properties of the …
اقرأ أكثر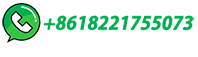
Flow diagram of iron ore sintering process [13]
Download scientific diagram | Flow diagram of iron ore sintering process [13] from publication: The use of ammonium sulfate as an inhibitor of dioxin synthesis in iron ore sintering process | The ...
اقرأ أكثر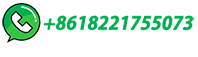
Effect of adding limestone on the metallurgical properties of iron ore
Acid iron ore pellets with 4.6 ... as can be seen in the CaO–FeO n phase diagram in contact with iron (Verein Deutscher Eisenhüttenleute, 1981). ... Metallic iron whisker formation and growth during iron oxide reduction: K 2 O effect. Ironmak. Steelmak., 36 …
اقرأ أكثر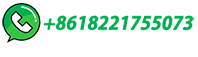
iron ore pellet plant flow diagram – Grinding Mill China
Flow chart of iron pellet plant grates kiln technology …. Flow chart of iron pellet plant grates kiln technology. Gulin supply Mining and construction equipment for mineral handling. The crushing, screening, washing … » Free Online Chat Iron ore processing plant equipment in iron ore …. Iron ore processing plant works the initial … From the iron ore processing flow chart picture ...
اقرأ أكثر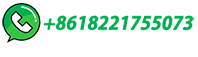
Reduction of Iron Ore Pellets: A Microstructural Perspective?
Twenty different iron ore pellets, consisting primarily of Hematite (Fe2O3) phase, were subjected to 'simulated' reduction studies. A wide range of reduction time periods, Rt of 122 to 211 minutes, were obtained. Detailed microstructural characterizations were then conducted at different locations of ten selected specimens. The Rt did not relate with initial phase mix or …
اقرأ أكثر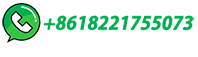
Direct Reduced Iron and its Production Processes – IspatGuru
The reductant can be a gas or a solid. Major DRI production processes are either natural gas based or coal based. Feed material for the DR process is either sized iron ore of size ranging from 10 mm to 30 mm or iron ore pellets of size ranging from 8 mm to 20 mm produced in an iron ore pellet plant.
اقرأ أكثر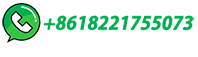
Exploring the effects of biomass utilization on the metallurgical
The adoption of a high proportion of pellet charging in the blast furnace smelting process can significantly enhance furnace operations, reduce fuel ratios, and lower energy consumption in ironmaking [1], [2].The annual production energy consumption of the pelletizing process is approximately half that of the sintering process, thereby resulting in considerably …
اقرأ أكثر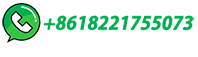
Iron Ore Pellets
The term iron ore pellet refers to he thermally agglomerated material formed by heating a variable mixture of iron ore, limestone, olivine, bentonite, dolomite, and miscellaneous iron bearing materials in the range of 1,250 deg C to 1,350 deg C. Iron ore pellets can be made from beneficiated or run of mine iron ore fines.
اقرأ أكثر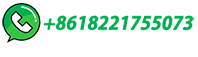
Inhibiting the Accretion in the Coal-Fired Rotary Kiln of
The rotary kiln at the iron ore pellet company has a diameter of 6.1 m and length of 40 m. After suspending production, ten samples of deposit formation were collected from the rotary kiln at 4-m intervals. Each sample was taken from a different position around the wall surface of the rotary kiln and labeled as S-1 to S-10.
اقرأ أكثر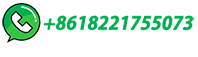