Effect of particle size distribution on sintering of agglomerate-free
In a recent work with near-monosized agglomerate-free submicron alumina compacts, Lim et al. 22 showed that despite being agglomerate-free to start with, agglomeration of particles still occurred during sintering due to the local differential densification effect produced by the different co-ordination numbers of individual particles. This led ...
اقرأ أكثر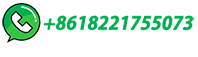
Effects of the number of particles and coordination number on …
These findings describe the configurational state of agglomerates, typical of mesoscale caking. In a multi-scale study, they can be used to characterize caking at a bulk …
اقرأ أكثر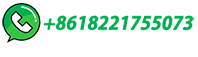
Factors influencing particle agglomeration during solid-state sintering
Discrete element method (DEM) is used to study the factors affecting agglomeration in three-dimensional copper particle systems during solid-state sintering. A new parameter is proposed to characterize agglomeration. The effects of a series of factors are studied, including particle size, size distribution, inter-particle tangential viscosity, temperature, …
اقرأ أكثر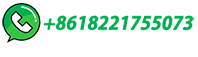
Agglomerate and Particle Size Effects on Sintering …
The initial-, intermediate-, and final-stage sintering of fine crystallite yttria-stabilized zirconia was studied. Experiments were conducted on powder lots of differing agglomerate size and one specially prepared agglomerate-free powder. Initial-stage sintering kinetics were compared with a sintering study on larger crystallite size calcia-stabilized zirconia to access the Herring scaling …
اقرأ أكثر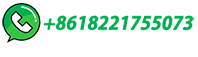
Iron Ore Agglomeration Technologies
Five iron ore agglomeration technologies can be defined: briquetting, nodulization, extrusion, pelletization and sintering.
اقرأ أكثر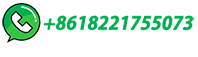
Characterizing Particle Size and Monitoring Agglomeration
This is because tiny particles with a high surface area and molecular gravity are more likely to agglomerate than coarse particles. Furthermore, agglomeration affects sintering efficiency and raises the likelihood of ceramic component failure. ... Sintering rates are greatly influenced by particle size and size distribution. As the sintering ...
اقرأ أكثر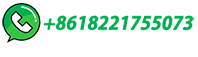
Agglomeration of Iron Ores
Agglomeration of iron ores is the iron ore pretreatment process in which the powdery iron ore that cannot be directly fed into a blast furnace experiences high-temperature solidification by sintering process and pelletizing process or low-temperature solidification by pelletizing process and briquetting process to generate the rich ore material that meets the …
اقرأ أكثر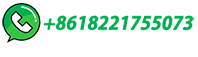
Sinterability of Agglomerated Powders | MRS Online
H.E. Exner, "Principles of Single Phase Sintering," Reviews on Powder Metallurgy and Physical Ceramics 1, (1–4), T.1–251 (1979).. Google Scholar . K. Haberko, "Characteristics and Sintering Behavior of ZrO 2 Ultrafine Powders," Ceramics Int'l. 5, 148 (1979).. CAS Google Scholar . A. Roosen and H. Hausner, "Sintering Kinetics of ZrO 2 Powders," Proc. ZrO 2 Conf., Stuttgart ...
اقرأ أكثر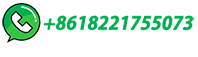
Comparison of Aerosol Pt, Au and Ag Nanoparticles …
Agglomerate sintering is caused by the diffusion flow of matter in a direction that provides minimal surface energy, which can be achieved with a spherical shape . To do this, we used a previously developed laser modification cell, which combined the studied aerosol flow with the optical axis of impacting radiation. In the experiments, the NPs ...
اقرأ أكثر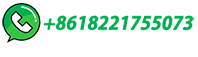
A Novel Preparation of Ag Agglomerates Paste with …
A novel bonding process using Ag agglomerates paste prepared by Ag2O reduction has been proposed, which solved the problem of Cu substrate oxidation in the conventional Ag2O sintering process for Cu–Cu bonding. By …
اقرأ أكثر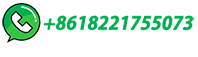
Modernization of the Drum Cooler for Returning Agglomerate OV …
The quality of iron ore agglomerate largely determines the performance of a blast furnace and is one of the main factors in increasing the technical and economic efficiency of the sintering and blast furnace processing stage [1–4].The quality indicators of finished products in agglomeration production depend not only on the characteristics of the charge materials, but …
اقرأ أكثر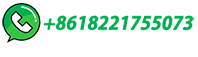
(PDF) A One-Dimensional Model for Coagulation, …
By adding gradual sintering, the growth rate of agglomerate particles by coagulation was slightly decreased and the primary particle size considerably increased compared with the results given by ...
اقرأ أكثر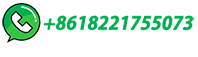
The capacitance and charge of agglomerated nanoparticles during sintering
Figure 6 shows the capacitance evolution of an exemplary agglomerate consisting initially of 128 PPs during viscous flow sintering that is typical of amorphous materials such as polymers and silica. The time t is normalized by the characteristic sintering time τ 0 =ηa 0 /ϒ, with η and ϒ being the particle viscosity and surface energy, respectively, and a 0 the initial PP …
اقرأ أكثر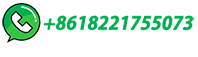
Three-dimensional simulation of viscous-flow agglomerate sintering
The viscous-flow sintering of different agglomerate particle morphologies is studied by three-dimensional computer simulations based on the concept of fractional volume of fluid. …
اقرأ أكثر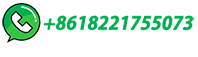
A One-Dimensional Model for Coagulation, Sintering, and …
In these models, the effect of the agglomerate structure on sintering and coagulation rates largely was neglected. Xiong and Pratsinis (1993) developed a 2-D sectional model in which agglomerate volume increased through coagulation, while surface area was assumed to be affected only by
اقرأ أكثر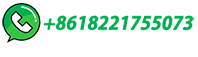
The Sintering Process of Iron Ore Fines – IspatGuru
The sintering process is used to agglomerate a mix of iron ores (blend), return fines, fluxes and coke, with a particle size of less than 10 mm, so that the resulting sinter, with a screened size of 10 mm to 30 mm, can withstand pressure and temperature conditions in the blast furnace. ...
اقرأ أكثر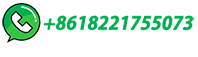
Formation of agglomerate particles by coagulation and …
The characteristic time for coalescence or sintering, ~f, is the time needed to reduce by 63% the excess agglomerate surface area over that of a spherical particle with the same …
اقرأ أكثر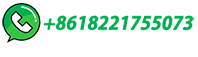
The agglomeration, coalescence and sliding of nanoparticles …
Here we show how the ordered agglomeration of zirconia primary crystallites into secondary particle assemblies ensures their homogeneous packing, while also preserving the high …
اقرأ أكثر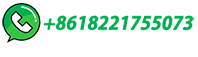
A Review of the Terms Agglomerate and Aggregate with a …
Agglomerate = assemblage of particles rigidly joined together, as by partial fusion (sintering) or by growing together. Aggregate = assemblage of particles which are loosely coherent. In 1966, Gerstner 3 defined assemblages of pigment particles as follows:
اقرأ أكثر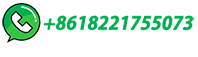
What is Agglomeration? Glossary of Powder Mixing Technology …
Sintering, also known as fritting, is a thermal agglomeration process in which atoms diffuse within materials. Powder masses are first shaped so that there is minimal cohesion between the …
اقرأ أكثر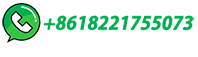
Agglomeration of powders : overview of mechanisms …
Sintering; Each of this technology is actually playing on a different mechanism to ensure that solid particles form an agglomerate solid enough to meet the target product properties. 2. Agglomeration binding mechanisms
اقرأ أكثر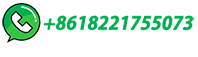
Formation of agglomerate particles by coagulation and sintering—Part …
Formation of agglomerate particles--Part I 285 Part I of this two-part paper series describes the theoretical formulation and numerical implementation of the two-dimensional particle size distribution model and its basic features. ... ( Sk.T+8k.T~1/2 )u2 fl=4 ~ml 7tm2 / [(stal +(s2a2)U2]2 . (8) The sintering contribution in equation (l) is ...
اقرأ أكثر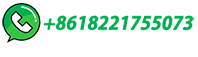
Sintering and agglomeration characteristics of industrially …
And with the intensification of particle sintering and uneven gas distribution, the newly established agglomerate layer became more compact, and the agglomerate layer …
اقرأ أكثر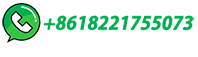
Study of the mobility, surface area, and sintering behavior of
By assuming that the proportionality between mobility diameter and surface area remained constant during agglomerate sintering, sintering behavior was determined for various temperatures and times. Predictions by the model of Koch & Friedlander ( 1990 ) and a geometric sintering model showed reasonable agreement to the data.
اقرأ أكثر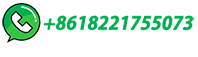
Formation of agglomerate particles by coagulation and sintering…
Formation of agglomerate particles by coagulation and sintering—Part II. The evolution of the morphology of aerosol-made titania, silica and silica-doped titania powders. ... Fast sintering results in low degrees of aggregation and consequently large primary particle sizes in the aggregates. The coales- cence rate is determined by process ...
اقرأ أكثر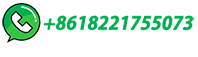
Polydispersity of primary particles in agglomerates made by …
By relating the rate of sintering to each individual PP size, the new model accounts for physical narrowing of the PPSD during hard-agglomerate formation that is caused by the faster sintering of the smaller than the larger PPs. Sintering kinetics of initially monodisperse and polydisperse titania powders have been validated and compared ...
اقرأ أكثر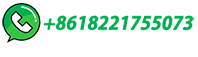
CFD-DEM investigation on the agglomeration behavior of micron …
Fig. 13 shows the normalized maximum agglomerate size vs. time. Note that the agglomerate size is normalized by the total number of particles in the bed system. As can be seen from the figure, the defluidization occurs rapidly in less than 0.1s after activating the sintering force when u g = 0 . 12 m/s .
اقرأ أكثر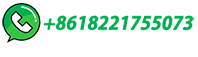
Effect of particle size in aggregated and agglomerated ceramic powders
A certain amount of aggregation is useful to enhance the flowability of the powder, which is inherently poor for fine particles. However, the agglomerate and aggregate length scales should be eliminated during further processing to ensure …
اقرأ أكثر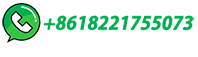
Aggregate Morphology Evolution by Sintering: Number
Here, aggregate sintering by viscous flow of amorphous materials (silica, polymers) and grain boundary diffusion of crystalline ceramics (titania, alumina) or metals (Ni, Fe, Ag etc.) is …
اقرأ أكثر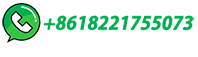
Sintering Temperature
For the non-agglomerated (N/A) powder, sintering time is 120 min; 69 for the 80 and 340 nm agglomerate powders, sintering time is 30 min. 70,71 In essence, a powder compact can be viewed as consisting of a bi-level hierarchical structure: the compact is made of agglomerates which consist of nanosized particles.
اقرأ أكثر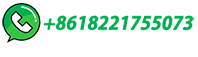