Ultimate Guide To Ore Washing
Ore washing is the process of by the use of water or mechanical force to agitate and scrub raw ore, wash and separate the clay from ore. The alluvial ore deposits ( like gold, platinum, tungsten, tin ) and other minerals such as lead, copper, iron and manganese which are deeply oxidized and weathered, usually …
اقرأ أكثر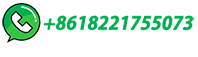
The six main steps of iron ore processing
When iron ore is extracted from a mine, it must undergo several processing stages. Six steps to process iron ore. 1. Screening We recommend that you begin by screening the iron ore to separate fine particles below the crusher's CSS …
اقرأ أكثر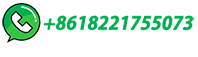
Overview of Ore Washing in the Mineral Processing …
Ore washing is used to process clay iron ore, manganese ore, apatite ore, and placer of gold, platinum, tin and tungsten. Ore washing is also used to process sand, gravel and ceramic materials for construction. ... If you …
اقرأ أكثر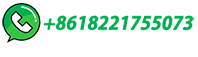
Log Washer | Through Ore Washing Machine
Log washer or trough washing machine is a kind of ore washing equipment widely used in various large pieces of easy-to-wash and hard-to-wash clay, mud or soft ore/stone. Such include washing and separating mud in ferrous and non-ferrous metal mines, construction, sand and gravel, stone plants, etc. We can provide single/double shaft log washers, which are especially effective for …
اقرأ أكثر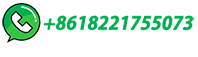
Characterization and Beneficiation of Dry Iron Ore …
Current industrial practice of processing of iron ore fines in India does not involve much beneficiation. However, few plants in India are treating fines during washing, classification, and jigging process [4]. In other parts of the world, iron ore fines are beneficiated for magnetite- and hematite-rich iron ore in * P. Dixit prashant.dixit ...
اقرأ أكثر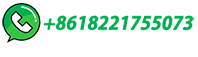
PLC (S7-400) CONTROLLED IRON ORE WASHERY
washing processes, but the most common process involves crushing the iron ore, followed by screening and washing. PLC-based iron ore washing systems are automated systems that use a programmable logic controller (PLC) to control the various processes involved in iron ore washing. The Iron Ore Washery System is a sophisticated and integral part ...
اقرأ أكثر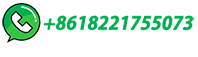
China Iron Ore Washing Plant
Iron Ore Washing Plant is widely used to combine with the ball grinder in a closed circulation for ore-sand separation in the ore separation plant., classify ore sand and fine silt in the gravity separation plant, classify the granularity from the pulp in the metal ore beneficiation flow and remove the slime and water in the ore washing process.
اقرأ أكثر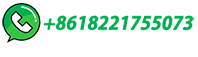
Iron Ore Processing Solution
Introduce how to crush iorn, whole iron ore crushing plant flow & layout (with photo), and related rock crusher machine. Contact us to do free flow design.
اقرأ أكثر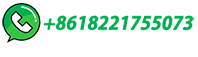
Simec Mining 950tph Iron Ore Beneficiation Wash Plant
Alumina levels range from 5.9% to 8.8% and are reduced to 2.8% after processing. The iron ore wash plant also removes clays from the feed material and the combined effect means the Fe content increases from between 43.4% and 52.7% in the feed to above 60% iron ore product, with a yield of up to 50%.
اقرأ أكثر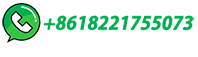
Iron ore washing process and equipment | LZZG
In the iron ore washing industry, if you want to get the ideal grade of ore, equipment is very critical. The crushing process of iron ore washing plant generally uses …
اقرأ أكثر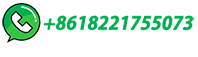
TIN ORE PROCESSING PLANT
Alluvial tin ore is separated by the gravity separation method.. For alluvial tin ore with a high degree of monomer dissociation, the final concentrate is obtained by the 6-S shaker tables at one time.The concentrate grade is above 60%. For alluvial tin ore with a low monomer dissociation degree, use a jig machine for primary selection, then concentrate enters 6-s shaking tables for …
اقرأ أكثر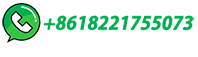
Advances in screening technology in the mining sector
Fig. 8 shows a modern processing plant flow diagram for hematite ore. ... mm). The fraction < 1 mm passes through another washing stage. Processing plants such as those of Roy Hill are characterized by a high number of screening devices. In fact, 16 banana screens are used in that plant alone. Fig. 9 shows a 40 Mta iron ore processing plant ...
اقرأ أكثر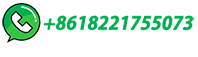
iron ore washing plant flow chart – stone cruxder
In this article, we'll explore what iron ore is, delve into the intricacies of its washing process, highlight its numerous advantages, and provide you with a comprehensive flow chart for better …
اقرأ أكثر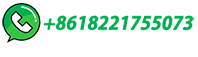
Copper Ore Processing Plants, Flow And Equipment
Copper industrial minerals include: natural copper, chalcopyrite, chalcocite, tetrahedrite, azurite, malachite, etc. Chalcopyrite (a compound of copper, sulfur, and iron) is mined mainly, followed by chalcocite and bornite. If copper ore wants to be fully utilized, it must be processed by flotation. Flotation separation is an important copper ore beneficiation process in …
اقرأ أكثر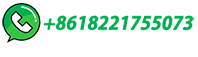
Physical separation of iron ore: magnetic separation
However, magnetic columns are used in this flow sheet instead of drum LIMS for the final cleaning stage to target a higher iron grade for the concentrate. The annualized plant results demonstrated that an iron ore concentrate containing 68.4% Fe could be produced using this flow sheet from run-of-mine ore containing 29.1% Fe, at a mass yield of ...
اقرأ أكثر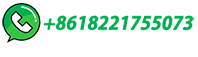
Iron Mining Process | Equipment | Flow | Cases
150TPH Iron Ore Processing Plant in Malaysia. Material: hard rock type iron ore Capacity: 150TPH Country: Malaysia Feeding size: 0-400mm Raw mineral description: 1. Weak magnetic iron 2. Contains slime 3. Need crushing – washing – magnetic separation flow. Customers requirements: 1. The particle size of finished products requires 0-10mm 2 ...
اقرأ أكثر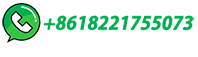
A critical review on metallurgical recovery of iron from iron ore
Fig. 2 illustrates the iron ore beneficiation process, particularly magnetic separation, resulting in the generation of inevitable tailings. Due to the characteristics of iron ores and the conditions during beneficiation, it is inevitable that approximately 2.5–3 tons of IOTs are generated for every 1 ton of iron ore concentrate produced [7].In 2019, the global annual …
اقرأ أكثر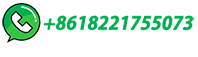
Iron Ore production in the Pilbara
Activities involved in finding, mining and processing iron ore at our Pilbara operations have been simplified in the following diagram. Rio Tinto operates 11 iron ore mines in the Pilbara and the specific sequence of activities varies from mine to mine. Excellence in planning, scheduling and quality control are fundamental to the process.
اقرأ أكثر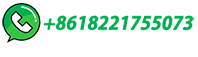
Flow diagram of iron ore sintering process [13]
Until the 1950s of the last century, the oxidized iron ores that were loaded into the blast furnace had granulometries within 10 and 120 mm. However, the depletion of high-grade iron ore sources ...
اقرأ أكثر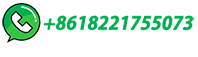
100TPH Alluvial Chrome Wash Process Plant In Zimbabwe
The raw ore also contains magnetite, so the iron content needs to be reduced to increase the chrome concentrate ratio; ... JXSC professional engineers customized a complete set of 100TPH alluvial chrome wash process plants, flow charts, equipment, and accessories for this project. It mainly includes feeding, washing, gravity separation ...
اقرأ أكثر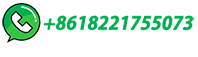
Process optimization of a chrome ore gravity concentration …
conventional chromite ore beneficiation process plant (Figure 3) consist of two sections: Communition (for preparing the material for the subsequent unit operations) Concentration (classification and beneficiation). The beneficiation process flow sheet varies from location to location according to the ore characteristics.
اقرأ أكثر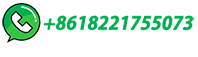
Top 6 Steps Of Iron Ore Processing
Visit our Australian Mining Product and Services to see what our professionals are equipped with to help you in your processing iron ore journey or what other services we can offer. Alternatively, call us on 1300 241 620 to …
اقرأ أكثر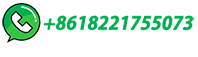
Process Optimization for Gangue Removal from Low-Grade Iron Ore …
This research aims to develop technology that can improve low-grade iron ore containing a large amount of α-FeOOH and gangue to the same level as the high-grade iron ores that are conventionally used. The main goal is to optimize the alkaline hydrothermal treatment conditions for iron ore when using a flow-type reactor for constructing a development …
اقرأ أكثر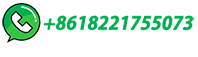
Iron Ore 2015 Conference Paper Number: 108 Optimisation …
the sliding splitter. The flow of the wash water is concurrent with the slurry flow on the spiral. Figure 4 - Wash water setup The spiral was first tested at 30%, 35% and 40% solid concentrations using the iron ore sample without wash water; this was done to establish a benchmark against which the effect of wash water would be compared.
اقرأ أكثر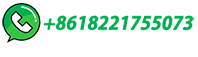
Challenges & Process Flow of Chromium Ore Dressing Technology
Chromium ore dressing process usually adopts gravity separation, flotation, magnetic separation or combined processes to maximize the efficiency of qualified concentrate. ... Challenges & Process Flow of Chromium Ore Dressing Technology. . ... Lead Zinc Ore Processing; Chrome Washing Process; Tin Ore Processing Plant; Contact Us +86 ...
اقرأ أكثر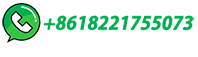
Tailings Filtration: Water Jet Spray Cleaning of a Blinded Iron Ore
Combining water and electric energy prices, the cleaning of the blinded iron ore tailings filtration cloth by using a front-wash costs approximately USD 6 m −2 for parallel operation of full cone nozzles and one pump per nozzle with the condition to increase the flow rate at least by a factor of 100. The cleaning costs presented refer to the ...
اقرأ أكثر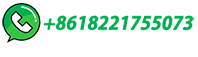
Fine Particle Processing Of Iron Ore Slimes From Wash Plant
site pilot plant tests are recommended as the process appears economically and ecologically feasible and can be retrofitted as tail piece in the existing washing plants. [Key words: WHIMS, Iron ore slimes, processing] 1 Introduction Indian Iron ore occurs mostly as oxides in nature. A substantial amount of this reserve is high grade hematite.
اقرأ أكثر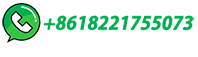
Iron Ore Processing Solution
The first stage: crushing & screening – three stage closed-circuit crushing Large pieces of iron ore are uniformly sent to the jaw crusher or coarse crushing mobile station by the vibrating feeder for coarse crushing; the coarsely crushed iron …
اقرأ أكثر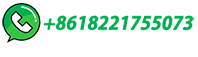
Indian Iron Ore Scenario : Low Grade Iron Ore Beneficiation
There are numerous reasons why it is beneficial to introduce washing of raw iron ore resources to increase efficiencies in steel production and maximize revenues from the ... improved product quality has also forced iron ore producers to review process flow sheets . and evaluate alternative or supplementary processing routes. This has led to ...
اقرأ أكثر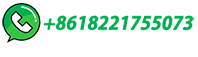
Tin Ore Processing Plant
Tin(Cassiterite) ore processing refers to the process of extracting tin from ore. Gravity separation, magnetic separation and flotation are mainly used to grade tin concentrate and remove other impurities. In order to achieve high efficient, low-cost beneficiation flow, JXSC will custom process and equipment according to ore characteristics.
اقرأ أكثر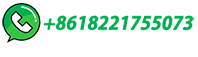