Iron Ore Pellets | 4MANN Group | Aluminum composite panel
The unit converts Low-Grade Iron Ore of 48% Fe to 52% Fe which is in the nature of waste having no alternative usage, into higher-grade ore of 63.00% Fe to be supplied to pelletisation and sinter plants for the manufacture of steel. We do beneficiation and pelletisation by sourcing low-grade iron ore directly from the mines.
اقرأ أكثر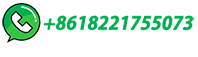
Life cycle assessment of iron ore in Brazil: The
Depending on iron ore price and operational problems, ... this study divided the iron ore mining process into the following stages: ... The data were estimated for 1 t of processed iron ore, except for pelletisation and pellet shipping, which were based on 1 t of pellets. Download: Download high-res image (331KB) Download: Download full-size image;
اقرأ أكثر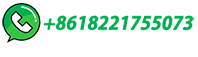
Iron Ore
Iron ore prices for cargoes with 62% iron content climbed above $106 per ton in early February, reaching a two-month high as steel production in China resumed following the Lunar New Year holidays, boosting short-term demand for the metal. On the supply side, weather disruptions in Australia added a risk premium to iron ore prices. ...
اقرأ أكثر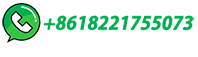
ROLE OF IRON ORE PELLETS TO ACHIEVE TARGET OF …
Beneficiation Pelletisation Iron Making Process Sponge Iron / DRI Steel Making Iron ore Pellets: Fe: 64.0% SiO 2: 3.0% Al 2 O 3: 2.7% LOI ~ NIL ... • Non-availability of calibrated ore and rising prices of Iron ore fines
اقرأ أكثر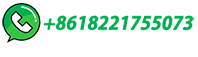
What Are Iron Ore Pellets and How to Make Them?
What are iron ore pellets? Iron ore pellets are spheres of typically 8-16 mm to be used as feedstock for blast furnaces. They contain 64-72% iron and additional materials, which can adjust the chemical composition and metallurgical properties of the pellets. The iron ore pelletization is the process of converting iron fines less than 200 mesh ...
اقرأ أكثر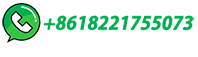
NMDC to double pellet production capacity; to set up ₹800-cr …
NMDC's existing iron ore pelletisation plant with a 1.2 MTPA capacity is located in Karnataka. ... Pelletising is the process through which iron ore fines are transformed into an agglomerated ...
اقرأ أكثر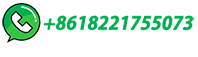
Recycling of steel plant mill scale via iron ore pelletisation process
Abstract. Mill scale is an iron oxide waste generated during steelmaking, casting and rolling. Total generation of mill scale at JSWSL is around 150 t/day and contains 60–70%FeO and 30–35%Fe 2 O 3.To recover the iron, the mill scale must be smelted in a blast furnace or other reduction furnace; however, it is usually too fine to use without previous agglomeration …
اقرأ أكثر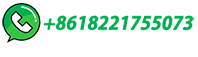
Organic Binder For Iron Ore Pelletisation
Organic Binder for Iron Ore Pelletisation. ... OB-1205 is a highly beneficial and an attractive alternative to bentonite in iron ore pelletizing process, mainly because it burns without leaving any residue in the final pellet. Benefits:-1. OB-1205 substantially reduces bentonite (reducing SiO2 & Al2O3 impurities) in iron ore pelletization and ...
اقرأ أكثر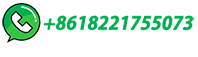
Iron Ore Briquettes
Announced in 2021, these iron ore briquettes began to be developed by us around 20 years ago at our Ferrous Metals Technology Center in Nova Lima, Minas Gerais. They are the latest in a long line of iron ore products we have offered over the course of our history, resulting from major investments in research and innovation.
اقرأ أكثر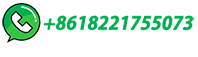
A review of binders in iron ore pelletization
A review of binders in iron ore pelletization. T. C. Eisele Department of Chemical Engineering, Michigan Technological University, Houghton, Michigan, USA & ... Recycling of LD converter sludge and iron-bearing fines using the NCP cold-bond-pellet process. Source: Elsevier BV. Replacement of bentonite by active lime in the production of iron ...
اقرأ أكثر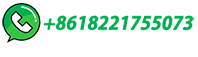
Life cycle energy consumption and greenhouse gas emissions of iron
The iron and steel production is a lengthy and comprehensive process, which includes iron ore processing, coking, sintering, pelletizing, blast furnace (BF) iron making, basic oxygen furnace (BOF) steelmaking, electric arc furnace (EAF) steelmaking, casting, rolling and etc., (Cavaliere, 2016, Ghosh and Chatterjee, 2008).
اقرأ أكثر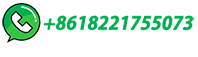
Applications of Iron Ore Pellets
What Is Iron Ore Pelletization Process. The process of pelletization begins with the use of finely powdered grains of iron ore. These grains are then converted into balls. This iron …
اقرأ أكثر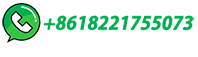
Iron Ore Pelletizing Process: An Overview
However, the content of iron in ore deposits has deteriorated and low-grade iron ore has been processed. The fines resulting from the concentration process must be agglomerated for use …
اقرأ أكثر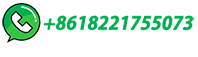
Iron Ore Pellet Production
A Perfect Storm for an Iron Ore Pellet Shortage. Benefits of utilizing iron ore pellets are extensive; in addition to lower emissions and a reduced requirement for coking coal, the use of iron ore pellets allows steel producers to lower …
اقرأ أكثر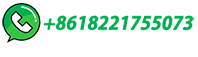
pelletization process by Kshirod | PPT
Pelletization is the process of making spheres of uniform quality iron ore with high carbon content. Iron ore is pelletized so that it can efficiently flow through a blast furnace for smelting. The process involves mixing iron ore …
اقرأ أكثر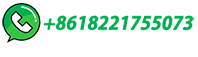
Iron Ore Pellatisation Application in Steel Industry – Grate Kiln Process
Vale S.A opened a 9 MTPA (2 x 4.5) Iron ore pellatisation plant in Sohar, Sultanate of Oman., on March 3rd, 2011. High grade iron ore for the plant is imported from Brazil & finished product is sold to Steel plants globally as a raw material feed for Blast furnace or Electric arc furnace.
اقرأ أكثر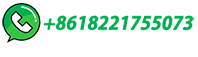
Competition In Pellet Manufacturing In India | Sree Metaliks
India is amongst the top 5 countries in iron ore pelletisation capacity. Palletizing is a process of converting very fine iron ore into uniform sized pellets, very convenient and fit for use in blast furnace and direct reduction furnace. ... The fluctuating prices on the world market are seriously affecting cost-efficient ironmaking. The ...
اقرأ أكثر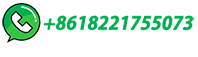
Technological Challenges on Low Grade Iron Ore …
backup. Both physical and reduction roasting process of beneficiation of low and lean grade ores should be exploited and maximized the iron recovery. To utilization of micro-fines concentrate from beneficiation process, pelletisation is the alternative method. The Indian hematite iron ore concentrate has high LOI because of the
اقرأ أكثر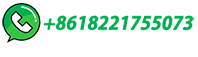
091102 Iron ore
Apart from the existing installations for iron ore pelletisation, there is currently an ongoing project for a new pelletising plant in Austria. The planned capacity could be around 1.4 Mt of ... 2.1 Description of the production process In the iron ore sector, iron ores and concentrates (excluding roasted iron pyrites) are ...
اقرأ أكثر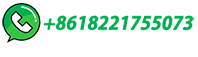
Realizing state of the art "All Indian Pellet plant" by MECON
Blaine number of ground iron ore fines is controlled during iron ore grinding in raw material preparation area. At times, it becomes difficult to maintain required Blaine number (1800-2200 cm2/gm) with change in iron ore characteristics. Lower Blaine
اقرأ أكثر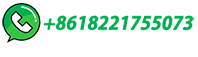
NIIR Project Consultancy Services:Iron ore Pelletization
Iron ore Pelletization - Manufacturing Plant, Detailed Project Report, Profile, Business Plan, Industry Trends, Market Research, Survey, Manufacturing Process, Machinery, Raw …
اقرأ أكثر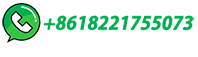
Pelletization
Pelletization is the process of transforming iron ore fines into spherical pellets through agglomeration and induration. These pellets are then used as feed to a blast furnace or direct reduction systems to produce iron. As the only supplier in the world, offers both straight grate and grate-kiln technologies for any required pelletizing ...
اقرأ أكثر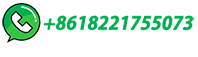
Applications of Iron Ore Pellets
This process of converting iron ore into pellets is known as Pelletization. Iron Ore Pellets are then used in the production of steel. Pellets are usually preferred instead of raw Iron Ore because it allows for maximum utilization of iron ore. This is important since iron ore reserves are depleting globally.
اقرأ أكثر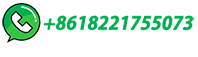
Iron Ore Pelletization: A Critical Review of Processes and
Iron ore pelletization is a critical aspect of the steel manufacturing process, providing a method to utilize fine iron ore particles and beneficiate lower grade ores, which enhances the overall output and efficiency of steel production processes. Pelletization involves converting iron ore fines into compact pellets, which are then used in blast furnaces or direct …
اقرأ أكثر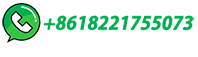
Influence of Pellet Size on Quality and Microstructure of Iron …
2. Pelletisation Process Pellets required for the present study were collected from a commercial straight-grate pellet plant of 3 Mt/year capac-ity. Production of iron oxide pellets from iron ore fines in-volves different operations like drying of ore fines to re-move the moisture and grinding to get the required fine-ness.
اقرأ أكثر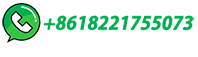
Iron ore pelletization
A brief introduction to recent developments in iron ore pelletizing is provided in this chapter, including the world output of fired pellets, pellet production ... Life cycle energy consumption and greenhouse gas emissions of iron pelletizing process in China, a case study. Journal of Cleaner Production, Volume 233, 2019, pp. 1314-1321. Wei Lv ...
اقرأ أكثر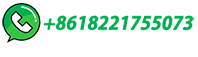
Converting iron ore into iron pellets
Iron ore pelletization is a key process in the steelmaking industry that helps improve the quality and efficiency of steel production. In this process, iron ore is powdered and then converted into small, round iron pellets using various methods such as wet or dry pelletization.
اقرأ أكثر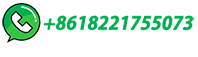
SINTERING AND PELLETISATION OF INDIAN IRON ORES
Growth of steel industry with depleting resources of high grade ores have led to a very strong demand for both pelletising and sintering of iron ores. Process objective is to transform fine …
اقرأ أكثر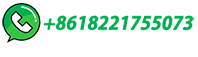
What Are Iron Ore Pellets and How to Make Them?
Iron ore pellets are spheres of typically 8-16 mm to be used as feedstock for blast furnaces. They contain 64-72% iron and additional materials, which can adjust the chemical composition and metallurgical properties of the pellets. The iron ore pelletization is the process of converting iron fines less than 200 mesh (0.074 …
اقرأ أكثر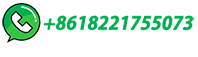
Study on the Induration Cycle During Pelletization of
Indian blast furnaces are fed with lump iron ore (10 - 40 mm) and sinter as burden. Sinter is a prepared burden, where iron ore fines of size -10 + 0.15 mm are agglomerated using mainly flux and coke. Iron ore fines of less than 0.15 mm are not utilized in sintering technology and hence are mostly discarded at mines during processing as slime.
اقرأ أكثر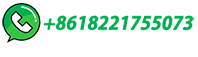