IRON ORES | PPT
14. Cast iron Wrought iron Pig Iron Carbon content 2-4% 0.08% 3.5-4.5% Main properties 1.Contains multiple constituents 1.Purest form 2.Tough,malleable 1.Treases of impurities of sulphur, phosphorus, manganese etc 2.Hard form of iron, brittle Uses Bridges, balusters, Columns, fences, structural connector in buildings Withstands shocks without …
اقرأ أكثر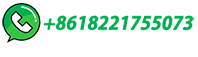
Ore To Iron In A Few Seconds: New Chinese Process …
The process of ironmaking has relied for centuries on iron ore, an impure form of iron oxide, slowly being reduced to iron by carbon monoxide in a furnace. Whether that furnace is the charcoal fire…
اقرأ أكثر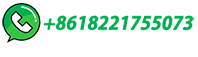
Planning an Iron Ore Mine: From Exploration Data to …
An iron ore mining company, operating in Western Australia, trucks ore from three geographi-cally isolated sources to a crusher, where it is blended before and during crushing.
اقرأ أكثر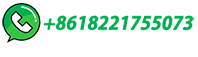
Iron Ore Mining Essentials: Key to Steel Production
Once the deposit of iron ore is feasible, the mining process is moved to digging the ore out from the earth. The most widely used technique is open-pit mining, which involves drilling and blasting the surface rock and soil to get to the ore deposit beneath it in states like Minnesota and Michigan, around the area of Lake Superior.
اقرأ أكثر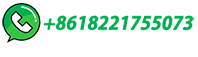
Iron Ore: Mineralogy, Processing and Environmental …
Iron Ore: Mineralogy, Processing and Environmental Sustainability, Second Edition covers all aspects surrounding the second most important commodity behind oil. As an essential input for the production of crude steel, iron ore feeds the world's largest trillion-dollar-a-year metal market and is the backbone of the global infrastructure. The book explores new ore types and …
اقرأ أكثر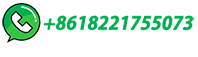
Iron Ore
Mining and processing hematite and magnetite ores. High-grade hematite ore is referred to as direct shipping ore (DSO) as, once mined, the ore goes through a simple crushing and screening process before being exported for steel-making. ... Total Australian Ore Reserves of iron ore reported in compliance with the JORC Code were estimated to be ...
اقرأ أكثر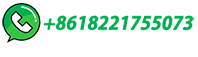
Froth Flotation of Iron Ores
With the depleting reserves of high-grade iron ore in the world, froth flotation has become increasingly important to process intermediate- and low-grade iron ore in an attempt to meet the rapidly growing demand on the international market. In over half a century's practice in the iron ore industry, froth flotation has been established as an efficient method to remove …
اقرأ أكثر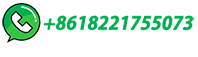
Towards iron ore mining sustainability and low-carbon …
The efficiency of iron ore mining plays a pivotal role in advancing both low-carbon transition and green recovery initiatives. A key focus in these endeavors is the imperative to improve iron ore mining efficiency, emphasizing the reduction of waste and environmental impact (Tang et al., 2023). In the context of a low-carbon transition ...
اقرأ أكثر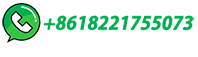
Iron ore beneficiation: an overview
Dry processing of iron ore: In dry processing of iron ore, ROM is generally crushed below 40 mm through three-stage crushing and thus segregated by screening into 10–40 and −10 mm fractions. For softer ore, tumbler index is generally low and hence lump ore is crushed below 10 mm to produce fine product. Yield from the plants has been ...
اقرأ أكثر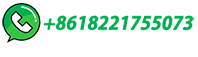
Top 6 Steps Of Iron Ore Processing
Visit our Australian Mining Product and Services to see what our professionals are equipped with to help you in your processing iron ore journey or what other services we can offer. Alternatively, call us on 1300 241 620 to speak to our experts today and learn all about the mining iron ore process. Types Of Iron Ore In Australia
اقرأ أكثر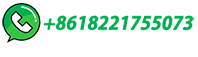
Iron Ore Processing
Resource Recovery and Recycling from Metallurgical Wastes. S. Ramachandra Rao, in Waste Management Series, 2006 9.8 Production of Ceramic Tiles from Iron Ore Tailings. Current practice of washing iron ore before it is processed for extractive metallurgical operation results in three products, coarse ore lumps with sizes in the range 10-80 mm, which are directly charged …
اقرأ أكثر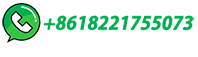
Iron Ore Processing
Iron Ore Dressing. The iron ore dressing process is aimed at the processing of iron ore materials, which is divided into crushing and screening, grinding and classification, separation, and dehydration.Crushing and screening refers to the crushing and screening of iron ore to ensure that the particle size of crushed ore can provide ore that meets the requirements of block size …
اقرأ أكثر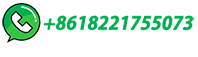
Open-Pit Mining | Method and Process | Epiroc US
In hard rock mining, much of the world's annual output of copper, gold and iron ore is won from open-pit operations. Other commodities produced from open-pit mining include diamonds, molybdenum, manganese, lead and zinc, uranium and a variety of industrial minerals, such as borates, talc and specialist clays.
اقرأ أكثر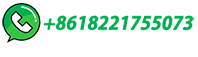
Comprehensive Guide to Iron Ore Mining and Mineral Processing
Iron ore is a naturally occurring rock that contains iron minerals. The process of iron ore mining and mineral processing involves several steps, including:Exploration and discovery: This is the …
اقرأ أكثر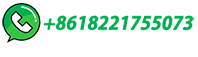
Ball Mill and Crusher for Iron Ore in Mineral Processing
Iron ore is one of the most important minerals in the world, serving as the primary raw material for steel production. As demand for steel continues to grow globally, efficient and reliable processes for extracting iron from its ore become crucial. Two critical pieces of equipment used in this process are the ball mill and the crusher.These machines play vital roles in the …
اقرأ أكثر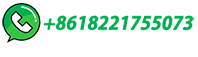
Iron Ore Processing, General
2.2 Mining Methods. Iron ore mining methods vary by the type of ore being mined. Currently, there are four main types of iron ore deposits, depending on the mineralogy and geology of the ore deposits. These are magnetite, titanomagnetite, massive hematite, and pisolitic ironstone deposits. For taconite iron ores, mining iron ore begins at ...
اقرأ أكثر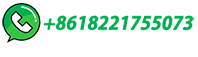
A critical review on metallurgical recovery of iron from iron ore
Fig. 2 illustrates the iron ore beneficiation process, particularly magnetic separation, resulting in the generation of inevitable tailings. Due to the characteristics of iron ores and the conditions during beneficiation, it is inevitable that approximately 2.5–3 tons of IOTs are generated for every 1 ton of iron ore concentrate produced [7].In 2019, the global annual …
اقرأ أكثر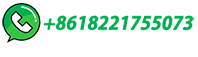
Dry beneficiation of iron ore
Dry iron ore beneficiation is without doubt currently being driven forward by Vale in Brazil. The company wants to increase its capacity from 340 Mta iron ore at present to 450 Mta in future, dry beneficiation is to be further increased by 10 % from 60 % at present. Dry beneficiation capacity will increase by around 110 Mta.
اقرأ أكثر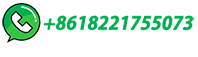
Seminar on iron ore beneficiation in india | PPT
3. Introduction Iron is the fourth most abundant mineral on earth having a reserve of 170 billion tonnes of crude iron ore. Iron & steel is the driving force behind industrial development in any country. The mining of iron ore, an essential raw material for Iron & Steel Industry, is arguably of prime importance among all mining activities undertaken by any …
اقرأ أكثر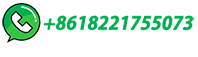
OneMine | Iron Ore
Iron Ore - Mineral Processing Overview Several years of iron ore price increases, coupled with a period of strong global demand for raw materials, presented iron and steel producers with unprecedented costs and difficulty procuring the demanded high quantities of iron ore. These conditions spurred many companies to investigate new ore bodies and also …
اقرأ أكثر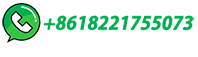
Energy and Environmental Profile of the U.S. Mining Industry 4
4.1 Process Overview 4.1.1 Iron Ore Mining There are two basic methods of mining iron ore. These are: • Surface mining or open-pit mining • Underground or shaft mining To be competitive, iron mining must be done on a very large scale. Surface mining is the preferred choice, although there are exceptions.
اقرأ أكثر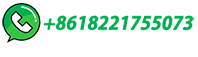
Life cycle assessment of iron ore mining and processing
The estimated greenhouse gas emissions were 11.9 kg CO 2 e for mining and processing 1 tonne of iron ore. The embodied energy values were 153 MJ/t ore for iron ore. The results showed that loading and hauling made the largest contributions (approximately 50%) to the total greenhouse gas emissions from the mining and processing of iron ore.
اقرأ أكثر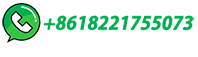
Iron Ore Mining | Techniques | Metal Extraction
Extracting iron from its ore requires following a series of steps and is considered the penultimate process in metallurgy. These steps involve first concentrating the ore, then extracting the metal from the concentrated ore, and finally purifying …
اقرأ أكثر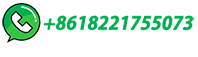
Brazilian company patents innovative dry iron ore processing …
Dry iron ore processing. The mining activity produces lots of materials with no commercial value. That is because the iron ore traded in the market must be composed of at least 58% of ore. With ...
اقرأ أكثر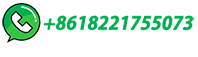
Quality Prediction in a Mining Process | by TechLabs Aachen
Starch flow, Amina flow, and Ore Pulp properties are the most important variables (control variables) as they impact ore quality at the end of the process. Airflow and column level from floatation columns 1–7 measure the process parameters. % Iron and Silica are the final iron ore pulp quality measures which are drawn from laboratory results.
اقرأ أكثر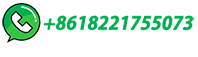
Iron processing
Iron processing - Ores, Smelting, Refining: Iron ores occur in igneous, metamorphic (transformed), or sedimentary rocks in a variety of geologic environments. Most are sedimentary, but many have been changed by weathering, and so their precise origin is difficult to determine. The most widely distributed iron-bearing minerals are oxides, and iron ores consist mainly of …
اقرأ أكثر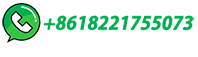
Iron Ore Processing: From Extraction to …
Iron ore processing is a complex and vital process that transforms raw iron ore into usable steel. From exploration and extraction to grinding, beneficiation, and ironmaking, each stage plays a crucial role in producing …
اقرأ أكثر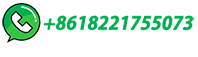
Analysis of life-cycle GHG emissions for iron ore mining and processing
Aggregated energy for the iron ore mining and processing stages is derived from The Chinese Energy Statistics Year Book (2012). The total energy consumption results from consumption of 1.8 kg of coal, 1.2 kg of coke, 25 MJ of diesel fuel and 34 kWh electricity use to produce a tonne of iron ore in 2013.
اقرأ أكثر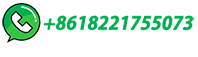
Revolutionising iron ore processing
In the dynamic world of mining, Corporation has become synonymous with innovation. W ith a legacy rooted in Australian iron ore processing since the 1950s, Corporation continues to ...
اقرأ أكثر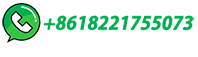
The six main steps of iron ore processing
Discover the iron ore mining process, from blasting to export, and its vital role in steel production. Learn about iron ore extraction and its history
اقرأ أكثر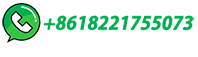