How a Coke Plant Works
Here, the coke is quenched with water. The coke is then taken to a coke wharf, where the remaining water evaporates. A reclaimer then feeds the coke from the wharf to a conveyor belt, which transfers the coke to the …
اقرأ أكثر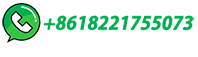
COKE CRUSHING CHARACTERISTICS
coke ovens must be crushed, usually to a top size of about 314-inch. Very small sizes must be screened from the crushed coke, leaving an acceptable size of about 3/4" ~1/8". Problems …
اقرأ أكثر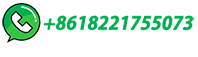
Production of petroleum coke (sponge coke)
Production of petroleum coke (sponge coke) Sponge coke, also known as petroleum coke or petcoke, is a carbon-rich solid material derived from the refining process of crude oil. It is produced when heavy residual oil undergoes thermal decomposition in a delayed coking unit. The resulting sponge coke has a porous and sponge-like structure, which gives […]
اقرأ أكثر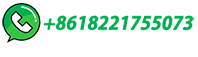
Closed Coke Slurry System
TRIPLAN is offering a unique system for coke handling in a Delayed Coker Unit (DCU). compared with traditional DCU design. During our presentation we will highlight these unique features of …
اقرأ أكثر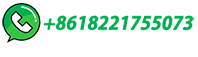
Coal vs. Coke
Once extracted, it undergoes various stages of preparation, including crushing, washing, and blending, to remove impurities and improve its quality. On the contrary, coke is produced through a process called coking. ... Due to the removal of volatile components during the coking process, coke has a higher concentration of carbon, resulting in a ...
اقرأ أكثر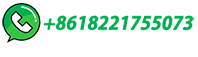
Effect of Binders on the Crushing Strength of Ferro-Coke
The traditional blast furnace (BF) iron-making process has great demand for coke, which results in large CO 2 emission. It has caused great pressure on the environmental governance, ... The crushing strength of ferro-coke with different amounts of iron ore is shown in Figure 6. Without iron ore, QM had the highest crushing strength, which was ...
اقرأ أكثر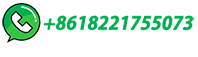
What equipment is used for coke crushing?
Coke crushing process. The coke enters the raw material bin and is evenly sent to the hammer crusher by the vibrating feeder for crushing. The crushed material is sent to the vibrating screen by the belt conveyor to screen out various …
اقرأ أكثر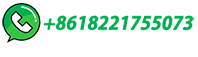
coke crushing plant
Here is a general overview of the process: Primary Crushing: The larger coke pieces obtained from the coke production process are initially crushed in a primary crusher. …
اقرأ أكثر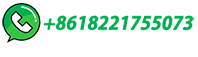
Co-pyrolysis of coal with biomass residues and coke breeze for …
The hot-pressed cokes have high crushing strength when the blending ratio of biomass or breeze is appropriate. Biomass and breeze were mixed with the coking coal with different blending ratios. The coke crushing strength is shown in Fig. 3. The crushing strength of coke is 2.61 MPa when coal is coked without pressing.
اقرأ أكثر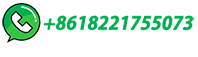
What is Semi Coke?
Semi coke, also known as semicoke, is a carbonaceous material produced through the low-temperature carbonization of coal or other carbon-rich materials in an oxygen-deficient environment. The process typically occurs at temperatures ranging from 600 to 1000°C, resulting in the removal of volatile compounds and the formation of a solid material primarily composed …
اقرأ أكثر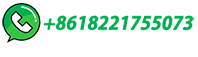
Technologies for Improvement in Coking process in …
At the crushing station, the coals are crushed type by type with individual crusher settings. After the crushing process, the crushed coal is transported to the blending station. Each coal type is stored in a separate blending bin. ... Fig 3 …
اقرأ أكثر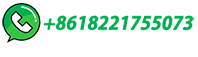
The Production Process of Coke from Coal: A Complete Overview
Quenching Process: After carbonization, the hot coke is rapidly cooled with water or an inert gas to stabilize its structure. Quenching Methods: Different quenching methods, such as wet quenching or dry quenching, are employed to achieve specific coke properties.
اقرأ أكثر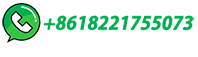
Safe, Automated, Pet Coke Dewatering and Crushing
General Kinematics Petroleum Coke Dewatering System produces a continuous, reliable dewatered flow stream for pet coke's fast and efficient processing. GK's patented dewatering deck technology eliminates blinding and constant screen …
اقرأ أكثر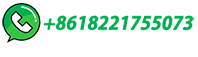
Justification of Rational Energy-Power Parameters of the Drive of …
Abstract Based on the results of the study of the crushing process of metallurgical coke, rational energy-power parameters of roller crushers used for fractional preparation of solid fuels in sintering production are substantiated. Under laboratory conditions, experiments were carried out to determine the conditions for the destruction of blast-furnace coke and dry …
اقرأ أكثر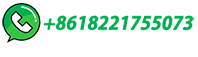
Sintering plant at a glance | PPT
This document provides information about the sintering process used in iron and steelmaking. It defines sintering as the agglomeration of iron ore fines into a porous mass through controlled combustion. ... COKE CRUSHING BY FOUR ROLL CRUSHERS 8 ( 08 Nos. CAPACITY – 16 T/Hr. EACH ) MIX COKE FROM C.O. COKE RETURN FROM B.F. ( - 15mm ) …
اقرأ أكثر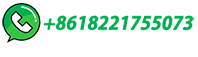
Environmental and economic impacts assessment of prebaked …
The petroleum coke consumed in the coarse crushing process accounted for the largest proportion of economic costs in the overall production process with a ratio of 63.55%. Less consumption of petroleum coke, higher recycle rate of prebaked anode help to reduce the environmental impacts and production cost of the whole process effectively. The ...
اقرأ أكثر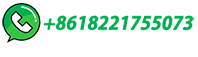
Process
This section collect the Raw materials like Lime Stone, Clay, Coke Breeze and Iron Ore. and analyze the chemical composition and prepare a raw mix design. Then crushing the lime stone small parts 50 mm below crusher the lime stone belt conveyer through the hummer mill. Hummer mill crushing the lime stone small parts 10…
اقرأ أكثر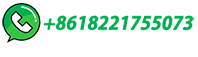
The fracture characteristics and enhancement mechanism of crushing
The pore structures of cokes were determined according to the mercury intrusion porosimetry. The finite element method with the brittle cracking model was used to simulate the crushing process of cokes. To obtain high-quality coke, the influences of hot pressing parameters on the crushing strength of coke were investigated.
اقرأ أكثر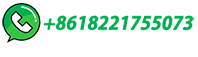
12.2 Coke Production
control the rate of coke falling onto a conveyor belt, which carries the coke to a crushing and screening system. The coke is then crushed and screened to the proper size for the blast furnace operation. The sized coke is transported to a storage area where it is kept until ready for use or shipment. 12.2.1.4 Byproduct Collection -
اقرأ أكثر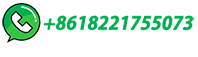
Coke Ovens-Sinter-BF-BOF Route
Selective Crushing of Coals : In this technology, the aim is to improve homogeneity of reactive & inert components in coal by reducing the difference properties of coarse & fine size fractions. ... Reduction in coke rate in blast furnaces; SINTERING PROCESS A Sinter Plant typically comprise the following sub-units as shown below. SINTERING ...
اقرأ أكثر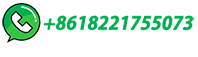
Silicon Manufacturing | The Silicon Manufacturing Process
Silicon metal is made from the reaction of silica and carbon materials like coke, coal and wood chips. When it comes to the manufacturing of silicon for wafers, the process can generally be broken down into three steps. ... Before shipping, the metal is sized according to customer specifications, which may require a crushing process using jaw ...
اقرأ أكثر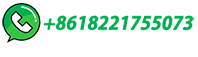
Graphite Manufacturing Process | Flowchart
Raw coke materials are typically stored in large storage silos before being inserted into the production process. 2. Crushing. The first step in graphite manufacturing involves crushing and pulverizing the raw coke materials, such as coal and petroleum, into a micro-fine powder. This is typically done using crushers and mills that break down ...
اقرأ أكثر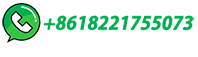
12.2 Coke Production
Coke manufacturing includes preparing, charging, and heating the coal; removing and cooling the coke product; and cooling, cleaning, and recycling the oven gas. Coal is prepared for coking …
اقرأ أكثر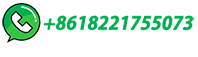
12.2 Coke Production
control the rate of coke falling onto a conveyor belt, which carries the coke to a crushing and screening system. The coke is then crushed and screened to the proper size for the blast …
اقرأ أكثر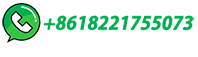
Petroleum Coke Crusher: Choosing the Right Equipment
The pet coke is fed into the crushing chamber, where the hammers repeatedly impact and crush the material against a breaker plate. Hammer crushers are versatile machines capable of handling a wide range of materials and are suitable for both primary and secondary crushing. Roll Crusher. Roll crushers are also commonly used for crushing ...
اقرأ أكثر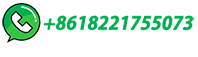
11.4 Calcium Carbide Manufacturing
The process for manufacturing calcium carbide is illustrated in Figure 11.4-1. Moisture is ... through primary crushing by jaw crushers, followed by secondary crushing and screening for size. ... Coke dryer with fabric filter (SCC 3-05-004-02) 0.13n ND NA ND Furnace room vents (SCC 3 …
اقرأ أكثر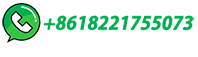
coke crushing plant
Coke crushing plants use specialized machinery to crush and process large amounts of raw coke material. The size of the crushed coke pieces varies depending on the desired final product size.
اقرأ أكثر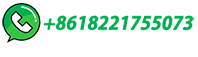
Variability of metallurgical coke reactivity under the NSC test
The differences in coke reactivity could be related to the coke crushing and fissuring. Even though the coke crushing process is standardised and it was previously concluded that coke on 20 mm size scale could be considered homogenous [12] and free of fissures [13], [14], recent research shown that coke crushing introduces micro-fractures into ...
اقرأ أكثر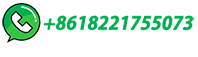
Coke crusher/coke mill
The crushing process can be either dry or wet, with dry crushing being more common. In dry crushing, the coke is typically conveyed directly to the crusher. In wet crushing, the coke may …
اقرأ أكثر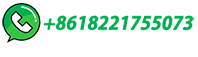
Effect of Coal Size on Coking Pressure and Coke Strength
Reducing the coking pressure and improving coke strength are important subjects in the coke-making process. Focusing on the fine crushing of coal to achieve them, we investigated the reduction of the coking pressure by a selective fine crushing of high-coking pressure coal and the effect of fine crushing of inertinite on coke strength.
اقرأ أكثر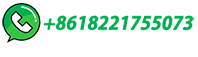