Pelletisation process | PPT
2. Introduction To Pelletisation Process Pellets are spherical balls formed by the agglomeration of natural or ground iron ore fines in the presence of moisture and binder These green balls of 5 – 20mm size are then dried, preheated and fired at 1250 – 13500 C Bonding is developed between the fine ore particles at such high temperatures Additives like Bentonite, …
اقرأ أكثر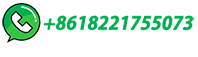
Scheme of gas flow among the pellets distributed in the furnace …
The MPG allows various firing profiles of iron ore pellets, which allows comparative studies for optimization of industrial heat profiles by correlating fired pellet qualities with induration time ...
اقرأ أكثر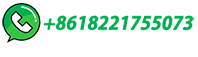
Gas Fired Iron Ore Pelletizing Kiln
A raw lignite gas flow of 20,455 std ft³/hr (3.5 million Btu/hr) was necessary to achieve the 1,300° C (2,372° F) temperature required for pellet induration. The raw gas had a …
اقرأ أكثر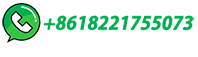
Iron ore pelletization
Iron ore lump, sinter, and pellets comprise the main burden of modern blast furnaces. However, sinter and pellets are now the dominant blast furnace burden, because the nat -
اقرأ أكثر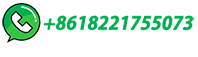
Virtual indurator: A tool for simulation of induration of wet iron ore
They have also developed a simulation software called INDSYS for iron ore pellet induration. Since gas flow distribution plays a critical role in induration, Cross, Patel, and Wade (1990) developed a gas flow distribution model and used the gas flow profile in making predictions of gas temperature profile using the mass and energy balance model.
اقرأ أكثر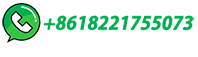
Abstract and Figures
The furnace was designed to permit continuous production of reduced pellets at the rate of 1.5t/day.Effects of operational factors such as reduction temperature, gas composition and gas flow rate ...
اقرأ أكثر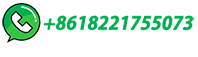
ANALYSIS OF IMPACT OF MECHANICAL DEGRADATION …
iron ore pellets occupy an important role in the iron production industry as raw material ... (Argentina) and Gilmore (India) plants [6-7]. ... Gas phase Temperature (K) 1100.0 Flow rate (Nm3/h ...
اقرأ أكثر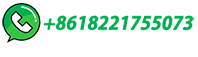
Beneficiation Plants and Pelletizing Plants for Utilizing Low …
In many cases, ore with a total iron content of 60% to 63%, or greater, is regarded as high grade, and ore with a lower iron content is regarded as low grade. Ores are also classified as follows, …
اقرأ أكثر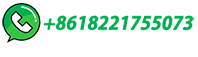
Optimization of the Iron Ore Direct Reduction Process through
Evolution of pellet structure along with reaction: (a) Unreacted Shrinking Core Model; (b) Grain Model.The porous structure evolution (b) was determined from experimental observations [].3. Shaft Furnace Model 3.1. Previous Works. The shaft furnace is the core of the DR process.Iron ore pellets are charged at the top, descend due to gravity, and encounter an upward counter …
اقرأ أكثر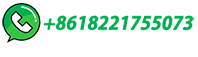
THE GROWING IMPORTANCE OF PELLETIZING FOR IRON ORE MINING AND IRON
The binder is an important additive widely applied in pelletizing iron ore concentrates, making iron ore pellets available as feedstocks for blast furnace ironmaking or direct reduction processes ...
اقرأ أكثر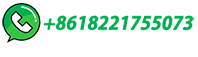
Gas Flow Digram Of Iron Ore Pellet Plant
The document discusses the grate-kiln technology used in a 1.2MTPA iron ore pellet plant. The grate-kiln process employs a straight grate followed by a rotary kiln to evenly heat and …
اقرأ أكثر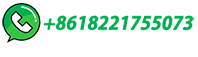
Cooling process of iron ore pellets in an annular cooler
and 7.14%, respectively, indicating the validity of the model. Further, the effects of process parameters, such as pellet diame ter, bed thickness, air velocity, and temperature, on the pellet bed temperature profiles were studied. Keywords: iron ore pellets; mathematical models; cooling; numerical analysis
اقرأ أكثر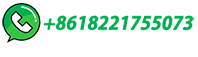
ANALYSIS OF IMPACT OF MECHANICAL …
This is a counter current gas-solid reactor, which transforms iron ore pellets into sponge iron.Simultaneous mass and energy balance along the reactor leads to a set of ordinary differential ...
اقرأ أكثر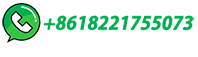
GUIDELINES FOR SELECTING PELLET PLANT TECHNOLOGY …
As greater amounts of fine iron ore concentrates enter the marketplace, new investments in iron ore pelletizing capacity are inevitable to deliver these concentrates to steel industry consumers.
اقرأ أكثر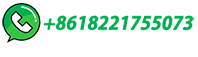
A Mathematical Model for Straight-Grate Iron Oxide Pellet …
a b s t r a c t A mathematical model is developed for induration of the iron-ore pellets in an industrial-scale plant based on the laws of mass, heat and momentum transfer. ... gas-flow through ...
اقرأ أكثر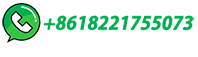
Process flow chart of preparation of pellets | Download …
The present study deals with the utilization of fines generated from comminution process (crushing, grinding and screening) of the Run of Mines into value added products i.e. fluxed iron ore...
اقرأ أكثر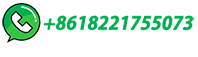
Iron Ore Pellet Plant | PDF | Iron Ore
The document discusses the production of iron ore pellets. It states that the major raw materials required are iron ore fines and bentonite. Iron ore fines of 0-5mm in size are used and must meet physical and chemical requirements. Bentonite …
اقرأ أكثر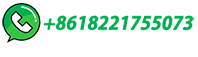
Novel Methodology of Modeling Iron Ore Induration Furnaces …
In this work, a three-dimensional model of the pellet bed has been combined with a one-dimensional model of the gas flow network for easy deployment to a wide range of process gas flow configurations. The model was validated against reference plant operating data and then used to improve the operational efficiency of an induration furnace.
اقرأ أكثر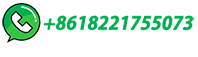
Reduction of Iron Ore Pellets: A Microstructural Perspective?
Twenty different iron ore pellets, consisting primarily of Hematite (Fe2O3) phase, were subjected to 'simulated' reduction studies. A wide range of reduction time periods, Rt of 122 to 211 minutes, were obtained. Detailed microstructural characterizations were then conducted at different locations of ten selected specimens. The Rt did not relate with initial phase mix or …
اقرأ أكثر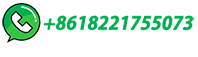
Converting iron ore into iron pellets
In this method, iron ore is heated with additives in a rotary kiln to become pellets. Advantages This method can enable the production of high-quality pellets. 6- Fluidized bed pelletizing: In this method, iron ore particles are placed in a fluidized bed and pelletizing is carried out under the influence of air or gas flow.
اقرأ أكثر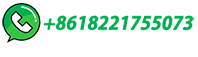
Initial stage of deposit formation process in a coal fired grate …
A large quantity of iron ore concentrate obtained by separation and beneficiation process must be agglomerated through sintering and pelletization before ironmaking [1].Iron ore pellets play an important role in the raw materials for ironmaking [2].In China, the grate-rotary kiln process is widely adopted to produce iron ore pellets [3].However, deposits are frequently …
اقرأ أكثر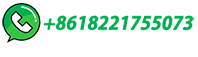
GAS FLOW IMPROVEMENT IN A PELLETIZING PLANT 1
flow diagram of the Vargem Grande Pelletizing Plant. The iron ore slurry passes through the following areas to become fired pellets i. Tanking – 6 slurry tanks, 3150 m³ each. ii. Grinding – …
اقرأ أكثر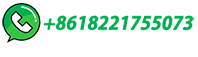
Analysis of impact of mechanical degradation of iron ore pellets on gas
In the furnace, five phases: gas, lump solids (iron ore, sinter, pellets and coke), liquids (pig iron and molten slag) and powders (tuyere injectants: pulverized coal, coke fines or dust from the ...
اقرأ أكثر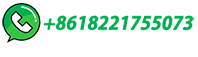
Formulating iron ore pellet induration process in an industrial
Induration is a crucial step in pellet making process in the steel industry. This unit is well-known as an energy intensive process [6] and motivated with this fact, the present work is undertaken to deal with this iron ore pellet induration system. The induration units used for heat hardening mainly differ in their designs, and the concerned technologies available for …
اقرأ أكثر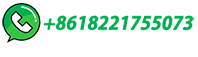
A Mathematical Model for Straight-Grate Iron Oxide Pellet …
In this work, a mathematical model for the straight-grate pellet induration furnace is presented. The induration furnace is an equipment used for the efficient heat and mass transfer between the pellet bed and the flowing gas. The model includes different physicochemical phenomenon like gas-solid heat and mass transfer, drying and condensation of free surface …
اقرأ أكثر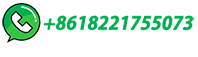
Pelletizing Process
There are two major methods of ironmaking: (1) ironmaking on large-scale using a blast furnace and (2) ironmaking on small-to-mid scale using an electric arc furnace (EAF). The raw …
اقرأ أكثر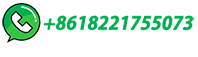
Pellet Plant Presentation-2019 | PDF | Nature | Chemistry
Pellet Plant Presentation-2019 - Free download as Powerpoint Presentation (.ppt), PDF File (.pdf), Text File (.txt) or view presentation slides online. The document discusses the iron ore pelletization process. It begins by defining pellets and describing their properties. It then discusses the history and various technologies used for pelletization, including vertical shaft furnace, …
اقرأ أكثر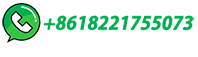
iron ore pellet plant flow diagram – Grinding Mill China
An iron ore plant contains many pieces of … to that of the process gas flow. For more detail see individual equipment. >See also Control Systems for iron ore pellet plants » Free Online Chat. iron ore mining process equipment,iron ore … Iron ore processing plant. Iron ore mining processing plant works … Iron ore processing flow chart.
اقرأ أكثر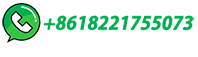
Biomass gasification for natural gas substitution in iron ore
The efficiency of using 40.4-60.7 vol.% of sunflower husks on the combined machine "straight grate - rotary kiln - annular cooler" to partially replace natural gas in iron ore pellets ...
اقرأ أكثر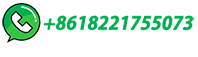
Production of iron ore pellets, process overview to the left, and
This paper summarizes more than a decade of systematic studies of the flow field in an iron ore pelletizing rotary kiln using computational fluid dynamics (CFD) on simplified models of a...
اقرأ أكثر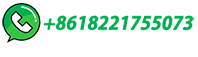