12.6 Primary Lead Smelting
The processing of lead concentrate into metallurgical lead involves 3 major steps: sintering, reduction, and refining. A diagram of a typical facility, with particle and gaseous emission sources
اقرأ أكثر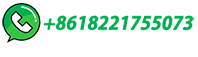
The wear-resistant ceramic liner has achieved excellent wear
Condition before transformation. The raw material of the sintering plant is lead-zinc sulfide-based concentrate, which is mixed with returned ore with a size of -6mm after sintering for sintering.
اقرأ أكثر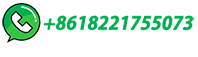
Factors influencing Sinter and Sintering Process
Fig 1 Flowsheet of sintering process. The iron ore fines are natural ore of size 0 mm to 10 mm. The raw mix (also called sinter mix) is made with the weighed amount of iron ore fines, limestone, dolomite, sand or quartzite fines (flux), solid fuel (coke breeze or anthracite) and metallurgical wastes (collected dusts, sludge and mill scale etc).
اقرأ أكثر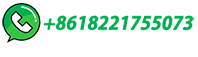
BACKGROUND REPORT PRIMARY LEAD SMELTING AND …
The processing of lead concentrate into metallurgical lead involves three major steps: sintering, reduction, and refining. A diagram of a typical facility, with particle and gaseous
اقرأ أكثر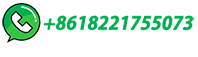
Preparation and characterization of glass ceramics synthesized …
According to the China Nonferrous Metals Industry Association data, China's lead-smelting enterprises produced more than 3 million tons of lead slag in 2017, and the historical stockpile exceeded 100 million tons [1, 2].Lead slag is mainly treated using the rough method of open storage or simple landfill, and every 10,000 tons of lead slag piled up requires an area of …
اقرأ أكثر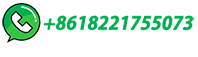
(PDF) Iron Ore Sintering: Process
Sintering is a thermal agglomeration process that is applied to a mixture of iron ore fines, recycled ironmaking products, fluxes, slag-forming agents and solid fuel (coke).
اقرأ أكثر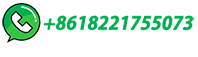
INTRODUCTION
grade and complex concentrate of lead (-40% Pb) in the sintering operation. The plant sinter produced exhibited low strength and its ncicrostructural examination revealed non - uniform distribution of
اقرأ أكثر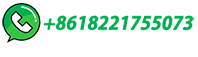
The Recovery of PW Zinc from Lead Blast Furnace Slags by …
The quantity of slag produced by blast furnace is approximately 65,000 tonnes/yr, 30,000 tonnes/yr of which is sent back to the sintering plant for mixing with lead concentrates. The …
اقرأ أكثر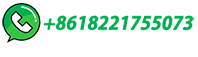
The Recovery of PW Zinc from Lead Blast Furnace Slags by …
The Chigirishima Smelter of Toho,Zinc Co., Ltd. is the largest independent custom lead smelter in Japan and produces about 60,000 tonnes/yr of electrolytic lead. The quantity of slag produced by blast furnace is approximately 65,000 tonnes/yr, 30,000 tonnes/yr of which is sent back to the sintering plant for mixing with lead concentrates. The remaining slag used to be piled up at the …
اقرأ أكثر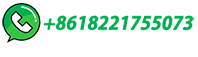
Projects Reports
Once the lead ore is mined, it must undergo several different processes in order to be turned into usable or metallurgical lead material: sintering, smelting, and refining. The sintering phase involves removing sulfur from the lead ore using …
اقرأ أكثر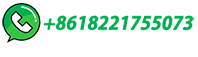
lead sintering plant return fines
Sintering Plant at A Glance PDF Blast Furnace Sintering WebOct 22, 2015 Ideal size of ore Fines -10 mm to 100 mesh Coke breeze -3.2 mm 85% Flux - - 3.2 mm 85% (2) Fuel content - Variation in Fuel content in Charge Mix affect the peak Temperature attained during sintering, the combustion zone will not be uniform leading to poor bed permeability ...
اقرأ أكثر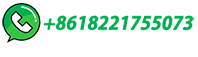
Technologies for Improvement in Sintering Process
By increasing the by-pass return fine ratio and size, the sintering speed and sinter productivity is increased. Fig 3 shows the typical material flow at the sinter plant. Transportation of return fines diverges into two routes by a divergence damper. One is to the existing return fine bin and the other to the new by-pass return fine bin.
اقرأ أكثر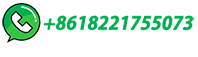
BACKGROUND REPORT PRIMARY LEAD SMELTING AND …
The processing of lead concentrate into metallurgical lead involves three major steps: sintering, reduction, and refining. A diagram of a typical facility, with particle and gaseous ... & Handling Facility Ore Proportioning Feeders Charge Preparation Baghouse Drossing Plant Slag Nodulizing Drum Lead Sinter Machine Converter Heat Exchanger ...
اقرأ أكثر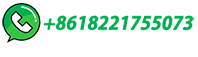
Slag Breaking Pig Iron Crushing
The Effect of Removing Hard-to-Grind Minerals from Steel Slag … The hard-to-grind minerals in steel slag are native-iron, magnesium ferrite and calcium ferrite, accounting for 22.38%, which are harder than other minerals, and the large amount of hard-to-grind minerals in the grinding process will lead to a decrease in the efficiency of grinding.
اقرأ أكثر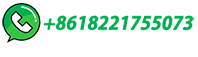
Sinter Plant Operation
Process Control of Sintering Plant. Sulfide concentrates, oxide materials and I.S.F. dross are prepared in the proportioning bins (There are ten bins for raw materials.). The raw …
اقرأ أكثر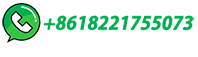
Schedule Slag Plant Tio2 Construction
Much of this will be in a new 120,000 tpa sulphate-route TiO 2 pigment plant, but Group DF also plans to construct a titanium slag plant, with the capacity of 150,000 tpa, and a … Slag recycling Of the approximately 5.6 Mta of steelworks slags, 36 % were recovered in 2017 and 23 % were recycled within the steel industry.
اقرأ أكثر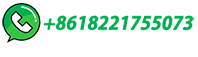
Iron Ore Sintering: Raw Materials and Granulation
Sintering is an agglomeration process that fuses iron ore fines, fluxes, recycled products, slag-forming elements and coke. The purpose of sintering is to obtain a product with suitable ...
اقرأ أكثر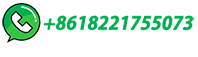
12.6 Primary Lead Smelting
12.6 Primary Lead Smelting 12.6.1 General15 Lead is found naturally as a sulfide ore containing small amounts of copper, iron, zinc, precious metals, and other trace elements. The lead in this ore, typically after being concentrated at or near the mine (see Section 12.18), is processed into metallurgical lead at 4 facilities in the U. S.
اقرأ أكثر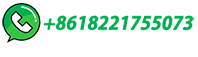
PROCESS BRIEF
Plant Dept.of an Integrated Steel Plant. 3. PROCESS BRIEF Sintering process is developed mainly to utilize under size of lump ore called iron ... charging bins for Iron Ore Fines/ Coke Breeze/ Lime Dust/ Return Fines, Mixing Drums, Sinter Machine, Sinter Breaker/ crusher, Screens (Hot & Cold), ESPs (Electrostatic Precipitator), Exhausters, ...
اقرأ أكثر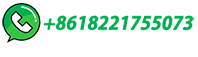
A cleaner process for lead recovery from lead-containing …
Thermodynamic analysis confirms feasibility and reliability of the experiment. 92% of lead was recovered and lead content in slag decreased to 1.2%. Other valuable metals are …
اقرأ أكثر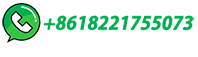
Sinter Plant Operation
Process Control of Sintering Plant. Sulfide concentrates, oxide materials and I.S.F. dross are prepared in the proportioning bins (There are ten bins for raw materials.). The raw materials and flux are fed by separate variable speed belt conveyers consisting of computer controlled belt weighers. ... Raw materials and crushed return sinter are ...
اقرأ أكثر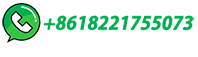
Blast Furnace Materials System Facilities
The public and auxiliary facilities of blast furnace ironmaking mainly includes storage and transportation of raw materials and fuel facilities, thermal facilities, gas facilities, water supply and drainage facilities and HVAC facilities. At project preliminary design, the storage and transportation facilities for raw materials and fuel are divided five sectors.
اقرأ أكثر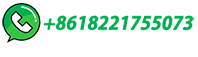
(DOC) SOLID WASTE UTILISATION -AN INITIATIVE AT BHILAI STEEL PLANT
The sintering process provides a perfect avenue for utilization of solid wastes especially fines. The major wastes generated in the steel plant and utilized in Sintering Plant – 3 are Mill scale, Flue Dust, sinter return, sludge, LD Slag, quenching pond coke residues and RMP arisings.
اقرأ أكثر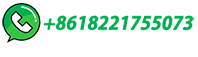
Sintering: Most Efficient Technologies for Greenhouse Emissions
This reduces off-gas volumes by about 40–50% without affecting the sintering process. In an emission optimized sintering plant, the whole sintering gases are collected and then forced to recirculate on the sintering surface to contribute to the material heating (Fig. 3.18). In this way <50% of the waste gas is emitted in the atmosphere.
اقرأ أكثر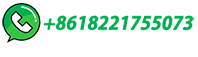
Sinter Plant Operations: Hazardous Emissions | SpringerLink
The chemistry of the raw materials is calculated to fit BF slag formation requirements; under this operational guideline, iron ores together with fluxes (limestone, dolomite, serpentine) and reverts (mill scale, flue dust BOF OG sludge, etc.) are blended in the blending yard and conveyed to the sinter plant proportioning silos, where the coke breeze, sinter plant …
اقرأ أكثر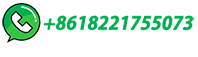
Design And Fabrication Of Iron Ore Sintering Machine | PDF
4. 4 Abstract The sintering process converts fine-sized raw materials, including iron, coke breeze, limestone, mill scale and flue dust, into an agglomerated product, sinter of suitable size for charging into the blast furnace. The raw materials are something mixed with water to provide a cohesive matrix, and then placed on a continuous, travelling grate called the …
اقرأ أكثر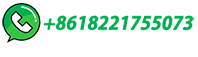
Microsoft Word
Second Sintering Plant was commissioned at 6th BF stage and started on 1st August 197 9 with one Sinter Machine of 75 sq. meter sintering area and rated capacity of 0.75 MT/Y. Subsequently three more machines were added to it making the total capacity of Sintering Plant-2 as 3.137 MT/Y. As the sinter
اقرأ أكثر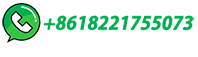
Reductants in iron ore sintering: A critical review
Iron-making plants, particularly those engaged in agglomeration processes like sintering; require alternative fuels to limit their CO 2 emissions to the environment. This review focuses on explaining the role that various reductants/fuels play in the sintering of iron ore and how those choices affect product quality and the surrounding ecosystem.
اقرأ أكثر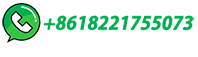
COMPARISON OF SINTER AND PELLET USAGE IN AN INTEGRATED STEEL PLANT 1
Hot metal production using sinter and pellets in the blast furnace is compared, considering aspects like; blast furnace productivity, environmental performance, solid waste management, slag-coke ...
اقرأ أكثر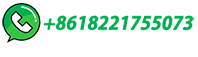
Lead Smelting
The production of primary lead is a process of extracting lead from lead sulfide concentrate by smelting. Smelting process mainly includes sinter plant–blast furnace route and direct smelting reduction process as shown in Figs. 2 and 3, including oxidation, reduction, and refining (Sohn and Olivas-Martinez, 2014).In sinter plant–blast furnace route, PbS is oxidized …
اقرأ أكثر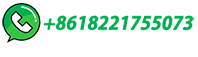