What is Sheet Metal Bending? A Comprehensive Guide for …
FAQ - Sheet Metal Bending . 1. What are the best sheet metal bending methods? The best sheet metal bending methods depend on the material, thickness, and the part's specific requirements. Common methods include: V-Bending: Suitable for high-precision bends, especially on thin to medium thickness materials.
اقرأ أكثر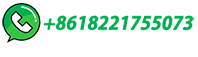
Top 5 Sheet Metal Design Formulas | Approved Sheet Metal
The K-Factor is a dimensionless value and typically ranges between 0 and 0.5 for most sheet metal materials and bending operations. The value depends on several factors, including material type, thickness, and bend radius. ... We use the Bend Deduction formula every day at Approved Sheet Metal to compute our standard sheet metal bend gains chart.
اقرأ أكثر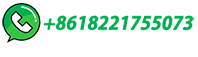
All About Sheet Metal – Materials, Standard Sizes & Forming …
Thickness Charts. Here are some examples of gauge thicknesses: Stainless Steel: Gauge 10: 0.1406 inches (3.57 mm) Gauge 18: 0.0500 inches (1.27 mm) ... Sheet metal bending is a key technique for shaping metal sheets into various forms. The bending process typically uses a press brake, a machine that clamps the metal sheet between a punch and a ...
اقرأ أكثر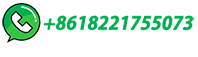
Sheet Metal Bending Radius: Full Guide Chart
Location: Home » News » Press Brake » Sheet Metal Bending Radius: Full Guide Chart. March 20, 2024. 134 views. Copy X Facebook LinkedIn Email Print. Sheet metal bending is a versatile field that allows for designs ranging from complex to simple to be created in a cost effective and efficient manner. As with all manufacturing processes and ...
اقرأ أكثر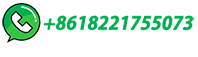
Minimum Bend Radius For Sheet Metal: Table & Calculator
How Manufacturers Use the Air Bend Force Chart for Sheet Metal Bending Switch 6061-T6 for 5052-H32 (bending), weight vs strength. Manufacturers use air bend force charts to determine the appropriate die V-opening, minimum flange length, and bending force required for specific sheet thicknesses and bend radii. Here's how the process works:
اقرأ أكثر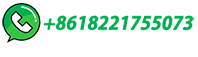
Air Bending Force Chart | Wilson Tool
Use this Air Bending Force Chart to help you select the correct V opening in your die to get the bend that you want and ensure your tool selection is safe.
اقرأ أكثر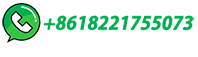
Sheet Metal Fabrication Design Guide
6 Sheet Stock Sizes and Gauge Lookup Chart 7 Stock Material Thickness Tolerances 8 Quoting Formats: 3D CAD and DXF Files ... bending or milled features. All flat sheet metal parts can meet a +/-0.005" (+/- 0.127mm) tolerance. ... Sheet metal parts are unique because they use common flat stock materials. The following
اقرأ أكثر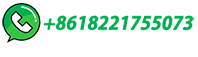
Bend Allowance Chart: Complete Guide
Whether you're working with simple cold-rolled steel or exotic alloys, understanding and accurately calculating bend allowance is crucial to achieving the desired results and understanding how sheet metal parts are …
اقرأ أكثر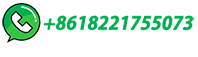
Sheet Metal Bending Guidelines Explained
The minimum sheet metal bending height should be calculated as 2 times the thickness of the sheet metal plus the bending radius, i.e., H ≥ 2t + R. As illustrated in the accompanying figure, if the bending height is too low, the …
اقرأ أكثر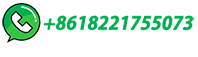
RECOMMENDED MINIMUM BEND RADII FOR 90 …
90-DEGREE COLD FORMING OF SHEET The radii listed are the minimum recommended for bending sheets and plates without fracturing in a standard press brake with air bend dies. Other types of bending operations may require larger radii or permit smaller radii. The minimum permissible radii will also vary with the design and condition of the tooling.
اقرأ أكثر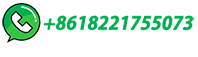
Sheet metal bending calculation basics
When a sheet metal part is bent, it physically gets bigger. The final formed dimensions will be greater than the sum total of the outside dimensions of the part as shown on the print—unless some allowance for the bend is taken …
اقرأ أكثر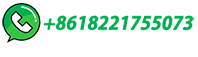
Bend Radii & Minimum Bend Sizes for Sheet Metal Design
It is most economical to use a single bend radius throughout the design, but if necessary, you can utilize multiple radii. Use this document to choose values that are both manufacturable and meet your needs. If you need help choosing a value, contact us at info@protocaseor 1-866-849-3911 and we can help. …
اقرأ أكثر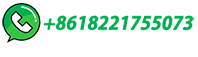
Minimum Recommended Bend Radius Chart from American …
Minimum Bend Radii: The minimum bend radius data shown in these charts is measured to the inside of the bend. The bend radii listed are standard minimum if manufacturing for aircraft and …
اقرأ أكثر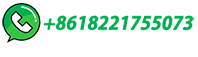
Understanding K Factor in Sheet Metal Bending: The Ultimate Guide
The K-factor in sheet metal bending is influenced by several key factors, including material properties, bending radius, material thickness, bending angle, and bending method. Material properties such as yield strength and elastic modulus significantly affect the K-factor, with softer materials generally having lower K-factors.
اقرأ أكثر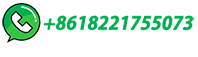
Sheet Metal Bend Allowance Calculator | Free To Use Tool
When bending sheet metal, precise calculations are crucial to achieve the desired results. Incorrect bend allowances can lead to material wastage and production delays. Our Sheet Metal Bend Calculator takes into account the material thickness, bend radius, bend angle, and K-factor to provide accurate bend allowance and bend deduction values.
اقرأ أكثر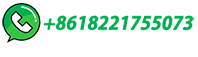
Bend Allowance – SheetMetal.Me
Unfortunately sheet metal bending is not always going to be the same in every shop. ... Sheet Metal Bend Allowance Chart (PDF) Sheet Metal Bend Allowance Chart (Excel) BEND ALLOWANCE; 8 Gauge: 10 Gauge: 12 Gauge: 14 Gauge: 16 Gauge: 18 Gauge: 20 Gauge: 22 Gauge: 24 Gauge: K factor: 0.33: K factor: 0.33: K factor:
اقرأ أكثر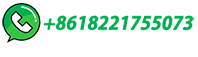
Bend Allowance Chart
Bend Allowance Chart K factor 0.33 K factor 0.33 K factor 0.33 K factor 0.33 K factor 0.33 K factor 0.33 K factor 0.33 K factor 0.33 K factor 0.33
اقرأ أكثر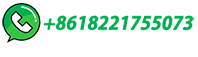
Sheet Metal Bend Allowance Chart
While the Sheet Metal Bend Allowance Chart is a valuable tool, it is important to consider the following tips and potential issues when using the chart: Material Variations: Different sheet metal materials may have varying ductility and springback characteristics. It is essential to consult the material supplier's recommendations and adjust ...
اقرأ أكثر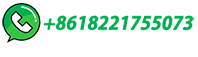
Sheet metal fabrication
A process where a piece of sheet metal is placed onto a die with a specific geometry and the punch presses into the material to form the sheet metal to the die. Bending sounds easy and straightforward but it can be more complex than expected. For example, if the desired bend is a standard rounded corner, a 45° V-die is used.
اقرأ أكثر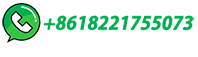
Sheet Metal Design Guidelines: Optimizing for Manufacturability
Features of sheet metal bending design ... The K-factor of your bending design should be chosen from a K-factor chart based on the material type, bend angle, and operation. It typically ranges from 0.25 to 0.50. 6. If your design has offset bends ( Z-shaped), Maintain flange length (on Both Sides)= 3 x thickness(t) 7.
اقرأ أكثر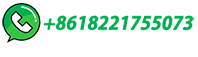
Air bending force chart
Air bending force chart for mild steel (Rm≈450 N/mm 2) Stainless Steel. Die opening V 4 6 7 8 10 12 14 16 18 20 25 32 40 50 ... Bending radius ir on the sheet metal; Press force F in KN / m; Tag`s. Exhibition; Machine; Laser; Sheet …
اقرأ أكثر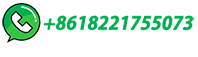
Press Brake Tonnage Calculator (Online & Free) | MachineMFG
For instance, if the sheet metal to be bent is mild steel, with a thickness of 4mm and a bending length of 3.2m, the theoretical width of the bottom die opening should be 8 times the thickness, which is 32mm. Input these figures into the calculator above (remember the units are in mm), and we get a value of 106.12 Ton. This means you'll need a minimum bending …
اقرأ أكثر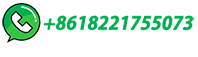
Sheet Metal Bending Calculation: Design Factors Explained
k-factor calculation In bending. In sheet metal bending, The K-factor is a constant used to calculate the amount of material needed for bending. It stands for the distance between the neutral axis and the working thickness of the material, which describes how the material is stretched or squashed in the region of the bend line.
اقرأ أكثر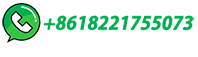
vol.3 PREPARATION FOR BENDING 1 | TECHNICAL GUIDE
Check the tonnage chart before Bending. The tonnage chart is always specified in the tool catalog, and is also displayed on the machine as a nameplate where it is easy to see. ... SHEARING METHOD AND WARPAGE TENDENCY BY SHEET METAL MACHINE) vol.12 TYPES OF BENDING SHAPES (HEMMING BENDING, STEP BENDING) vol.13 BENDING …
اقرأ أكثر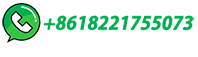
Sheet Metal Bend Allowance Explained in Detail
When a piece of sheet metal goes through the process of bending, its upper layer (with inside radius) is compressed and the lower layer (with outside radius) is stretched. Due to this tension and compression, the length of the …
اقرأ أكثر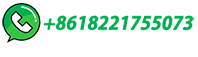
Applying Sheet Metal Bend Gains (Updated for 2024) …
Before a prototype becomes the complex structure an engineer designed it to be, it needs to be formed via bending, cutting, punching, and welding. ... Using Approved Sheet Metal's bend gains chart can streamline …
اقرأ أكثر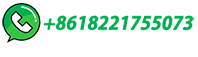
Air Bend Force Chart – SheetMetal.Me
An Air Bend Force Chart, or Force Chart breaks down a number of key components of sheet metal bending in an easy to reference format. Being able to read a bend force chart is crucial for any Brake Press operator and sheet …
اقرأ أكثر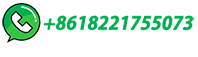
Sheet Metal Bend Radius: A Complete Guide to Precision and
Bending diagram Image credit: https:// Bending Direction. Sheet metal displays anisotropic behavior when being bent, and direction matters to prevent general manufacturing defects like cracks and tears during the bending process. If sheet metal is bent in line with the direction of the metal fibers, the likelihood of experiencing a crack or tear at the …
اقرأ أكثر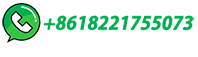
How to Design Bend Reliefs & Corner Reliefs for Sheet Metal Parts
More information on best practices for sheet metal bending. Depending on the shape of your part and location of your bend, you may need to include bend relief to avoid tearing or warping along the edges where your part transitions from flat to bend. Not all bends will require relief, but when they do you can look up or calculate the size you ...
اقرأ أكثر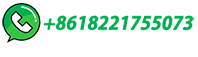
Sheet Metal Bending Design Guide: Rules, Tips & Considerations …
Bending is a fundamental process in sheet metal working that involves deforming a metal workpiece into a desired shape by applying force between two tools by a press brake: an upper tool (known as a punch) and a bottom tool (known as a V-die). Bending can improve a part's structural integrity by increasing part stiffness, redistributing stress within a part, and help …
اقرأ أكثر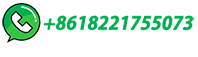