Effect of Dry- and Wet-Milling Processes on Chemical, …
of dry- and wet-milled rice starches isolated from dry- and wet-milled rice flours. MATERIALS AND METHODS Rice starch preparation Three varieties Thai milled rice were analyzed: low amylose (Pathum Thani 1), medium amylose (RD 7) and high amylose (Leuang 11). Two milling processes, dry-milling and wet-milling, were used to prepare rice flour ...
اقرأ أكثر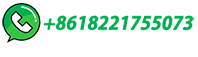
Wet Milling vs Dry Milling
Milling is essentially an intermittent machining process. This would cause the temperature at the cutting edge to fluctuate continuously between high temperatures (around 1000 °C) and low temperatures. What follows is which is better wet milling or dry milling (wet milling vs dry milling).
اقرأ أكثر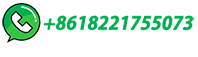
Effect of wet and dry milling on the functional properties of whole
The effect of wet and dry milling on the functional properties of whole sorghum grain flour (SF) and extracted kafirin were assessed. White sorghum landrace was used to prepare two SFs by wet milling (SF1) or dry milling (SF2) and to extract their respective kafirins SK1 and SK2. Protein contents of SK1 and SK2 were 90.07 and 94.23%.
اقرأ أكثر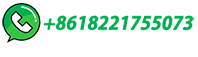
Facts At Your Fingertips: Wet and Dry Milling
Wet mills use liquid as their working fluid, whereas dry mills use gas. Common mill types and their characteristics are shown in Table 1. This one-page reference provides a brief review of wet milling versus dry milling.
اقرأ أكثر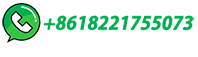
Effects of Dry-Milling and Wet-Milling on Chemical, Physical and
Rice (Oryza sativa L.) is a staple food for more than half of the world's population (Xiang et al., 2015).Rice is consumed mostly as cooked grains, and it is also processed to puffed rice (Joshi et al., 2013) or flour and starch that can be further formulated into a variety of products.In order to successfully incorporate rice or its flour into products, the properties of the …
اقرأ أكثر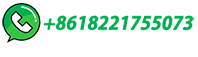
Dry ball milling and wet ball milling for fabricating copper–yttria
Yttria-reinforced copper matrix composites were prepared by dry ball milling (DBM) and wet ball milling (WBM), respectively, followed by spark plasma sintering (SPS). It is to determine which milling process is better for fabricating Cu–Y2O3 composites. It is found that Cu–Y2O3 composites synthesized by DBM exhibit better densification, mechanical and …
اقرأ أكثر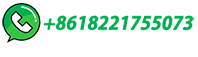
(PDF) Effect of Dry and Wet Ball Milling Process on Critical …
Optimized processing parameters were found to be 300 rpm in wet milling and 450 rpm in dry milling (average grain size of 760–800 nm, hardness of 1700–1720 HV30, and fracture toughness of 10.5 ...
اقرأ أكثر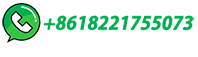
The Quest for Nanotechnology and the Evolution of Wet and Dry Milling
Dry-milled materials have the tendency to agglomerate after processing, or when later added to liquid, will also tend to agglomerate. This can be avoided when initially mixed with the liquid carrier and processed in a wet media mill. Wet milling encapsulates the dry particle, surrounding it with liquid and preventing re-agglomeration.
اقرأ أكثر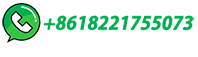
Nanoparticle preparation of pharmaceutical compounds via wet milling
One operational step can produce micronized or nanosized dry particles, making ultra cryo-milling a hybrid process that combines the benefits of both dry milling and wet milling in an aqueous medium. LN2 spontaneously evaporates at ambient temperature and pressure, therefore eliminating the drying procedure once the grinding process is complete.
اقرأ أكثر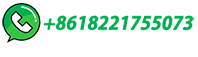
Wet Ball Milling Vs Dry Ball Milling
Wet ball milling processes produces smaller particles, compared to dry ball milling process. Wet ball milling allows easy introduction of surface active media having to do with the reduction of the required energy for the inhibition of aggregation …
اقرأ أكثر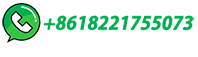
Atmosphere matters: The protection of wet ball milling instead of dry
The reasons of the optimal S/Fe molar ratio for S-mZVI/BC-wet preceded that of S-mZVI/BC-dry were that wet ball milling promoted more effective sulfidation, encouraged corrosion, and formed looser structure (Fig. 1). Therefore, considering the removal and economic efficiency, S: Fe molar ratio of 0.1 was chosen for further studies. ...
اقرأ أكثر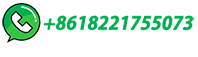
Dry and Wet Milling of Red Cowpea
Red cowpea flours, starch and protein were prepared using dry and wet processing methods. At optimum condition, dry dehulling with an abrasive dehuller gave 75% yield of dehulled seeds with 30% hull remaining and 18% cotyledon loss compared with 70% yield, 2% hull remaining and 20% cotyledon loss from wet dehulling of soaked seeds (8–10 h at 30°C) …
اقرأ أكثر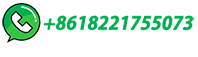
ABITHA FRANCIS drymilling and wet milling of corn | PPT
The document discusses the two main processes for milling corn - wet milling and dry milling. Wet milling is a more complex process that separates the corn kernel into its main components like germ, fiber, gluten, and starch. It uses steeping and grinding steps to extract these parts and produces co-products like corn oil, starch, and gluten meal.
اقرأ أكثر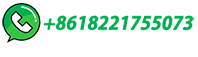
Dissolution of mechanically activated sphalerite in the wet and dry
Crystallite size calculation of the wet and dry mode milling after 180 min were performed by TEM and HRTEM analysis according to the Fig. 8. TEM images of the wet and dry milled sphalerite are depicted in Fig. 8 (a-b). To calculate the crystallite size, the particle frequency distribution was used in a specified range of size and the average ...
اقرأ أكثر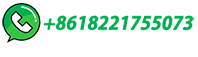
Flow chart of dry and wet milling of quinoa.
During dry milling, maize is ground between stones in a hand-driven plate mill, a hammer mill, or a powered plate mill on a larger scale. Before milling with a manual plate mill, the grain is ...
اقرأ أكثر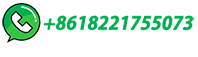
Wet and dry milling solutions. How they work and
have been built specifically for wet or dry milling. Indeed, we have applied our 30 years of experience to optimise the performance of both our dedicated wet and dry solutions. Hybrid composite Glass ceramics. Roland's dry milling machines are perfect for a host of applications. All these materials work perfectly with the dry milling process:
اقرأ أكثر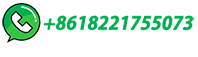
Wet vs. Dry Milling: Key Differences
The use of mechanical energy to break down particles through various mechanical forces including grinding media, pegs, rods, pebbles, and screens. When the material is pumped through the mill, the mill's components act on the solids in the mixture to tear them apart or crush them, further reducing them in size. The …
اقرأ أكثر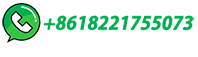
COMPARISON OF WET AND DRY STIRRED MEDIA …
COMPARISON OF WET AND DRY STIRRED MEDIA MILLING FROM ENERGETIC AND MECHANOCHEMICAL POINT OF VIEW Á.Rácz* 1), K. Bohács 1), F. Kristály2), É.Gregus 1) and G. Mucsi 1) 1 Institute of Raw Material Preparation and Environmental Processing, University of Miskolc, Hungary, 3515 Miskolc-Egyetemváros2 Institute of Mineralogy and Geology, …
اقرأ أكثر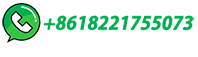
Impact milling of pharmaceutical agglomerates in the wet and dry …
After studying the wet milling and dry milling operations separately, the next set of experiments sought to investigate any interdependencies between the two milling steps. These experiments evaluated the impact of wet milling on the dry milling process. Wet milled and non-wet milled samples at 65% fluid level were tray dried and then dry milled.
اقرأ أكثر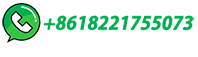
Effects of wet and dry ball milling on the
In this study, micron-sized particles of carbon biomass derived from coconuts were obtained by milling the biomass via wet and dry methods. The milling duration for both methods was 10, 15, and 20 ...
اقرأ أكثر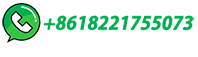
Wet and Dry Milling Equipment
Our conical mills are perfectly suited to both wet and dry applications. The versatility of the Uni-Mill means that the same machine can be used to mill wet and dry powders – providing a cost effective solution for many manufacturers.. Dry Milling. Conical mills are most commonly used for the particle size reduction and de-agglomeration of dry materials such as …
اقرأ أكثر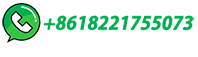
Milling of corn.ppt
17. Milling of Corn The basis of the maize milling process is the separation of the maize kernel into its different parts. Starch has been produced from corn for many years by two general procedures, namely 1. Dry milling 2. Wetmilling Both dry and wet milling procedures accomplish separation of the germ from which corn oil is obtained and removal of the hull …
اقرأ أكثر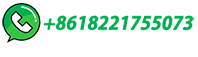
Effect of wet and dry milling on the functional properties of whole
The effect of wet and dry milling on the functional properties of whole sorghum grain flour (SF) and extracted kafirin were assessed. White sorghum landrace was used to prepare two SFs by wet milling (SF1) or dry milling (SF2) and to extract their …
اقرأ أكثر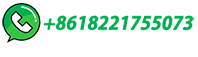
Planmeca PlanMill® 35 | Milling unit for wet and dry milling
Capable of wet and dry milling. With Planmeca PlanMill 35, you can easily switch between dry milling zirconia and wet milling a wide range of ceramic and composite materials. For dry milling, the unit is equipped with a suction system, which removes the dust from the system during the fabrication process.
اقرأ أكثر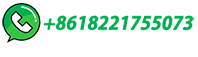
Dry Milling or Wet Milling: What's the Best Direction to
So, if all-ceramic production is going to increase – especially zirconia - let's take a look at the differences between each of them with respect to dry or wet milling as we head into 2016.
اقرأ أكثر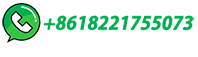
Influence of dry- and wet-milling processes on physicochemical
The molecular weight of both amylopectin from dry-milled rice starches (0.95-1.7 ¥ 10 7 Da) was lower than that of wet-milled rice starches (1.11-1.90 ¥ 10 7 Da), suggesting that the dry-milling ...
اقرأ أكثر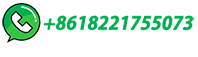
A comparative study of dry and wet top-down milling approaches …
Jet milling is a dry top-down technique used in the pharmaceutical industry for the micronisation of particles [[9], [10], [11]].Micronisation is achieved by using a continuous grinding gas that creates a vortex in a milling chamber where particles repeatedly collide with newly injected particles, inducing breakage.
اقرأ أكثر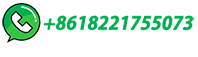
Comparison of Wet and Dry Milling
Wet milling and dry milling are two widely investigated and utilised milling techniques within the field. Wet milling is characterised by the utilisation of a liquid medium throughout the milling procedure, whereas dry milling is predicated on the absence of a liquid medium (Loh et al., 2015).
اقرأ أكثر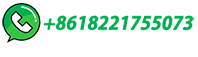
Overview of the dry milling versus wet milling
Wet milling involves soaking the material in water or other liquids to make it easier to process, while dry milling involves grinding the material into a powder or fine particles without …
اقرأ أكثر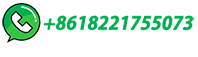
Differences Between Wet and Dry grinding: Why …
While there are various techniques, they can be broadly categorized into two main methods: wet and dry grinding. The distinction between these techniques is primarily based on the presence or absence of liquid during the processing.
اقرأ أكثر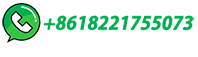