Fluidized magnetization roasting of refractory siderite-containing iron
Stable magnetite can be obtained through maghemite reduction only at low temperature. The optimal fluidized magnetization roasting parameters included preoxidation at 610°C for 2.5 min, followed by reduction at 450°C for 5 min. For roasted ore, weak magnetic separation yielded an iron ore concentrate grade of 62.0wt% and an iron recovery rate ...
اقرأ أكثر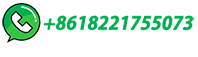
Recovery of iron from pyrite cinder by suspension magnetization
The results showed that the raw ore for PyC has an iron grade of 56.47%, and after SMR-magnetic separation, magnetic concentrate with an iron grade of 63.24% and an iron recovery of 95.05% could be achieved under conditions of a roasting temperature of 480°C, a reductant concentration of 30% (CO: H 2 = 1:3), a roasting time of 20min, 1200Oe ...
اقرأ أكثر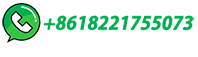
(PDF) Separation and recovery of iron from a low …
In this study, a process of magnetizing roasting followed by low-intensity magnetic separation (MR-LMS), which is used to separate and recover iron from a low-grade carbonate-bearing iron ore...
اقرأ أكثر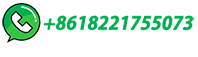
Effect of roasting time on the separation and recovery …
In this study, a process of magnetizing roasting followed by low-intensity magnetic separation (MR-LMS), which is used to separate and recover iron from a low-grade carbonate-bearing iron...
اقرأ أكثر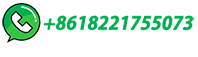
[PDF] Feasibility of Applying a Rotary Kiln to Roast Vanadium in
We investigated the feasibility of roasting domestic vanadium titanium-magnetite ore in a rotary kiln as a pretreatment to effectively leach vanadium from the ore. Such feasibility analyses should consider the various mechanisms and aspects of rotary kilns such as structure, thermal fluid flow, heat/mass transfer, solid (ore particulate) bed behavior, and reaction/operation optimization.
اقرأ أكثر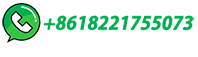
Characterization vis-á-vis utilization of blast furnace flue dust in
The results discussed so far suggest that an iron ore concentrate of ∼63% with an iron recovery of ∼66–67% is obtainable with BFD to ore ratio of 0.4 under two sets of temperature and time that are: (850 °C 90 min) and (950 °C, 30 min). Understandably, under these conditions, magnetite conversion is at its highest level.
اقرأ أكثر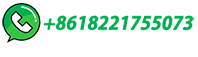
Mineralogy of Magnetite Concentrate and Its Preparation for
A comprehensive investigation was undertaken on the mineralogy of ordinary magnetite concentrate to achieve ultra-pure iron concentrate. Various analytical methods, including chemical analysis, X-ray fluorescence spectroscopy, optical microscopy, scanning electron microscopy–energy dispersive X-ray spectroscopy (SEM-EDS), and mineral liberation …
اقرأ أكثر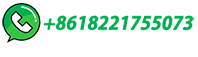
Recovery of vanadium from titaniferous iron ores
the means whereby silicate minerals can be removed prior to salt roasting the ore for vanadium recovery are similar to those used for the processing of titaniferous iron ores for ilmenite recovery and magnetite recovery. Magnetic concentration is common for removing magnetite, and gravity methods are common for separating titaniu minerals from ...
اقرأ أكثر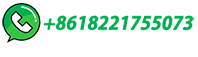
Phase transformation assisted reduction roasting of low-grade …
In general, in the reduction roasting process, iron oxides such as hematite (Fe 2 O 3) and goethite (α-FeO (OH)) are reduced to the magnetite (Fe 3 O 4) phase under the …
اقرأ أكثر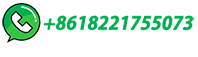
A novel approach of utilizing the waste biomass in the …
The RHC biochar was the most effective, having the highest GCV value, and helped to roast the iron ore sample more than other biochar. In set 7, experiment 32 has the highest iron ore grade among all the four biochars at 72.93%, and recovery was 77.34%. In set 7, most iron ore recovery was 88.22% in of RHC.
اقرأ أكثر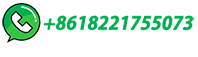
Beneficiation of low-grade, goethite-rich iron ore using microwave
At respective optimum conditions, the titano-magnetite ore (O1) could yield an iron concentrate having a grade of 62.57% Fe with a Fe recovery of 60.01% while the goethitic ore (O2) could be ...
اقرأ أكثر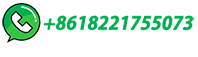
Physical separation of iron ore: magnetic separation
An iron ore concentrate containing 64.6% Fe can be produced using this flow sheet from a run-of-mine ore containing 51.1% Fe at a mass yield of 69.6% to the iron ore concentrate, an iron recovery of 88.0%, and a tailings grade of 20.2% Fe. 2.
اقرأ أكثر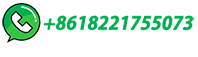
Reduction roast and magnetic separation of oxidized iron ores for …
However, the recovery of iron in the process is above 90%, which affords a reasonable opportunity for cleaning operations. ... The amenability of Aswan iron ore to reduction roast-magnetic separation concentration was investigated on a laboratory scale. ... C. L., Hematite, Magnetite Grain Growth in the Reducing Roast. XI IMPC, Cannes, May 26 ...
اقرأ أكثر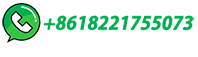
tungsten recovery from magnetite ore
tungsten recovery from magnetite ore futuretechsystems The iron ore and reduced product were in iron ore recovery magnetite roast . The Enrichment of Stale Tailings of Bom gorhon Tungsten . It allows increasing the recovery rate of two or more to Professor Kulyov The enrichment of stale tailings of Bom Gorhon tungsten ore .
اقرأ أكثر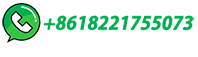
Iron ore magnetite processing
Iron ore magnetite processing (LIMS, MIMS, WHIMS, Davis Tubes) The increased worldwide demand for steel in recent decades has led to an increase in the exploitation of magnetite iron ore deposits as an alternative to hematite DSO ores. Magnetite concentrate is a higher-grade product than hematite and very desirable as a smelter feed.
اقرأ أكثر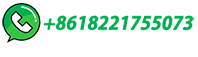
Maximizing the recovery of fine iron ore using magnetic …
Maximizing the recovery of fine iron ore using magnetic separation . M. Dworzanowski. Anglo American Mining and Technology, Anglo Research, South Africa ... In this study, magnetite is the iron ore mineral of economic interest. To generate a sample for evaluation purposes, 6 kg of diamond drill core was crushed and then milled to 80% -150 µm ...
اقرأ أكثر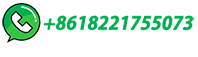
Beneficiation of low-grade, goethite-rich iron ore using microwave
A magnetizing roast to reduce iron oxyhydroxides [e.g. goethite, FeO(OH)] and carbonates (e.g. siderite, FeCO 3) to magnetite, followed by a magnetic separation process, is …
اقرأ أكثر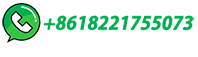
Recent Advances in Magnetization Roasting of Refractory Iron …
Thus, the iron recovery reached 82.2%, and the iron content in the magnetic concentrate reached 62.1% (Li et al. 2010 ). Rath et al. explored the process of simultaneous roast-
اقرأ أكثر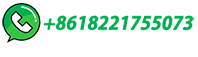
Optimal Recovery of Iron Values from a Low Grade Iron Ore using
Best set of optimal recovery and iron ore grade acquired are 87.44% and 72.46% with operating conditions at (a) roasting temperature — 850 °C, (b) roasting time — 30 min, and (d) magnetic ...
اقرأ أكثر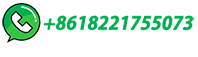
Iron Recovery from Iron Ore Tailings by Direct Hydrogen …
Flotation and roast reduction/magnetic separation are the main processes investigated to recover iron from the tailings ... in the form of magnetite, with a recovery rate of 94.60% using CO as reducing agent and a roasting temperature of ... but no work was found using pure hydrogen and magnetic separation for iron recovery from iron ore tailings.
اقرأ أكثر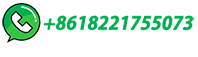
Utilization of low-grade BHQ iron ore by reduction roasting …
conditions, maximum grade and recovery of final magnetite concentrates were found to be 66.42 and 93.53%, ... ≥600°C. It is also undesirable to roast iron ore at a higher
اقرأ أكثر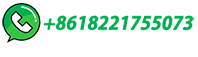
(PDF) Magnetization Roasting of Refractory Iron Ores: …
In this study, an innovative suspension magnetization roasting (SMR) technology was developed and utilized for the recovery of iron from a typical refractory iron ore.
اقرأ أكثر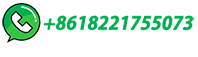
Effect of roasting time on the separation and recovery of iron
In this study, a process of magnetizing roasting followed by low-intensity magnetic separation (MR-LMS), which is used to separate and recover iron from a low-grade carbonate-bearing iron ore ...
اقرأ أكثر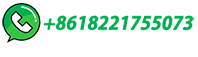
Towards sustainable processing of vanadium-bearing titaniferous
Optimal iron recovery is achieved at an initial temperature of 1000°C. ... ilmenite and vanadium-bearing magnetite. Magmatic ore deposits associated with ultramafic and mafic rocks span most of ...
اقرأ أكثر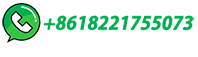
A new approach for recovering iron from iron ore tailings using
An increase in the roasting temperature accelerated the reduction of hematite and siderite to magnetite, resulting in its easier recovery during the LIMS process. However, the magnetite over-reduces to wustite (FeO) at an excessive high roasting temperature (Eq. ... A pilot-scale experiment on iron recovery from iron ore tailings using pre ...
اقرأ أكثر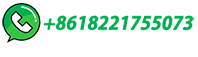
Investigation on beneficiation of goethite-rich iron ores using
iron values by upgrading to a high-grade product suitable for pelletisation and sintering. The received ore contains 58% Fe, 7.82% silica, 4.26% alumina and 4.97% loss on ignition.
اقرأ أكثر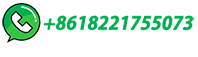
A comparative study of vanadium recovery from titaniferous …
and the roast-leach process for vanadium primary production (Gupta and Krishnamurthy, 1992; Mefos, 2006; Steele and Wilson, 1966; Moskalyk and Alfantazi, 2003; Taylor et al., 2006; Roskill, 2010). In terms of cumulative vanadium recovery, the roast-leach process is reported to be superior to the smelting process (Goso et al., 2016). The ...
اقرأ أكثر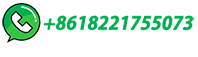
On controllability of fluidized bed reduction of iron ore by CH
Li et al. [25] obtained an iron concentrate with 67 % iron grade and 86 % iron recovery from another iron tailing through magnetization roasting in a 30 %CO-containing reductive gas flow of 0.6 L/min at 600 °C for 20 min. Yuan et al. [26] obtained an iron concentrate with 58 % iron grade and 91 % recovery from a brown iron ore through roasting ...
اقرأ أكثر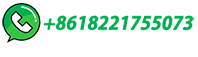
Recovery and separation of iron from iron ore using …
RECOVERY AND SEPARATION OF IRON FROM IRON ORE USING INNOVATIVE ... completely converted into magnetite by a gas mixture of 4 Nm 3/h CO and 1 Nm 3/h N 2 at roasting temperature of 540 °C for
اقرأ أكثر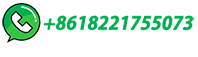
ore recovery magnetite roast
Recovery and separation of iron from iron ore using - doiSerbia,In this investigation, a pilot-scale fluidized magnetization roasting reactor was introduced and used to enhance magnetic …
اقرأ أكثر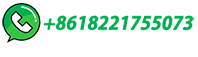