Extraction of Iron from its ores, Iron dressing, Reduction
Extraction of iron or its metallurgy is the process of obtaining this metal in a form where it can be put to practical use, and this process of extraction consists of three stages: Ore dressing, Reduction of ores and Iron production.
اقرأ أكثر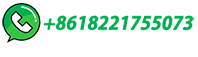
Extracting Copper from Ore: A Step-by-Step Guide
In this process, the ore is crushed and ground into a fine powder, then mixed with water to form a slurry. Air is injected into the slurry, creating bubbles. ... This step partially oxidizes iron and sulfur, creating sulfur dioxide (SO₂) gas and iron silicate slag. Separation: The denser matte sinks to the furnace's bottom, while the ...
اقرأ أكثر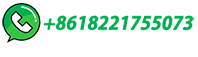
Extraction of iron
The calcium oxide formed reacts with the silicon dioxide, which is an impurity in the iron ore, to form calcium silicate. This melts and collects as a molten slag floating on top of the molten iron, which is tapped off separately. …
اقرأ أكثر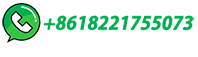
How is iron extracted from ore in an industrial process?
Iron ore extraction typically occurs in a blast furnace using coke as a fuel and limestone as a flux. First, the ore is heated with a reducing agent, such as coke, which removes the oxygen from ...
اقرأ أكثر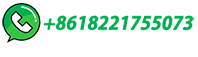
Separation and Recovery of Iron from Vanadium Titanomagnetite …
Abstract Vanadium titanomagnetite (VTM) is a complex polymetallic symbiotic mineral dominated by iron, titanium, and vanadium. Iron extraction from VTM is an issue for the utilization of Vanadium titanomagnetite concentrate. In this work, flotation method combined with magnetic sorting was proposed to separate and recover the iron resources from VTM. The …
اقرأ أكثر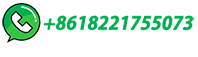
The reactivity of metals Extraction of metals from their ores
The method used to extract a given metal from its ore depends upon the reactivity of the metal and how stable the ore is. In each case the metal ions in the compound gain electrons to form atoms ...
اقرأ أكثر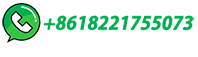
what is the process of separating iron from ore called
Process Of Separating Iron From Its Ore The process of separating a metal from its ore is known as smelting..to the high tech, and are applied to a variety of materials, including aluminum, iron and copper..these three steps are actually part of one general process used in smelting .
اقرأ أكثر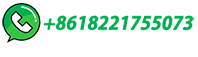
What is the process of extracting iron from its ore?
The extraction of iron from its ore is a long and subdued process, that helps in separating the useful components from the waste materials such as slag. The process begins with the …
اقرأ أكثر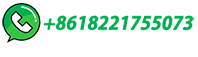
(PDF) Flotation of Iron Ores: A Review
The aim of this paper is to provide a well-detailed, well-referenced source for the current status of iron ore flotation, and thus provide a useful guide to its future development and to further ...
اقرأ أكثر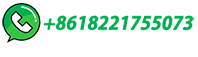
Lesson Explainer: Extracting Iron | Nagwa
In this explainer, we will learn how to describe the extraction of iron from its ore in the blast furnace. Extraction of iron is arguably one of the most important industrial processes on Earth. Iron is used to make steel, which is …
اقرأ أكثر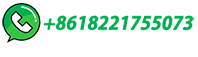
Extracting Metals: Process, Meaning & Methods
For example, in the extraction of iron from its ore, the balanced chemical equation Fe2O3(s) + 3CO(g) -> 2Fe(s) + 3CO2(g) can be broken down to show how the reactants and products contribute to the overall process. ... Concentration: Also known as ore dressing, this is a physical process aimed at separating the ore from its surrounding gangue ...
اقرأ أكثر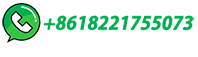
Mineral processing | Metallurgy, Crushing & Grinding | Britannica
mineral processing, art of treating crude ores and mineral products in order to separate the valuable minerals from the waste rock, or gangue. It is the first process that most ores undergo after mining in order to provide a more concentrated material for the procedures of extractive metallurgy.The primary operations are comminution and concentration, but there are other …
اقرأ أكثر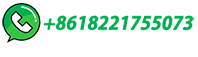
Extraction of Iron | Metallurgy | Blast Furnace and …
How is iron extracted from its ore? It's a long process which begins with Concentration through calcination roasting. Concentration removes the water …
اقرأ أكثر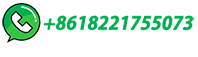
Concentration of Ore – Definition, Methods of Separation, Examples
Metal extraction is the process of extracting metal from its ore. The techniques for extracting metals from their ores and refining them are referred to as metallurgy. ... Metals are essential to industry and trade, such as copper, gold, and iron, which are found in the most valuable ore deposits. Ore is a solid substance containing minerals or ...
اقرأ أكثر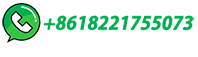
Extraction of Copper: Detailed Process
The process of extraction of copper from its ores and preparing copper metal or chemical compounds for use in various goods is known as copper processing. ... Copper is extracted from its ore by a series of …
اقرأ أكثر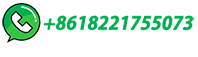
Extraction of Metals from Ores – Different Processes Involved
The frothed ore collects on the oil section whereas the impurities settle down in the water medium. Chemical Separation: One way of concentrating the ore is by chemical separation. For example, the separation of aluminium (Al) from the bauxite ore. This process of separating aluminium from the bauxite ore is also termed Bayer's Process.
اقرأ أكثر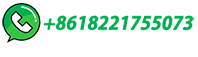
Extraction and separation of copper and iron from copper …
Iron was recovered from flotation tailings by deep reduction followed by magnetic separation process (at reduction temperature 1290 °C for 25 min; reductant blue carbon 15.9%; additive limestone 10%, soda ash 1.5% and binder 5%), and iron concentrate with an iron content of 92.6% and iron recovery of 91.33% was obtained.
اقرأ أكثر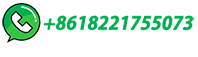
Froth flotation process and its application
The sulfide ore flotation process can be studied by both chemical and electrochemical phenomena considering the interfacial energies. A broad application of this process in industrial field is the ...
اقرأ أكثر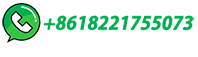
22.3: Metallurgy
Originally, the iron was collected in pools called pigs, which is the origin of the name pig iron. Figure 23.3.2: A Blast Furnace for Converting Iron Oxides to Iron Metal. (a) The furnace is charged with alternating layers of iron ore (largely Fe 2 O 3) and a mixture of coke (C) and limestone (CaCO 3). Blasting hot air into the mixture from the ...
اقرأ أكثر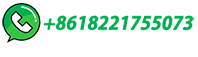
Extraction of Iron from Hematite
Iron is extracted in a large container called a blast furnace from its ore, hematite Modern blast furnaces produce approximately 10,000 tonnes of iron per day The process is demonstrated and explained below: ... Separation & Purification Techniques. 12.5 Identification of …
اقرأ أكثر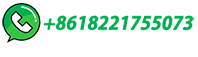
Principles of Iron Extraction | Methods & Processes Explained
The extraction of iron involves the reduction of iron ore, primarily hematite (Fe₂O₃), using carbon in the form of coke. This process occurs in a blast furnace, where coke acts as a reducing …
اقرأ أكثر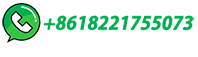
Optimization of iron and aluminum recovery in bauxite
Recovering iron and aluminum efficiently is the key route to utilize low-grade high-iron bauxite. Aiming to optimize the iron separating process and elevate both Fe and Al recovery ratio, three different Fe–Al recovery processes with different magnetic roasting (R), Bayer leaching process (L) and magnetic separation (S) orders were investigated. The studied processes …
اقرأ أكثر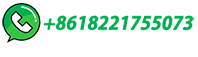
The Process of Making Iron: From Ore to Product
These chunks are then screened to separate the ore from waste material. Grinding. The crushed ore is then ground into a fine powder. This step is crucial as it increases the ore's surface area, making it easier to extract the iron during subsequent processes. ... In this process, the iron ore pellets are heated in a blast furnace to high ...
اقرأ أكثر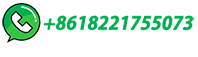
What is the process of extracting iron from its ore?
The extraction of iron from its ore is a long and subdued process, that helps in separating the useful components from the waste materials such as slag. The process begins with the crushing of the raw ore, which is the haematite. The ore is then concentrated by removing impurities like soil etc. This process is called beneficiation.
اقرأ أكثر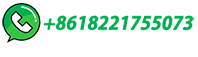
A critical review on metallurgical recovery of iron from iron ore
Fig. 2 illustrates the iron ore beneficiation process, particularly magnetic separation, resulting in the generation of inevitable tailings. Due to the characteristics of iron ores and the conditions during beneficiation, it is inevitable that approximately 2.5–3 tons of IOTs are generated for every 1 ton of iron ore concentrate produced [7].In 2019, the global annual …
اقرأ أكثر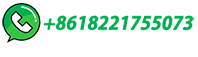
Developments in the physical separation of iron ore: Magnetic
This chapter introduces the principle of how low-grade iron ores are upgraded to high-quality iron ore concentrates by magnetic separation. Magnetite is the most magnetic of all the naturally ...
اقرأ أكثر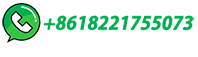
Methods for Separating Alloys: A Comprehensive Guide
The primary goal of smelting is to separate the metal from its ore in its pure form. This process typically involves a reducing agent, often carbon in the form of coke, which helps to reduce the metal oxides to their elemental metal state. Key Steps in Smelting. Preparation of the Ore: First, the ore is crushed and sometimes concentrated to ...
اقرأ أكثر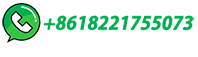
Pilot-scale recovery of iron from refractory specularite ore using
The mechanism behind this process enhances the magnetism of non-magnetic or weakly magnetic iron ore, combined with processes such as grinding and magnetic separation to achieve an effective separation of iron minerals from gangue minerals (Cao et al., 2021; Sun et al., 2023; Tang et al., 2022a; Xu et al., 2024).
اقرأ أكثر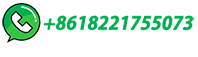
CK12-Foundation
Steps in the extraction of metals from their ores. Concentration of Ores. The very first step, which is the concentration of ore, involves the removal of gangue particles that can be achieved using gravity separation, froth floatation, magnetic separation, and leaching processes.. The gravity separation method is used when gangue particles are lighter than the ore.
اقرأ أكثر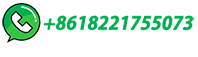