LECTURE NOTES ON Sponge Iron & Ferro Alloys
1930-1950s Saggers in Tunnel Kilns- Small Shaft Furnace- Rotary Kilns- Hogganas- Wiberg- Krupp & Lurgi- Coal Based Coal Based Coal Based 1950-1960s Static Reactors- ... 1995 OSIL supplied the technology to Llyods India for their sponge iron production plant at Chandrapur, Maharastra. The OSIL process uses a rotary kiln of 3.5mtr diameter and
اقرأ أكثر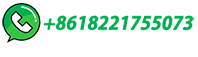
Sponge Iron
SIPL is operating 4 x 100 TPD Direct Reduced Iron Rotary Kilns for production of 2000 TPA Sponge Iron at Purulia, using the proven German SL/RN technology. Sponge Iron, also known as Direct Reduced Iron is produced from Hematite Iron ore (5 to 18 mm size) by removing the oxygen by direct reduction process using non coking coal as the fuel and ...
اقرأ أكثر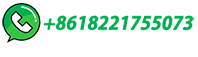
Chapter 1 Review of Sponge Iron Making Process Historical …
1930-1950s Saggers in Tunnel Kilns- Small Shaft Furnace- Rotary Kilns- Hogganas- Wiberg- Krupp & Lurgi- Coal Based Coal Based Coal Based 1950-1960s Static Reactors- ... sponge iron production plant at Chandrapur, Maharastra. The OSIL process uses a rotary kiln of 3.5mtr diameter and 84mtr long. The output of this plant is 300 tons
اقرأ أكثر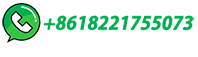
Sponge Iron Production by Calcium Carbonate, Sodium …
Keywords: Sponge iron; Tunnel kiln; Sodium carbonate; Barium carbonate; Calcium carbonate. Abstract Due to the high price of natural gas in the production of sponge iron, the overall cost of production is also high in gas methods. Coal methods are an appropriate alternative to gas methods, in which anthracite coal is used to produce sponge iron.
اقرأ أكثر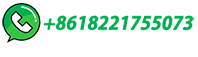
Iron
Sponge iron powder . The Höganäs process is a direct reduction method for production of sponge iron powder using magnetite ore (Fe3O4) and carbon as raw materials. The reduction process takes place in a gas fired tunnel kiln at around 1200°C for 60 hours producing a sponge iron cake that is crushed, milled and
اقرأ أكثر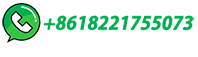
Sponge iron making process | PPT
The document discusses the inputs and process for manufacturing sponge iron in a rotary kiln. It describes the chemical and physical composition of iron ore, coal, and dolomite that are fed into the kiln. It then outlines the rotary …
اقرأ أكثر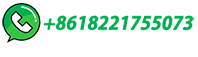
Tunnel Kiln
Production of sponge iron by Tunnel Kiln technology was developed in 1911 as Höganäs method. Now very popular, the technology has become an effective method for sponge iron production. With the Tunnel Kiln technology, it is …
اقرأ أكثر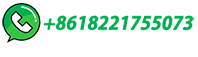
Optimization of Biomass Materials for use in the Sponge Iron …
1.5.2 The Sponge Iron Process The sponge iron process is a process for producing sponge iron, which is porous iron [1]. The raw material used for producing sponge iron is magnetite ore concentrate (Fe 3 O 4), which is the material that will become reduced [1]. The reduction mixture consists of coke and anthracite [1]. Figure 1.1 shows the ...
اقرأ أكثر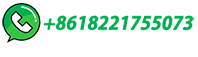
Reduction Efficiency of Iron Ore–Coal Composite Pellets in …
In the year 1908 use of tunnel kiln started for iron oxide reduction. This process was invented by Sieurin as Hoganas process . In 1954, more kilns came into operation in …
اقرأ أكثر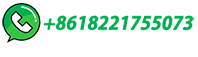
(PDF) i) Direct Reduced Iron: Production
In book: Encyclopedia of Iron, Steel, and Their Alloys (pp.pp 1082-1108) Chapter: i) Direct Reduced Iron: Production; Publisher: CRC Press, Taylor and Francis Group, New York.
اقرأ أكثر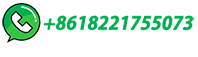
Mathematical Modelling of Sponge Iron Production in …
In this study, the goal is to apply the methodology to production of direct reduced iron (DRI) or sponge iron using the model developed by Runkana et al. (2010). Direct reduction is an alternative ...
اقرأ أكثر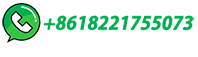
Production of Sponge Iron through Tunnel Kiln Process
Hi, you can read this article, please {Production of Sponge Iron through Tunnel Kiln Process}, by Swaren Bedarkar. Cite. Hadi Poorhosseinali. Isfahan University of Technology. Hi.
اقرأ أكثر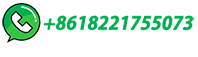
Tunnel Kiln
Production of sponge iron by Tunnel Kiln technology was developed in 1911 as Höganäs method. Now very popular, the technology has become an effective method for sponge iron production. With the Tunnel Kiln technology, it is possible to build small plants with low investment costs.
اقرأ أكثر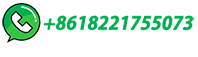
An optimized process of drying titanium pellets in a tunnel kiln
[Show full abstract] using Tunnel Kiln technology.To get optimal production, carried out the Process design and simulation of combustion furnaces both structural and fluid flow of heat (CFD).This ...
اقرأ أكثر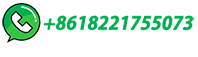
CN105331761A
The invention discloses a technology for producing sponge iron in a tunnel kiln. The technology mainly solves the problems that an existing tunnel kiln technology is low in capacity, high in energy consumption, large in loss and the like. Raw materials, a reducing agent and additives are mixed and subjected to ball milling to obtain a ball grinding material; the ball grinding material …
اقرأ أكثر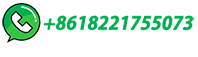
Sponge Iron
DRI, also known as sponge iron, is the product of reducing iron oxide in the form of iron ore and steel plant wastes into metallic iron, below the melting point of iron and typically in the range of 800–1200 °C. Iron oxide is charged into shaft furnace, rotary kiln, or fluidized beds in the form of pellet, iron ore lumps, or fines. The reduction takes place using gaseous reductants (CO + H ...
اقرأ أكثر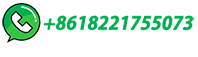
Tunnel Kiln
The tunnel kilns have the ability to convert Haematite and Magnetite sponge iron, and also work well with coal fines and mill scale. ... Coal consumption is reduced to 45% per batch of production. The tunnel kilns provide temperature conformity, and lower the fuel consumption. Design Features of GrowMech Tunnel Kilns . Consistent, high volume ...
اقرأ أكثر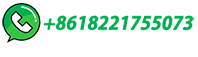
Conversion of Sponge Iron From Low Grade Iron ore And …
Abstract: The present investigation deals with the feasibility study of the process development for production of Directly Reduced Iron (DRI) using waste/low grade iron ore (slime), mill scale …
اقرأ أكثر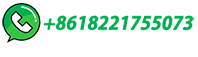
Sponge iron production in tunnel kiln
In sponge iron production plant by tunnel kiln method, after crushing and screening raw materials, iron ore, coal and limestone are mixed and charged in storage bins in certain ratios. By using an automatic charging system, raw …
اقرأ أكثر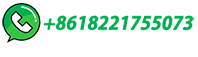
Tunnel Kiln Sponge Iron Turnkey Project
Tunnel Kiln Sponge Iron Turnkey Project, Find Details and Price about Direct Reduced Iron Direct Reduction Iron from Tunnel Kiln Sponge Iron Turnkey Project - Suzhou CMT Engineering Company Limited ... all of these help to reduce production costs; (5) Stable power supply and low noise during smelting; (6) Sponge iron is easy to handle and ...
اقرأ أكثر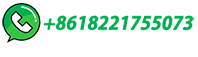
Coal based Direct Reduction Rotary Kiln Process – IspatGuru
The main raw materials for the production of DRI by the rotary kiln process are (i) sized graded iron ore or iron ore pellets, (ii) non-coking coal, and (iii) dolomite in small quantities to scavenge the sulphur. Iron ore of the right quality is the basic input for the coal based direct reduction process.
اقرأ أكثر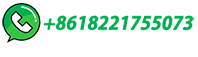
SPONGE IRON PRODUCTION FROM ORE -COAL …
In the year 1908 use of tunnel kiln started for iron oxide reduction. This process was invented by E.Sieurin as Hoganas process [3]. In 1954, more kilns came in operation in SWEDEN and …
اقرأ أكثر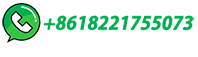
Reduction Efficiency of Iron Ore–Coal Composite Pellets in Tunnel Kiln
In order to explore the efficacy of iron ore–coal composite pellets over ordinary green pellets, indurated pellets, briquettes as well as standard charging of material in the form of concentric layers of iron ore and coal fines, or their mixture, these pellets were tested at 1,150 °C in a 7 tons per day (7 tpd) pilot tunnel kiln. Reduction of iron ore coal composite pellets in tunnel ...
اقرأ أكثر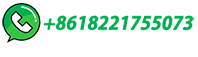
Sponge Iron Production Using Tunnel Kiln Report
CV Asri Keramik conducted a demonstration of producing sponge iron from iron ore using a tunnel kiln. The demo involved crushing iron ore, mixing it with coal to form briquettes, and firing the briquettes in a mini shaft kiln simulating a tunnel kiln. Over five trials with different iron ore sources, the demo successfully produced sponge iron in yields ranging from 2.5% to 63% of …
اقرأ أكثر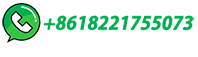
Sponge Iron Manufacturing
SPONGE IRON PRODUCTION USING TUNNEL KILN D E M O BRIEF REPORT ON TEAM VISIT TO CV ASRI KERAMIK LAB IN BANDUNG 1st Sept 270 37 3MB Read more. Citation preview. EXECUTIVE SUMMARY 1. Sponge Iron is iron ore reduced directly in solid state using coal gas, natrual gas or coal as reductants and is also known as Directly Reduced Iron (DRI). …
اقرأ أكثر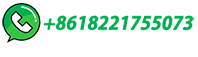
Services – Tunnel Kiln | Metcon Power Consultant & Engineers
We are a consultant agency dealing in industrial and green field projects in the field of DRI from Mill Scale through Tunnel Kiln technology, Iron & Steel making Industry, in various fields and application of extractive metallurgy, Waste Plastic Recycling Plant, Recovery of Zinc from SMS Flue Dust, automation of plant, non conventional Power.
اقرأ أكثر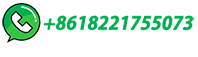
LECTURE NOTES ON Sponge Iron & Ferro Alloys
Sponge Iron & Ferro Alloys 8 TDR Process: It stands for TISCO Direct Reduction. The TISCO plant is also known as TATA Steel. TATA steel established a sponge iron plant in Keonjhar …
اقرأ أكثر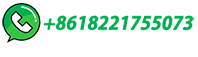
Reduction Efficiency of Iron Ore–Coal Composite Pellets in Tunnel Kiln
In order to explore the efficacy of iron ore–coal composite pellets over ordinary green pellets, indurated pellets, briquettes as well as standard charging of material in the form of concentric layers of iron ore and coal fines, or their mixture, these pellets were tested at 1,150 °C in a 7 tons per day (7 tpd) pilot tunnel kiln. Reduction of iron ore coal composite pellets in tunnel kiln ...
اقرأ أكثر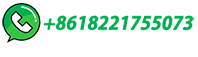
| Engineering & Consultancy
We have provided engineering and consultancy services for more than 500 Sponge Iron Kilns of different modules / capacities ranging from 15,000 TPA to 100,000 TPA. ... We have proficiency in converting cement kilns for Sponge …
اقرأ أكثر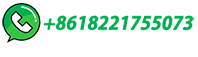
Tunnel Kiln: A Technoeconomic Route of Sponge Iron Making
The conventional coal-based sponge iron process (Rotary Kiln) used for the production of sponge iron (DRI- Directly Reduced Iron) requires high-grade ferruginous materials in the form of lump or pellets and quality coal. Moreover, these Rotary Kiln processes require pre-indurated pellets to sustain the mechanical abrasion during reduction and suffer from low thermal and chemical …
اقرأ أكثر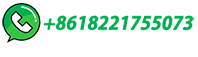