A new insight into iron ore oxidized pellets prepared by steel belt
Iron ore oxidized pellet is a superior furnace burden for the blast furnace process, possessing high iron grades, good strength, and excellent metallurgical properties [].Additionally, compared to the sintering process, the energy consumption of the pelletizing process is approximately 50% lower, with emissions of pollutants such as SO 2, NO x, and particulate …
اقرأ أكثر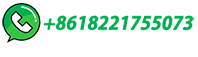
Iron Ore Pellets and Pelletizing Processes | PDF
Iron ore pellets are produced through a process called pelletizing where iron ore fines are mixed with additives, formed into balls, and then fired to increase strength. This process creates uniform feed for blast furnaces. The main stages are: raw material preparation, ball formation in discs, induration (heat hardening) through drying, firing, and cooling, and final screening and storage ...
اقرأ أكثر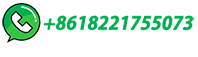
Iron ore pellets for blast furnace
Iron ore pellets are a man-made iron-riched ore. The pellet production method was invented in Sweden in 1912, and then began to be used in the United States in 1946 by shaft …
اقرأ أكثر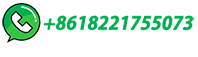
How Is Iron Ore Processed into Pellets?
Iron Ore Pellets are small balls of iron ores. These Pellets use the powder that is derived from extracting ore as a raw material. Iron Ore Pellets help in utilizing iron ore …
اقرأ أكثر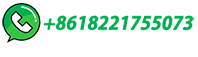
What is Iron Ore Pelletizing? How It Worked? An In-depth Look at …
Iron ore pelletizing is an essential industrial process that transforms powdery iron ore into uniform, robust pellets, serving as a premium feedstock for blast furnaces and direct …
اقرأ أكثر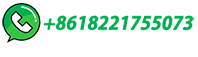
The effect of particle size on green pellet properties of iron ore fines
Iron ore pellet making process involves balling of green mix (containing iron ore fines, binder, limestone and coke) using rotating disk or drum to produce green pellets. ...
اقرأ أكثر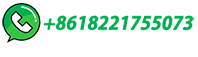
Iron Ore Pelletizing Process: An Overview
Iron ore and iron ore pellets are important sources of iron for manufacturing steel. The iron ore production has significantly expanded in recent years, owing to increasing steel demands in
اقرأ أكثر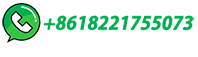
Converting iron ore into iron pellets
Iron ore pelletization is a key process in the steelmaking industry that helps improve the quality and efficiency of steel production. In this process, iron ore is powdered and then converted into small, round iron pellets using various methods such as wet or dry pelletization.
اقرأ أكثر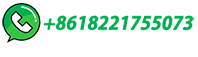
What Are Iron Ore Pellets?
Iron ore pellets are tiny spheres or pellets that are constructed by combining iron ore with other products in order to create materials that are easy to transport.
اقرأ أكثر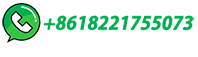
Reduction Behavior and Kinetics of Iron Ore–Charcoal Composite Pellets
Applications of carbon–neutral biomasses and derived charcoals have potential to reduce GHG emissions in the steel industry. The reduction behavior and kinetics of iron ore coal composite pellets for ironmaking have been studied extensively by several researchers. However, fast-growing and high-carbon yielding hardwood biomasses such as Acacia (W1), Albizia …
اقرأ أكثر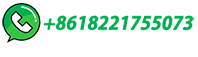
Iron Ore Pellets
What are particles? Iron ore pellets, like concentrates, are raw materials for the manufacture of iron, which is pulverized and ground into pellets ranging from 0 to 100 microns for supply to industry as pellet feed. Green pellets and hardened …
اقرأ أكثر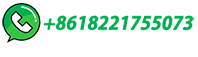
An industrial image processing-based approach for estimation of iron
Iron ore mining companies often refine the extracted ore to produce iron ore pellets, which have a uniformly high grade of iron oxide. Green pellets are produced primarily from crushed iron ore in a rotating pelletizing disk, and then baked in a furnace to produce hardened black pellets. Since iron ore pellets provide consistent and high ...
اقرأ أكثر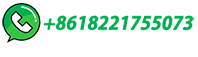
Iron Ore Pellet Production
A Perfect Storm for an Iron Ore Pellet Shortage. Benefits of utilizing iron ore pellets are extensive; in addition to lower emissions and a reduced requirement for coking coal, the use of iron ore pellets allows steel producers to lower …
اقرأ أكثر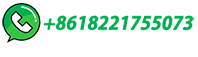
Granulation Behavior of an Iron Ore Sintering Mixture Containing …
Nowadays, as the demand for iron ore increases together with the depletion of high grade ore deposits, mining companies have been investing to produce iron ore concentrates, such as pellet feeds ...
اقرأ أكثر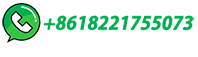
Fracture probability and fragment size distribution of fired Iron ore
Fig. 7 shows a comparison among median fracture energies (E 50i) of iron ore pellet sample D and of other steelmaking materials, namely an iron ore from Brazil [17] and a coking coal from Mozambique, which confirms the significantly higher strength of the pellets and their potentially lower amenability to mechanical degradation during handling ...
اقرأ أكثر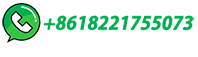
Functions and molecular structure of organic binders for iron ore
Organic binders of iron ore pellets were widely investigated in past decades because they do not contaminate the product. This paper mainly involves the functions and molecular structure of ideal organic binders for iron ore pelletization based on fundamental principles of molecular design, interface chemistry, polymer science as well as failure model of …
اقرأ أكثر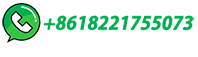
Our Products
IOC pellets are high quality with a clean chemistry, which helps to lower the carbon footprint compared to lower quality grades and forms of iron ore when used in the iron & steel industry. IOC's pellets and concentrate are high grade products with world leading low alumina and ultra-low phosphorus, beneficial to the iron & steel industry.
اقرأ أكثر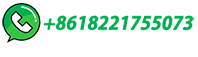
Iron Ore Pellets
Iron ore pellets, like concentrates, are raw materials for the manufacture of iron, which is pulverized and ground into pellets ranging from 0 to 100 microns for supply to industry as …
اقرأ أكثر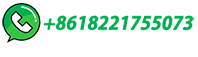
Fracture probability modelling of impact-loaded iron ore pellets
Iron ore pellets consist of a hard and brittle porous material and can be compared with materials such as rocks and ceramics. It is assumed that iron ore pellets have an elastic behaviour until fracture. In [3] a plastic constitutive model with linear isotropic hardening is used to model the iron ore pellet material behaviour. In this work the ...
اقرأ أكثر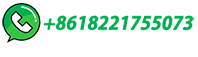
Physical Properties of Goethite Ore–Carbon Composite Pellets …
The rise in demand for iron- and steel-based products globally has resulted in the depletion of high-grade iron ores, high energy consumption, and CO2 emissions. The world is rich in low-grade ores that have not been exploited, and this study aims to develop a feed for cast iron production, goethite ore–carbon composite pellets. A pelletizing disc was used to make the …
اقرأ أكثر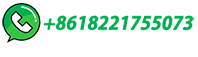
Chapter 3 Pelletization | PDF | Iron Ore | Porosity
Chapter 3 Pelletization - Free download as PDF File (.pdf), Text File (.txt) or read online for free. The document discusses the pelletization process used to agglomerate iron ore fines into pellets suitable for use in iron and steelmaking. It describes the steps involved, including mixing the iron ore concentrate with additives and binders, forming green pellets in a drum or disc pelletizer ...
اقرأ أكثر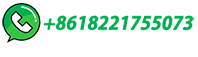
IRON ORE PELLET INDUSTRY
Iron ore fines specific consumption A MT/MT of pellet 1.1 Power specific consumption B KWh/MT of pellet 50 Iron ore fines price (64% Fe) C Rs./MT 9,700 Royalty, DMF, NMET D % of C 20% Cost of iron ore E= A*C*(1+D) Rs./MT of pellet 12,804 Other consumables and power cost @Rs. 7/kwh F Rs./MT of pellet 1,150
اقرأ أكثر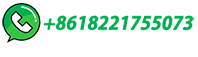
Features of the Iron Ore Pellets Structure Depending on the …
The iron ore pellets structure has some features determining their metallurgical properties. These include the nature of the porosity and the structure (defects) of raw pellets, which are largely inherited by calcined pellets. The influence of the mineral composition of the silicate binder decreases as the degree of enrichment of the ...
اقرأ أكثر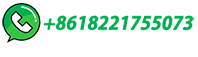
Iron Ore Pellets Industry Forecast to Reach USD 128.1 Billion by …
Steel production is an energy-intensive process, and coal is the main energy sourceNEWARK, Del, Jan. 21, 2025 (GLOBE NEWSWIRE) -- The global iron ore pellets industry is poised for robust growth ...
اقرأ أكثر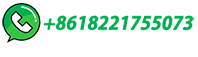
Iron ore pelletizing
Iron Ore Pellets are formed from beneficiated or run of mine iron fines. The iron is usually ground to a very fine level and mixed with limestone or dolomite as a fluxing agent and bentonite or …
اقرأ أكثر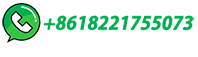
(PDF) Combustion Evaluation of Renewable Fuels for Iron-Ore Pellet
Induration (or sintering) of iron-ore pellets requires high temperature (~1300°C) which today is generating by burning fuel oil in the firing zone of the straight-grate plant (SG) or coal in the ...
اقرأ أكثر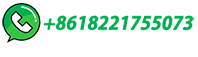
Three-dimensional characterization of porosity in iron ore pellets: …
Iron ore pellets, alongside lump ore and sinter, are fundamental raw materials for steel production, generated through the pelletizing process (Singh et al., 2023). The porosity developed during pellet manufacturing is a critical attribute. It enables internal gas flow, enhancing reducibility and process efficiency (Kim and Sohn, 2023 ...
اقرأ أكثر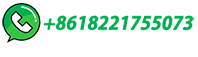
Determination of bulk properties and fracture data for iron ore pellets
Confined iron ore pellet compression tests are carried out using a cylindrical steel tube and two compressive platens. The material is confined by the tools and compressed axially in a press. The iron ore pellets continuum stresses and strains are derived, and the constitutive data required for the proposed material model are determined. 2.1.
اقرأ أكثر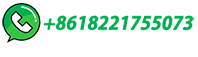
Iron Ore Pelletization: A Critical Review of Processes and
Iron ore pelletization is a central process in the steel industry, transforming iron ore fines into pellets that can be efficiently smelted in blast furnaces. As high-grade natural iron …
اقرأ أكثر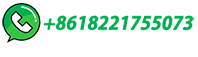