ENERGY BENCHMARKING
Lowest possible specific power consumption for a new plant with all the best technologies and equipment 91. Confederation of Indian Industry CII - Sohrabji Godrej Green Business Centre x. xi ... Figure 11 Thermal SEC of top cement plants in India 20 Figure 12 Specific heat consumption Breakup for plant 1 20. Confederation of Indian Industry ...
اقرأ أكثر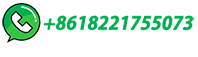
Selection of AC Induction Motors for Cement Plant Applications
Next is the determination of the available power voltage. The cement plant operator, process equipment supplier or engineering consulting firm must determine the most effective power source, taking load hp and amp values of the entire system into consideration. The Hz rating is determined by the power system available at the site.
اقرأ أكثر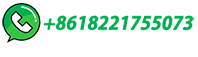
Cement Plant Process and Instruments Used | PPT
4. Limestone Quarry and Crushing Plant The major raw material for cement production is limestone.The limestone most suitable for cement production must have some ingredients in specified quantities i.e., calcium carbonates, silica, alumina, iron, etc.. Quarrying is done through drilling and subsequently, using heavy earth moving equipment such as …
اقرأ أكثر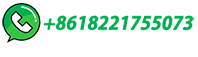
WASTE HEAT RECOVERY POWER PLANTS IN CEMENT …
Based on the experience of the cement/ captive power plants, this paper deals with the various issues involved in decision-making, as well as in implementation of WHRPP in cement industry. ... Heat balance (per kg. of clinker) for a typical cement plant, is depicted in Table - 1: 5-Stage Preheater 6-Stage Preheater Description Kcal / Kg % Kcal ...
اقرأ أكثر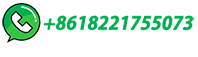
Financial Planning: How To Budget For A Cement Plant
Developing storage and distribution infrastructure: $1,000,000 - $10,000,000: Obtaining necessary permits and licenses: $50,000 - $500,000: Investing in research and development: ... In general, a cement plant may require between 10 to 50 acres of land, with the average cost ranging from $50,000 to $500,000 per acre, depending on the region and ...
اقرأ أكثر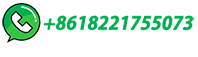
Waste Heat Recovery in India – Part 2
In a typical Indian cement plant, the potential generation of power from waste heat is estimated at roughly 20 – 25 kWh/t of clinker. The process goes through four basic stages: ... Where they substitute power from an external grid or a captive power plant, there is an additional advantage of reduced fuel consumption and lower CO 2 emissions ...
اقرأ أكثر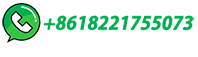
Clinker grinding technology in cement manufacturing
Clinker grinding technology is the most energy-intensive process in cement manufacturing. Traditionally, it was treated as "low on technology" and "high on energy" as grinding circuits use more than 60 per cent of total energy consumed and account for most of the manufacturing cost. Since the increasing energy cost started burning the benefits significantly, …
اقرأ أكثر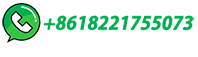
Operating and Maintenance of Electrostatic Precipitator in Cement
The cement process industries utilizing raw materials for the production of cement and these raw materials are burnt in the kiln at the temperature around 1400°C. During cement manufacturing process air gets pollute which includes particulate matter NOx, SOx., CO, CO2, hydrocarbons and other substances are released to the atmosphere. The burning of organic material such as …
اقرأ أكثر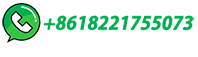
OPTIMIZING OPERATING COSTS TO IMPROVE …
An energy audit is required to evaluate the operation of a cement plant against the benchmark of similar wellmanaged - plants. After a detailed evaluation of the current raw materials and operating parameters, benchmarks are adjusted to correspond to the specific conditions of the plant. Raw materials are a major variable in this evaluation.
اقرأ أكثر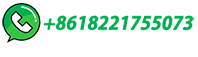
Power distribution for a cement plant expansion project
The power distribution requirements and the selection of drives for a cement plant expansion project are defined by the new process, the equipment features and ratings, the plant layout and the electric utility characteristics and requirements. These factors are considered in pre-feasibility studies, feasibility studies and basic engineering, prior to starting the final project …
اقرأ أكثر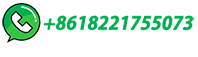
How the electrical systems in cement plants work
Power distribution design for cement plant. Power distribution system of a cement plant begins with the substation of the grid where power is received and ends with individual drives and points of usage.
اقرأ أكثر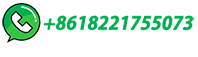
Cement Sector
4.3.3 Input-Output for a typical Cement plant 4 4.3.4 Normalisation Factor considered 5 4.3.4.1 Equivalent major grade of cement production 5 4.3.4.2 Calculation for Gate to Gate Specific Energy Consumption (SEC) 6 4.4 Methodology (Summary) 7 5. Target Setting in Cement Plants 7 5.1 Grouping of Cement plants 7 5.2 Energy Consumption Range 8
اقرأ أكثر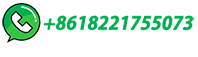
The essentials of electrical systems in cement plants | EEP
Power distribution system of a cement plant begins with the substation of the grid where power is received and ends with individual drives and points of usage. It is a large network consisting of elements like: distribution transformers, MV/LV control panels, individual distribution switchboards and motor control …
اقرأ أكثر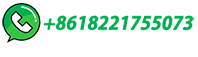
Improving Energy Efficiency: Cement industry steps …
The figure below depicts the typical thermal energy distribution in a cement plant. Three technologies are used for generating power from waste heat. These are – steam Rankine cycle based, organic Rankine cycle (ORC) …
اقرأ أكثر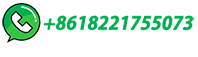
Unveiling Cement Manufacturing Plant Costs
Discover the secrets of cement manufacturing plant costs and optimize production for maximum ROI. ... and minimize environmental impact. By leveraging the power of AI, cement plants can achieve higher efficiency and productivity levels. ... Selling Expenses: Expenses associated with marketing, distribution, and sales should be considered when ...
اقرأ أكثر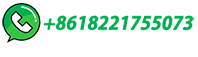
A typical arrangement of an ESP in the power plant [1] …
The effect of the baffle on flow distribution of an electrostatic precipitator has been presented by Sayema et al. (2015) for the coal based power plant. The result shows that residence time of ...
اقرأ أكثر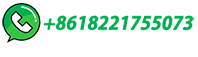
POWERING THE CEMENT INDUSTRY
On the cement plant's demand side, a flexible grinding approach could be used for raw meal production and cement manufacturing as power-intensive processes. The management of silo and production capacities could then be utilised similar to a battery and to make optimal use of excess renewable energy.
اقرأ أكثر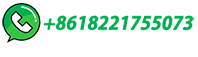
Innovations in power distribution in cement plants
A few of the many new product applications and protection methods first used in the decade between 1971 and 1981 for cement plant power distribution systems are surveyed. References noted in each brief discussion contain application details as well as equipment descriptions, ratings, and application advantages of the innovations discussed. Transformers: Transformer …
اقرأ أكثر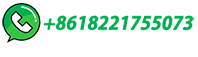
CONSTRUCTION ASPECTS OF CONTAINMENT …
2. SOME SPECIAL ASPECTS OF STRCUTURES FOR NUCLEAR POWER GENERATION . The heart of a Nuclear Power project is the Calandria and it is housed in a Reactor Building typically with a double containment system. Hence the most significant structure for a nuclear power plant is the Reactor Containment Structure.
اقرأ أكثر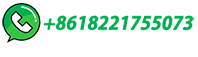
Power Consumption of Cement Manufacturing Plant
At present, the average level of unit power consumption of Cement Manufacturing Plants is at 33 kWh, in some Cement Manufacturing Plants, it could be 40 kWh higher than the average number.
اقرأ أكثر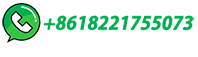
A Case Study on Evaluation of Energy Management System …
line, power distribution. These are the problem faced by the industries during the operation. To identify and have a holistic analysis of energy points and adopt new ... The Typical Cement factory for the study, situated in Tamil Nadu, India, is an ... 9 27 MW Captive Power Plant 2005 10 4000 TPD FLS Cement Plant 2006
اقرأ أكثر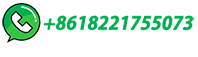
The Cement Plant Operations Handbook
The Cement Plant Operations Handbook is a concise, practical guide to cement manufacturing and is the standard reference used by plant operations personnel worldwide. Providing a …
اقرأ أكثر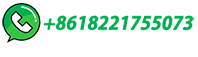
CAPTURING VALUE IN THE U.S. CEMENT INDUSTRY …
Cement was produced at 96 plants in 34 States, and at 2 plants in Puerto Rico. In 2019, sales of cement was valued at $12.5 billion, most of which was used to make concrete, with approximately 70%-75% of sales to ready-mix concrete producers, 10% to concrete product manufactures, 8% to 10% to contractors, and 5% to 12% to other customer types.
اقرأ أكثر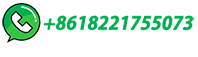
What is a Concrete Plant? (The Ultimate Guide)
Concrete plants are machines that mix and pour concrete. Learn more about the different types of concrete plants, how they work, and what to look for when buying one. ... The advantages of stationary plants include their larger size and power, which allows them to produce more concrete in a shorter period of time. Stationary plants also tend to ...
اقرأ أكثر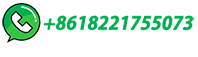
Decarbonization In Cement Plants With Waste Heat …
Enhances plant power reliability Improves plant competitive position in the market Lowers plant specific energy consumption, reducing greenhouse gas emissions (based on credit for reduced central station power generation or reduced fossil-fired captive power generation at the cement plant) Reduces auxiliary power consumption of a cement process.
اقرأ أكثر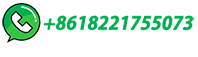
IEEE Recommended Practice for Cement Plant Power …
This document has been developed as a recommended practice for electrical distribution systems in cement plants with the objective of satisfactory equipment utilization, …
اقرأ أكثر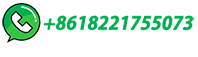
The Comprehensive Guide to Cement Plant Costs: An …
6. Cement Mill. The cement mill grinds the clinker to a fine powder, which is then mixed with gypsum to form cement. Equipment: Ball mills, vertical roller mills. Technical Specifications: Ball Mills: 10-30 tons/hour capacity, 500-1500 kW …
اقرأ أكثر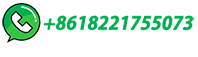
Cement Grinding
Chemical analysis of cement, generally on hourly basis. Product fineness, Blain surface and 45-micron residue. Cement SO3, % Grinding aid usage, grams/tonne Cement moisture, % Production rate, tonnes/hour Operating hours as run factor in % Specific power consumption (SPC) kWh/tonne. Specific Wear rate, g/t (checked during maintenance of mills)
اقرأ أكثر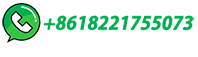
IEEE Recommended Practice for Cement Plant Power Distribution …
The continuing expansion and modernization program in the cement industry has placed an increasing importance on the cement plant power distribution system. Increasing plant capacity accompanied by larger kilns, grinding mills, crushers, and the increasing use of automatic controls has placed greater stress on the adequacy and reliability of the distribution system. Safety, …
اقرأ أكثر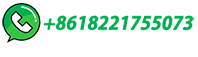
Cement Sector
4.3.3 Input-Output for a typical Cement plant 4 4.3.4 Normalisation Factor considered 5 4.3.4.1 Equivalent major grade of cement production 5 4.3.4.2 Calculation for Gate to Gate Specific …
اقرأ أكثر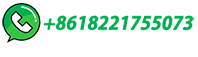