Operation at High Pellet Ratio and Without External Slag Formers
A high amount of pellets was balanced with high basicity sinter. An improved blast furnace operation is shown when operating at ultra low slag volume and without external slag …
اقرأ أكثر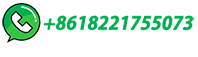
Reduction of Iron Ore Pellets, Sinter, and Lump Ore under …
gasandiron oxides. Herein,thereducibilityoftheiron ore pellet, sinter,andlump ore in the BF shaft are focused on. The experiments are conducted isothermally with a blast furnace simulator (BFS) high-temperature furnace at four different temperatures (700, 800, 900, and 1000 C) for 300min. The experimental atmosphere consists of CO, CO 2,H 2,H ...
اقرأ أكثر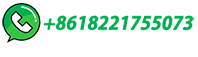
Reduction of Iron Ore Pellets, Sinter, and Lump Ore …
A blast furnace (BF) is the dominant process for making iron in the world. The BF is charged with metallurgical coke and iron burden materials including iron ore pellets, sinter, and lump ore. While descending in the BF the …
اقرأ أكثر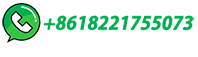
Blast Furnace Performance Under Varying Pellet Proportion
As a promising method to strengthen the blast furnace smelting and to realize reduced fuel operation, high-proportion pellet charging has become the practice of BF ironmaking. Use of pellet gives rise to uniform bed permeability in comparison with iron ore or sinter. This leads to better gas–solid contact resulting in higher productivity at reduced coke and fuel rate. …
اقرأ أكثر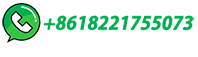
Optimum Pellet Basicity Desirable for Blast Furnace Operation
The stability of blast furnace process depends upon the quality of raw materials charged into the furnace. Among iron-bearing materials, pellets are an important feed material for the blast furnace operation. However, pellets exhibit swelling inside the blast furnace due to the high temperature inside the furnace, which causes dissociation of pellets and if swelling index is not controlled ...
اقرأ أكثر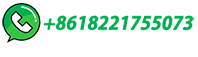
High lump use in the blast furnace – implications for sinter …
proportion of sinter, pellet and lump in blast furnaces around the globe [1-5]. The average lump proportion in Chinese blast furnaces is only around 10% [1], however, much higher lump proportions
اقرأ أكثر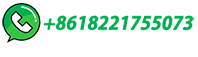
Influence of blast furnace pellet proportions on environmental …
The utilization of a high proportion of pellets in blast furnace enhances the reducing of the emission of CO 2 and other pollutants, such as SO 2, NO x, dioxin, during the ironmaking process, thereby contributing to environmentally sustainable and low-carbon ironmaking.The influence of pellet proportions on the pollutants and greenhouse gas emissions from blast …
اقرأ أكثر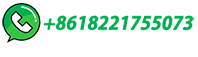
Hydrogen affection on softening and melting behaviours of high …
As the Al 2 O 3 content increasing in iron ore, some problems presented in blast furnace (BF) processing, such as worsened burden permeability and slag viscosity. Injection of H 2 may improve the permeability and reduce the CO 2 emission of BF, because of its less density and higher reduction potential when temperature is higher than 820 °C. Therefore, the …
اقرأ أكثر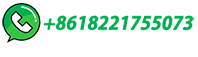
Iron ore pellets for blast furnace
Such a fine concentrate cannot be processed by the sintering process, so the pellet production method was adopted. Raw material preparation. Raw material preparation includes crushing, dehydration and conditioning. ... Alkaline and flux pellets have good metallurgical properties for blast furnace operation. Due to the addition of limestone or ...
اقرأ أكثر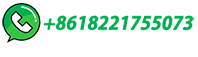
Investigating the Effect of the Iron Ore Pellet Addition on the
The efficient operation of a blast furnace requires burden materials with high softening temperatures and a narrow softening–melting range. This leads to the formation of a thinner cohesive zone in the lower part of the furnace, which improves permeability. In this study, softening–melting tests were conducted on pellets with different levels of basicity, combined …
اقرأ أكثر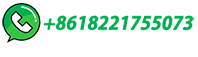
Modelling of blast furnace ironmaking process based …
The blast furnace operation model is constructed on the digital twin model construction platform, and the accuracy of the proposed model is demonstrated by experiments. ... The ore stream consists of pellet stream …
اقرأ أكثر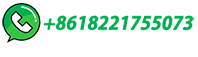
Magnesium-containing pellet regulating blast furnace ferrous …
MgO participates in all stages of sintering, pelletizing, and blast furnace ironmaking, and synergistically optimizing the distribution of MgO in ferrous burden can effectively enhance the interaction within the ferrous burdens and optimize the softening–melting properties of the mixed burden. Magnesium-containing pellets mixed with low-MgO sinter or mixed with …
اقرأ أكثر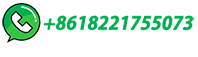
Improvement of Technical and Economic Performance of Blast-Furnace
Abstract One of the main methods to intensify blast-furnace smelting is to improve the quality of the sintered raw materials. The article presents the study results of the influence of the composition and metallurgical properties of various Mikhailovsky GOK pellets introduced into the blast-furnace charge based on the technical and economic indicators of the blast-furnace …
اقرأ أكثر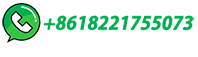
Influence of Sinter and Pellets on Blast Furnaces Operation
Results of the analysis of physical-chemical properties of sinter and pellets are presented. It shows that at BF transition to operation with high proportion of acidacid pellets in furnace …
اقرأ أكثر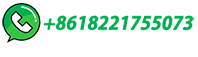
A comparative study of pellets, sinter and mixed ferrous burden
Effect of nut coke addition with ferrous burden (pellet and sinter mixture) is experimentally investigated under simulated blast furnace conditions. Nut coke mixing degree was varied (0, 20 and 40 ...
اقرأ أكثر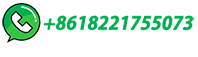
Blast Furnace Performance Under Varying Pellet Proportion
based on the effect observed in the blast furnace operation. Keywords Blast furnace Burden Pellet Burden distribution Gas permeability Gas efficiency Above burden probe Working index 1 Introduction The blast furnace (BF) is a counter-current gas–solid chemical reactor in which iron-bearing materials, namely iron ore, sinter and pellet and ...
اقرأ أكثر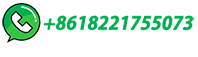
Effect of Pellet Proportion and Charging Sequence on Burden
The utilization of a high pellet ratio in blast furnace smelting represents a pivotal strategy for achieving green and low-carbon ironmaking, which can improve raw material quality, reduce energy consumption, and decrease CO2 emissions. In this study, the impact of pellet proportion and charging sequence on the burden distribution was investigated using the …
اقرأ أكثر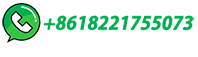
A comparative study of pellets, sinter and mixed …
The physicochemical behaviour of pellets, sinter and its mixture (60% pellet:40% sinter) is investigated under simulated blast furnace conditions in the reduction, softening and melting (RSM) apparatus.
اقرأ أكثر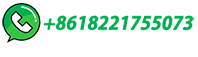
All Pellets Operation in Kobe No. 3 Blast Furnace under …
sive coal injection in a bell-less blast furnace based on the relationship between changes of various phenomena and blast furnace controllability with a hope to contribute to further improvement of operational flexibility. 2. Concept of Shifting from Sinter Operation to Pellet Operation 2.1. Comparison of Pellet and Sinter
اقرأ أكثر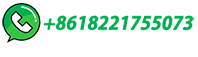
Proportion of sinter/pellet and iron ore in burden mixture.
Dilband iron ore is inappropriate for blast furnace operation due to its excessive silica and alumina contents [5], which generate operational problems in smelting, such as creating more slag ...
اقرأ أكثر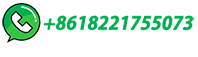
Understanding Pellets and Pellet Plant Operations
These pellets are suitable for blast furnace and direct reduction processes. Pelletizing differs from sintering in that a green unbaked pellet or ball is formed and then hardened by heating. ... It is difficult to adjust the drum operation for varying raw material conditions. The operation, however, is stable for uniform raw material conditions ...
اقرأ أكثر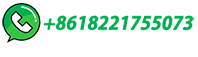
Blast Furnace Performance Under Varying Pellet …
As a promising method to strengthen the blast furnace smelting and to realize reduced fuel operation, high-proportion pellet charging has become the practice of BF ironmaking. Use of...
اقرأ أكثر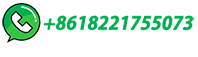
Exploring a new path of green and efficient utilization of sinter
Efficient utilization of sinter return fine is an important measure to reduce cost, increase efficiency, save energy and reduce emission. A new path of green and efficient utilization of return fine was proposed to produce composite pellets. The metallurgical properties of composite pellets under the condition of hydrogen-rich blast furnace were studied. The …
اقرأ أكثر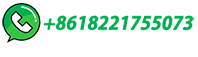
(PDF) Optimizing Gas Distribution in High Pellet Blast Furnaces
Gas distribution control under high pellet blast furnace (BF) burden operation is more difficult than with sinter due to low angle of repose, high rolling characteristics and layer collapse tendency. ... Additionally, burden profile control in the blast furnace throat is easier with sinter compared to pellet. However, due to non-availability of ...
اقرأ أكثر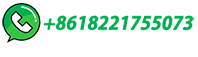
Review of pellets and blast furnace slag research progress: the …
High pellets operation is a developing direction in the future. The function of blast furnace slag system cannot be ignored. In order to balance the MgO content in blast furnace slag and improve the metallurgical properties of pellets in the high pellets ratio operation, the research on MgO-bearing pellets is necessary.
اقرأ أكثر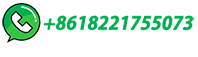
Optimization of four-component furnace burdens with hydrogen …
The conventional furnace burden comprises sinter, pellet, and natural lump ore [6].Nonetheless, conventional furnace burdens, particularly sinter, necessitate more coke consumption during production, leading to high carbon emissions [7].Industrial trials of metallized pellet blast furnace ironmaking have been conducted and demonstrated technically feasible [8].
اقرأ أكثر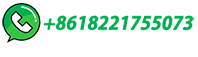
(PDF) COMPARISON OF SINTER AND PELLET USAGE IN AN
Effects of pellet ratio on the burden movement and distribution
Segregations of sinter and pellets were discussed based on the actual multi-ring burden matrix in a practice. In order to solve the urgent problem of energy conservation and …
اقرأ أكثر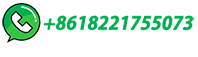
Blast Furnace Operation
A key component of the low-temperature blast furnace operation is to reduce the fuel rate significantly by lowering operating temperatures by 150–200 °C particularly in the thermal reserve zone [43].Consequently, the kinetics of the major blast furnace reactions must be increased so that production rates at lower operating temperatures are the same as for the traditional …
اقرأ أكثر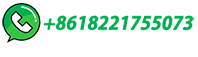
High-chromium vanadium–titanium magnetite all-pellet
High-chromium vanadium–titanium magnetite (HVTM) is a crucial polymetallic-associated resource to be developed. The all-pellet operation is a blast furnace trend that aims to reduce carbon dioxide emissions in the future. By referencing the production data of vanadium-titanium magnetite blast furnaces, this study explored the softening-melting behavior of high …
اقرأ أكثر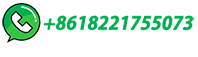
Effects of pellet ratio on the burden movement and distribution
Pellet tends to accumulate near the center of the blast furnace, with a segregation index reaching 0.8 in this region. Adjusting the burden ratio has a more pronounced effect on the segregation of sinter. This work provides theoretical support for charging optimization in blast furnace operation.
اقرأ أكثر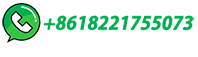