Introduction to Iron ore Pellets and Pelletizing processes
Raw material preparation – During the process for pelletization iron ore concentrate from iron ore beneficiation plant is dried and heated to around 120 deg C. The dried material is fed to the ball mill for grinding. ... Formation of …
اقرأ أكثر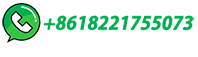
Study on the Induration Cycle During Pelletization of …
Indian blast furnaces are fed with lump iron ore (10 - 40 mm) and sinter as burden. Sinter is a prepared burden, where iron ore fines of size -10 + 0.15 mm are agglomerated using mainly flux and coke. Iron ore fines of less than 0.15 mm are not utilized in sintering technology and hence are mostly discarded at mines during processing as slime.
اقرأ أكثر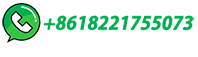
Iron Ore Pelletizing Process: An Overview
The iron ore pelletizing process consists of three main steps: Pelletizing feed preparation and mixing: the raw material (iron ore concentrate, additives—anthracite, …
اقرأ أكثر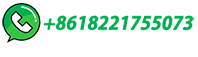
–– Iron Ore Pelletization Iron Ore Pelletization …
This was the first iron ore pelletizing plant installed for Wuhan Iron & Steel Company Equipment Specifications : Traveling Grate – 5664 mm x 69500 mm Rotary Kiln – 6858 mm diameter x 45720 mm long Annular Cooler – 21945 mm x 3657 mm Plant Commissioning : March 2006 Iron Ore Feed Material: Combination of 80% Hematite and 20% Magnetite
اقرأ أكثر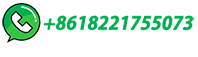
Iron Ore Pelletizing Essential in Meeting Future Steel …
Iron ore pelletizing, or balling, is the process of transforming fines into spherical granules anywhere from 8 – 16mm in size via tumble-growth (agitation) …
اقرأ أكثر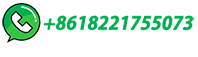
Review of Organic Binders for Iron Ore Agglomeration
During iron ore agglomeration or pelletization, moist iron concentrate particles and flux materials are rolled into balls with the aid of a binder (Figure 1). Balls tumble and grow in …
اقرأ أكثر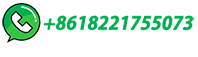
Iron ore pelletizing
Both drums and discs ball the ore to about 9-16mm size. Drums typically have very high recycle rates so have a screening circuit to screen out undersize and oversize pieces to be put back through the drum.
اقرأ أكثر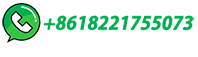
Exploring Low-Grade Iron Ore Beneficiation Techniques: A
The beneficiation of low-grade iron ores is a key research and development topic in the mineral processing industry. The gradual exhaustion of high-grade iron ore reserves, and rising consumer iron and steel demand globally necessitate efficient low-quality iron ore beneficiation to meet steelmaking quality requirements. This comprehensive review explores …
اقرأ أكثر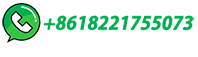
Iron Ore Pelletization
Iron ore must go through a lengthy pre-processing stage before it can be pelletized – a series of steps that work to beneficiate and concentrate low-grade ores. This process varies depending on the ore source, but typically involves various stages of crushing and grinding to reduce the size of the iron ore. …
اقرأ أكثر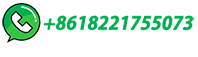
Iron Ore Pelletizing Disc | Products | CVIC | Iron Ore Pellet Balling
Balling Disc, Balling Drum, Disc Pelletizer, iron ore pelletizing disc, balling pelletizer, pan granulator, pivot base, discs. Iron Ore Pelletization, Iron Ore Pelletizing, Iron Ore Pellets Screening Equipment/Solutions, Iron Ore Pellets Handling Equipment/Solutions, Iron Ore Pellets Roller Screen/Feeder, Iron Ore Pellets Reciprocating Belt Conveyor, Iron Ore Straight Grate …
اقرأ أكثر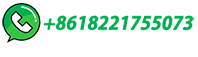
Iron Ore Pelletizing Process: An Overview
The iron ore pelletizing process consists of three main steps: 1. Pelletizing feed preparation and mixing: the raw material (iron ore concentrate, additives anthracite, dolomite and binders are …
اقرأ أكثر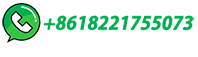
New Paradigms for Iron Ore Pelletization | SpringerLink
Thus, in iron ore pelletization, class C and class F fly-ashes may both undergo pozzolanic reactions. Fly-ashes which do not meet ASTM C618 may still be useful as pellet binders, so long as they are pozzolanic. ... This mixed concentrate was then pelletized in the laboratory balling drum. The laboratory pelletization process starts by allowing ...
اقرأ أكثر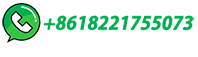
Iron Ore Balling Drums
Iron ore pelletizing plants rely on high-capacity balling drums to agglomerate ore fines and concentrates into pellets ranging from 8 – 16 mm for optimal performance in the blast furnace. Pelletizing iron ore products in a balling drum offers the following benefits:
اقرأ أكثر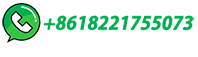
CVIC | Iron Ore Pelletization Solutions | Roller Screen | Belt …
CVIC Inc. - Leading Supplier for Iron Ore Pellet Screening Solutions, Iron Ore Pellet Belt Conveyor Solutions, Iron Ore Pellet Roller Screen/Feeder, Iron Ore Pellet Reciprocating Belt Conveyor, Wide Belt Conveyor, Undersize and Oversize Belt Conveyor, Balling Disc/Pelletizer, Straight Grate Pellet
اقرأ أكثر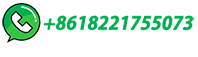
Pelletization of iron ore fines with parameter optimization …
methods against the conventional ones. 11The iron ore pellets produced through Pelletization operations are used in the Blast Furnace (BF) for production of iron and in DRI for sponge iron production.12,13 The parameters which affect the Pelletization process are moisture content, drum or disc inclination, fineness of feed, speed of drum or ...
اقرأ أكثر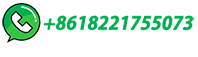
Pelletizing Plant Equipment & Process Development
ROTARY DRUM DRYERS & COOLERS. As a wet process, pelletizing typically requires a drying step. This is frequently carried out in a rotary dryer, a high-capacity dryer that utilizes a cascading motion to dry pellets, while also …
اقرأ أكثر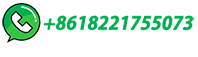
Advances in Sintering and Pellet Technology
Amongst various processes used in agglomeration, sintering and pelletization are widely used in the iron ore industries. About 70% of the blast furnace feed is reporting from the sintering processes. The objective of iron …
اقرأ أكثر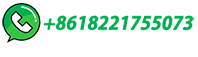
Iron Ore Pelletizing Process: An Overview
The idea of rolling moist fine ore in a drum to form balls and then drying and firing it was first patented by A. G. Andersson in Sweden in 1912. Further development was performed to bring
اقرأ أكثر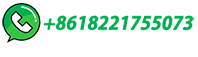
EFFECT OF SIZE DISTRIBUTION AND WATER CONTENT …
pelletization of iron ore has been found to markedly increase the efficiency of the blast furnace operation. This is due to the spherical shape and close ... Drum Pelletizer – It is a steel drum open on both ends. Its length to diameter ratio varies in the range 2.5 to 3.5. The typical value of the diameter is 2-3m
اقرأ أكثر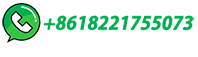
A review of binders in iron ore pelletization
In pelletizing, iron ore, water and a binder are balled in a mechanical disc or drum to produce agglomerates. Bentonite is the most widely used binder. ... Bentonite is a predominant binder used in iron ore pelletization. However, the presence of a high content of silica and alumina in bentonite is considered undesirable for ironmaking ...
اقرأ أكثر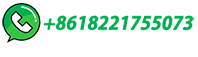
Iron Ore Balling Drums
Robust balling drums for green balling in iron ore pelletizing plants. As a leader in rotary equipment, all FEECO balling drums are engineered around the unique characteristics of iron …
اقرأ أكثر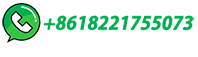
The Iron Pelletizing Process
When leaving the drum, the pellets are screened, and all pellets with too small a diameter are fed back to go through the drum once more. Oversized pellets are crushed and recycled. ... Therefore, the iron ore pelletizing process may be described as a chain of several sub-processes which may depend highly upon each other's performance.
اقرأ أكثر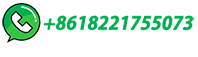
Humic Substance-based Binder In Iron Ore Pelletization: A Review
They can be used as binders in iron ore pelletization mostly in the form of salt, such as sodium humate and amine humate via extraction from lignite coal. ... 2017, the pelletizing test with MHA was also conducted in the lab, and the procedure was similar to the regular drum pelletizing procedure. Previous research showed that with a 0.6 wt ...
اقرأ أكثر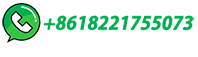
Iron Ore Pellet
The Direct Reduction of Iron. Thomas Battle, ... James McClelland, in Treatise on Process Metallurgy: Industrial Processes, 2014. 1.2.2.2 Agglomeration of Iron Ore. The three major forms of iron used in ironmaking are pellets, lump, and sinter. The major change in the past 50 years has been the development of cost-effective pelletization technology allowing pellets to be a …
اقرأ أكثر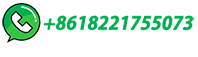
Use of Boron Compounds as Binders in Iron Ore Pelletization
1. IRON ORE PELLETIZING The main raw material in iron-steel industry is iron ore. Iron ores can be classified as high grade and low grade in terms of their Fe content. High grade iron ores which can be used directly in the blast furnace to produce metallic iron are not abundant in earth's crust to supply the need of iron-steel industry.
اقرأ أكثر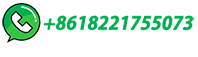
(PDF) IRON ORE PELLETIZING PROCESS
The mechanism of chemisorptions and compound molecule bridged linkage by organic complex bentonite to improve the pelletization of iron ore concentrates was demonstrated by the determination of X ...
اقرأ أكثر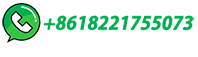
What Are Iron Ore Pellets and How to Make Them?
What are iron ore pellets? Iron ore pellets are spheres of typically 8-16 mm to be used as feedstock for blast furnaces. They contain 64-72% iron and additional materials, which can adjust the chemical composition and …
اقرأ أكثر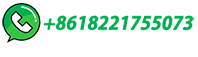
Pelletization
The pelletization process is the primary consumer of binders in the iron ore industry. The selection of an appropriate binder type and dosage is of critical importance in producing good quality pellets at a reasonable price. Binders accomplish two …
اقرأ أكثر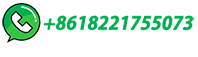
Iron Ore Pelletizatton Layering Mechanism
Pelletization is the unit operation of agglomerating moist particulate materials by tumbling in horizontal rotating drums or inclined discs. Pelletization has extended the life of iron ore industry by enabling the treatment of low grade iron ores which are available in large reserves through out the world.
اقرأ أكثر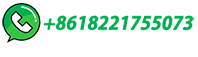
Bentonite binder effective strength (BESt) test for unfired iron …
long-term tests may not reflect the true behavior of bentonite during iron ore pelletization. Third, the tests are tedious and the results are often inconsistentfordifferent iron ore concentrates, laboratories and technicians. Fourth, some of the testing equipment is difficult to procure. Fifth, procedures are often difficult to
اقرأ أكثر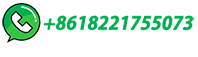