Flotation Reagents: Uses and Advantages in Ore Processing
The performance of froth flotation cells is affected by changes in unit load, feed quality, flotation reagent dosages, and the cell operating parameters of pulp level and aeration rates. In order to assure that the flotation cells are operating at maximum efficiency, the flotation reagent dosages should be adjusted after every change in feed ...
اقرأ أكثر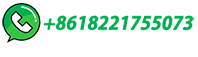
pH/ORP measurement Copper flotation process
A high pH is important in copper ore processing to maximize this mineral's flotation properties. Most copper ore slurries tend to be acidic. Plants typically add lime to the slurry in the mill or floatation circuit, increasing its alkalinity. A typical copper operation contains many flotation cells, often with a pH sensor in each cell.
اقرأ أكثر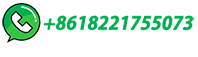
Modelling H2S gas generation in Copper/Molybdenum flotation cells
Even though gas extraction and scrubber systems play a fundamental role in the control and reduction of potentially dangerous H2S levels, currently there are no formal methods to estimate the H2S ...
اقرأ أكثر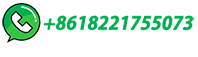
Copper Flotation: A Simple Guide to Efficient Copper Extraction
2. Flotation Cells. Flotation cells are large tanks where the separation process happens. The ore slurry is mixed with reagents, and air is blown into the mixture. Different designs of flotation cells exist, but they all serve the same purpose: to create bubbles that the copper minerals can attach to and float to the surface. 3. Air Bubbles
اقرأ أكثر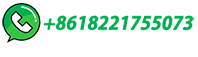
Copper Rougher-Scavenger Flotation Grade-Recovery
A modal examination of the products produced by the copper flotation rougher-scavenger circuit reveal important information regarding the limits to the efficiency of the process, imposed by mineralogy, fragmentation …
اقرأ أكثر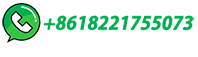
Copper Sulfide Flotation
Copper Sulfide Flotation Circuit. Beneficiation of Copper Sulfide by Flotation. Copper, due to the present world demand and price, is of foremost …
اقرأ أكثر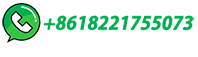
Copper Concentrate flotation Plant
Designed with multi-stage separation tanks, the copper ore flotation machine gradually completes the entire flotation process, optimizing it in a cascading manner. This design accommodates the changing properties of materials in …
اقرأ أكثر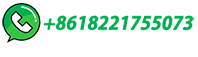
Copper Flotation: A Simple Guide to Efficient Copper Extraction
The key components in copper flotation, including reagents, flotation cells, air bubbles, and concentrators. Here are the essential parts involved in the copper flotation process: 1. Reagents. Reagents are special chemicals added to the slurry to help separate copper minerals from …
اقرأ أكثر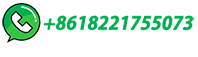
Copper recovery improvement with performance …
Annual copper production from the mine is expected to be 160,000 tonnes in concentrate form. Antapaccay's flotation circuit was commissioned in 2012. The operation was expanded in 2019 with a rougher line of five 300 m3 …
اقرأ أكثر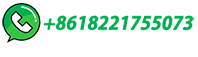
Copper recovery from copper slags through flotation enhanced by …
In previous years, numerous methods have been developed on the recovery and utilization of valuable metals in copper smelting slags, which can be summarized as pyrometallurgy [26], hydrometallurgy [27] and flotation [28].Through pyrometallurgy of copper slags, the precipitation of suspended matte (Cu 2 S) droplets is promoted into the matte layer …
اقرأ أكثر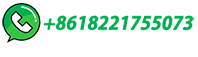
Extracting Copper from Its Ore: The Process Explained
Electrolytic Cell: The copper electrolyte is placed in an electrolytic cell, where an electric current deposits pure copper onto cathodes, ready for industrial use. Comparison of Extraction Methods Sulfide ores use froth flotation, roasting, smelting, and air blowing to produce high-purity copper, while oxide ores use heap leaching, solvent ...
اقرأ أكثر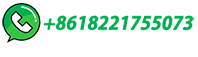
Solvent Extraction & Electrowinning (SX/EW) Plant Design
Electrolyte flow to the cells is kept between 2.7 to 3.0 l/m/m 2 of the cathode surface area. This represents a flow of 17.5 m 3 /h per cell. This flow rate ensures a high concentration of copper at the boundary layer. Cell manifolds along the bottom and length of the cells are critical for distributing the electrolyte.
اقرأ أكثر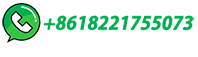
Design, Modeling, Optimization and Control of …
Copper content in the ore feed, collector dosage in the rougher and the scavenger flotation circuits, slurry pH in the rougher flotation circuit and frother consumption were selected as input parameters to estimate the copper …
اقرأ أكثر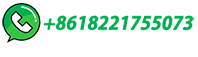
Flotation and Leaching Processes in Metallurgy
In decreasing order of importance, the factorial experimental results showed that the H 2 O 2, H 2 SO 4, NaCl, NaIO 3, and KI concentrations affect the copper extraction percentage. The highest copper extraction percentage (i.e., 60.6%) was obtained using a leaching solution containing the highest reagent concentrations. At these conditions ...
اقرأ أكثر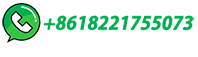
copper processing plant, copper flotation plant, copper …
Flotation is the common copper processing technology, which can be used for sulfide ore and oxide ore. The copper flotation plant usually includes following steps: crushing and screening, stage grinding and flotation, thickening and …
اقرأ أكثر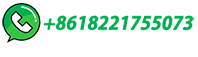
Flotation of copper oxide minerals: A review
Chrysocolla is a copper oxide mineral with a complex structure, and it is characterized by multiphase inhomogeneity and multiple micropores. The ideal molecular model of the chrysocolla unit cell is shown in Fig. 1 [12].However, isomorphism exists in the molecular structure of chrysocolla because of impurity-atom doping, resulting in chrysocolla not having a …
اقرأ أكثر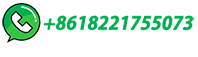
Parametric Optimization in Rougher Flotation Performance of a
The dominant challenge of current copper beneficiation plants is the low recoverability of oxide copper-bearing minerals associated with sulfide type ones. Furthermore, applying commonly used conventional methodologies does not allow the interactional effects of critical parameters in the flotation processes to be investigated, which is mostly overlooked in …
اقرأ أكثر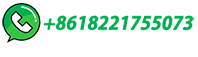
Design and Comparison of Fractional-Order Controllers in Flotation Cell
This study employs models of both a bank series of five flotation cells and a flotation column. Their performance results are compared against traditional controllers, such as an integer-order PID ...
اقرأ أكثر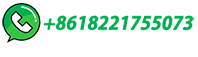
IMPROVED CLEANER CIRCUIT PERFORMANCE AT THE …
Ore is processed through a conventional flotation circuit to separate the valuable copper sulphide bearing particles. The details of the flotation cells are listed in Table 1. Figure 1: DeGrussa …
اقرأ أكثر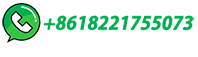
COPPER FLOTATION PLANT
Achieve optimal mineral ore recovery with minimal impact on the environment. The Pineer froth flotation process enables sustainable and cost-effective copper/lead/zinc ore recovery. Comes from one supplier, responsible …
اقرأ أكثر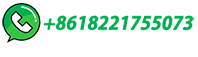
Recovery of Copper from Slags Through Flotation at the Hern
The significant volume of copper smelting slags poses environmental challenges, particularly concerning soil and surface water contamination. However, these slags contain valuable elements such as copper and iron, the recovery of which can contribute to both environmental protection and the circular economy in Chile. This study analyzes, at both …
اقرأ أكثر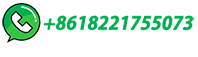
Extracting Copper from Ore: A Step-by-Step Guide
In the context of copper extraction, the process begins with crushing and grinding the copper ore into a fine powder to increase the surface area. ... Air is then injected into the flotation cell, creating bubbles that rise through the slurry. The hydrophobic copper minerals attach to these air bubbles and are carried to the surface, forming a ...
اقرأ أكثر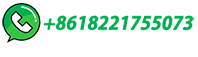
Molybdenum Ore Processing by Flotation
This molybdenum flotation circuit, based on 250-500 tons per 24 hours is designed for low-grade molybdenum ore having high-grade streaks and with pyrite-quartz gangue.It is also basically sound for many other friable …
اقرأ أكثر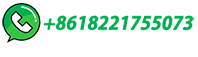
60 Centuries of Copper: The Flotation Process
The powdered product of grinding the ore is fed into a series of tanks called flotation cells which are filled with a solution containing various oils capable of forming a froth. Air is pumped into …
اقرأ أكثر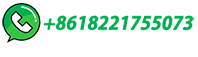
Copper Extraction Process Demystified: Expert Insights
Learn about the copper extraction process in detail. Explore the steps involved and the techniques used in our latest blog. ... The type of reagents used and the conditions within the flotation cells determine the efficiency of the flotation process in the separation of copper minerals from the gangue. ... Successful Plant Projects. 40+
اقرأ أكثر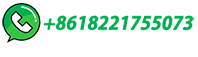
Optimizing the Rougher Flotation Process of Copper Ore
Due to the diversity of the geological aspects between the copper ore deposit, which implies different structures between the chemical and physical conditions of these, in addition to various configurations that make up the flotation cells between concentrate plants, it is interesting to replicate this study in other mining plants, in order to ...
اقرأ أكثر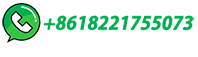
Improving the performance of a low-grade porphyry copper ore flotation
A large porphyry copper flotation plant has been simulated using a flotation model developed from first principles using the hydrophobic force as a kinetic parameter (Huang et al., 2022, Gupta et al., 2022).The input to the simulation was the size-by-class liberation matrix (m ij) of a flotation feed, which was essential for predicting the size-by-class flotation rate constants …
اقرأ أكثر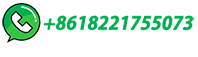
Sources, Performance and Mechanisms of Metal Ions in the Flotation
In mineral processing operations, besides target minerals, slurries often contain various metal ions, including common ones with different valence states such as Pb2+, Cu2+, Fe2+, and Fe3+. These metal ions originate from multiple sources during the flotation process, including the dissolution of co-occurring metal minerals during crushing and grinding, the …
اقرأ أكثر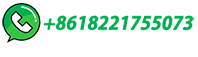
How to Enhance the Copper Flotation Cell?
Jameson Cells: These cells combine the principles of flotation with those of dense medium separation, resulting in a more efficient and faster separation process. Pneumatic Flotation Cells: These cells use micro …
اقرأ أكثر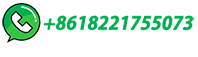
Enhancing the flotation recovery of copper minerals in smelter …
The rougher tails are fed to a series of scavenger cells before exiting the plant as final tailings. Potassium amyl xanthate (~300 g/t) is the primary flotation collector reagent used, and Sodium Dialkyldithiophosphate (200 g/t) is added as a secondary collector. ... Various flotation reagents that are commonly used for copper flotation were ...
اقرأ أكثر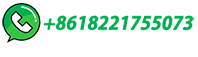