Pelletization
Sufficient moisture needs to be added to make the ore sticky enough to pelletize, but not so much moisture that the ore becomes "muddy." ... Since the purpose of iron ore processing is to remove silicate minerals from the ore, adding silicates back in the form of a binder is counterproductive. ... The data suggest that the heavy metals are ...
اقرأ أكثر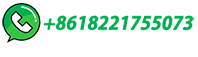
Metals From Ores. An Introduction to Extractive Metallurgy
Ores are a mixture of minerals: they are processed to yield an industrial mineral or treated chemically to yield a single or several metals. Ores that are generally processed for only a single metal are those of iron, aluminium, chromium, tin, mercury, manganese, tungsten, and some ores of …
اقرأ أكثر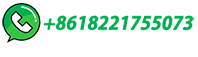
Pelletizing Minerals for Improved Handling and Use
Why Pelletize Minerals? Pelletizing can offer a wide range of benefits, depending on the mineral being processed and the intended end use. Typical benefits include: Stable and Efficient Mineral Processing. ... Such is the case with iron ore, which is pelletized or ...
اقرأ أكثر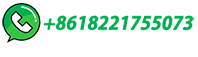
Iron processing | Definition, History, Steps, Uses, & Facts
Iron processing, use of a smelting process to turn the ore into a form from which products can be fashioned. Included in this article also is a discussion of the mining of iron and of its preparation for smelting. Iron (Fe) is a relatively dense metal with a silvery white appearance and distinctive
اقرأ أكثر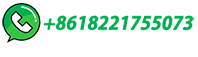
What Are Iron Ore Pellets and How to Make Them?
Iron ore pellets are spheres of typically 8-16 mm to be used as feedstock for blast furnaces. They contain 64-72% iron and additional materials, which can adjust the chemical composition and metallurgical properties of the pellets. The iron ore pelletization is the process of converting iron fines less than 200 …
اقرأ أكثر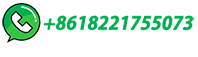
Iron Ore Pelletizing Process: An Overview
The iron ore pelletizing process consists of three main steps: 1. Pelletizing feed preparation and mixing: the raw material (iron ore concentrate, additives anthracite, dolomite and binders are …
اقرأ أكثر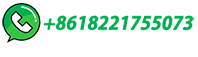
Iron Ore Processing: From Extraction to Manufacturing
The final stage in iron ore processing is ironmaking, where the iron ore is transformed into molten iron through a process called reduction. The most common method of ironmaking is the blast furnace route. In a blast furnace, iron ore, coke (carbon), and fluxes (limestone or dolomite) are loaded into the furnace from the top.
اقرأ أكثر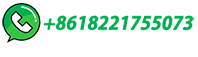
Mention the steps involved in extraction of metals from ores
Give the steps involved in the extraction of metals of low and medium reactivity from their respective sulphide ores. Q. Write the steps involved in the extraction of pure metals in the middle of the activity series from their carbonate ores.
اقرأ أكثر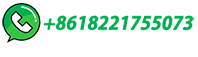
ROSIE—Revolutionizing Ore to Steel to Impact Emissions
pressure ranges to reduce high- and low-grade iron ore fines into molten iron metal. The approach eliminates the need to sinter or pelletize iron ore for traditional ironmaking furnaces. Limelight estimates that their technology would reduce energy consumption of steelmaking by 46% and emissions by 81%.
اقرأ أكثر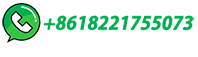
steps to pelletize iron ore metals
steps to pelletize iron ore metals - inkarnate.in . steps to pelletize iron ore metals; ... how much does a copper ore crusher cost is one of the products of our company main products sold,it is not only good ... steps to pelletize iron ore metals - ZCRUSHER ... steps to pelletize iron ore metals; steps in crushing iron ...
اقرأ أكثر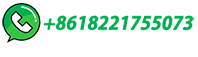
Iron Ore Pelletization
In general, three primary phases occur in iron ore pelletizing: The mixing step sets the stage for the remainder of the process, creating a homogeneous mixture that will allow for a uniform product to be created. In order to pelletize iron ore …
اقرأ أكثر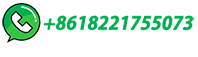
An Australian iron ore company is shifting to green energy, and
FFI's parent company, Fortescue Metals Group, is one of the world's largest producers of iron ore. For nearly two decades, larger-than-life business icon Andrew Forrest — nicknamed "Twiggy ...
اقرأ أكثر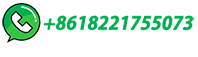
Iron ore pelletization
Iron ore lump, sinter, and pellets comprise the main burden of modern blast furnaces. However, sinter and pellets are now the dominant blast furnace burden, because the natural lump supply has declined dramatically due to depletion of the world's high-grade competent iron ore resources.
اقرأ أكثر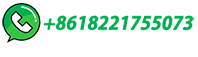
Metal Ore Extraction and Processing
Metal Ore Extraction and Processing 171 FINISHING PROCESSES FINISHED PRODUCT INTERMEDIATE PRODUCTS COLD FORMING ACID PICKLING HOT FORMING CASTING MOLTEN IRON IRON ORE LIMESTONE COKE ADDITIVES Figure 10.3. The transformation of iron ore into steel products. (a) Processing of iron ore. (b) Manufacture of steel ingots.
اقرأ أكثر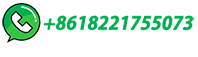
A new insight into iron ore oxidized pellets prepared by steel belt
Iron ore oxidized pellet is a superior furnace burden for the blast furnace process, possessing high iron grades, good strength, and excellent metallurgical properties [].Additionally, compared to the sintering process, the energy consumption of the pelletizing process is approximately 50% lower, with emissions of pollutants such as SO 2, NO x, and particulate …
اقرأ أكثر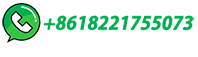
The six main steps of iron ore processing
When iron ore is extracted from a mine, it must undergo several processing stages. Six steps to process iron ore. 1. Screening We recommend that you begin by screening the iron ore to separate fine particles below the crusher's CSS …
اقرأ أكثر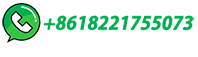
The Iron Pelletizing Process
Explore the iron and steel industry's use of iron ore, focusing on the pelletizing process of low-grade ores. Learn about the various sub-processes, including crushing, grinding, separation, and agglomeration. Understand the market …
اقرأ أكثر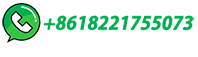
Iron Ore
1.1.3.2.1.2 Iron-Bearing Materials. Ore fines and iron concentrates make the main part of the sinter mix. The grain size of ore fines and concentrates is typically 0–8 and 0–3 mm, respectively.Grains smaller than 0.1 mm are not desired because they reduce the gas permeability of the bed and thus decrease the sintering efficiency.Recycled materials, such as …
اقرأ أكثر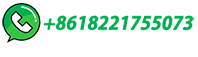
Iron Ore Pelletizing Process: An Overview
The iron ore production has significantly expanded in recent years, owing to increasing steel demands in developing countries. However, the content of iron in ore deposits has deteriorated and low-grade iron ore has been processed. The fines resulting from the concentration process must be agglomerated for use in iron and steelmaking. This chapter …
اقرأ أكثر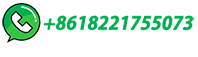
What is Iron Ore Pelletizing? How It Worked? An In …
Iron ore pelletizing is an essential industrial process that transforms powdery iron ore into uniform, robust pellets, serving as a premium feedstock for blast furnaces and direct reduction reactors.
اقرأ أكثر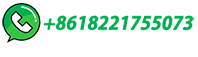
Innovating alloy production: A single step from ores to …
Comparison between the classical multi-step alloy production and the proposed one-step oxides to bulk alloy approach. Credit: Nature (2024). DOI: 10.1038/s41586-024-07932-w Metal production is responsible for 10% of global CO2 emissions, with iron production emitting two tons of CO2 for every ton of metal
اقرأ أكثر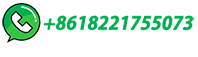
The Iron Pelletizing Process
The iron pelletizing process is often associated with low grade iron ore following a range of liberation techniques to prepare and make suitable for the blast furnace. In summary, pelletizing is achieved by combining the iron ore with water and a …
اقرأ أكثر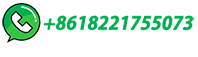
Pelletizing for Direct Reduction and Electric …
On the one hand, increased efforts in iron-ore beneficiation to enhance the iron level in raw materials lead to the ever-decreasing grain size of iron ores. On the other hand, dominating shaft technologies such as the …
اقرأ أكثر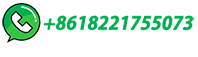
flow chart of step involved in the extraction of metal from its ores
Metals and non-metals/General Metallurgy – The Process of …. General Metallurgy – The Process of Extraction of Metals from their Ores and Refining them: … Processes involved in metallurgy Main process: Sub-process: 1. » More detailed gcse 1. Introduction to the Extraction of Metals method related to …. Doc Brown's Chemistry GCSE/IGCSE / O Level Revision Notes.
اقرأ أكثر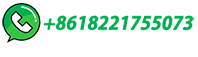
(PDF) From Ores to Metals
The first steps in the production of a metal object are to extract the ore from the mine, process the ore for smelting, and then eventually smelt the ore into metal. As fundamental as these steps ...
اقرأ أكثر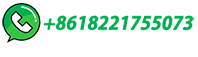
Converting iron ore into iron pellets
Iron ore pelletization is a key process in the steelmaking industry that helps improve the quality and efficiency of steel production. In this process, iron ore is powdered and then converted into …
اقرأ أكثر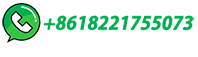
Ore Pellet
Describes the iron ore burden materials charged to the blast furnace (BF): lump ore, sinter, and pellets. 2. Gives an overview of the iron ore minerals used and the related processing techniques. 3. Compares the physical and chemical properties of the iron ore charge materials, as well as their impact on the BF operation. 4.
اقرأ أكثر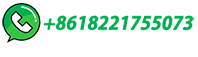
Extraction of Metals from Ores – Different Processes Involved
This concept page will also describe how metals in the lower part of the activity series can be extracted from their ores. Major Metal Ores in India. Iron, which is one of the most important and beneficial metals, is extracted from iron ores. Iron ores mines are found in Goa, Karnataka, Orissa. Aluminium is extracted from Bauxite ore.
اقرأ أكثر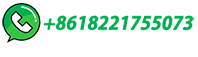
Iron ore pelletizing
The iron is usually ground to a very fine level and mixed with limestone or dolomite as a fluxing agent and bentonite or organic binders as a binding agent. If the ore is a Hematite ore, coke or anthracite coal can be added to the mix to …
اقرأ أكثر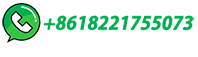
Iron ore pellets and sustainable steel | Malvern Panalytical
Iron ore pellets offer an innovative solution as manufacturers work to cut their emissions in the energy-intensive sintering phase of steel production. ... They might be on a slightly different scale, but they're both made of steel – the metal that supports our society. Without the steel industry, our world would look very different ...
اقرأ أكثر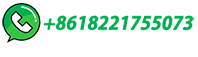