Iron Ore Sintering Process: Transforming Raw Ore into High …
Explore the intricate steps involved in the sintering process of iron ore. Discover how raw materials are transformed into a high-quality final product, enhancing industrial …
اقرأ أكثر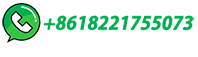
Iron ore sintering
A sample of goethite iron ore sinter feed (G_SF) was employed as a raw material in a sintering bed. This sample partially replaced hematite sinter feed (H_SF), which is currently used as raw ...
اقرأ أكثر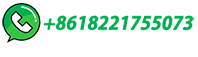
OneMine | A Sintering Ore Blending Optimization Model Based On "Iron
Finally, sinter pot test was carried out to verify the validity and practicability of the sintering ore blending optimization model which was aimed at giving consideration to the sintering indexes and the cost.IntroductionIn recent years, the price of imported iron ore with high quality is always at a high level, while iron ore self-sufficient ...
اقرأ أكثر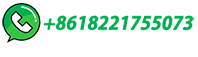
Iron Ore Sintering: Raw Materials and Granulation
Sintering is an agglomeration process that fuses iron ore fines, fluxes, recycled products, slag-forming elements and coke. The purpose of sintering is to obtain a product with suitable ...
اقرأ أكثر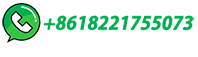
(PDF) Iron Ore Granulation for Sinter Production: …
Correspondingly, the challenges in sintering granulation field are proposed to include: (1) Development of iron ore sintering industry; (2) Ore blending optimization based on synergistic coupling ...
اقرأ أكثر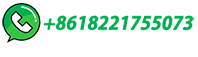
(PDF) Iron ore sintering. Part 1. Theory and practice of …
Sintering is a process by which a mixture of iron ores, fl uxes and coke is agglomerated in a sinter plant to manufacture a sinter product of a …
اقرأ أكثر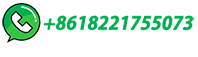
Iron Ore Sintering: Raw Materials and Granulation
Granulation practice Sinter productivity is directly related with bed permeability. ... (ultra concentrates of high fineness). The boundaries for each group are: Group A: ≤ 15 Group B: Group C: ≥ 70 35 35 70 t Group D: 15 rip In this way it is possible to achieve the optimal sintering mix from the granulometric point of us c view. 3.6 ...
اقرأ أكثر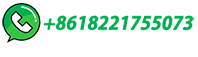
Mathematical Modelling and Simulation of the Iron Ore …
Preparation of iron ore sinter consists essentially of two steps. One, granulation in a rotary drum of moist raw sinter feed comprising iron ore fines, coke breeze, limestone, lime, dun-
اقرأ أكثر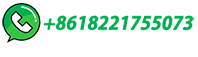
CURRENT PRACTICES IN INDIAN IRON ORE …
3 in sinter fines. 4. The present iron ore washing circuit produces slimes, particles below 0.15 mm (-100mesh) which are discarded ... The generation of slimes is about 20-25% of the feed to the ...
اقرأ أكثر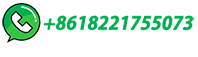
Prediction of the granule size distribution of iron ore sinter feeds
In addition to being the main driver of lowering CO2 emissions, new ironmaking technologies need to be able to process any type of iron ore directly, preferably in the form of ultra-fines, owing ...
اقرأ أكثر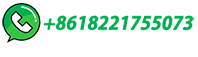
Iron Ore Sintering
Iron ore sintering is the iron ore powder agglomeration process that changes fine iron ore powder into the lumpy iron-bearing raw material used for blast furnace ironmaking. High-temperature process and addition of alkaline flux will improve metallurgical performance of iron-bearing raw material. Besides, the sintering process will consume the ...
اقرأ أكثر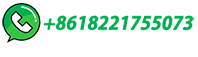
(PDF) Iron Ore Sintering: Process
Sintering is a thermal agglomeration process that is applied to a mixture of iron ore fines, recycled ironmaking products, fluxes, slag-forming agents, and solid fuel (coke). The purpose of...
اقرأ أكثر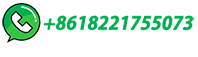
Utilization of Pellet Fines in the Iron Ore Sintering Process
The sinter plant that converts the iron ore fines into a desirable blast furnace feed, offers an avenue for recycling wastes. One of the several wastes that are produced at an iron and steel plant ...
اقرأ أكثر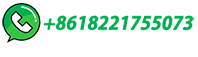
Iron ore mining and dressing
Iron is one of the most important metals in mechanical engineering, as it is present in sufficient quantities on earth. The extraction of iron can therefore be very economical. However, pure iron is not suitable for use as a construction material. It is much too soft in its pure form and has too little strength to meet most …
اقرأ أكثر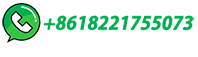
Granulation Effectiveness of Iron Ore Sinter Feeds: Effect of …
16) A group of mainstream iron ore fines possessing different mineralogical properties and particle size distributions were tested. 2. Mechanistic Model Proposed by J.D. Litster et al. According to an earlier study,17) the iron ore particles act either as nuclei particles or adhering particles in the granulation process. A partition coefficient ˚
اقرأ أكثر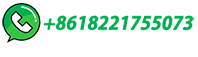
(PDF) Iron ore sintering. Part 1. Theory and practice of the sintering
The present work provides information on the iron ores that form part of the mineral mix which, once granulated, is loaded onto the sinter strand where it is partially melted at a temperature of between 1250-1350 °C and undergoes a series of reactions that give rise to the formation of sinter; a material of a suitable composition and strength ...
اقرأ أكثر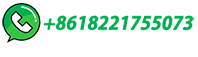
Iron Ore Sintering: Process
Sintering is a thermal agglomeration process that is applied to a mixture of iron ore fines, recycled ironmaking products, fluxes, slag-forming agents, and solid fuel (coke). The purpose of the ...
اقرأ أكثر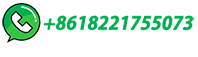
IRON ORE SINTER FEED (FSF)
IRON ORE SINTER FEED (FSF) IRON ORE FINES (CBF) LUMP ORE (SICLO-1) DIRECT REDUCED IRON (A) BRIQUETTES HOT - MOULDED DIRECT REDUCED IRON (C) (BY - PRODUCT FINES) DIRECT REDUCED IRON (B) PELLETS Ferro Silico Manganese (FeSiMn) 3" x ½" - 2" x ½" Ferro Silico Manganese (FeSiMn) 4" x 1"
اقرأ أكثر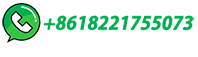
Relationship Between Iron Ore Granulation Mechanisms, Granule …
This technique is used to study in detail the factors which determine the voidage of packed beds of granulated ferrous sinter feed. 10 sinter feed blends are used varying the type of ore (7 ores ...
اقرأ أكثر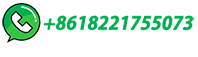
Numerical Simulation Model of the Iron Ore Sintering Process Directly
The obtained structural change of the sintering bed show that the proposed model is a potential tool to analyse the agglomeration phenomena occurring in the iron ore sintering process under various conditions. KEY WORDS: iron ore sintering; DEM; simulation; agglomeration; granules; heat transfer; structural change; packed bed. 1.
اقرأ أكثر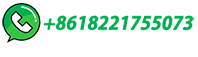
Iron ore concentrate vs fines: An In-Depth Comparison
Iron ore concentrate is primarily used in the production of pellets and sinter feed. Its high iron content and low impurities make it ideal for: 1. ... high-quality concentrates are directly used in blast furnaces, bypassing the need for pelletizing or sintering. Iron Ore Fines. Iron ore fines are used in various ways in the steel industry ...
اقرأ أكثر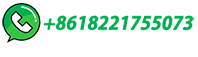
Ore Sinter
The iron ore operations of Vale are spread across four systems, namely, the northern, southeastern, southern, and midwestern systems, as shown in Figure 1.26. The northern system comprises the high-grade Carajás mine, which produces lump ore, sinter fines, pellet feed, and special feed for direct reduction.
اقرأ أكثر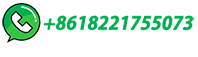
Segregation Charging Behavior of Ultra-Fine Iron Ore Briquette in
Abstract The sinter–briquette complex firing process which is an effective technology for utilization of low grade ultra-fine ore is a method for charging sinter feed mixed with briquette made of ultra-fine ore. To uniformly fire briquettes using the excess heat from the lower part of the sinter feed bed, they must be segregated in that region. In this study, the particle …
اقرأ أكثر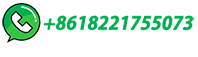
Study of iron ore sinter when fine ore is replaced with coarse ore
In present work pot grate sintering experiments have been carried out in laboratory with different level iron ore size (mean particle size from 1.22 to 3.95 mm) to understand the influence of iron ...
اقرأ أكثر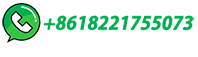
Granulation Effectiveness of Iron Ore Sinter Feeds: Effect of Ore
Granulation of sinter feeds is an indispensable step in the iron ore sintering process. Through granulating, iron ore fines, fluxes, fuels and recycle materials ( e.g., return fines, dust, etc.) are …
اقرأ أكثر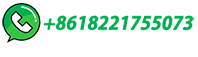
A Sintering Ore Blending Optimization Model Based on "Iron …
Comparison of the Property of Iron Ore before and after Ore Dressing. Sintering Ore Blending Optimization Model. Model Application and Sinter Pot Experiment. Conclusions. …
اقرأ أكثر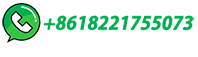
Sintered Iron-Ore Manufacturing Capabilities when Using
Abstract In order to create thermal conditions that form the same time-temperature conditions throughout the height of the sinter-feed mixture after (1) blending, (2) source material pelletizing, (3) laying on the fire grate, (4) initial layer heating under the ignition hood, and (5) ignition of the solid charge fuel, a natural gas-air mixture with an air flow coefficient > 3.5 is …
اقرأ أكثر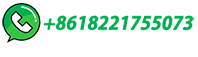
Iron Ore Sintering: Process
Sintering is a thermal agglomeration process that is applied to a mixture of iron ore fines, recycled ironmaking products, fluxes, slag-forming agents, and solid fuel (coke).
اقرأ أكثر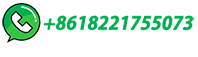
Ore-blending optimization model for sintering process based on
An ore-blending optimization model for the sintering process is an intelligent system that includes iron ore characteristics, expert knowledge and material balance.
اقرأ أكثر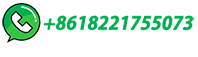
Segregation Charging Behavior of Ultra-Fine Iron Ore Briquette in
The sinter–briquette complex firing process which is an effective technology for utilization of low grade ultra-fine ore is a method for charging sinter feed mixed with briquette made of ultra ...
اقرأ أكثر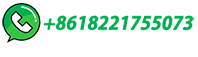