Sintering Technology | PPT
5. Raw Material Preparation Preparation of sinter mix exerts considerable influence on productivity, quality (RDI,RI), consistency of sinter chemistry as well as machine operation. Quality and productivity are determined by coke combustion behavior during sintering process Following raw materials are used for sintering: I/o fines 0 - 10mm (generated ) flux fines 0 - …
اقرأ أكثر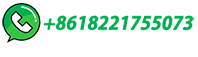
THE PERFECT SINTER PLANT
– with unique process optimization and expert systems for a safe and reliable production • Continuous improvement – upgrades and lifecycle support during operation of the sinter plant When it comes to major investments, there is no substitute for an experienced partner. Every step in the sintering process – each plant area
اقرأ أكثر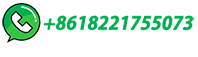
SINTERING AND PELLETISATION OF INDIAN IRON ORES
Growth of steel industry with depleting resources of high grade ores have led to a very strong demand for both pelletising and sintering of iron ores. Process objective is to transform fine …
اقرأ أكثر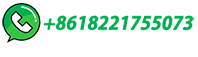
Automation of Sinter Charge Moistening during Pelletising
To increase the efficiency of pelletising, it is proposed to automate the process of moistening of sinter charge. The functional scheme of the automatic humidity control system is …
اقرأ أكثر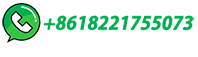
Mixing and Pelletizing Process in Sinter Production
In large sintering plants, to extend pelletizing time, a three-stage mixing and pelletizing process is adopted. The first stage uses a drum mixer for blending, and the second and third stages use drum mixers for pelletizing to …
اقرأ أكثر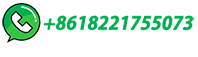
What is Sintering? A Complete Guide to the Process and Uses
1. Raw Material Preparation: The first step is to create or acquire the powdered metal needed for sintering. The powders are often produced through atomization or chemical reduction. 2. Compaction: The powder is placed into a die or mold and compacted using high pressure to create a green part. This compacted part is fragile and requires further processing …
اقرأ أكثر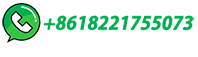
(PDF) Physicochemical Processes in Pelletizing Sintering Mixture
Data on the physico-chemical processes occurring during the pelletization of sintering mixture were obtained by bench and laboratory studies. Both the sintering parameters of the mixture …
اقرأ أكثر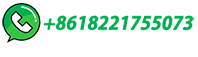
A New Approach of Pelletizing: Use of Low-Grade Ore as a
For carbon neutrality, the use of sinter should be decreased owing to higher CO 2 emission in the sintering process of the blast furnace operations. This trend might contribute to …
اقرأ أكثر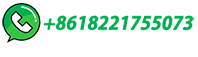
Application of deep learning in iron ore sintering process: a review
The sintering process is an intricate system with a protracted process flow. The steps in the manufacturing line are primarily composed of the ingredients and mixing process, the sintering operation process, and the treatment of the sintered ore [39, 40].2.2 Important parameters and characteristics of sintering process. As shown in Fig. 2, all variables affecting …
اقرأ أكثر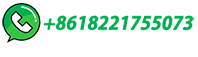
(PDF) IRON ORE PELLETIZING PROCESS
PDF | Iron Ore, Iron Ore Pellets, Direct Reduced Iron )DRI( Pellets, Iron Ore Pellets Market, Pelletizing Process, Sintering, Binder, Induration... | Find, read and cite all the research you need ...
اقرأ أكثر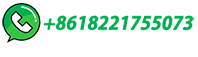
Improvement in the permeability of sintering beds by drying …
The typical iron ore sintering process supplies the main ferrous charge for blast furnaces in most steel mills. During sintering, first the sinter raw materials are intimately mixed and granulated to produce granules with a narrow …
اقرأ أكثر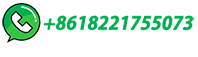
Importance of fine ore chemical composition and high …
However, little has been published on the implications of ore chemical composition for iron ore sinter and pellet product quality. The ore bulk composition and the nature of the minerals in the fine ore both play a critical role in determining the type of high temperature bonding phases that form during sintering and pelletising.
اقرأ أكثر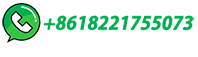
A New Approach of Pelletizing: Use of Low-Grade Ore as a
For carbon neutrality, the use of sinter should be decreased owing to higher CO2 emission in the sintering process of the blast furnace operations. This trend might contribute to the increased use of iron ore pellets with lower CO2 emission in the fabrication process, high reducibility and gas permeability due to higher mechanical strength. The pelletizing process …
اقرأ أكثر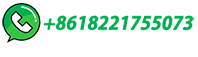
(PDF) COMPARISON OF SINTER AND PELLET USAGE IN AN …
Traditionally, fine ores are treated either by the process of sintering and/or by pelletizing to prepare an agglomerate with suitable metallurgical characteristics for ironmaking processes.
اقرأ أكثر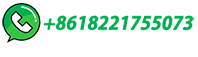
Pelletizing Process
The sintering process uses the combustion heat of coke breeze (fuel). Pellets are made from iron ore that is finer than that used for sintered ore. The ore fine is formed into spheroids, called …
اقرأ أكثر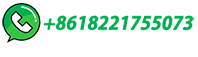
Advancing contact angle of iron ores as a function of their …
The granulation process is typically performed in a rotary drum using water as the binder liquid. Minimisation of the volume of water used during the granulation step is of vital economic importance due to the associated energy costs …
اقرأ أكثر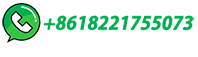
Sintering and Pelletizing
Ensure your plant's high performance and profitability while lowering investment and operating costs with our agglomeration technologies. Our innovative sintering and pelletizing solutions are based on over 60 years' experience and world …
اقرأ أكثر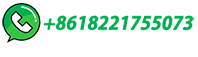
Influence of Biomass Absorptivity on the Process of Sinter Charge
The pelletising ability of coke dust is generally known and coke dust exhibits good pelletisability. ... The erosion and permeation behavior of coal ash on refractories during coal ash sintering ...
اقرأ أكثر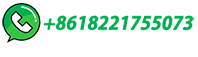
Comparative review on the technologies of briquetting, …
ents for agglomeration methods of iron ore via sintering and for the conveyor sintering machine [4] were obtained in Germany in 1902 and in USA in 1907-1909. Owing to insufficient strength of briquettes and low productivity of briquetting machines, the sintering method was widely ap-plied in the iron and steel industry and non-ferrous metal-
اقرأ أكثر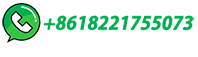
Automation of Sinter Charge Moistening during Pelletising
The influence of sintering charge moisture content on the indicators of sintering production of Ural Steel JSC was studied. It was found that the current pelletising and moistening regime has insufficient efficiency, not providing stable sinter charge with constant moisture and good gas permeability. The reason for sinter charge moisture fluctuations affecting pelletising …
اقرأ أكثر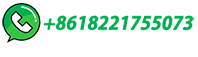
Advancing contact angle of iron ores as a function of their …
DOI: 10.1016/J.MINPRO.2004.01.007 Corpus ID: 96783070; Advancing contact angle of iron ores as a function of their hematite and goethite content: Implications for pelletising and sintering
اقرأ أكثر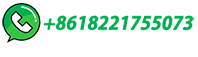
Agglomeration of Iron Ores
Agglomeration of iron ores is the iron ore pretreatment process in which the powdery iron ore that cannot be directly fed into a blast furnace experiences high-temperature solidification by sintering process and pelletizing process or low-temperature solidification by pelletizing process and briquetting process to generate the rich ore material that meets the …
اقرأ أكثر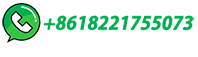
Iron Ore Agglomeration Technologies
Until the 1950s of the last century, the oxidized iron ores that were loaded into the blast furnace had granulometries within 10 and 120 mm. However, the depletion of high-grade iron ore sources has made necessary the utilization of concentration processes with the purpose of enriching the iron ore. Because of these processes, a fine granulometry is produced, and thus …
اقرأ أكثر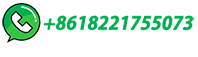
Development of Chromite Sinter from Ultra-Fine Chromite …
of coke breeze (as in iron ore sintering) may be an alterna-tive, cost-effective process of agglomeration which is likely to be free from the preceding limitations. However, sintering of chromite fines is still challenging, because the melting point of chromium spinel is too high to form a molten phase required for the bonding during the sintering.
اقرأ أكثر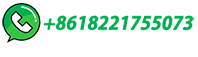
Mineralogical characteristics, metallurgical properties and phase
In order to study the sintering characteristics of Ca-rich iron ore, chemical analysis, laser diffraction, scanning electron microscopy, XRD-Rietveld method, and micro-sintering were used to analyze the mineralogical properties and sintering pot tests were used to study the sintering behavior. In addition, a grey correlation mathematical model was used to calculate …
اقرأ أكثر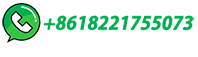
Outotec Steel Belt Sintering
Sintering Scrubbing Scrubbing CO gas filtering Preheating Smelting Outotec Steel Belt Sintering (SBS) takes ferroalloy production efficiency to a new level. Pelletizing and sintering enable good charge uniformity, resulting in consistent submerged-arc furnace performance, lower power consumption, and higher recovery yields. It is the industry's
اقرأ أكثر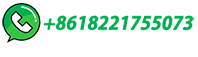
Digestion of Solid Waste During Sintering-Pelletizing Process
3.1.4 Experimental Results 3.1.4.1 The Effect of Steel Slag Dosage on Sintering Process. As can be seen from Fig. 3.2, with the increasing amount of steel slag, the sintering temperature of the sintering pot rises continuously.The main reason is that converter steel slag belongs to clinker itself, which is easy to melt and low in energy consumption during sintering, …
اقرأ أكثر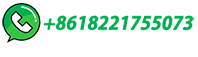
Advances in the sources, chemical behaviour, and whole process
The sintering/pelletising process provides refined iron ore raw materials for BF ironmaking. With the increasing use of refined materials, the techno-economic indicators of modern BF production have steadily improved. Consequently, sintering has become an indispensable component of steel manufacturing. ... During the sintering process, the ...
اقرأ أكثر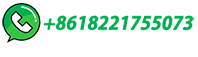
Improvement in the permeability of sintering beds by drying …
The waste heat of the cooling process accounts for approximately 19–35% of the total energy consumption during sintering [27]. The temperature of the sinter at the cooling bed inlet is within the range of 500–600 °C depending on the specific operating conditions [26] .
اقرأ أكثر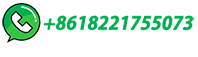