Iron Ore Sintering: Raw Materials and Granulation
For better blast furnace performance, there has always been a need for better quality raw materials like sinter, lump ore, and pellets. Among these raw materials the usage of sinter in blast furnace is at higher side compared to other iron bearing materials. As the quality of sinter product improves, its usage in blast furnaces also increases.
اقرأ أكثر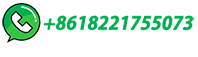
Model of an iron ore sinter plant with selective waste gas
Eq. 2 describes the chemical conversions of each gaseous fuel (CO, C x H y, (g))) with the reaction degree RD. The reaction degree describes the stoichiometric conversion of each chemical reaction. ... To show the validity of the selected operational settings, the SWGR was introduced in an iron ore sinter plant. The simulated stack gas ...
اقرأ أكثر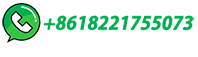
Design And Fabrication Of Iron Ore Sintering Machine | PDF
The function of the Sinter Plant is to supply the blast furnaces with sinter, combination of blended ores, fluxes and coke, which is partially 'cooked' or sintered. ... The merits of sintering process are listed below in comparsion to iron ore pellets: i. The sintering process uses cheap coke breeze as fuel while pellets need expensive oil ...
اقرأ أكثر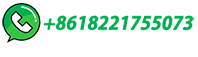
DIRECT SINTERING OF CHROMITE ORE FINES FOR FERROCHROME PRODUCTION …
Chromite ore is available in nature mainly in the form of Cr2O3.FeO which contains 40 - 52% Cr2O3 and 15- 20% FeO by weight. Global annual output of chromite ore is approximately 20 Mt, which has ...
اقرأ أكثر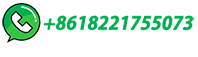
(PDF) Iron ore sintering. Part 1. Theory and practice of the sintering
Sintering is a process by which a mixture of iron ores, fl uxes and coke is agglomerated in a sinter plant to manufacture a sinter product of a suitable composition, quality and granulometry to be ...
اقرأ أكثر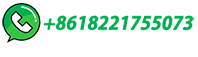
(PDF) Combustion Evaluation of Renewable Fuels for Iron-Ore Pellet
Induration (or sintering) of iron-ore pellets requires high temperature (~1300°C) which today is generating by burning fuel oil in the firing zone of the straight-grate plant (SG) or coal in the ...
اقرأ أكثر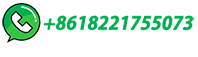
Recycling and Reuse of Iron Ore Pellet Fines | SpringerLink
For pelletization study, as received iron oxide pellet fines were ground to below 150 μ using ball mill. The particle size distribution of ground iron ore fines was determined by the Malvern particle size analyzer (Hydro 2000MU, UK) and shown in Fig. 2.Blaine number was measured to determine surface area of the iron oxide pellet fines using air permeability …
اقرأ أكثر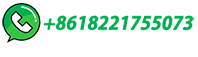
GUIDELINES FOR SELECTING PELLET PLANT …
plants compared to sinter plants. ... Figure 2 forecasts iron ore pellet feed production until 2025. Figure 2. Additional iron ore pellet feed production tha t must be pelletized, 2011-2025. (1)
اقرأ أكثر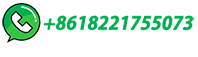
Making Sinter from Concentrate of Low-Grade Manganese Ore …
The sinter production from concentrate of low-grade manganese ore for use in the production of ferrosilicomanganese was discussed. It was found that the chemical composition of the concentrate ...
اقرأ أكثر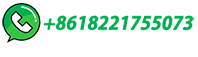
Modeling and simulation of processes from an iron ore sintering plant
The aim of this work was to develop a model for the iron ore sintering process with special focus on heat front propagation through the packed bed and to provide a powerful tool ("SinterSim v1.1 ...
اقرأ أكثر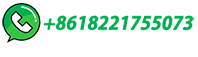
Sintering Technology for Iron ores and Optimization of Sinter Machine
A typical sinter plant consists of a number of sequential operating units with the sinter machine at the heart of the plant. The simplified process sequence is as follows. ... namely (i) pellet cars, (ii) drive for sinter strand, (iii) take-up mechanism, (iv) ignition furnace, and (v) crash deck and hot sinter crusher. ... Depending on the ore ...
اقرأ أكثر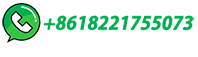
Advances in Sintering and Pellet Technology
The objective of iron ore agglomeration is to generate a suitable product of granules in terms of thermal, mechanical, physical, and chemical properties. Sintering and pelletization processes are largely influenced by the …
اقرأ أكثر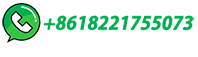
THE PERFECT SINTER PLANT
As a leading supplier of complete sinter plants, Primetals Technologies provides engineering, design, and equipment as well as integrated automation solutions. Specific technology …
اقرأ أكثر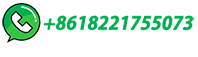
Behaviour of Iron Ore Granules: Laboratory and Commercial Sinter Plant
When the sinter chemistry was fixed and fine Si-bearing materials (e.g., quartz sand) were used, increasing the amount of ultrafine ores in the ore blends tended to reduce the adhering-layer ...
اقرأ أكثر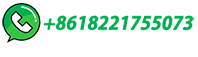
Optimizing Manganese Ore Sinter Plant
OPTIMIZING MANGANESE ORE SINTER PLANT - Free download as PDF File (.pdf), Text File (.txt) or read online for free. OPTIMIZING Manganese ore sinter PLANTS: process parameters and design IMPLICATIONS. Manganese ore sintering process relies on a number of complex process parameters. This paper seeks to describe some design considerations of sinter plants.
اقرأ أكثر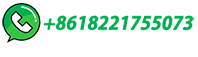
Influence of Chromite Ore Selection on the Pelletized Oxidative
The smelting of chromite to produce ferrochrome (FeCr) and subsequently, stainless steel, is an energy-intensive carbothermic process. Various countries apply the Outotec FeCr process, which employs oxidative sintering in air to produce mechanically strong chromite pellets. During this process, iron (Fe) is liberated from the chromite spinel due to the elevated …
اقرأ أكثر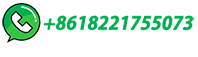
Pellet Plant – PMAI I Pellet Manufacturers Association of India
List of pellet plants in India provided by the Pellet Manufacturers Association of India.
اقرأ أكثر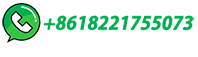
Sinter Plant Design, Engineering, Construction | M HEAVY …
Enhance iron ore sintering processes with our Sinter Plant solutions of M HEAVY TECHNOLOGY. Improve productivity, quality, and environmental performance for optimal results.
اقرأ أكثر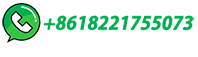
Iron Ore Pelletizing Process: An Overview
Iron ore and iron ore pellets are important sources of iron for manufacturing steel. The iron ore production has significantly expanded in recent years, owing to increasing steel demands in …
اقرأ أكثر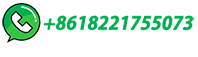
Understanding Pellets and Pellet Plant Operations
Understanding Pellets and Pellet Plant Operations. satyendra; March 21, 2015; ... Pelletizing differs from sintering in that a green unbaked pellet or ball is formed and then hardened by heating. ... Iron ore pellets. The iron ore pellets may be acid or basic pellets. Acid pellets are also called as DRI (direct reduced iron) grade pellets while ...
اقرأ أكثر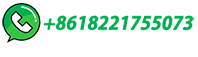
COMPARISON OF SINTER AND PELLET USAGE IN AN …
2.2 Comparing Sinter and Pellets Sinter and pellets are agglomerated forms of iron ore, both suitable for use as blast furnace burden materials. The principle difference between sinter and pellets arises from the type of raw materials used in their preparation and the nature of the sinter and pelletizing agglomeration processes.
اقرأ أكثر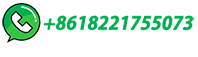
A forecast model of the sinter tumble strength in iron ore fines
As a traditional blast furnace (BF) iron-making burden, Iron ore sinter has numerous virtues in aspect of metallurgical and intrinsic properties [[1], [2], [3]].The sintering process of iron ore targets to achieve the consolidation of fine ore, containing the granulation of mixed powdery materials in a roller/disc, the ignition of solid fuel (coke fine/coals), the combustion of coke …
اقرأ أكثر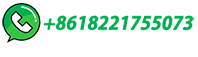
Sintering: Most Efficient Technologies for Greenhouse Emissions
Studies performed on iron ore sintering plants have indicated that PCDD/Fs are formed through a de novo synthesis, taking place in the sinter bed in regions where the temperature is 250–450 °C. ... P-eq from 0.15 lg/m 3 to 0.17 lg/m 3. Overall the results from the laboratory scale test suggest that it is feasible to replace up to 20% of coke ...
اقرأ أكثر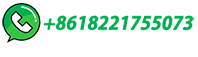
Sintering and pelletizing services Pallet cars for sintering and
pelletizing plants and 20 sinter plants in the last 20 years. Our experience has resulted in an unparalleled sintering and pelletizing process know-how as a technology leader with an in-house R&D center, engineering, and control of manufacturing from a single source. The continuous development of pallet cars for new plant
اقرأ أكثر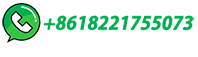
Reduction of Iron Ore Pellets: A Microstructural Perspective?
Twenty different iron ore pellets, consisting primarily of Hematite (Fe2O3) phase, were subjected to 'simulated' reduction studies. A wide range of reduction time periods, Rt of 122 to 211 minutes, were obtained. Detailed microstructural characterizations were then conducted at different locations of ten selected specimens. The Rt did not relate with initial phase mix or …
اقرأ أكثر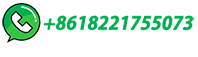
Iron ore pellets for blast furnace
What is iron ore pellet. Iron ore pellets are made by adding a small amount of additives to the fine ore powder (-200 mesh, that is, the ore powder with a particle size of less than 0.074mm accounts for more than 80%, and the …
اقرأ أكثر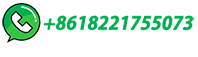
Sintering and Pelletizing
Traveling grate pelletizing plant is an induration technology for iron ore pellet production for a wide range of plant capacities. Traveling grate sinter plant reduces off-gas volumes and the …
اقرأ أكثر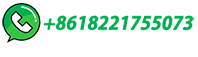
Development of high-strength ceramsite via sintering of iron ore
Over the years, various applications for IOTs have been explored. For instance, B. B. Das produced coarse aggregates based on fly ash (FA) by incorporating iron ore tailings (IOTs) into the FA precursor as an additional component in the mix [7].Lucas Augusto de Castro Bastos investigated the use of iron tailings as paving materials [8].Ranjeet Kumar Singh explored the …
اقرأ أكثر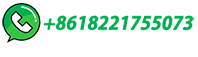
COMPARISON OF SINTER AND PELLET USAGE IN AN INTEGRATED STEEL PLANT
PDF | Global iron ore production has grown dramatically in recent years to meet increasing world steel demand, especially in Asia. High grade lump ore resources are being depleted and a greater amount of fine concentrate/pellet feed will enter into production as lower grade deposits are mined. Integrated steel plants need to make convenient use of the available iron ore resources …
اقرأ أكثر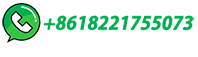