Brief of cement production process
Before transportation of raw materials to the cement plant, large size rocks are crushed into smaller size rocks with the help of crusher at quarry. Crusher reduces the size of large rocks to the size of gravels. ... Kiln is a huge rotating furnace also called as the heart of cement making process. Here, raw material is heated up to 1450 ⁰C ...
اقرأ أكثر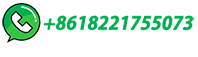
Cement Processing Equipment Market Size and Share Analysis …
New Jersey, United States,- "Cement Processing Equipment Market" [2024-2031] Research Report Size, Analysis and Outlook Insights | Latest Updated Report | is segmented into Regions, Types (Less ...
اقرأ أكثر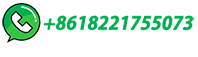
In-Depth Cement Processing Equipment Market Review: Size
The "Cement Processing Equipment Industry Analysis Report" offers a comprehensive and current examination of the market, encompassing crucial metrics, market dynamics, growth drivers, production ...
اقرأ أكثر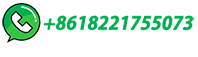
Mini Cement Plant | Cement Line Capacity 100-600tpd
A cement mill is a key equipment used in production for grinding cement, mainly including a cement ball mill and cement vertical mill. The cement grinding is the last step. In this process, the cement clinker uses a cement mill to ground a specific particle size. This can speed up the hydration reaction of cement.
اقرأ أكثر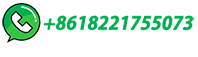
Cement Processing Equipment Market Size, Projections: Share, …
6. Cement Processing Equipment Market, By Application. 7. Cement Processing Equipment Market, By Geography. North America. Europe. Asia Pacific. Rest of the World . 8. Cement Processing Equipment ...
اقرأ أكثر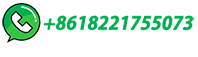
What Equipment is Used for Cement Manufacturing?
Cement Manufacturing Equipment. The abrasiveness of material and high temperatures involved in processing requires that cement manufacturing equipment be particularly robust. For North American cement manufacturing plants, vertical roller mills commonly handle the raw materials that will become cement, often with a throughput of 150-750 tons ...
اقرأ أكثر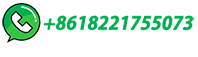
What Equipment is Used for Cement Manufacturing?
Cement manufacturing equipment needs to withstand the heat and the abrasive material from which cement is made. Making cement involves combining raw materials including limestone, clay, and shale, which are milled into a very fine …
اقرأ أكثر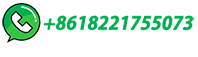
Cement Euipment Overview | Cement Making Machines
Providing a comprehensive guide to the entire cement production process from raw material extraction to the finished product, the industry's favourite technical reference book is now fully …
اقرأ أكثر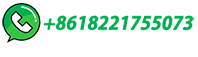
Modern Processing Techniques to minimize cost in Cement Industry
Selecting equipment or a system has never been easy. ... The apprehension regarding particle size distribution, cement strength, water cement ratio and consumer acceptance are being slowly addressed adequately. ... Dry process cement plants with 4-stage suspension preheater systems have already become universal and further technological ...
اقرأ أكثر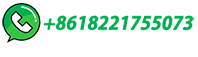
Cement Manufacturing Machine
Cement rotary kiln is the core equipment of cement plant, mainly responsible for clinker calcination, which can be used both in dry process cement production line and wet process cement production line. It is usually placed horizontally and at an angle to the ground, forming a state of one end high and one end low. ... (particle size, moisture ...
اقرأ أكثر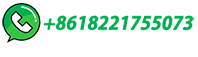
Cement Plant Process and Instruments Used | PPT
4. Limestone Quarry and Crushing Plant The major raw material for cement production is limestone.The limestone most suitable for cement production must have some ingredients in specified quantities i.e., calcium carbonates, silica, alumina, iron, etc.. Quarrying is done through drilling and subsequently, using heavy earth moving equipment such as …
اقرأ أكثر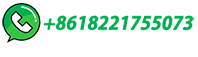
Cement Conveyor | Belt Conveyor In Cement Plant | AGICO
Cement conveyor refers to a belt conveyor in cement plant, which is necessary accessory equipment in the cement production line.. A belt conveyor is a kind of material handling equipment with strong adaptability, applied for conveying bulk density less than 1.67t / m³, it is mostly used for powder, granular, small lump materials, and bagged materials, such as sand, ore, coal, …
اقرأ أكثر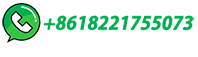
Pneumatic homogenization of raw mix
This circumstance together with lower heat consumption has resulted in an increasing preference for the dry cement production process. ... Sizes of blending silos ·12 m diameter and 17-m height, are not uncommon; the silo size for …
اقرأ أكثر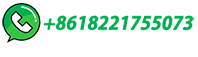
The mill shell Optimum dimensions
The thickness of the mill liners depends upon the mill diameter as well as on the size of the grinding media and generally fluctuates within limits of 30- 63 mm. Shape of the mill liners is usually rectangular; dimensions are approximately 300-400 x 450- 650 mm. Corresponding weights are 50-125 kg.
اقرأ أكثر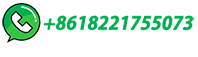
Types of Rotary Kilns
Dry-process kiln dimensions are similar to wet kilns in that they are long and typically show a length-to-diameter ratio of approxi mately 30:1 to 35:1. Dry-process kilns operate with a very high, back-end temperature and require watersprays at the feed end to cool the exit gases to safe levels before they enter the baghouse or precipitator ...
اقرأ أكثر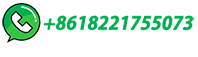
Kiln Control and Operation
Previous Post Next Post Contents1 Kiln Control and Operation2 1. INTRODUCTION3 1. CONTROL PARAMETERS3.1 1.1 Location of the control parameters and variables3.1.1 1.1.1 Wet kiln3.1.2 1.1.1 Lepol kiln3.1.3 1.1.1 Preheater kiln3.1.4 1.1.1 Precalciner kiln3.2 1.1 Burning Zone Temperature (BZT)3.2.1 1.1.1 Pyrometer reading3.2.2 1.1.2 NOx of the exhaust gases3.2.3 …
اقرأ أكثر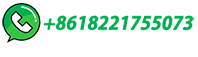
Cement Processing Equipment Market Size
🌐 Cement Processing Equipment Market Research Report [2024-2031]: Size, Analysis, and Outlook Insights 🌐 Exciting opportunities are on the horizon for businesses and investors with the ...
اقرأ أكثر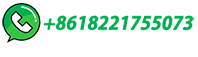
Everything you need to know about Kiln System Operations in Cement
A typical indirect system incorporates the following pieces of process equipment: • A hot air take-off, typically from the clinker cooler, with a dedusting cyclone to remove entrained clinker dust • Duct work to the hot air inlet of the mill • The mill to simultaneously grind and dry the solid fuel
اقرأ أكثر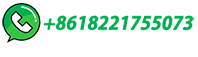
Operating Costs of Cement Plants: Comprehensive Analysis
Electricity is a crucial input, used to power various equipment and machinery throughout the cement production cycle, from raw material processing to kiln operations and packaging. Industry estimates suggest that electricity can make up 30-40% of the total operating costs for a cement plant.
اقرأ أكثر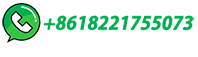
Cement Processing Equipment Market By Type
In 2024, the "Global Cement Processing Equipment Market" holds a value of $7.5 billion, with forecasts indicating it may rise to $16.67 billion by 2031, fueled by a CAGR of 14.23%.
اقرأ أكثر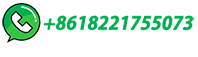
Cement Processing Equipment Market Size | Trends
Our report on the Cement Processing Equipment market provides comprehensive insights into the market size, trends, and opportunities in the industry. Our report provides a detailed analysis of the ...
اقرأ أكثر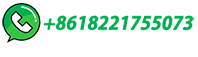
Concrete Masonry Unit Shapes, Sizes, Properties, and Specifications
Specified dimensions of concrete masonry units are typically 3/8 in. (9.5 mm) less than nominal dimensions, so that a 4 or 8 in. (102 or 203 mm) module is maintained with 3/8 in. (9.5 mm) mortar joints. ... Some of the surfaces are molded into the units during the manufacturing process, while others are applied separately. ...
اقرأ أكثر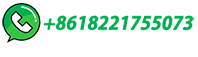
Cement Processing Equipment Market Size | Emerging Growth
The Cement Processing Equipment Market was valued at USD xx.x Billion in 2023 and is projected to rise to USD xx.x Billion by 2031, experiencing a CAGR of xx.x% from 2024 to 2031.
اقرأ أكثر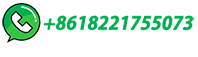
Everything you need to know about Preheaters and …
A more accurate characteristic is a cut size (dpc), which is defined as a particle size for which the efficiency is 50%. This particle size can be calculated approximately by equating the centrifugal force on a particle (due to its angular …
اقرأ أكثر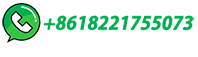
WBC-Primary Cement Equipment Catalog_REV2.indd
non-cement filled. Cement-filled float equipment is, as the name implies, filled with cement during manu-facturing. This "cement" is technically concrete, as it is a mix of cement, coarse aggregate (gravel) and fine aggregate (sand). The concrete used is significantly stronger that cement. Non-cement filled float equipment is, as the name
اقرأ أكثر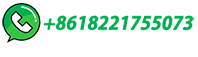
Everything you need to know about cement Materials …
In a cement plant, crushing is the primary size-reduction process carried out under the action of external mechanical forces. Generally, three levels of crushing are recognized: coarse (top product size, up to 150 to 200 mm), intermediate …
اقرأ أكثر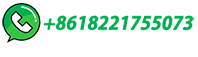
equipment Archives
The cost of investing in a concrete batching plant depends on the scale, ranging from $100,000 to $2,000,000 (about 700,000 to 15 million yuan) for small-scale to large-scale concrete mixing plants.
اقرأ أكثر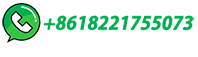
Cement Equipment Product Guidebook
Cement Equipment Product Guidebook .No.8026/E ... ©NTN Corporation . NTN provides a range of products suited for the cement manufacturing process. NTN products are utilized in a diverse range of machinery used with raw materials, and ˜ring and ˜nishing ... POINT Heat-resistant specifications to handle high temperatures. 11 Spherical ...
اقرأ أكثر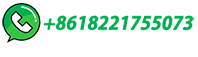
Global Cement Processing Equipment Market Insights and
Cement Processing Equipment Market Size And Overview Our report on the Global Cement Processing Equipment Market provides an in-depth analysis of the market, including its trends, drivers, and ...
اقرأ أكثر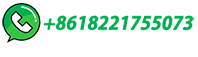
Cement Manufacturing Process
Blast holes are drilled using drilling machines according to the desired length, diameter, spacing, and geometric features. The typical Drill depth and Diameters are: Drill …
اقرأ أكثر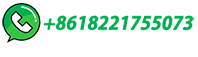