11.6 Portland Cement Manufacturing
Portland cement manufacturing plants are part of hydraulic cement manufacturing, which also includes natural, masonry, and pozzolanic cement. The six-digit Source Classification Code (SCC) for portland cement plants with wet process kilns is 3-05-006, and the six-digit SCC for plants with dry process kilns is 3-05-007. Portland cement accounts ...
اقرأ أكثر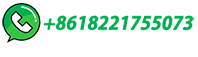
Alternative Fuels in Cement Manufacturing | IntechOpen
Fossil fuels such as coal, petroleum and natural gas provide most of the energy needs of the world today. Coal and natural gas are used in their natural forms, but petroleum and other fossil fuels such as shale and bituminous sands require distillation and refinement to give usable fuels. ... Cement production process . Cement is considered one ...
اقرأ أكثر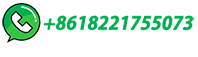
11.6 Portland Cement Manufacturing
11.6 Portland Cement Manufacturing 11.6.1 Process Description1-7 Portland cement is a fine powder, gray or white in color, that consists of a mixture of hydraulic ... The most commonly used kiln fuels are coal, natural gas, and occasionally oil. The use of supplemental fuels such as waste solvents, scrap rubber, and petroleum coke has expanded ...
اقرأ أكثر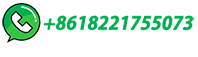
Emissions of Greenhouse Gases in the Manufacturing Sector
The manufacturing sector has used more natural gas than coal since at least 1990. 8 Since 2002, the share of coal in manufacturing's fuel use has fallen from 11 percent to 5 percent, while the natural gas share has grown from 39 percent to 46 percent. Because natural gas releases fewer emissions to generate the same amount of heat, the ...
اقرأ أكثر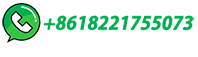
Fuels in the cement industry
The most important gaseous fuel in the cement indus try is natural gas. The main components of natural gas are methane, CH4, and ethane, C2H6. The heavier hydrocarbons such as …
اقرأ أكثر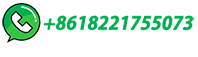
Cement Manufacturing Process
Kiln is heating up from the exit side by the use of natural gas and coal. When material reaches the lower part of the kiln, it forms the shape of clinker. After passing out from the kiln, clinkers are cooled by mean of forced …
اقرأ أكثر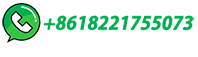
Alternative Fuel Use in Cement Manufacturing
There are three key levers for reducing emissions from cement manufacturing in the short term: improving thermal and electric energy efficiency, reducing the clinker-to-cement ratio by …
اقرأ أكثر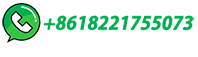
Efficiency enhancement and cost reduction in cement clinker production
The calculations showed that the loss in the cement production process was at a substantial level. To reduce the unit cost and improve the cement kiln performance, it was necessary to carry out improvement studies specific to the cement kiln. ... Natural gas was utilized as a supplementary fuel or for auxiliary processes in cement kilns. It had ...
اقرأ أكثر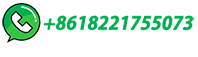
Carbon Capture in Cement Production
Carbon capture in cement production focuses on capturing CO 2 released during the calcination of limestone and fuel combustion in kilns. Technologies like post-combustion capture using …
اقرأ أكثر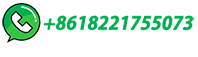
The Cement Plant Operations Handbook
Providing a comprehensive guide to the entire cement production process from raw material ... Gas properties – 5. Plant air distribution – 6. Pitots, orifices and venturis – 7. False air – 8. ... natural or synthetic, for set control, and quite often other components: blastfurnace slag, pozzolan, silica fume, limestone or pulverised ...
اقرأ أكثر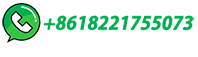
UCLA engineers develop scalable process to decarbonize cement
The new process could significantly reduce greenhouse gas emissions in cement production and, potentially, other industries. Researchers from UCLA's Institute for Carbon Management have developed a method that could eliminate nearly all of the carbon dioxide emitted during the process of cement production, which accounts for about 8% of ...
اقرأ أكثر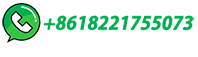
Analysis of material flow and consumption in cement …
Cement production, which is highly dependent on the availability of natural resources, will face severe resource constraints in the future. This is especially true for the cement industry in China.
اقرأ أكثر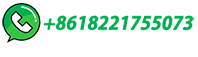
Recent development on the uses of alternative fuels in cement
Generally fossil fuels such as coal, petroleum coke (petcoke) and natural gas provide the thermal energy required for cement industry. Due to environmental concerns, many researchers tried different alternative operating option for coal fired plant. ... The basic chemistry of the cement manufacturing process begins with calcination, the ...
اقرأ أكثر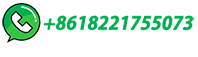
Enhancing energy efficiency and decarbonization of cement …
CO 2 emissions were analyzed at key stages of cement production process, focusing on fuel combustion and carbonate decomposition at the calciner and rotary kiln, with a comparison of the conventional method and the CaL-DRM process to quantify emissions at each stage.
اقرأ أكثر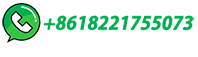
(PDF) Waste Heat Recovery in Cement Production
The cement production process is one of the most energy and cost intensive in the world. In order to produce clinker, a cement industry requires the substantial energy consumption. ... and the cooler to simulate the operating condition and study effect of waste heat recovery and natural gas feed on production and heat consumption. A model was ...
اقرأ أكثر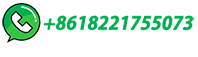
Energy and Economic Comparison of Different Fuels …
In this paper, energy data including specific energy consumption, forms, and types of energy used at different units of cement manufacturing …
اقرأ أكثر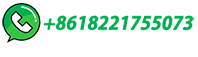
A practical guide to improving cement manufacturing …
The cement production process 1. The Quarry: The cement production process begins ... The heat source to run the very hot kilns can be either coal, natural gas, and/or biofuels. Coal is still used in approximately 90% of cement plants globally to deliver the energy needed for the heat inside the kiln. Online coal analyzers using PGNAA ...
اقرأ أكثر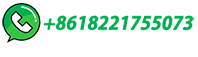
Review Roadmap to a net-zero carbon cement sector: Strategies
The cement production process is initiated with the extraction and processing of raw materials, including limestone, clay, shale, and other supplementary materials (Schneider et al., 2011; Gao et al., 2016). These materials are extracted from quarries and undergo crushing and fine grinding to create a homogeneous raw material mix known as raw meal.
اقرأ أكثر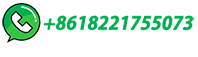
The potential of hydrogen in decarbonising cement
Within the cement manufacturing process, the hydrogen could then used as renewable-based fuel. An example is the Carbon2ProductAustria (C2PAT) scheme that sees synergy between several partners to produce a renewable …
اقرأ أكثر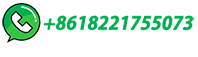
Decarbonisation pathways of the cement production process via …
Technical options for reducing carbon dioxide emissions from the cement production process. Oxy-combustion decreases energy demand by 35% vs the reference …
اقرأ أكثر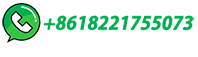
Journal of Cleaner Production
The property method used to simulate the new cement process unit was PR-BM. The molar ratio of natural gas to oxygen in the new cement process was about 3:2, and the molar ratio of natural gas to raw meal was about 1.1:1. The methane was excess in the methane oxidation reaction to achieve a total conversion of oxygen.
اقرأ أكثر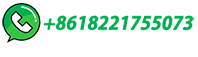
Electrifying the Carbon-heavy Cement Industry
Cement is the world's most massively produced material with over four billion metric tons made a year, and it cranks out enormous emissions due to its production process. Current cement manufacturing requires temperatures …
اقرأ أكثر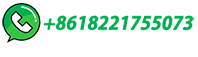
Energy Evaluation of the Cement Manufacturing Process Using Natural Gas
Request PDF | Energy Evaluation of the Cement Manufacturing Process Using Natural Gas-hydrate Technology in Consideration of CO2 Separation | Recently Japanese government' s energy policy calls ...
اقرأ أكثر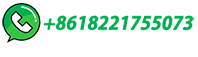
Cement plant flue gas characteristics. | Download Table
The aim of this work was to evaluate the effect of different inorganic compounds as electron donors for the capture of CO2 from a model cement flue gas CO2/O2/N2 (4.2:13.5:82.3 % v/v) using a non ...
اقرأ أكثر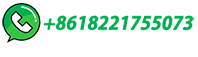
Oil Well Cement Production – Oil Well Cement Uses, Types
Oil well cement, also called oil well Portland cement, is a kind of special cement used for drilling oil well and natural gas well. The oil well cement production process is divided into 5 steps. AGICO offers complete oil well cement production lines.
اقرأ أكثر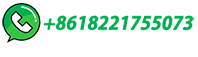
Energy and Economic Comparison of Different Fuels …
In this paper, energy data including specific energy consumption, forms, and types of energy used at different units of cement manufacturing processes were analyzed and compared for...
اقرأ أكثر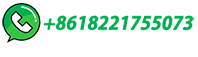
Toward smart and sustainable cement manufacturing process: …
Cement manufacturing is a major contributor to environmental degradation, primarily due to the depletion of natural minerals, the use of fossil fuels, and the emission of significant amounts of CO 2.To mitigate these negative impacts, the industry is actively seeking ways to improve manufacturing efficiency, shift toward renewable energy, utilize alternative fuels, and …
اقرأ أكثر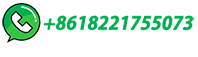
Manufacturing process
The main source of heat is natural gas. Natural gas is fired as a main fuel (100 %) in the main burner rotary kiln and a 95% natural gas and 5.0% heavy oil combination in the combustion chamber. The fuel is used to provide the heat …
اقرأ أكثر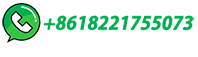
Cement Manufacturing Process and Its Environmental Impact
The cement manufacturing process involves the extraction and processing of raw materials, such as limestone, clay, and shale, which are then heated in a kiln at high temperatures to form clinker.
اقرأ أكثر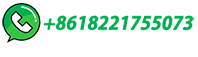
Manufacturing Process – Continental Cement
To save energy, modern cement plants preheat the meal before it enters the kiln. Rising more than 350 feet, hot exit gases from the kiln and clinker cooler combined with fuels such as ground coal, petcoke, natural gas, and recycled waste streams, heat the raw materials as they swirl through the cyclones.
اقرأ أكثر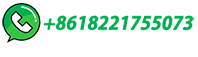