Preparation and properties of fly ash-based geopolymer
The aim of the research was to investigate the influences of high alkaline content foundry sand regeneration wastes incorporated with fly ash in the production of geopolymer concrete. The fly ash-based geopolymer concrete was activated using alkaline solutions of sodium silicate and sodium hydroxide. The geopolymeric products were characterized using X …
اقرأ أكثر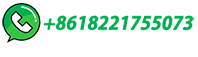
Copper Slag Beneficiation Process & Equipment
Compared with returning slag to smelting, ferric oxide, and some impurities can be removed from the process, and the amount of quartz used in the smelting and blowing process will be greatly reduced. The copper flotation recovery rate is generally above 90%, the copper concentrate grade is greater than 20%, and the tailings contain 0.3% to 0.5% ...
اقرأ أكثر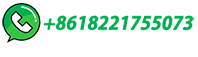
What is Blast Furnace Slag and How to Process It?
Blast furnace slag is a solid waste formed by gangue in ore, ash in fuel and nonvolatile components in solvent (generally limestone) in the process of blast furnace ironmaking. It mainly contains oxides of calcium, silicon, …
اقرأ أكثر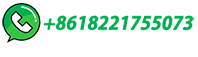
How to Make Cement From Blast-Furnace Slag
The most important method of regulation used with the low-percentage Al2O3 slag cements in the U.S.A. is the Whiting process. This process includes the use of caustic soda, caustic potash, sodium chloride, &c., added either as aqueous solution or in a dry state at some stage of the process of cement manufacture.
اقرأ أكثر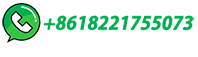
Black Diamond Sand Blast: Effective And Eco-Friendly
The hard, angular particles of the coal slag material enhance speed and cutting, making it perfect for removing paint and rust or cleaning brick and stone. The low free silica content, low dusting, and consistent uniform weight of Black Diamond make it a safer and cleaner option compared to other blasting media.
اقرأ أكثر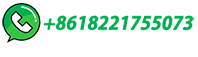
Wet Frac Sand Processing | Agg-Net
The wet processing of frac sand involves taking natural silica sand proppants from the point of a quarried stockpile of silica sand through to the stockpile that feeds the dryer and final dry sizing process.
اقرأ أكثر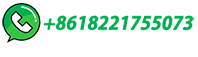
Cement Production
Manufacturing cement at the Lafarge Seattle plant is by a "wet process". As a result, raw materials are mixed with 30 to 40% water during grinding to form well mixed slurry. ... Slag modified portland cement for use in general concrete …
اقرأ أكثر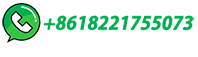
(PDF) Enhancing the Mechanical Properties of Ultra-High
The main goal of this article is to evaluate the enhancement of the mechanical properties of UHPC by replacing silica sand with steel slag at various percentages (25%, 50%, 75%, and ).
اقرأ أكثر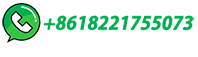
Slag uses in making an ecofriendly and sustainable
Slag, as shown in Fig. 1, is the 16th ingredient of high-performance concrete production [22], called supplementary cementitious materials (SCM) [23], that can enhance the strength and durability of concrete [2].The highly fine slag powder, with a surface area of 400–600 m 2 /kg and a bulk density of 1200 kg/m 3, can be mixed with free lime to replace 40% to 65% …
اقرأ أكثر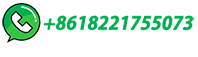
(PDF) Geopolymer Bricks Using Iron Ore Tailings, Slag Sand, …
Similar iron ore tailings are available in other parts of India and world too which have different percentage of iron in the tailings. 2.1.2 Slag sand Slag sand, is an eco-friendly building material obtained as a by-product of the industrial process which can replace conventional river sand in the construction of buildings.
اقرأ أكثر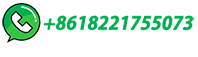
AN IMPROVING PROPERTIES OF WET MIX MACADAM …
sand could be utilized to make this material as environmentally friendly and resolve the problem of its disposal. Similarly, tyre chips are industrial wastes which can be reused. This project discusses about the improvement of Wet Mix Macadam properties of flexible pavement by blending the mix with foundry sand tyre chips and Ferromanganese Slag.
اقرأ أكثر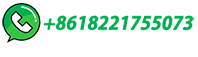
The recycling and reuse of steelmaking slags — A review
For example, if the slag is used in a road surface that gets wet, ... The process of making slag wool involves melting the slag and drawing it through a tap hole. The slag then passes through a jet of air, which disperses the slag into a cone of liquid droplets, which then develop into long fibers. ... An alternative to sand would be BOS slag, ...
اقرأ أكثر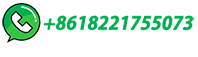
How to Process Slags (with detailed process)? | Fote Machinery
Slag bricks Slag brick production process Slag brick is made by mixing, watering, grinding and pressing slag and limestone. In the production process of slag brick, the particle size of the slag is generally smaller than 8 mm, and the steam temperature injected into the kiln is about 80 ℃ to 100 ℃, the maintaining time is about 12 hours.
اقرأ أكثر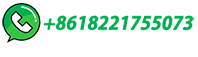
(PDF) RECENT DEVELOPMENTS IN DRY SLAG …
Here we review common slag handling practices, the developments in dry slag granulation over the last three decades, introduce the Ecomaister-Hatch dry slag granulation process, and elaborate on ...
اقرأ أكثر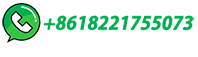
Carbon dioxide-hardened sodium silicate-bonded sand
Moreover, via wet grinding process, D50 of CS was reduced from 15.90 μm of raw CS (RCS) to 2.40 μm, thereby wet grinded CS (WGCS) could further increase the compressive strength of WGGBS mortar ...
اقرأ أكثر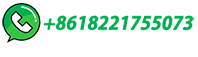
How to Make Sand Bricks | Describe in 8 Steps (2025)
Place the sand bricks in the wet sand, making sure they are covered. 4. Allow the sand bricks to dry for at least 24 hours. ... By following this process, you will make excellent quality and long-lasting sand bricks with minimum effort and time. ... A slag-based mix is perfect for making bricks with metallic sheen or color.
اقرأ أكثر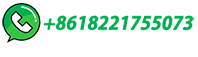
Granulation and Heat Recovery from Metallurgical Slags
In this paper, the slag granulation and heat recovery options are reviewed and given a critical evaluation, aiming to provide a basis for future directions in slag handling. The metals …
اقرأ أكثر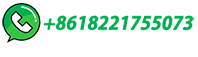
Artificial Sand: Dry And Wet Sand Production
The wet sand making process has a longer history than the dry sand making process. It is a sand making process to remove fine powder and impurities on the surface of machine-made sand by the sand washing machine (wheel or spiral). The wet sand making process is more suitable for places with heavy rain or rich water resources.
اقرأ أكثر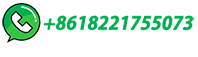
Properties and Uses of Steelmaking Slag – IspatGuru
Uses in flue gas desulphurization and CO2 capture – The method of flue gas desulphurization includes wet process, dry process and semi-dry process, among which wet limestone/lime method is most widely used. Steelmaking slag can be used for desulphurization due to its high CaO, especially free CaO content.
اقرأ أكثر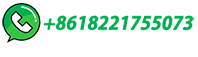
The Differences Between Dry Sand Making and Wet Sand Making
Both dry and wet sand making processes offer distinct advantages and disadvantages, and the choice between them should be based on specific project …
اقرأ أكثر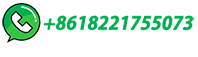
Geopolymer Bricks Using Iron Ore Tailings, Slag Sand
World is pound with million tonnes of industrial wastes such as ground granulated blast furnace slag (GGBS), flyash and mine tailings as a various industrial waste. The best way to make use of these wastes is to incorporate these materials as structural elements, which in turn minimizes the carbon foot print. In this contest, this study focuses on using iron ore tailings …
اقرأ أكثر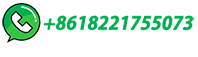
Cement: History, Types, Manufacturing Process
The blending of raw materials can be accomplished through two primary methods: the dry process and the wet process. Dry process. The dry process involves the crushing of raw materials, namely limestone, and clay, into fine powder. These materials are then carefully mixed in precise proportions.
اقرأ أكثر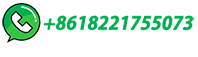
Development of slag-based filling cementitious materials and their
Specifically, the active material is derived from the byproduct of the blast furnace ironmaking process, namely S95 slag powder, sourced from Shijiazhuang Rui Na Mining Products Co., Ltd.; a combination of alkali and salt activation methods is employed, utilizing cement clinker from Zhucheng Yangchun Cement Co., Ltd. as the alkali activator and ...
اقرأ أكثر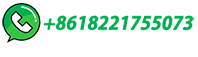
Carbon dioxide-hardened sodium silicate-bonded sand …
Then, they dissolved the quartz sand and waste residue in a hot-pressing environment and filtered and concentrated them to recover sodium silicate. Although the process was complex, it proved that the use of water glass surface film was feasible. The wet regeneration process separated the shell on the sand surface into wastewater.
اقرأ أكثر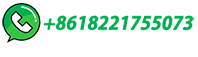
A Succinct Review on Use of Steel Slag in Mortars and Concrete
2.1 Mineralogical Properties of Steel Slag. Steel slag's primary chemical components are CaO, SiO 2, Fe 2 O 3, Al 2 O 3, MgO, MnO, FeO, and several.Steel slag composition alterations are primarily based on raw material, smelting process, and steel type [].Table 1 displays the chemical composition of steel slag and conventional Portland cement. It …
اقرأ أكثر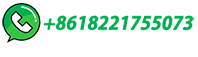
Detailed Performance Analysis of the Wet Extractive Grinding Process
The dosage of converter steelmaking slag (CSS) is less than 20 wt.% in the field of cementitious materials. This work aims to increase the dosage of CSS in cementitious materials containing ...
اقرأ أكثر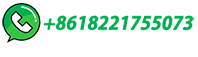
Sand Casting – Process, Sand Properties, Pros & Cons
Key Takeaways. Sand casting is a highly versatile metal casting process that produces components ranging from small pins to large locomotive parts. It accommodates various metals, including ferrous and non-ferrous alloys, making it the most widely used casting method globally.; The properties of moulding sand, such as refractoriness, permeability, thermal …
اقرأ أكثر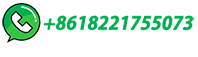
Wet Processing Equipment: The Pros and Cons
There are many equipment choices and system designs to consider when wet processing fine materials to produce sand that meets construction grade specifications for concrete, asphalt or mortar sands.
اقرأ أكثر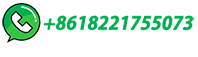
Cement Manufacturing Process: Know Extraction, Processing …
Steps of Cement Manufacturing. The steps involved in cement manufacturing are as follows: Quarrying: Raw materials such as limestone and clay are extracted from quarries or mines.; Crushing and Grinding: The extracted raw materials are crushed and ground into a fine powder.; Blending: The crushed and ground raw materials are blended in specific proportions …
اقرأ أكثر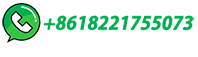