Evaluation of Iron Ore Concentrate and Micropellets as Potential Feed
The use of iron ore concentrate and micropellets as sinter feed was evaluated. Five mixtures containing different proportions of concentrate and micropellets, together with iron ore fines, were granulated and sintered in a pilot scale sinter plant.
اقرأ أكثر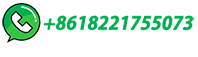
Minerals | Special Issue : Mineralogy of Iron Ore Sinters
Dear Colleagues, Iron ore sintering is an important stage in the production of steel from iron ore. Sinter can constitute more than 60% of ferrous burden in modern blast furnaces in Japan and most blast furnaces in Europe.
اقرأ أكثر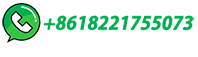
(PDF) Iron Ore Sintering: Process
using large amounts of fine iron ores, including pellet feed. with high iron content. As opposed to the traditional sintering. ... SFCA-I in synthetic iron ore sinter mixtures). Fan et al., 2011.
اقرأ أكثر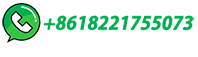
Characterization of Granule Structure and Packed Bed …
The iron ore sintering process produces the main iron-bearing material for blast furnaces in most integrated steel mills. This important pre-processing technology can be viewed as a two-stage process of cold packed bed prepara-tion followed by hot bed transformation. For the cold bed preparation, raw materials including iron ores, fluxes, fuel
اقرأ أكثر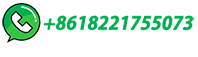
Understanding the high-grade iron ore market
iron ore worldwide at lower in-situ grades (generally about 20-40% Fe), which can be readily enriched ... alternative sinter feed to natural fines. Whether referring to naturally iron-rich DSO fines or lump or artificially enriched beneficiated concentrate, one of the key elements that
اقرأ أكثر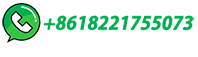
Recent progress in sustainable and energy-efficient technologies …
Iron ore sinter plants are energy-intensive components of integrated iron and steel production (see Table 1), where the iron ore fines (<5 mm) are converted into larger (>5 mm) lump sinter cakes with greater gas permeability, which are the most important burden materials for iron making in blast furnaces (BFs) [7].The main process is shown in Fig. 2 and described in detail …
اقرأ أكثر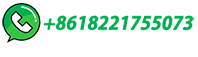
Factors influencing Sinter and Sintering Process
Fig 1 Flowsheet of sintering process. The iron ore fines are natural ore of size 0 mm to 10 mm. The raw mix (also called sinter mix) is made with the weighed amount of iron ore fines, limestone, dolomite, sand or quartzite fines (flux), solid fuel (coke breeze or anthracite) and metallurgical wastes (collected dusts, sludge and mill scale etc).
اقرأ أكثر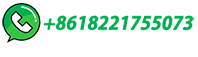
Effect of Metallic Iron Sinter Feed on Sinter Mineralogy and Quality
Effects of Metallic Content on Sinter Cooling Rates. Figure 2 shows the temperature readings registered by thermocouples during sintering and cooling at low vacuum (4-in. Hg or 13.5 kPa) and high vacuum (6-in. Hg or 20.1 kPa) condition. It can be seen that high metallic iron feed (HI) sintering test had lower peak temperature at upper part of bed and …
اقرأ أكثر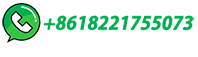
Important iron ore characteristics and their impacts on sinter …
In this review, the sintering process is first described and analyzed to identify the key factors affecting the structure and quality of iron ore sinter. Under fixed sintering conditions, the granulation efficiency, nucleus stability and primary sinter melt volume and properties of the iron ore are considered to have significant influence on the sinter structure and quality. …
اقرأ أكثر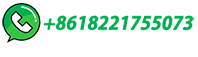
Modelling of Iron Ore Sinter Feed Granulation
Modelling of Iron Ore Sinter Feed Granulation 91. Tata Search, 1997 Where W is moisture content of the granulating charge, g »1 is a minor correction for any entrapped air bubbles in layers
اقرأ أكثر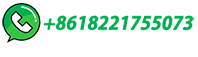
Chemical composition of sinter and iron ore
Download Table | Chemical composition of sinter and iron ore from publication: Assessment of blast furnace behaviour through softening–melting test | Blast furnace operation is a complex ...
اقرأ أكثر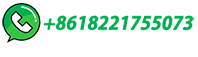
Segregation Charging Behavior of Ultra-Fine Iron Ore
Abstract The sinter–briquette complex firing process which is an effective technology for utilization of low grade ultra-fine ore is a method for charging sinter feed mixed with briquette made of ultra-fine ore. To uniformly fire briquettes using the excess heat from the lower part of the sinter feed bed, they must be segregated in that region. In this study, the particle …
اقرأ أكثر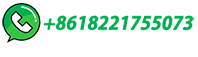
Granulation Effectiveness of Iron Ore Sinter Feeds: Effect of …
Granulation of sinter feeds is an indispensable step in the iron ore sintering process. Through granulating, iron ore fines, fluxes, fuels and recycle materials (e.g., return fines, dust, etc.) are made into granules that possess appro-priate moisture, reasonable size distribution and good bed permeability for sintering.
اقرأ أكثر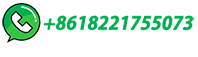
Liquefaction risks
This is misconceived, as non-concentrated grades of sinter feed are the same as iron ore fines, whichthe IMO has ruled should be considered as Group A cargoes (see the Association's circular of 13 December 2010 on Indian iron ore fines and IMO Circular No. DSC.1/Circ.63 of …
اقرأ أكثر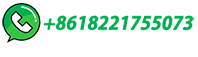
Introduction: Overview of the global iron ore industry
The products include sinter fines, lump ore, and pellet feed which are railed to the Tubarão port near Vitoria for export, with the pellet feed being pelletized in one of the eight Vale solely or jointly owned straight-grate pellet plants prior to export. ... The largest iron ore producer in Russia is Metalloinvest, producing about 40.4 Mt of ...
اقرأ أكثر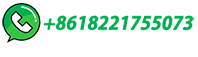
Kinetics of iron ore sinter feed granulation
The kinetics of iron ore sinter feed granalation were shown to have a major impact on granule size distribution. At laboratory scale, it was shown that granule growth continued until a maximum stable size distribution was achieved. Two stages to granule growth were observed. Fine particles quickly adhered to intermediate and large nuclei particles.
اقرأ أكثر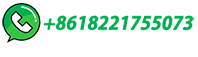
(PDF) Iron Ore Sintering: Process
Sintering is a thermal agglomeration process that is applied to a mixture of iron ore fines, recycled ironmaking products, fluxes, slag-forming agents and solid fuel (coke).
اقرأ أكثر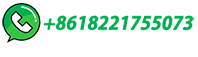
Influence of the material properties of iron ore sinter feed on
The effects of feed properties on the granulation of iron ore sinter feed have been studied using simplified sinter mixes. A measure of granulation effectiveness, x 0.5, has been defined as the particle size at which half the particles act as adhering particles and half as nuclei particles.High values of x 0.5 correspond to large mean granule sizes. . The granulation …
اقرأ أكثر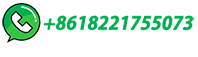
Automated Optical Image Analysis of Iron Ore Sinter
Sinter quality is a key element for stable blast furnace operation. Sinter strength and reducibility depend considerably on the mineral composition and associated textural features. During sinter optical image analysis (OIA), it is important to distinguish different morphologies of the same mineral such as primary/secondary hematite, and types of silico-ferrite of calcium …
اقرأ أكثر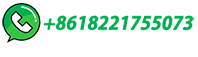
Resurgent demand for iron ore pellet feed to drive wedge within …
The improvement in demand for high-grade iron ore has however, not been uniform, with lower anticipated levels of consumption across Chinese steelmakers, alongside abundant supply in the seaborne market that weighed on prices of high-grade sinter feed cargoes. "Portside volumes of Iron Ore Carajas (IOCJ) fines have remained at record-high ...
اقرأ أكثر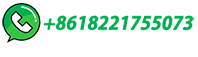
The Relationship Between Mining and Sintering
The sintering process converts fine-sized raw materials, including iron ore, coke breeze, limestone, mill scale, and flue dust, into an agglomerated product, sinter, of suitable size for charging into the blast furnace.
اقرأ أكثر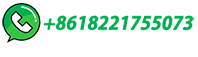
Modeling of Reduction Degradation of Iron Ore Sinter by Feed …
MODELING OF REDUCTION DEGRADATION OF IRON ORE SINTER BY FEED-FORWARD NEURAL NETWORKS Kimmo Kinnunen†, Petteri Laitinen‡ † Rautaruukki Oyj, Production Division, P.O. Box 93, FIN-92101 Raahe, Finland, e-mail: [email protected] ‡ Heat Engineering Laboratory, Abo Akademi University, Biskopsgatan 8, FIN-20500 Abo, Finland, e …
اقرأ أكثر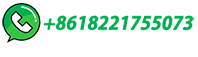
HS Code 26011200
- Iron ore sinter feed (agglomerated, 5mm to 50mm size, 20,000 kg cargo) - Briquettes of iron ore concentrate (agglomerated, 100mm x 50mm x 20mm size, 15,000 kg shipment) - Agglomerated iron ore fines (0.5mm to 6mm size, 25,000 kg per container) - Iron oxide pellets (agglomerated, 12mm diameter, 30,000 kg cargo)
اقرأ أكثر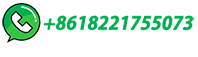
Prediction of the granule size distribution of iron ore sinter feeds
Granulation is the first stage in the agglomeration of iron ore for sinter production. Fine iron ores, fluxes, coke breeze and other fine materials (collected dusts, mill scale) are mixed together to form large and bigger agglomerates [1], [2], [3], [4].
اقرأ أكثر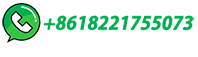
FUNDAMENTALS OF IRON ORE, SINTER FEED AND …
The production of steel often requires to store and handle iron ore, sinter feed and pellet feed in stockpiles, silos, bins, hoppers, feeders, railcars and chutes. However, these materials may experience flow problems such as arching, ratholing, limited storage capacity, erratic flow,
اقرأ أكثر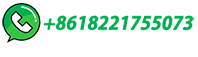
Steel Production | Process Solutions
The raw feed material chemistry changes and the additives feed rates should be adjusted to smooth out these variations in the sinter strand feed chemistry. The basicity of sinter feed material is an important parameter in the efficient operation of the sintering and iron making process and stabilization of the basicity delivers benefits not only to the sinter operations but to the …
اقرأ أكثر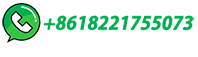
Sticking and Swelling of Iron Ore Pellets: Mechanisms and
According to the Institute for Energy Economics and Financial Analysis (IEEFA) and S&P Global, global iron ore quality is degrading, with the average iron content (Fe%) of global …
اقرأ أكثر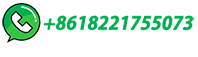
How to Achieve Uniform Sinter Quality
Sinter is the primary feed material for making iron in a blast furnace. During the iron ore sintering process in iron and steel manufacturing, sinter is created by mixing iron ore concentrate with several additives such as limestone and silica to control the chemistry and then igniting it at 1200°C in a continuous belt-fed furnace. The production of high-quality sinter is …
اقرأ أكثر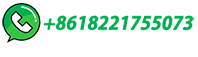
Analysis of a compact iron ore sintering process based on …
The sinter plant receives sinter feed iron ores, solid fuels and slag agents as fine materials from several sources and uses high-temperature reactions to promote the agglomeration phenomena [1], [2] ... The iron ore sinter process is an important operation unit in the integrated steel plant. This unit plays an important role at the steel plant ...
اقرأ أكثر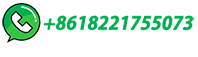