How Is Cement Produced in Cement Plants | Cement Making Process
Phase IV: Calcination. The calcination is the core phase of the cement making dry process. The calcination of the preheated raw meal takes place in the rotary kiln of the cement plant. The rotary kiln is a huge rotating furnace in which the raw meal is heated up to 1450 ⁰C and turned to clinker.
اقرأ أكثر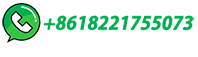
What Do You Know About Wet Process Of Cement Production
Dry process of cement production. The raw materials are dried and ground at the same time, or the raw materials are first dried and ground into raw meal powder and then fed into the dry kiln to be calcined into clinker. However, there is also a method of adding raw meal powder to an appropriate amount of water to make raw meal balls and sending ...
اقرأ أكثر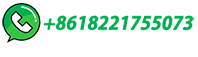
Manufacture of Cement- Materials and Manufacturing …
The raw mix of dry process of corrected slurry of wet process is injected into the kiln from the upper end. The kiln is heated with the help of powdered coal or …
اقرأ أكثر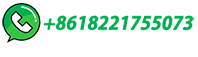
Cement Kilns: Rotary kilns
In the Semi-Wet Process, raw material is prepared as a slurry, but a substantial proportion (50-80%) of the water is mechanically removed, usually by filtration, and the resulting "filter cake" is fed to the kiln system. In the Dry Process, the kiln system is fed with dry raw meal powder. In the Semi-Dry Process, a limited amount of water (10 ...
اقرأ أكثر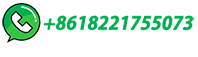
Chapter 4 Cement Manufacturing and Process Control
The most common way to manufacture Portland cement is through a dry process. The first step is to quarry the principal raw materials, mainly limestone, clay, and ... mixed, and fed to the cement kiln. 62 In the cement kiln, all the ingredients are heated to about 1400–1500 °C in huge horizontal cylindrical steel tubular vessel called rotary ...
اقرأ أكثر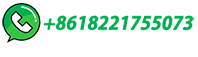
Manufacturing of Cement By Dry and Wet Process
In the manufacturing of cement, the following three important and distinct operationsoccur: 1. Mixing of Raw materials. 2. Burning 3. Grinding The process, by which cement is manufactured, depends upon the technique adopted in the mixing of raw materials. Therefore, on the basis of mixing the …
اقرأ أكثر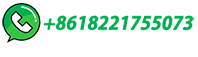
Cement Kiln, Cement Plant Kiln, Kiln In Cement Plant | Shaft Kiln
wet process cement kiln: the cement raw material is grinded with water powder into raw slurry (33-40% water) and then fed into the wet process rotary kiln and burn into cement clinker. dry process cement kiln: the cement raw materials are dried, ground, and calcined into the cement clinker in the dry process rotary kiln.
اقرأ أكثر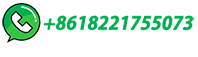
Cement manufacturing process | PPT
It begins with an overview of what cement is and how it is used to make concrete. It then describes the industrial process for manufacturing cement, involving grinding raw materials like limestone and clay at high temperatures in a kiln to form clinker, which is then pulverized with gypsum to become Portland cement powder.
اقرأ أكثر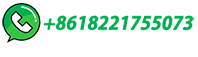
Cement Clinker Manufacturing Process with Reactions
Kiln phase. Since clinker is a complex mixture of ingredients, it requires a multi-staged heat treatment, which is done in the kiln. The main part of the manufacturing process of clinker takes place in the kiln. The stages in the kiln phase are as follows:
اقرأ أكثر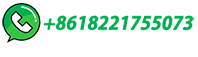
Manufacture of Cement- Materials and Manufacturing Process of …
The raw mix of dry process of corrected slurry of wet process is injected into the kiln from the upper end. The kiln is heated with the help of powdered coal or oil or hot gases from the lower end of the kiln so that the long hot flames is produced. ... Fig: Manufacture of Cement by Dry Process. b) Wet Process The raw materials are firstly ...
اقرأ أكثر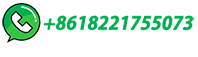
Dry Process of Cement Manufacturing: Step-by-Step …
Among the most popular methods is the dry process of cement manufacturing, renowned for its energy efficiency and reduced environmental impact. In this article, we will explore the key steps, concepts, and advantages of this method.
اقرأ أكثر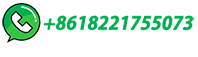
Cement Kilns: Long dry kilns
The kilns of Norman, Kirtlington, Southam, Premier and Ellesmere Port all had a common design: they consisted of relatively short kilns (L/D inside brickwork of 9-19) without any sort of internal heat exchanger, from which the hot dusty exhaust gases were ducted through a rotary raw material drier. All except Norman had hard raw materials suitable for processing by dry grinding.
اقرأ أكثر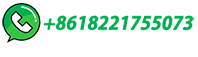
How Cement is Made
Each step of the cement production process is carefully monitored to ensure efficiency and quality. Grinding, Mixing, and Blending ... which uses heat generated by the plant to start chemical reactions between the components—making the next process, kiln firing, even more efficient. ... This happens throughout the manufacturing process ...
اقرأ أكثر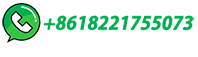
How Cement is Made
Stage 2: Grinding, Proportioning, and Blending The crushed raw ingredients are made ready for the cement-making process in the kiln by combining them with additives and grinding them to ensure a fine homogenous mixture. The composition of cement is proportioned here depending on the desired properties of the cement. Generally, limestone is 80%, and the remaining 20% …
اقرأ أكثر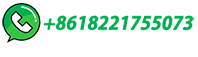
Dry process kiln systems
2 · Dry process kiln systems F.L. offers a range of six standard dry-process kiln systems, each with its unique advantages depending upon the particular application. In this way we are able to provide the industry with the most suitable kiln system configuration for any given set of conditions and requirements.
اقرأ أكثر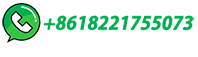
Cement Making Process: Equipment & Manufacturing
Cement manufacturing equipment needs to withstand the heat and the abrasive material from which cement is made. Making cement involves combining raw materials including limestone, clay, and shale, which are milled into a very fine …
اقرأ أكثر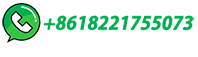
The Cement Plant Operations Handbook
– 5. Drying – 6. Pre-blending – 7. Storage and handling 3. Raw milling and blending 3. Computerised Maintenance Management Systems 30 1. Raw milling – 2. Blending – 3. Kiln feed 4. Flames and fuels 38 1. Chemistry of combustion – 2. Fuels – 3. Physics of combustion – 4. Burner design – 5. Cement kiln burners – 6. Heat ...
اقرأ أكثر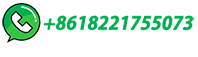
The Cement Manufacturing Process
Cement is a finely ground powder which, when mixed with water, forms a hardening paste of calcium silicate hydrates and calcium aluminate hydrates. ... There are three major variations of dry- process kilns in operation in the U.S.: long dry (LD) kilns, preheater (PH) kilns, and preheater/precalciner (PH/PC) kilns. In PH kilns and PH/PC kilns ...
اقرأ أكثر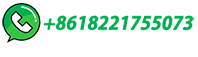
Cement Manufacturing
Cement making process – Raw materials, clinker, cement • Cement Chemist' Language
اقرأ أكثر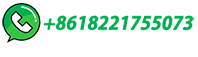
The Cement Manufacturing Process
Rotary kilns are divided into two groups, dry-process and wet-process, depending on how the raw materials are prepared. In wet-process kilns, raw materials are fed into the kiln …
اقرأ أكثر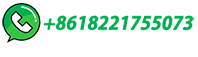
Wet Process vs. Dry Process Cement | LUTON …
Dry process cement is actually a dry-mixed mixture in which dry materials are uniformly mixed. Usually dry process cement is supplied in bulk or in bags. When used, it needs to be mixed with an appropriate amount of water or additives at …
اقرأ أكثر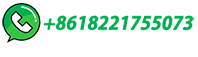
Portland cement manufacture
STEP4: Preheating and precalcining of Portland cement. When the airflow carries the raw meal into the cyclone, it is forced to make a rotating flow in the annular space between the cyclone cylinder and the inner cylinder (exhaust pipe), and it moves downward while rotating, from the cylinder to the cone, and the movement can be extended to the end of the cone, and then …
اقرأ أكثر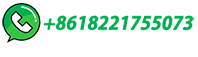
Energy Efficiency Improvement and Cost Saving …
Heat requirements for dry kilns with different number of preheater stages..... 8 Table 2. 2009 Energy consumption and Specific Energy Consumption (SEC) in the U.S. ... Energy efficiency measures in dry process cement plants..... 87 Table 9. Energy efficiency measures in wet process cement plants ..... 88 Figures Figure 1. ...
اقرأ أكثر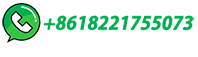
Manufacturing
The basic dry process system consists of the kiln and a suspension preheater. The raw materials, limestone and shale for example, are ground finely and blended to produce the raw meal. The raw meal is fed in at the top of the …
اقرأ أكثر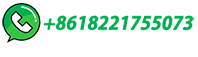
Cement Production Process | Cement Manufacturing …
There are three steps of the high-temperature system: Drying or preheating, calcining, and sintering. The calcining is the core part of the clinker production; the raw meal is weighed and sent into preheater and cement kiln …
اقرأ أكثر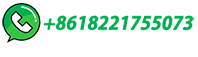
Cement Clinker Calcination in Cement Production Process | AGICO Cement
Dry method cement kiln. In general, the moisture content of materials in the dry method cement kiln is less than 1%, so this kind of kiln can reduce the heat needed for evaporating water. But this method also has its drawbacks, that is, the fluidity of materials in the cement kiln is poor, resulting in uneven clinker composition. Wet method ...
اقرأ أكثر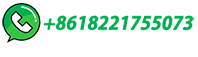
Everything you need to know about Kiln System Operations in Cement
Consider some of the basics of the calcination zone from the standpoint of the energy requirement in the process of making portland cement clinker. The calcination reaction is an endothermic reac-tion (one that occurs with the absorption of heat), and this heat is not recoverable to the process. ... Once water is evaporated, the dry kiln feed ...
اقرأ أكثر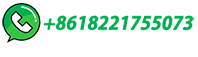
Cement Kilns: Dry and semi-dry process kilns
In the subsequent half century, efficient dry process kilns have almost completely displaced slurry-fed kilns. The pioneering was done by Blue Circle, who had eight dry process kilns in operation before the start-up of Tunnel's Padeswood A3 in 1966. The types of dry process kilns fall roughly into four categories:
اقرأ أكثر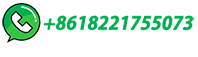
Step-by-Step Guide to the Manufacturing of Cement
In the dry process of cement manufacturing, workers first mine and crush raw materials such as limestone, clay, and sand, then transport them to a grinding mill where they dry and reduce them to a fine powder. They then store this dry …
اقرأ أكثر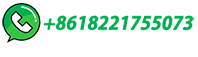
Comprehensive Guide to Cement Kilns: Processes, …
Definition and importance in the cement manufacturing process. Historical development and technological advancements. Types of raw materials used (limestone, clay, etc.). Extraction and transportation methods. Techniques for …
اقرأ أكثر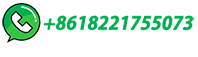