Iron Ore Pelletizing Process: An Overview
Induration process: the green pellets are hardened in a high temperature processing at controlled heating rates, and aiming to achieve the physical and metallurgical require- ments for handling...
اقرأ أكثر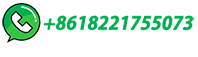
Rio Tinto and H2 Green Steel partner to accelerate the green …
LONDON--(BUSINESS WIRE)-- Rio Tinto and H2 Green Steel, an industrial startup establishing large scale production of green steel, have signed a multi-year supply agreement for high grade direct reduction iron ore pellets from Rio …
اقرأ أكثر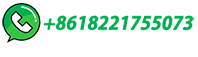
Stegra green iron
To produce green iron, quality iron ore pellets are needed. These pellets must meet stringent criteria to ensure efficient conversion using green hydrogen. By selecting high-quality iron ore pellets from partners like Rio Tinto and Vale, we …
اقرأ أكثر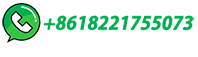
CO 2 -Free Flux for Sustainable Iron Ore Pelletizing
The iron and steel manufacturing sector directly accounts for 7–9% of global CO2 emissions. Raw material preparation, such as iron ore sintering, pelletizing, and cock making, is the major CO2 emitter. As climate change becomes a bigger concern, steel manufacturers need to lower CO2 emissions without hindering efficiency or increasing costs. In recent years, the …
اقرأ أكثر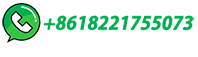
Investigation of cigarette effect and elastic-plastic behavior of green
The green iron pellet demonstrates elastic-plastic deformation behavior during classification on a roller screen, which has a significant effect on its inefficiency due to the occurrence of ...
اقرأ أكثر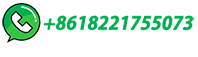
The effects of iron ore concentrate grinding methods (HPGR and …
Particle size and shape of iron ore concentrate are effective parameters in the production of quality green pellets. In this research, the effect of particle morphology on green pellet quality was ...
اقرأ أكثر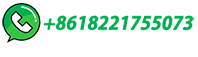
Investigation on Loss on Ignition to Study the Effect of Iron Ore
This study corroborates that the iron ore mineralogy has significant effects on green pellet growth and its properties by both experimental and mathematical arguments. In this context, three iron ore samples with different loss on ignition (LOI): 2.64, 4.85 and 9.19 wt.% were taken. The mineralogical differences were investigated through X-ray diffraction, thermogravimetric …
اقرأ أكثر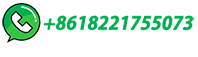
Investigation of cigarette effect and elastic-plastic behavior of green
The green iron pellet demonstrates elastic–plastic deformation behavior during classification on a roller screen, which has a significant effect on its inefficiency due to the occurrence of phenomena such as the cigarette effect. This phenomenon causes the quantity and quality of produced pellets to drop by transferring the on-size pellets to ...
اقرأ أكثر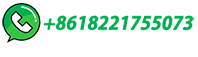
NextGen Pelletizing™
Iron ore pelletizing is crucial for the "green" future Outotec Traveling Grate Pelletizing The traveling grate indurating process is responsible for two-thirds of the world's installed pelletizing capacity. Outotec offers the industry's leading induration technology for iron ore pellet processing, which is based
اقرأ أكثر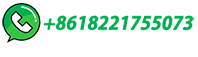
Iron Pellets | High-Quality Iron Pellets for Steel Manufacturing and
By improving furnace operations and reducing emissions, iron pellets contribute to eco-friendly and sustainable steel manufacturing. Key Benefits of Iron Pellets: 1. High Iron Content for Efficient Steel Production: - Iron pellets typically contain between 63% and 67% iron, providing a highly efficient source of iron for steel production.
اقرأ أكثر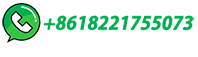
Iron ore pelletization
Green pellets are made by combining moist ore with a binder and rolling it into balls using either a pelletizing disk or a pelletizing drum. The green pellets are then dried, preheated, and finally heated to a temperature below the melting point of iron oxides, approximately 1300°C, to achieve strength.
اقرأ أكثر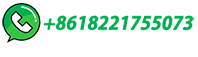
Breakage of green iron ore pellets | Request PDF
Mechanical degradation of green iron ore pellets prior to induration is a concern and can result in return of material to discs or drums or contamination of the feed to the induration furnace ...
اقرأ أكثر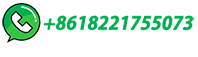
Why green iron ore may be the next big wave
A novel composite binder (humic acid modified bentonite, HAMB) and two other binders (bentonite and Modified humic acid, MHA) were used to explore the effects of binders on the …
اقرأ أكثر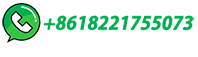
Chapter 3 Pelletization | PDF | Iron Ore | Porosity
The document discusses the pelletization process used to agglomerate iron ore fines into pellets suitable for use in iron and steelmaking. It describes the steps involved, including mixing the iron ore concentrate with additives and binders, forming green pellets in a drum or disc pelletizer, and indurating the pellets in a kiln. The properties and standards required of the iron ore pellets ...
اقرأ أكثر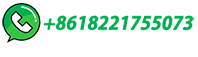
Mechanical strengths of green pellet.
Mechanical strengths of green pellet. The present study aims to investigate the use of mixed hematite and magnetite ores in iron ore pellet production. Pelletizing tests were carried out...
اقرأ أكثر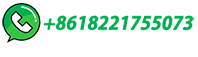
A study on plasticity and compression strength in wet iron ore green
Therefore, in iron ore green pellets balled with a viscous binder, the main binding force originates from the viscous binder; only less than one half of the binding force is due to the capillary force. The most common binder in the iron ore industry is bentonite, which is a tixotrop. Bentonite is known to increase the green pellet wet-CS, dry ...
اقرأ أكثر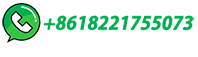
Iron Ore Pelletizing Process: An Overview
Balling process: the green pellet is the rolled pellet without any thermal process. It is obtained under strict control of moisture and has a spherical shape and diameter of 8–16 mm; ... The final use of iron ore pellets in ironmaking reactors requires minimum mechanical properties. Pellets must withstand tumbling and falling during transport ...
اقرأ أكثر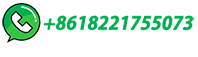
Drop strength measurement of green pellet based on drop …
The construction of blast furnace charge structure based on pellet and the development of short process from non-blast furnace to electric furnace will be an efficient way to accomplish "carbon peak, carbon neutral". Since drop strength is one of the most crucial quality indexes for green pellet, the crack detection in the collision process is an indispensable …
اقرأ أكثر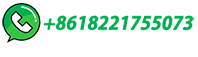
Binding mechanisms in wet iron ore green pellets with a bentonite
As industrial iron ore green pellets were found to be oversaturated, the influence of liquid viscosity on green pellet growth rate could be explained by a simpler mechanism, namely, by the viscosity in the superficial liquid layer. The viscosity needs to be such that the surface water layers on the colliding objects can coalesce within the time ...
اقرأ أكثر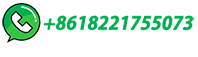
Improving the roller screen efficiency to classify green iron pellets
Modeling and simulation of green iron ore pellet classification in a single deck roller screen using the discrete element method. Powder Technol. (2018) B. Barbabela et al. Improvement in roller screening of green iron ore pellets by statistical analysis and discrete element simulations. Miner. Process. Extr. Metall. Rev.
اقرأ أكثر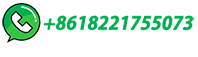
Detection and segmentation of iron ore green pellets in
In steel manufacturing industry, powdered iron ore is agglomerated in a pelletizing disk to form iron ore green pellets. The agglomeration process is usually monitored using a camera. As pellet size distribution is one of the major measures of product quality monitoring, pellets detection and segmentation from the image are the key steps to determine the pellet …
اقرأ أكثر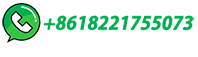
Online size distribution measurement of dense iron green pellets …
As the disc continues to rotate, the iron ore fines accumulate into increasingly larger green pellets and are eventually discharged from the rotary disc as the final product [2]. The pellet size distribution is a key quality indicator that affects the combustion efficiency of the blast furnace and the quality of the iron ore pellets [3 ...
اقرأ أكثر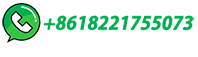
Green Pellet
Green pellets are made by combining moist ore with a binder and rolling it into balls using either a pelletizing disk or a pelletizing drum. The green pellets are then dried, preheated, and finally …
اقرأ أكثر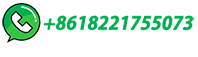
Improving the Properties of Magnetite Green Pellets with a Novel
The drying process of green pellets of iron ore concentrate is an intermediate step in the preparation of green pellets and preheating and roasting of pellets, which is usually realized by convective heat transfer with hot air. Setting the pellet drying stage can prevent the green pellets from cracking and pulverizing in the preheating stage ...
اقرأ أكثر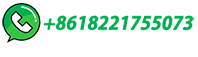
Iron Ore Pellets – IspatGuru
On the other hand, the increased carbon content in the pellets produced with high reducible iron ore in the green pellets lead to a negative scenario regarding the mechanical strength. The results show that for the firing conditions as per the industrial practice, the limitation related to the carbonaceous material addition in the pelletizing ...
اقرأ أكثر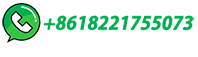
(PDF) The effect of particle size on green pellet …
For example, the particle size distribution of iron ore fines is important because green pellets adhere together through capillary and viscous forces from the liquid trapped between solid ...
اقرأ أكثر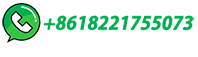
(PDF) The effect of particle size on green pellet …
In this work, using high-silicon iron ore concentrates as raw material, the effect of high-silicon iron ore concentrates with different particle size on the oxidation behavior of pellets was...
اقرأ أكثر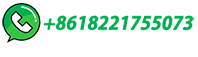
An industrial image processing-based approach for estimation of iron
Green pellets are produced primarily from crushed iron ore in a rotating pelletizing disk, and then baked in a furnace to produce hardened black pellets. Since iron ore pellets provide consistent and high quality iron feed to the furnace, they are particularly useful products for steel manufacturers [1] .
اقرأ أكثر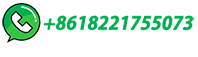
Iron Ore Pelletizing Process: An Overview
The optimum moisture content and particle size distribution are two decisive factors for green pellets formation. The moisture interferes with two important properties of green pellets: compressive strength and drop resistance.
اقرأ أكثر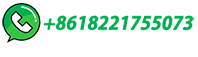
Drying and Roasting Characteristics of Iron Ore Pellets with
Drying and roasting behavior of iron ore pellets with microwave and conventional heating have been comparably investigated. The results showed that the dehydration time of green pellets can be shortened by approximately two-thirds with microwave heating. Meanwhile, the average compressive strength of pellets with organic binders dried by microwave heating reached 40 …
اقرأ أكثر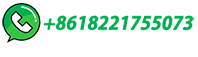