how is wet processing of iron ores.md
Contribute to dinglei2022/en development by creating an account on GitHub.
اقرأ أكثر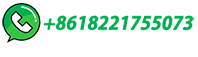
Beneficiation of Fine Iron Ores using the Desand Process
A new two-stage wet gravity separation flow sheet, referred to as the desand' process, has been designed to overcome these issues for the upgrading of low-grade clay-rich goethitic or hematite-quartz fine iron ores. The desand process is designed to treat the -1.0 mm range from -8.0 mm natural fines, to recover a -1.0 +0.038 mm higher-grade ...
اقرأ أكثر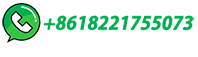
Iron Ore Processing
Iron ore quality in India is deteriorating due to continual increase in consumption of good grade ores. It is imperative to use low grade iron ores to meet the current demand. In the Jharkhand …
اقرأ أكثر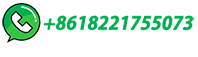
Recovery of Iron Ore Fines and Ultrafines from Tailings byUsing Wet
In addition, consideration is given to dewatering of iron ore product and tailings.Two types of tailings have been identified for processing. Firstly, tailings that have already been deposited in a tailings storage facility, and secondly, live tailings streams from an existing wet iron ore beneficiation plant.
اقرأ أكثر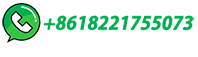
Mineral Processing Plants: What You Need to Know
A mineral processing plant is a place dedicated to processing ores, converting raw ores extracted from mines into high-grade mineral products or metals through a series of physical and chemical methods.
اقرأ أكثر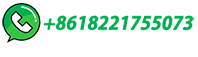
Iron ore – tailored solutions
Dewatering iron ore concentrates is a crucial step in enhancing their handling and transportation by removing excess water. The selection of a suitable dewatering method depends on various factors, including moisture content, particle size distribution, and …
اقرأ أكثر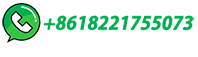
Seminar on iron ore beneficiation in india | PPT
3. Wet Processing The wet processing circuit is generally practiced for low/medium-grade (60-62% Fe) hematite iron ore. The process consists of multi-stage crushing followed by different stages of washing in the …
اقرأ أكثر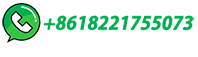
Iron Ore Tailing Beneficiation
not only enhance the life of the existing operating mines but also finds the route to achieve the sustainable process. Iron ore tailing/slime (-150 μm) is produced after scrubbing and wet screening of a low-grade iron ore. Tailing beneficiation of iron ore has been addressed either by flotation or wet high intensity high gradient separation.
اقرأ أكثر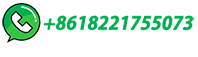
Beneficiation of Iron Ores
Fig 3 Types of processing ores. The wet processing (Fig 4) is normally practiced for low / medium grade (60 % Fe to 63 % Fe) hematite iron ore. The wet process consists of multi-stage crushing followed by different stages of washing in the form of scrubbing and / or screening, and classification etc., but the advantage is only partial removal of adhered alumina and free …
اقرأ أكثر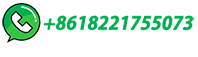
Wet Drum Separator [LIMS] for Iron Ore …
The MAGQUIP SCC Wet drum separator is a multi stage, low intensity wet drum separator with a "steffensen" semi counter-current tank style and axial "interpole" type magnet arrangement which is typically used in the "finishing" stage for the …
اقرأ أكثر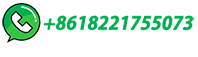
Wet High Intensity Magnetic Separation
WHIM is the short acronym for Wet High Intensity Magnetic Separation. At present, most U.S. iron raw materials are produced from magnetic taconites, which are ground to a nominal minus 270 mesh (53 micrometers), …
اقرأ أكثر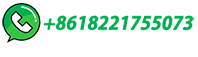
Developments in the wet and dry processing of lower grade magnetite ores
The results of early laboratory test work on the development of an efficient and environmentally sustainable dry processing option for the beneficiation of lower grade magnetite ores were tabled by IMP Technologies Pty. Ltd. (IMPTEC) and Cyclomag Pty.Ltd. at Iron Ore 2017 in Perth W.A. Since that time, the companies have experienced increasing demand for laboratory testing of …
اقرأ أكثر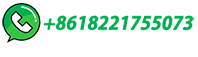
Pelletisation process | PPT
2. Introduction To Pelletisation Process Pellets are spherical balls formed by the agglomeration of natural or ground iron ore fines in the presence of moisture and binder These green balls of 5 – 20mm size are then dried, preheated and fired at 1250 – 13500 C Bonding is developed between the fine ore particles at such high temperatures Additives like Bentonite, …
اقرأ أكثر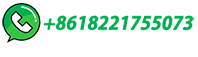
Vale to invest 11 billion reais in dry iron ore processing over the
In Carajás, as the iron content is already high (above 64%), the ore is only crushed and sieved, so it can be classified by size (granulometry). In Minas Gerais, the average content is 40% iron, contained in rocks known as itabirites. To increase the content, the ore is concentrated by means of wet processing (with water).
اقرأ أكثر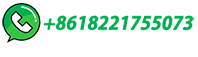
Iron Ore Processing
covering crushing, screening or wet circuit consisting of crushing, scrubbing, washing and classification [3-4]. This kind of simple approach of washing and scrubbing is not sufficient enough to produce iron ... Iron Ore Processing 503. 5 Tabling of -1+0.1mm fraction The (-1+0.1 mm) fraction so obtained from scrubbing and wet screening ...
اقرأ أكثر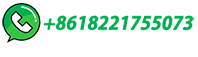
Ball Mill and Crusher for Iron Ore in Mineral Processing
Iron ore is one of the most important minerals in the world, serving as the primary raw material for steel production. As demand for steel continues to grow globally, efficient and reliable processes for extracting iron from its ore become crucial. Two critical pieces of equipment used in this process are the ball mill and the crusher.These machines play vital roles in the …
اقرأ أكثر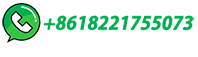
Iron Ore Processing: From Extraction to Manufacturing
Iron ore processing is a complex and vital process that transforms raw iron ore into usable steel. From exploration and extraction to grinding, beneficiation, and ironmaking, each stage plays a crucial role in producing …
اقرأ أكثر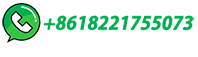
The Iron Pelletizing Process
The most commonly employed agglomeration technique is pelletizing by which a mixture of iron ore, water, and binder is rolled up in a mechanical disc or drum to produce agglomerates (green or wet pellets). Figure 1: Iron pellets The pelletizing process is a process which contains numerous sub-processes, or process segments. On the way from the ...
اقرأ أكثر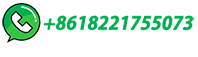
Processing options for removal of silica and alumina from low …
Global demand for iron and steel has increased substantially over the past 20 years and there has been a greater focus on developing suitable processing options to treat low-grade hematite-goethite ores containing higher levels of silica and alumina impurities. The processing applicable to reduce the impurity levels in these lower-grade iron ores depends on their mineralogy and a …
اقرأ أكثر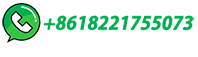
Physical separation of iron ore: magnetic separation
Most iron ore processing takes place in the fine particle size ranges and is often carried out on a wet basis. However, some iron ore resources are located in dry areas where adequate water supply is very difficult to obtain and hence dry processing is the only option.
اقرأ أكثر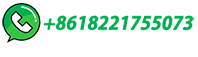
Iron Mining Process
At the processing plant, the taconite is crushed into very small pieces by rock crushing machines. The crushers keep crushing the rock until it is the size of a marble. The rock is mixed with water and ground in rotating mills until it is as fine as powder. Separation The iron ore is separated from the taconite using magnetism.
اقرأ أكثر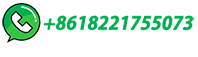
A critical review on metallurgical recovery of iron from iron ore
Fig. 2 illustrates the iron ore beneficiation process, particularly magnetic separation, resulting in the generation of inevitable tailings. Due to the characteristics of iron ores and the conditions during beneficiation, it is inevitable that approximately 2.5–3 tons of IOTs are generated for every 1 ton of iron ore concentrate produced [7].In 2019, the global annual …
اقرأ أكثر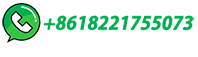
Indian Iron Ore Scenario : Low Grade Iron Ore Beneficiation
Significant quantity of slimes, about 18 - 25 % of ROM has been generated during wet processing of the high grade iron ore. The amount of iron ore being lost in the tails is of the order of 10 - 15 Million tonnes per year.
اقرأ أكثر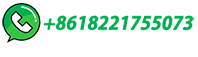
CURRENT PRACTICES IN INDIAN IRON ORE …
• The wet processing circuit is generally practiced for low/medium-grade (60-62% Fe) hematite iron ore. The process consists of multi-stage crushing
اقرأ أكثر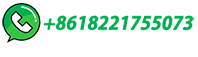
Exploring Low-Grade Iron Ore Beneficiation Techniques: A
The beneficiation of low-grade iron ores is a key research and development topic in the mineral processing industry. The gradual exhaustion of high-grade iron ore reserves, and rising consumer iron and steel demand globally necessitate efficient low-quality iron ore beneficiation to meet steelmaking quality requirements. This comprehensive review explores …
اقرأ أكثر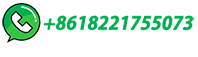
Iron Ore
Iron ores are rocks from which metallic iron can be economically extracted. ... Sino Iron produced and shipped more than 19 million wet metric tonnes of magnetite concentrate to the company's steel plants and Asian steel mill customers. Project owner Citic Ltd has stated that improvements in its processing lines, ...
اقرأ أكثر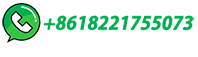
Crushing and Grinding Wet & Sticky Ore
Solution to the Wet Ore Processing Problem. A washing section is a "must" in all operations handling wet, sticky ore. This facilitates ore handling, crushing, and also affords a means for separation of primary slimes and …
اقرأ أكثر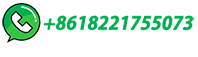
Iron Ore production in the Pilbara
Activities involved in finding, mining and processing iron ore at our Pilbara operations have been simplified in the following diagram. Rio Tinto operates 11 iron ore mines in the Pilbara and the specific ... Processing may be wet or dry. Stockpile and rail-load out The processed ore is stockpiled and blended to meet product quality
اقرأ أكثر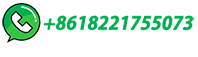
Iron Mining Process
The iron ore is separated from the taconite using magnetism. The remaining rock is waste material and is dumped into tailings basins. The taconite powder with the iron in it is called concentrate.
اقرأ أكثر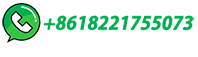
What is an iron ore wet plant? | Shibang China
An iron ore wet plant, also known as a wet processing plant, is used to process iron ore. The processing method involves the use of water to wash and classify the iron ore,...
اقرأ أكثر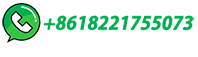