CN114849582A
The invention relates to the technical field of wastewater treatment, in particular to a wastewater desulfurization device for production in a rotary kiln factory, which comprises a main body mechanism, wherein a stirring mechanism is matched and rotated on the main body mechanism; a material storage mechanism is fixed on the main body mechanism; the material storage …
اقرأ أكثر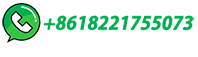
Coprocessing of Stainless-Steel Pickling Sludge with Laterite Ore …
The rotary kiln-electric furnace (RKEF) process is one of the most efficient ferronickel production technologic route, where the feed is usually pre-reduced in a rotary kiln …
اقرأ أكثر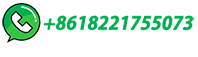
(PDF) i) Direct Reduced Iron: Production
In book: Encyclopedia of Iron, Steel, and Their Alloys (pp.pp 1082-1108) Chapter: i) Direct Reduced Iron: Production; Publisher: CRC Press, Taylor and Francis Group, New York.
اقرأ أكثر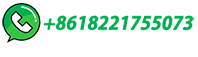
Modelling and optimization of a rotary kiln direct reduction process
Rotary kilns are used for a range of mineral processing operations. Kilns range in size from 2-6 m in diameter and can be 50-225 m long with an operating mass of up to 3000 t. Two of the most …
اقرأ أكثر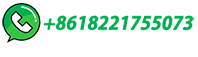
Coprocessing of Stainless-Steel Pickling Sludge with Laterite Ore …
The sulfur distribution within the entire smelting process is systematically analyzed, determining that the critical procedure for pressuring the desulfurization system is the rotary ...
اقرأ أكثر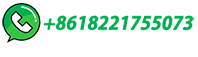
CN112237816B
The invention discloses a rotary kiln flue gas desulfurization method and an ion exchanger used for the method, comprising the steps of enabling sulfur-containing flue gas to sequentially pass through a filtering device for absorbing large particles and an active carbon adsorption device for absorbing small particles, then enabling the sulfur-containing flue gas to enter a desulfurization ...
اقرأ أكثر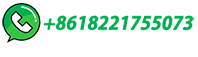
Green Low-Carbon Tech: Rotary Kiln Pelletizing Flue Gas …
Innovative green low-carbon technology for rotary kiln pelletizing with ultra-low emission flue gas processing, featuring SNCR and SCR denitrification and semi-dry …
اقرأ أكثر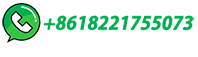
Desulfurization of petroleum coke during its calcination in a rotary kiln
The patent application describes a method and apparatus for desulfurizing green petroleum coke during its calcination in the rotary kiln. Water vapor is introduced through the refractory lining of the rotary kiln into the underside of the bed of petroleum coke in the temperature range of 800-1200 ° C. Hydrogen is generated by the reaction of the water vapor with the carbon material …
اقرأ أكثر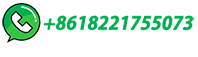
sbm/sbm rotary kiln desulfurization in gold process.md at main
Contribute to chengxinjia/sbm development by creating an account on GitHub.
اقرأ أكثر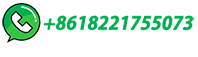
Enhancing Rotary Kiln-Electric Furnace Process of Saprolitic
How to reduce the energy consumption of the rotary kiln-electric furnace (RKEF) process has become an important issue for the stainless steel industry. The aim of this study is to reduce the energy consumption of ferronickel production from saprolite nickel laterite in the RKEF process. The effects of the slag binary basicity, FeO content, and Cr2O3 content on the …
اقرأ أكثر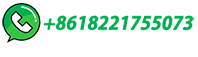
Hazardous waste incineration in a rotary kiln: a review
Hazardous waste incineration in a rotary kiln: a review Xuguang Jiang1 · Yanhui Li 1 · Jianhua Yan1 Received: 23 January 2019 / Revised: 16 March 2019 / Accepted: 19 March 2019 / Published online: 18 April 2019 ... process, the incineration law cannot be validated in a limited timeframe by experiments. Researchers often use computer
اقرأ أكثر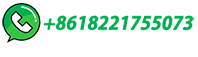
Method for flame control in a rotary lime kiln
Process and apparatus for improving the combustion of secondary fuel in a rotary kiln and process for retrofitting a rotary kiln with a burner assembly (22) 04.10.2013 (43) 20.08.2015 (57) The present invention relates to a process and apparatus for improving the combustion of a secondary fuel supplied in a first stream in a rotary kiln ...
اقرأ أكثر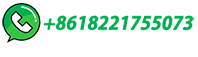
Elevated short-process energy-saving novel RKEF (Rotary Kiln …
The invention discloses an elevated short-process energy-saving novel RKEF (Rotary Kiln Electric Furnace) ferro-nickel alloy production process, comprising the following steps: (1) drying; (2) burdening; (3) roasting-prereduction; (4) electric furnace smelting; and (5) casting molding. The invention also discloses elevated short-process energy-saving novel RKEF ferro-nickel alloy …
اقرأ أكثر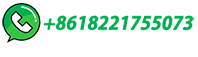
Fixing sulfur dioxide by feeding calcine oxide into the rotary
Sulfur dioxide (SO2) is a toxic pollutant and its fixation is a high cost but imperative task for sulfide metallurgy industry. Although being a mature technology for on-line fixation of SO2 by limestone injection in coal-fired boilers, its application is rarely investigated in the sulfide metallurgy plant. Extending this technology to the metallurgy industry is highly plausible, but …
اقرأ أكثر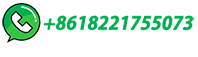
Hazardous waste incineration in a rotary kiln: a review
Hazardous waste output in the world is increasing every year. To achieve higher efficiency and lower pollution, the incineration technology for hazardous waste needs to be studied further. This study mainly reviews the research progress in incineration, slagging, and pollutant emission in the rotary kiln in China and abroad in the last 10 years, and conducts a …
اقرأ أكثر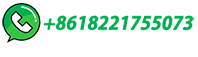
Improving long-term operation performance of hazardous waste rotary
The stable operation and management of rotary kiln incineration facilities are very important, and they still face severe challenges. For instance, the production capacity of current facilities is generally unsatisfactory, owing to factors such as unstable operating conditions, unskilled work operations, low level of equipment operation and maintenance, and …
اقرأ أكثر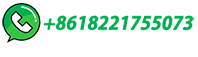
Rotary Tube Firing – An Increasingly Popular Option
Explore NUTEC Bickley's rotary tube kilns, ideal for gold mining, material purification, and sustainable processes with high efficiency and customization.
اقرأ أكثر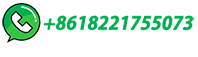
Enhancing Rotary Kiln-Electric Furnace Process of Saprolitic
How to reduce the energy consumption of the rotary kiln-electric furnace (RKEF) process has become an important issue for the stainless steel industry. The aim of this study …
اقرأ أكثر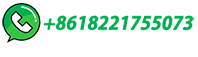
Rotary kiln process: An overview of physical mechanisms, …
The heat and mass transfer modeling process in rotary kilns is summarized. The commonly used correlations involving rotary kilns are categorized by application. The solid-wall heat exchange coefficient is examined.
اقرأ أكثر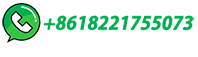
Coprocessing of Stainless-Steel Pickling Sludge with Laterite Ore …
The rotary kiln-electric furnace (RKEF) process is one of the most efficient ferronickel production technologic route, where the feed is usually pre-reduced in a rotary kiln at 800–950 °C followed by reduction smelting at 1500–1550 °C in an electric furnace for the separation of alloy from slag (Li et al., 2015; Li et al., 2012; Rao et al ...
اقرأ أكثر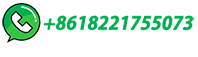
CN102818449A
A process of roasting refractory gold comprises the steps of preparing sulfuric acid by using SO2 after vacuum dehydration, desulfuration and dearsenification. ... The vacuum rotary kiln is used for roasting in a metallurgy process, so that heat of mineral itself can be sufficiently used. Thus, the vacuum rotary kiln has the advantages of ...
اقرأ أكثر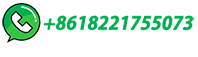
Novel method for temperature prediction in rotary kiln process …
The dimensions and process parameters of the rotary kiln in this study were determined on a 1:1 scale based on a steel company, ensuring authenticity. ... (Intel(R) Xeon(R) Gold 6248R CPU with 3.00 GHz and 2.99 GHz dual processors and 128 GB of RAM on board) Soft Measurement Methods: 5–6 s: Python on a workstation:
اقرأ أكثر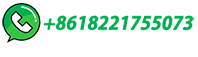
CN221788579U
The utility model relates to the technical field of rotary kiln production smoke discharge, and discloses a dry rotary kiln tail smoke pipeline desulfurization device, which comprises a rotary kiln desulfurization tank body, wherein a smoke secondary treatment bin is arranged on the side edge of the rotary kiln desulfurization tank body, a smoke channel is arranged on the side edge of …
اقرأ أكثر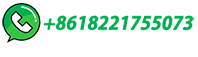
Gold Ore Roasting Techniques
the rotary kiln; the vertical, multiple-hearth furnaces with rabble arms attached to a central shaft, of which the Wedge furnaces are typical; and; the Dorrco FluoSolids reactor. Recover Gold by Roasting Pyrite Ore
اقرأ أكثر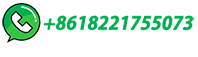
Clarifying the decomposition process of pyrite and SO2 release in …
The new suspension preheater dry rotary (NSP) kiln system is widely adapted to produce Portland cement clinker, which can be divided into raw materials processing, raw meal proportioning and grinding, raw meal preheating and precalcination, and clinkerization processing, as shown in Fig. 1. ... Process compatible desulfurization of NSP cement ...
اقرأ أكثر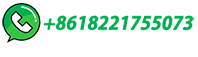
Magnetization roasting process of iron ores in the rotary kiln.
Download scientific diagram | Magnetization roasting process of iron ores in the rotary kiln. from publication: Recent Advances in Magnetization Roasting of Refractory Iron Ores: A Technological ...
اقرأ أكثر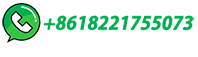
Zinc Oxide Rotary Kiln Project Case
After multiple demonstrations, a zinc oxide rotary kiln solution suitable for local resources and needs was selected. Equipment Selection and Design. The most advanced rotary kiln technology on the market is adopted, including multi-stage heating, temperature control precision control system, and efficient dust removal and desulfurization ...
اقرأ أكثر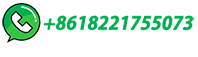
Quality and Process Performance of Rotary Kilns and Shaft …
Rotary kilns have been used successfully for many years to produce calcined coke for the aluminium industry and they offer a high level of automation, performance and flexibility. Shaft calciners make a high bulk density, coarse particle size product and several papers have been published recently highlighting these benefits. This paper presents a comparison of the …
اقرأ أكثر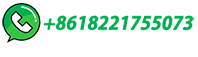
CN215027589U
The utility model discloses a rotary kiln sweetener, comprising a tower body, the tower body upper end is provided with the gas outlet, be provided with the air inlet on tower body bottom one side, the tower body inboard down has set gradually the defroster from last, has sprayed the mechanism, has divided cigarette mechanism and reservoir.
اقرأ أكثر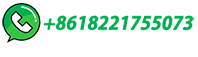
Numerical simulation of a rotary kiln for fine control of the rutile
The calcination of titanium dioxide (TiO 2) is one of the most important processes for its production, during which the feedstock is heated by the hot gas in a rotary kiln, experiencing drying, desulfurization, anatase-to-rutile crystal phase transformation and crystal growth.The product quality of titanium dioxide as a white pigment highly depends on the conversion …
اقرأ أكثر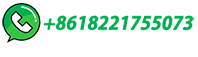