Pelletisation process | PPT
2. Introduction To Pelletisation Process Pellets are spherical balls formed by the agglomeration of natural or ground iron ore fines in the presence of moisture and binder These green balls of 5 – 20mm size are then dried, preheated and fired at 1250 – 13500 C Bonding is developed between the fine ore particles at such high temperatures Additives like Bentonite, …
اقرأ أكثر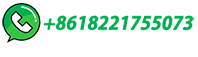
SINTERING AND PELLETISATION OF INDIAN IRON ORES
High grade iron ore less than 10% of the total reserves. ROM iron ore with Fe less than 58 – 60% discarded as waste. After beneficiation iron ore availability can improve by about 50%. Steel community and the country demand technological solutions for utilising low grade ores. The technology task that would be imperative: 1.
اقرأ أكثر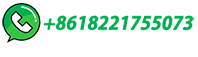
Advances in Sintering and Pellet Technology
The objective of iron ore agglomeration is to generate a suitable product of granules in terms of thermal, mechanical, physical, and chemical properties. ... The double-layer ignition sintering process can reduce the emission of nitrogen oxides in the sintering process under the condition of guaranteeing the quality of sinter, which has great ...
اقرأ أكثر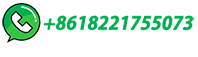
Iron Ore Pelletization: Part I. Fundamentals | Request PDF
Comminution, separation and agglomeration are the three typical processes applied to increase the grade of iron ore. Agglomeration is the process of converting iron ore fines into easily handled ...
اقرأ أكثر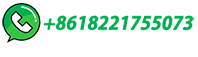
THE POTENTIAL OF PELLETIZING FOR IRON ORE …
The growth agglomeration of iron ore concentrate in the pelletizing disc is therefore an indispensable part of iron ore processing. Is this method becoming more and more known/popular? And why? The worldwide pig iron production developed in the years 2007 to 2015 with an annual increase of about 3.5%. Iron ore production in 2019 is estimated at ...
اقرأ أكثر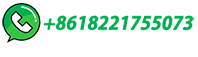
Study of Iron Ore Mixtures Behavior in the Grinding Pelletizing Process
The main unit operations of pelletizing process are grinding, filtering, pressing, pelletizing, and firing. Grinding, the first operation in the process, is a crucial step for the subsequent operations. Three iron ore mixtures with different grindability index (low, medium, and high) were used in order to verify the influence in the operational ...
اقرأ أكثر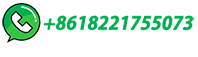
Pelletization
Pelletization refers to the process of converting iron ore fines into agglomerates by mixing them with a binder and water to produce pellets, which are then dried and heated to become hard enough for storage and handling. ... In the underwater pelletising system (Fig. 4.29), the extruder conveys the molten plastic through the start-up valve ...
اقرأ أكثر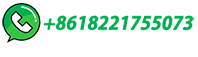
The Iron Pelletizing Process
The iron pelletizing process is often associated with low grade iron ore following a range of liberation techniques to prepare and make suitable for the blast furnace. In summary, pelletizing is achieved by combining the iron ore with water and a …
اقرأ أكثر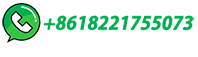
(PDF) IRON ORE PELLETIZING PROCESS
A brief introduction to recent developments in iron ore pelletizing is provided in this chapter, including the world output of fired pellets, pellet production processes, preparation of...
اقرأ أكثر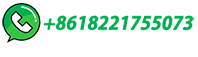
What are the advantages of pelletizing iron ore?
There are several different sub-processes, or process segments, that make up the pelletising process. The iron ore passes through the following primary process steps on its journey from the mine to a finished product: Step 1: The iron ore is crushed, and the waste rock is removed. About 85 % of the particles should be less than 44 μm (in ...
اقرأ أكثر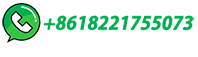
Iron Ore Pelletization
Explore the process and equipment that transforms iron ore fines into uniform pellets, improving transportation and furnace efficiency in steelmaking.
اقرأ أكثر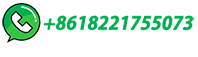
Iron Ore Pellets and Pelletization Process – IspatGuru
Hence the iron ore pelletizing process is a chain of several sub-processes which depends highly upon each other's performance. The addition of binder to the ore serves two main objectives They are (i) to make the ore plastic so that it can nucleate seeds which grows into well formed pellets, and (ii) to hold the pellet together during ...
اقرأ أكثر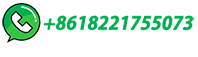
Understanding the Pelletizing Process: Techniques, Benefits, and
Pelletising of crude ore further improves the control of the blast furnace enabling higher efficiency and lower production costs at the same time. ... As noted earlier, the process of iron ore pelletization leads to the production of high-grade pellets rather than un-pelletized ores. The products have a standardization of three properties ...
اقرأ أكثر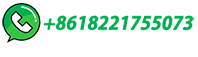
The Iron Pelletizing Process
Explore the iron and steel industry's use of iron ore, focusing on the pelletizing process of low-grade ores. Learn about the various sub-processes, including crushing, grinding, separation, and agglomeration. Understand the market …
اقرأ أكثر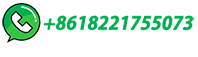
The impact of goethitic ore types across the value chain – Process
Key goethite ore types and properties. Our blog on understanding textural classification systems to improve business outcomes described the different types of goethite present in iron ores. Outlined in the table below is an overview of key goethite properties and the impact these can have on the various stages of the iron ore value chain.
اقرأ أكثر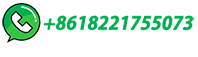
Direct reduction of iron ore pellets by H2 and CO: In-situ
With the aim of reducing CO 2 emissions in basic industries, the sector of iron and steel metallurgy is also faced with the question of how carbon can be replaced in ore reduction. By means of in-situ observation, this study investigates the direct reduction (DR) of individual iron ore pellets under an atmosphere of hydrogen (H 2) and carbon monoxide (CO) and at …
اقرأ أكثر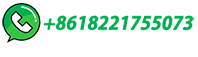
CO 2 -Free Flux for Sustainable Iron Ore Pelletizing
The iron and steel manufacturing sector directly accounts for 7–9% of global CO2 emissions. Raw material preparation, such as iron ore sintering, pelletizing, and cock making, is the major CO2 emitter. As climate change becomes a bigger concern, steel manufacturers need to lower CO2 emissions without hindering efficiency or increasing costs. In recent years, the …
اقرأ أكثر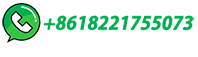
Iron Ore Pelletization: A Critical Review of Processes and
Pelletization involves converting iron ore fines into compact pellets, which are then used in blast furnaces or direct reduction iron processes, contributing to more sustainable and …
اقرأ أكثر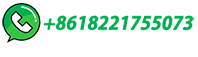
091102 Iron ore
project for a new pelletising plant in Austria. The planned capacity could be around 1.4 Mt of pellet production. The project is still in the early planning phase and an earliest start-up date is ... 2.1 Description of the production process In the iron ore sector, iron ores and concentrates (excluding roasted iron pyrites) are produced. A ...
اقرأ أكثر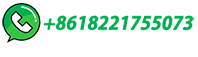
Iron Ore Quality a Potential Headwind to Green Steelmaking
iron ore, it seems likely that the great majority of output will be blast furnace-grade. Vale forecasts that, although there will be a shift towards higher quality iron ore over the rest of this decade, there will be no change in the proportion of seaborne iron ore supply over 66% Fe by 2030, remaining at just 3% of the total as it was in 2020.
اقرأ أكثر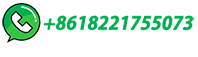
Iron Ore Agglomeration Technologies
Until the 1950s of the last century, the oxidized iron ores that were loaded into the blast furnace had granulometries within 10 and 120 mm. However, the depletion of high-grade iron ore sources has made necessary the utilization of concentration processes with the purpose of enriching the iron ore. Because of these processes, a fine granulometry is produced, and thus …
اقرأ أكثر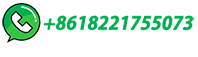
Energy analysis of pelletising in a straight grate induration
process integration tool for an iron ore upgrading process system. Proceeding of the Symposium on Environmental Issues and Waste Management, Bangkok, Thailand, 11-13 Dec 2007 B. Nordgren S, Dahl J, Lindblom B, Wang J. Process integration in an iron ore upgrading process system - analysis of mass and energy flows within a straight grate
اقرأ أكثر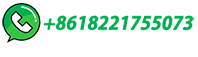
A new insight into iron ore oxidized pellets prepared by steel belt
The steel belt roasting process has the advantages of low cost, small footprint, and high thermal efficiency, making it widely used in the smelting of ferroalloys such as ferrochrome, ferromanganese, and ferroniobium. However, its application in preparing iron ore oxidized pellets has not been sufficiently explored. The optimal thermal process conditions for magnesium …
اقرأ أكثر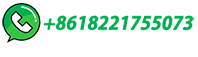
A New Approach of Pelletizing: Use of Low-Grade Ore as a
For carbon neutrality, the use of sinter should be decreased owing to higher CO2 emission in the sintering process of the blast furnace operations. This trend might contribute to the increased use of iron ore pellets with lower CO2 emission in the fabrication process, high reducibility and gas permeability due to higher mechanical strength. The pelletizing process …
اقرأ أكثر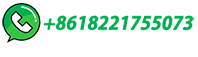
Development of a Novel Grinding Process to Iron Ore
Modern iron ore pelletizing process operations may be divid-ed into two main process sections: feedstock preparation and agglomeration processes. In most plants, the required particle size distribution (PSD) is obtained through the wet ball mill circuit. In the past few years, natural resource awareness be-
اقرأ أكثر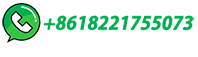
What is Iron Ore Pelletizing? How It Worked? An In …
Iron ore pelletizing is an essential industrial process that transforms powdery iron ore into uniform, robust pellets, serving as a premium feedstock for blast furnaces and direct reduction reactors.
اقرأ أكثر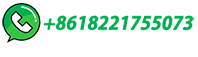
An integrated optimal control model for the drying and preheating
The drying and preheating process plays a crucial role in the induration of iron ore pellets. It is conducted on a closed, moving bed in both the straight grate and grate-kiln processes. The intern...
اقرأ أكثر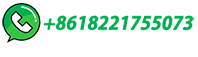
NextGen Pelletizing™
The traveling grate indurating process is responsible for two-thirds of the world's installed pelletizing capacity. Outotec offers the industry's leading induration technology for iron ore pellet processing, which is based on over 60 years of experience and world-class R&D. This process produces pellets with excellent physical
اقرأ أكثر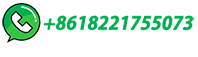
What is Iron Ore Pelletizing? How It Worked? An In-depth Look at …
Iron ore pelletizing is an essential industrial process that transforms powdery iron ore into uniform, robust pellets, serving as a premium feedstock for blast furnaces and direct reduction reactors. This process has witnessed significant advancements since its inception, primarily driven by the escalating requirements of the steel industry, which demands higher …
اقرأ أكثر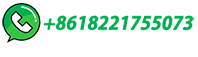
CFD analysis of an induration cooler on an iron ore grate-kiln
During the re-configuration of their grate-kiln induration system for the firing of iron ore pellets at the Whyalla Steelworks, caused by a change from an earthy hematite to a magnetite ore with considerably less flux, OneSteel commissioned a detailed thermal flow analysis of the design options on the existing cooler in support of the process change.
اقرأ أكثر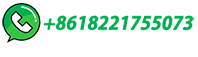