Process optimization of a chrome ore gravity concentration plant …
In a research article on chemical beneficiation with the subsequent gravitational beneficiation of chrome-containing slurry tailings of Donskoy Ore-Mining and Beneficiation Plant (DOMBP), which ...
اقرأ أكثر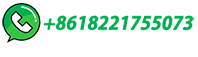
Beneficiation of Low-Grade Hematite Iron Ore Fines by …
However, the slimes with 6–8% Al 2 O 3 that accounts 20–25% of total iron ore mined is dumped in tailing ponds as slimes. 15 The available beneficiation methods for treatment of these slimes by gravity separation, magnetic separation, froth flotation, selective flocculation, etc., have limitations due to various physical properties, ore ...
اقرأ أكثر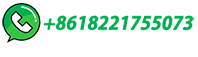
A Study on High-Grade Iron ore Beneficiation to Reduce
Iron ore pellets are largely characterized by inherent physical and chemical properties of the ore. Alumina and silica play important roles in determining the productivity of a Blast Furnace. On average, one percent increase in iron content improves productivity by 2% and reduces coke consumption by 1%. Therefore higher iron ore feed content to blast furnace is …
اقرأ أكثر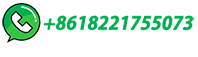
Global Capability
for magnetic separation of fine minerals for the extraction of iron ores with low magnetic susceptibility. They afford the most efficient separation of minerals in slurry form, when drying of the material is undesirable or uneconomical. Features and Benefits Beneficiation of iron ore fines from 10 microns to 1.5mm
اقرأ أكثر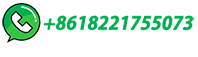
Beneficiation Plants and Pelletizing Plants for Utilizing Low Grade
Various Types Of Iron Ore Beneficiation Processes
One popular beneficiation method is mechanical crushing and screening, which involves breaking down large chunks of ore into smaller pieces and separating them based on size. This method is particularly effective for …
اقرأ أكثر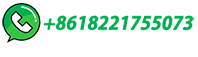
Potential Applications for Dry Beneficiation of Iron Ore Fines …
ST Equipment & Technology LLC (STET) tribo-electrostatic belt separator technology allows for the beneficiation of fine mineral powders with an entirely dry technology at a high throughput. The STET separator is well suited for separation of very fine (<1µm) to moderately coarse (500µm) particles, in contrast to other electrostatic separation processes that are typically limited to …
اقرأ أكثر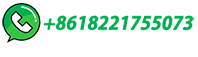
Characteristics Of Iron Ore Beneficiation Technology
Depending on the composition of materials in the drum a low or high-intensity magnetic force can be used to separate the particles. Again, wastewater is created and water treatment becomes necessary. Dry Iron Ore Beneficiation Technology. Within dry iron ore separation, there are a few techniques that can be used. They include gravity ...
اقرأ أكثر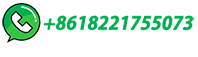
Dry beneficiation of iron ore
Falling prices for iron ore with lower quality than 60 % Fe have led increasingly to the design of iron ore beneficiation lines. General problems of water scarcity and risks with tailings dams have led to the focus shifting to dry beneficiation …
اقرأ أكثر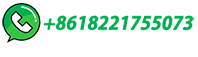
Mineral Processing Plant & Beneficiation Solutions
Ore processing is the process of separating valuable minerals from its ores by ore beneficiation equipment. Mineral dressing plant is recovers or extracts minerals through a range of ore processing solutions, including washing, crushing, grinding, gravity concentration, flotation & magnetic separation, electrostatic separation and more. JXSC provide full mining process …
اقرأ أكثر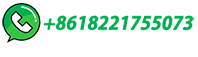
SEPARATION EXPERTISE FOR YOUR SUCCESS IN THE …
Whether it's thickening or filtration, concentrate or tailings, the list of success stories goes on and on. With thousands ... with leading iron ore separation technologies. 5 countries 40 solid/liquid separation specialists 2,000 Your separation ... In designing a new beneficiation plant or extension and modernization, our engineers draw on ...
اقرأ أكثر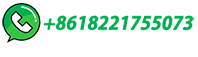
Beneficiation of Magnetically Separated Iron-Containing Ore Waste
It is shown that iron-containing ore tailings beneficiation is optimal without any additional grinding. Relative distribution N(x) of particles by size x in tailings. Cascade separator layout.
اقرأ أكثر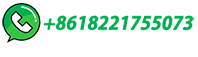
Beneficiation of Low-Grade Hematite Iron Ore Fines by …
Present investigation includes the magnetizing roasting of low-grade iron ore fines followed by grinding and beneficiation using magnetic separation. The hematite iron ore used in the investigation contains 53.17% T Fe, 10.7% SiO2, and 4.5% Al2O3. Powdered bituminous coal of 210 μm size with an ash content of 12.5% and fixed carbon of 54.25% was used as …
اقرأ أكثر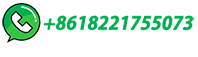
Treatment of iron ore beneficiation plant process water by
In the present study, process water collected from iron ore beneficiation plant was treated by electrocoagulation (EC) to obtain treated water suitable for reuse or safe for …
اقرأ أكثر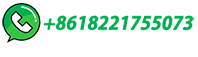
The Processing of Copper Ore Beneficiation
In the development and utilization of copper resources, the grading operation of the copper ore beneficiation plant is also an important production link in the separation of copper ore. As the difficulty of copper mining and sorting increases, the requirements for screening efficiency and classification efficiency are getting higher and higher. Therefore, efficient screening and […]
اقرأ أكثر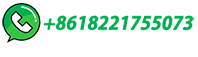
Treatment of iron ore beneficiation plant process water by
Abstract Process water collected from the iron ore beneficiation plant was treated by electrocoag- ulation (EC) process to make it suitable for reuse or safe for discharge. Experimental studies were
اقرأ أكثر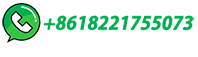
Electrostatic Separation in Iron Ore Processing: A Revolutionary
Following this, the ore is subjected to various iron ore beneficiation processes such as gravity separation, magnetic separation, and flotation to remove impurities and increase iron content. Magnetic separation is particularly effective in separating iron ore from gangue minerals due to the magnetic properties of iron.
اقرأ أكثر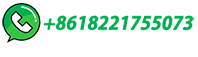
Iron Ore Tailing Beneficiation
Iron ore tailing/slime (-150 μm) is produced after scrubbing and wet screening of a low-grade iron ore. Tailing beneficiation of iron ore has been addressed either by flotation or wet high intensity high gradient separation. The present study aims to recover iron values from discarded slime containing assay ~56% Fe, ~6.5% SiO 2, and ~7.0% Al 2 O 3
اقرأ أكثر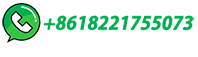
Characteristics Of Iron Ore Beneficiation Technology
Separation technology equipment allows fine low-grade iron ore to be processed into much higher-grade iron ore. The different types of separation technology equipment fall into two main categories—wet and dry iron ore …
اقرأ أكثر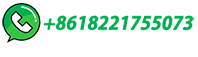
Iron Ore Beneficiation Technology By Electrostatic Separation
Almost of mined iron ore is used in steel production, making it essential for everything from staples to buildings. Beneficiation is the term for reducing the size of valuable iron ore particles and separating them from the gange (unusable minerals), which are then discarded. There are several different methods of wet and dry separation.
اقرأ أكثر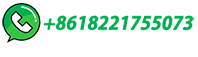
(PDF) Beneficiation and flowsheet development of a low grade iron ore
In the present study a detailed characterization followed by beneficiation of low grade iron ore was studied. The Run of Mine (R.O.M) sample assayed 21.91 % Fe, which is very low grade in nature.
اقرأ أكثر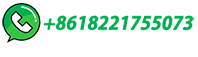
Techno Analysis of Solid-Liquid Separation of Iron Ore …
The project mainly deals with dewatering efficiency of Iron Ore Concentrate using different types of filters in the filtration process carried out at Iron Ore Pelletization Plant in India.
اقرأ أكثر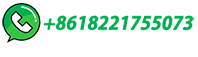
Haiwang Overseas Project
The iron processing plant trust Made in China and Haiwang is its first choice for separation equipment. In the technical exchange with Haiwang experts in the early stage, …
اقرأ أكثر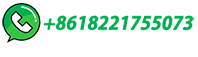
Wet High Intensity Magnetic Separation
The capital cost, which is also high, would be reduced if roasted ore were processed in an existing magnetic separation plant. However, processing of reduction-roasted ore in a conventional taconite plant would require some modifications, because artificial magnetite has a higher remanence and coercivity than natural magnetite.
اقرأ أكثر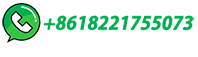
(PDF) Lean Iron Ore: Beneficiation Prospects
Some of the major beneficiation techniques include froth flotation process, selective flocculation, enhanced gravity separation, multi-gravity separation, etc. Various studies carried out on ...
اقرأ أكثر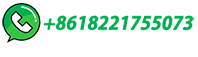
Iron Ore Processing: From Extraction to Manufacturing
The final stage in iron ore processing is ironmaking, where the iron ore is transformed into molten iron through a process called reduction. The most common method of ironmaking is the blast furnace route. In a blast furnace, iron ore, coke (carbon), and fluxes (limestone or dolomite) are loaded into the furnace from the top.
اقرأ أكثر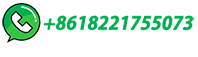
Solutions
At present, Haiwang Technology has a professional mineral classification, coal preparation consulting team and standard sale and consulting process, which can provide customers with consulting services for the whole beneficiation classification, coal preparation machine and EPC project of each life cycle phases to help the customers to confirm the next step of development …
اقرأ أكثر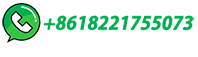
A Beneficiation Study on a Low Grade Iron Ore by Gravity and …
In this paper, a sample from Tange-zagh iron mine was characterized by gravity and magnetic separation methods. The mineralogical studies showed that hematite and goethite are the main iron-bearing minerals with insignificant amounts of FeO. The results indicated that spiral separation yields higher separation efficiency than others. The combination of spiral and multi …
اقرأ أكثر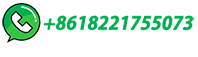
Dry Beneficiation of Iron Ore Fines Using Tribo-Electric Belt …
Iron ore extraction is mainly performed through open pit mining operations, resulting in significant tailings generation [2]. The iron ore production system usually involves three stages: mining, processing and pelletizing activities. Of these, processing ensures that an adequate iron grade and chemistry is achieved prior to the pelletizing stage.
اقرأ أكثر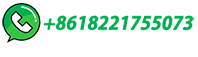
Beneficiation of Ultrafine Iron Ore Using Tribo-electrostatic …
Table 1. Mineralogy of "ultrafines" iron ore and "air-classified" iron ore samples Sample Hematite Goethite Quartz Kaolinite Ultrafines Iron Ore 50.8% 17.9% 12.5% 18.5% Air-classified Iron Ore 50.6% 3.4% 40.9% 3.5% The majority of both samples are composed of hematite and no significant proportion of magnetite is present in
اقرأ أكثر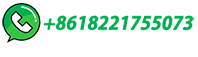
Coal beneficiation: theory and practice
Coke is used primarily as a fuel and a reducing agent in a blast furnace during the smelting of iron ore into iron before it is converted into steel. ... Rain water treatment. ... Typical results in a coal beneficiation plant using spirals to treat fine coal indicated very little deterioration in performance with the under-slimed and deslimed ...
اقرأ أكثر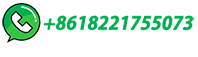