Schematic overview of the Grate-Kiln process (to the left) and a
Download scientific diagram | Schematic overview of the Grate-Kiln process (to the left) and a grate-link before service (to the right). A is the grate-chain and B is the rotary kiln. C, D, E and ...
اقرأ أكثر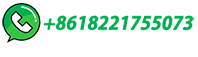
Grate-Car process design, Pot-Grate and CAF testing
Svedala has a ported kiln process, designed specifically for the direct reduction of pelletized or natural lump iron ores. The process is called ACCAR. This ported kiln technology has been coupled with Svedala`s Grate-Kiln System, for iron ore pelletizing, into the Grate-Car System for the reduction of fine grained ore concentrates through the steps of agglomeration, …
اقرأ أكثر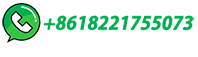
Grate Kiln | PDF | Iron Ore | Industrial Processes
The document discusses the grate-kiln process for producing iron ore pellets. It was originally developed by Allis Chalmers in 1960 as an improvement over the straight grate process. The grate-kiln process uses three connected machines - a traveling grate for drying and preheating pellets, a rotary kiln for induration, and an annular cooler. This allows independent control of …
اقرأ أكثر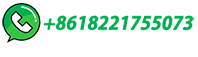
(PDF) IRON ORE PELLETIZING PROCESS
Sc hematic diagra m of the grate-rotary kiln induration process / grate-kiln pelletizing process (also known as the rotary-kiln proce ss) (Mourão et al., 2013). 1.2.
اقرأ أكثر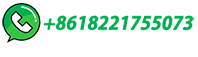
Iron Ore Pelletizing Grate-Kiln System Brochure
The slope and rotation of the kiln move the material through it. Kiln speed is variable to vary pellet retention time. The kiln is a single chamber with an open feed end connected by housing to the grates preheat furnace Through this …
اقرأ أكثر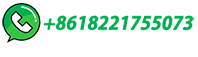
Iron Ore Pellatisation Application in Steel Industry – …
Process experts did a thorough analysis & found the best ESP design for the 'Grate Kiln' process based on performance data of the 'straight grate' Pellatisation Process. SUSTAINABLE SOLUTIONS IN ENERGY AND ENVIRONMENT …
اقرأ أكثر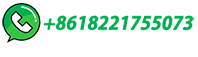
XI. AGGLOMERATION
The process of 'agglomeration' can be classified mainly into the following groups, namely, Briquetting, Nodulizing (rotary kiln sintering), Vacuum extrusion, Sintering and Pelletizing. Briquetting : This is a very simple process, in which fine …
اقرأ أكثر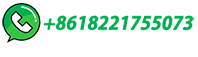
Iron Ore Agglomeration Technologies
There are several agglomeration processes including: briquetting, extrusion, nodulization, pelletizing and sintering, although pelletizing and sintering are the most widely used, and especially sintering process (70% blast furnace …
اقرأ أكثر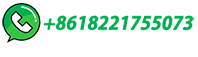
Pelletizing Process.pdf
Schematic diagram of the grate-rotary kiln induration process/ grate-kiln pelletizing process (also known as the rotary-kiln process) (Mourão et al ... Elsevier Sequoia S.A.: Lausanne; 1980 Ball D. Agglomeration of Iron Ores. New York: American Elsevier Pub. Co.; 1973 Biswas, A.K. Principles of Blast Furnace Ironmaking; Cootha Publishing House ...
اقرأ أكثر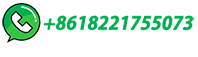
Induration of Green Pellets | 14 | Agglomeration of Iron Ores
These functions are dependent on the type of ore concentrate. The characteristic features of a grate-kiln-cooler system, scheme of heat recuperation, and design parameters are mentioned. Its merits/demerits with respect to techno-economic parameters, product quality, and heat recuperation are compared with a straight-grate system.
اقرأ أكثر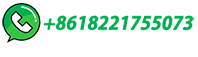
The effect of co-firing coal and woody biomass upon the slagging
Woody biomass is being considered a potential co-firing fuel to reduce coal consumption in iron-ore pelletizing rotary kilns.An important consideration is the slagging inside the kiln caused by ash deposition that can lead to process disturbances or shutdowns. In terms of ash chemistry, co-firing woody biomass implies the addition of mainly Ca and K to the Si- and …
اقرأ أكثر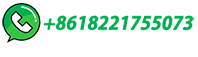
Iron Ore Agglomeration Technologies
Briquetting is the simplest agglomeration process. Fine grained iron ore is pressed into two pockets with the addition of water or some other binder agent (molasses, starch, or tar pitch) …
اقرأ أكثر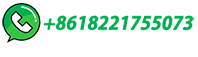
Davi Silva Braga
Researcher at COREM - Agglomeration and thermal processes · Process Engineer and Innovation Researcher, with 17 years of combined experience in steel producer company and innovation research center, with emphasis on iron ore pelletizing, project management, continuous improvement, quality control, process modeling, production control and planning. …
اقرأ أكثر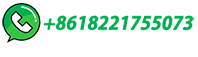
Coal fueled ported kiln direct reduction process in Norway
The process is called ACCAR. This ported kiln technology has been coupled with Svedala`s Grate-Kiln System, for iron ore pelletizing, into the Grate-Car System for the reduction of fine grained ore concentrates through the steps of agglomeration, induration and reduction in a single production line.
اقرأ أكثر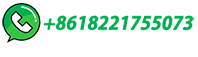
Schematic of the straight grate pelletizing process.
However, the grate-kiln system consists of three separate process units connected in series: a traveling grate for drying and preheating green balls, a rotary kiln for indurating preheated pellets ...
اقرأ أكثر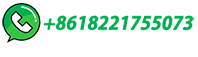
Expert System for Control Guidance of Grate-Kiln Pellet …
ment make grate-kiln process hard for parameter detection and difficult to control. The accuracy and nor-malization of grate-kiln process control need to be improved. Therefore, an expert system providing real ... grate, go through grate, kiln and cooler successively for dry-ing, preheating, roasting and cooling, and finally discharged
اقرأ أكثر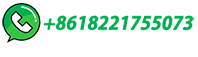
(PDF) Advances in Iron Ore Pelletizing Binders
However, the final pellet properties are more uniform, and fines generation during transport for final use is therefore expected to be lower for pellets produced in the grate-kiln process. The worldwide pelletizing capacity is divided into 60% for …
اقرأ أكثر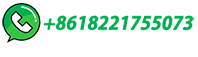
SINTERING AND PELLETISATION OF INDIAN IRON ORES
Travelling grate process. Process adopts three equipment viz. grate, rotary kiln and annular cooler. The pellet bed on the grate is only 150 -200 mm deep, and no protective layer is …
اقرأ أكثر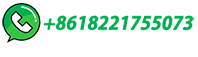
The study of granular agglomeration mechanism
Wet particle agglomeration is dependent on liquid forces (e.g., static capillary forces and dynamic viscosity forces) between particles [4]. The liquid content played an important role in the wet agglomeration process. Benali [5] observed the granule-surfaces produced by using different liquid to solid ratios. From SEM images four types of ...
اقرأ أكثر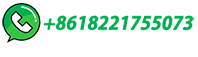
Agglomeration of Iron Ores
Agglomeration of iron ores is the iron ore pretreatment process in which the powdery iron ore that cannot be directly fed into a blast furnace experiences high-temperature solidification by sintering process and pelletizing process or low-temperature solidification by pelletizing process and briquetting process to generate the rich ore material that meets the …
اقرأ أكثر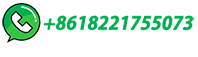
Pelletization
Pelletization is the process of transforming iron ore fines into spherical pellets through agglomeration and induration. These pellets are then used as feed to a blast furnace or direct …
اقرأ أكثر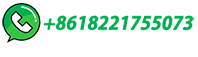
A Comparison of Pellet Quality from Straight-grate and Grate-kiln
The grate-kiln process is an industrial applied process to produce pellet production in China [4] [5] [6]. With the expense of high-quality iron ore resources, many researchers focus on utilizing ...
اقرأ أكثر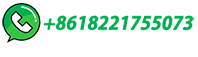
Iron Ore Pelletizing Process: An Overview
The worldwide pelletizing capacity is divided into 60% for the straight grate process and 40% for the grate-kiln. Both systems are used to produce quality blast furnace and direct reduction
اقرأ أكثر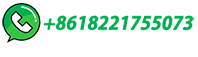
Pelletization
Pelletization is the process of transforming iron ore fines into spherical pellets through agglomeration and induration. These pellets are then used as feed to a blast furnace or direct reduction systems to produce iron. ... offers both straight grate and grate-kiln technologies for any required pelletizing applications. Environment ...
اقرأ أكثر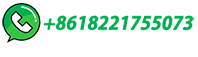
NOx Emission Reduction by Advanced Reburning in Grate …
China is mainly produced by a grate-rotary kiln process, and its output accounts for nearly 60% of the output of the total pellet [11,12]. Many studies have shown that NO x formation in rotary ...
اقرأ أكثر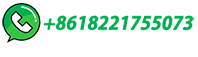
Agglomeration Equipment
Process Description. In the pelletizing process, fine ore concentrate is mixed with a binder (bentonite) and formed into green balls in the balling drums. These green balls are then fed into traveling grate kiln furnaces where they are dried and heated and then pass into a rotary kiln for final heating to a point just below fusion (2400°F).
اقرأ أكثر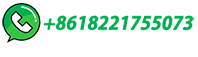
Novel method for temperature prediction in rotary kiln process through
Noteworthy contributions also include Zhikai Liang's exploration of the heat transfer rate's correlation with pellet diameter during pellet reduction within a rotary kiln through CFD simulations [21]. Additionally, Peter J. Witt et al. [22] employed CFD to model a rotary kiln for the prediction of key process parameters like bed temperature. In ...
اقرأ أكثر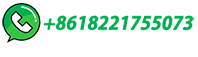
Introduction to Iron ore Pellets and Pelletizing processes
Fig 2 Flowsheet of straight travelling grate process. Grate kiln process. The grate kiln process was developed by former Allis Chalmer and the first plant on this technology was constructed in 1960. In the grate kiln process (Fig 3) the traveling grate is used to dry and preheat the pellets.
اقرأ أكثر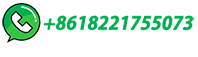
Pelletizing Process
Agglomeration Equipment
Process Description. In the pelletizing process, fine ore concentrate is mixed with a binder (bentonite) and formed into green balls in the balling drums. These …
اقرأ أكثر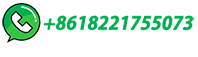
Pelletization Solutions
Pelletizing is the process of transforming iron ore fines into spherical pellets through agglomeration and induration to be used as feed to a blast furnace or direct reduction systems …
اقرأ أكثر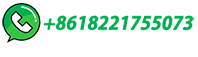