Breakthrough in Clinker Grinding
Raw materials crushing and grinding seeks to reduce materials from roughly one meter cubes of blasted stone to a size where at least 80 percent of the raw material is less than 75 microns. Finish grinding of clinker and other cement ingredients reduces 25 mm clinker balls to particle sizes optimally ranging from 3 to 30 microns.
اقرأ أكثر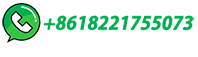
Homogenization of Cement Raw Meal
Cement raw meal is the raw material for producing cement clinker, which is prepared in a certain proportion after crushing and grinding. After being calcined in a rotary kiln, the raw meal is turned into the clinker. The composition and …
اقرأ أكثر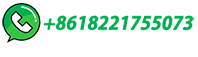
Manufacturing process flow 1. Quarrying and Crushing
8. Clinker Storage A clinker storage silo with capacity of 15000tons and an open yard with capacity of 20000tons are built up in the plant. Under the clinker silo, the rod gate and the motorized discharging gate are installed. The clinker discharged by these equipment is fed to different belt conveyors
اقرأ أكثر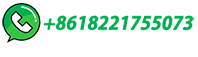
sbm/sbm crushing of clinker.md at main · jgw2023/sbm
Contribute to jgw2023/sbm development by creating an account on GitHub.
اقرأ أكثر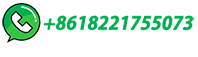
3000tpd cement production line-China Cement …
The Pengfei EPC cement production line project includes services such as process design, equipment supply (including mechanical and electrical parts), civil engineering, installation and commissioning, trial operation, reaching …
اقرأ أكثر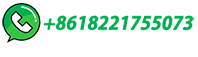
Cement Production Line – ACAC info
The focus of this article-cement production line refers to the production line which composed of a series of devices. It is mainly constituted by crushing and pre-homogenizing, …
اقرأ أكثر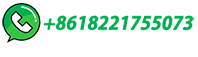
Cement Manufacturing Process
In brief, cement production has the following 7 steps: crushing and pre-homogenization, raw meal preparation, homogenization of raw meal, preheating decomposition, firing of cement clinker, cement grinding and cement package. 1. crushing and pre-homogenization (1)Crushing.
اقرأ أكثر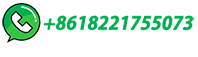
Cement
There are four stages in the manufacture of portland cement: (1) crushing and grinding the raw materials, (2) blending the materials in the correct proportions, (3) burning the prepared mix in a kiln, and (4) grinding the burned product, known as " clinker," together with some 5 percent of gypsum (to control the time of set of the cement). The three processes of …
اقرأ أكثر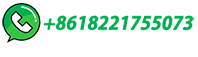
Emission reduction through process integration and …
by crushing and milling, preheating, pre-calcining, kiln r - ing, clinker cooling, clinker storage, cement milling with additives and nally, storage and packing of the cement (Gao et al. 2016). Figure 1 shows the schematic of the cement manufacturing process. The chief raw material for …
اقرأ أكثر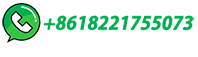
Cement production line
This production line mainly consists of the process of crushing and prehomogenization, raw materials homogenizing, preheating decomposition, cement clinker firing, cement grinding & packaging. The main equipments used in this whole production line include the vibrating feeder, jaw crusher, impact crusher, cement ball mill lifer, preheating ...
اقرأ أكثر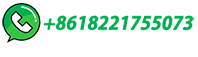
cement clinker vertical mill | Mining & Quarry Plant
The cement clinker equipment is popular in the traded of mining, building materials, chemical engineering and metallurgy for size reduction, dispersion, or specialized needs, powder generation and processing for industrial process. Following are the crushing processing and raw material advance homogenization for cement clinker.
اقرأ أكثر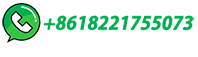
Grinding and homogenization
The grinding process takes place in a raw mill to reduce the particle size of the components to a typical value of 10-15 % residue on a 90 um sieve. The output of the grinding process – called …
اقرأ أكثر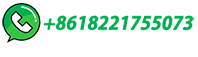
Evaluation and Analysis of Cement Raw Meal …
clinker quality. The principal techniques employed in the homogenization of raw meals include [6,7]: (1) Gravity Homogenizing Silos: The utilization of gravity for layered stacking and mix-ing during discharge allows for the achievement of homogenization. The advantages of this system include its simple structure and ease of operation. However ...
اقرأ أكثر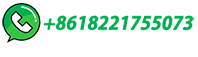
Dry Process Of Cement ManufacturingDry Process Of …
Dry process cement kiln is a kind of rotary kiln which is mainly used in calcining cement clinker. The cement clinker made by the dry process has better quality and stability. It can bring more economical and social benefits in production. ... Crushing and pre-homogenizing. Raw materials preparation. Raw material homogenization. Preheat ...
اقرأ أكثر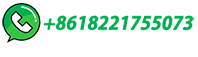
Cement Production Line|Portland Cement …
The cement rotary kiln works as the principal equipment to roast cement clinker in the industries of cement production, metallurgy and chemical engineering. Cement Production Line Production process 1.Crushing and pre …
اقرأ أكثر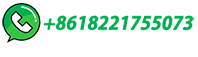
Selected references | PSP Engineering
Clinker storage. Main equipment: KTS 800 chain conveyor, silo Ø 28 x 43.5 m, de-dusting equipment. ... New primary crushing plant 370 t/h and pre-homogenizing storage with 20 000 t capacity. Main equipment: OKD 2000x2000 impact-hammer crusher, belt conveyor, KTM 360 vertical mill, circular pre-homogenizing storage, stacker, scraper ...
اقرأ أكثر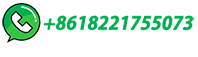
CN112919833B
The invention discloses a pre-crushing and high-protection cement clinker processing integrated device which comprises a storage box, a high-pressure jet machine and a control box, wherein a feed inlet is penetrated through the upper side of the storage box, a pre-crushing assembly is fixed on the lower side of the storage box, a first cleaning assembly is fixed on an upper …
اقرأ أكثر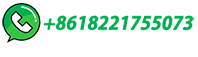
New Type Dry Process Cement Production Line
Crushing and Pre-homogenizing: Most of the raw materials, like limestone, clay, iron ores, and coal, should be crushed before their pre-homogenization. ... The raw meal homogenization is a key factor for stable clinker calcination. 4. Preheating and Decomposing: The preheater is used to preheat as well as decompose raw meal. So the length of ...
اقرأ أكثر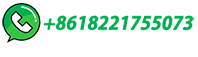
Cement Production Line--Henan Engineering
Crushing and Pre-homogenizing:Most of the raw materials, like limestone, clay, iron ores, and coal, should be crushed before their pre-homogenization. Limestone is the primary material in this line, and due to its large particle size and high hardness, its good crushing plays an important role in the whole line. ... Clinker Calcining:After its ...
اقرأ أكثر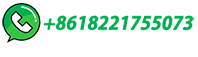
Name already in use
sbm sintering clinker crushingiron ore size required for sintering Mineral Processing, After mining,its particle size is larger and its hardness is stronger,so crushing The next p
اقرأ أكثر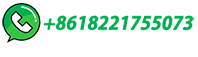
Grinding and homogenization
The grinding process takes place in a raw mill to reduce the particle size of the components to a typical value of 10-15 % residue on a 90 um sieve. The output of the grinding process – called 'raw meal' – is transferred to a homogenization silo before the clinker manufacturing process.
اقرأ أكثر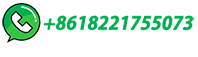
CEMENT MANUFACTURING PROCESS
produce the clinker. To reach the necessary temperatures for processing the raw materials and for the production of clinker, the kiln has a main flame that burns at 2,000ºC. Clinker process: cooler At the exit of the kiln, the clinker is introduced into the cooler, which injects cold air from the outside to reduce its temperature from 1,400ºC
اقرأ أكثر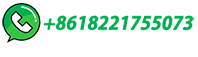
China Leading Construction of Portland Cement Clinker Grinding
China Leading Construction of Portland Cement Clinker Grinding Production Plant, Find Details and Price about Cement Grinding Unit Clinker Grinding Unit from China Leading Construction of Portland Cement Clinker Grinding Production Plant - Jiangsu Pengfei Group Co., Ltd.
اقرأ أكثر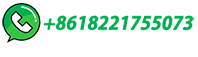
Cement Manufacturing—Technology, Practice, and Development
Clinker Manufacturing Process. Cement grinding. ... Fossil fuels preparation consists of crushing, drying, grinding, and homogenizing which takes place at the plant site. Specific installations are required for fuel preparation such as grinding mills and silos for solid fuels and tanks for liquid fuels. ... takes place is a rotary kiln with or ...
اقرأ أكثر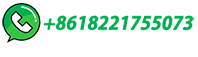
Energy Efficiency Improvement Opportunities for the Cement …
various kiln types used in China: raw materials (and fuel) preparation; clinker making (applicable to all kilns, rotary kilns only, vertical shaft kilns only); and finish grinding; as well as plant wide measures and product and feedstock changes that will reduce energy consumption for …
اقرأ أكثر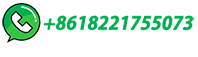
cement clinker plant cost | Mining & Quarry Plant
The cement clinker equipment is popular in the traded of mining, building materials, chemical engineering and metallurgy for size reduction, dispersion, or specialized needs, powder generation and processing for industrial process. Following are the crushing processing and raw material advance homogenization for cement clinker.
اقرأ أكثر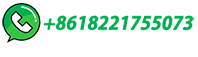
Manufacturing process flow 1. Quarrying and Crushing
8. Clinker Storage A clinker storage silo with capacity of 15000tons and an open yard with capacity of 20000tons are built up in the plant. Under the clinker silo, the rod gate and the …
اقرأ أكثر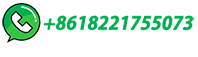
Portland Cement Manufacturing Plant Machinery and Clinker Crushing
Portland Cement Manufacturing Plant Machinery and Clinker Crushing Production Line, Find Details and Price about Cement Clinker Production Line Dry Process Cement Plant from Portland Cement Manufacturing Plant Machinery and Clinker Crushing Production Line - Jiangsu Pengfei Group Co., Ltd.
اقرأ أكثر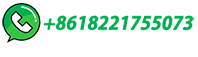
Cement Manufacturing Process
In brief, cement production has the following 7 steps: crushing and pre-homogenization, raw meal preparation, homogenization of raw meal, preheating …
اقرأ أكثر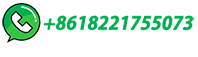
How to processing cement clinker | Mining & Quarry Plant
The cement clinker equipment is popular in the traded of mining, building materials, chemical engineering and metallurgy for size reduction, dispersion, or specialized needs, powder generation and processing for industrial process. ... Raw material pre-homogenizing technology is in the retention of the raw materials, to take the process to use ...
اقرأ أكثر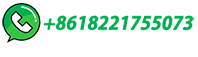