Kinetics of iron oxide reduction using CO: Experiments and …
Reduction of iron ore is central to iron and steel making process. The reaction kinetics are generally studied using classical models that are based on the mechanism of interface control, nucleation control, or diffusion control. This paper presents a different approach in which physical governing equations for the solid phase are solved ...
اقرأ أكثر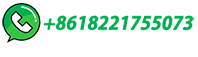
Reduction of Iron Oxides with Hydrogen—A Review
Reduction with hydrogen, in the best case produced via renewable energies, is a future-minded alternative to commonly used fossil fuels. Direct reduction …
اقرأ أكثر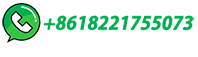
Reduction of Iron Oxides with Hydrogen—A Review
Reduction with hydrogen, in the best case produced via renewable energies, is a future-minded alternative to commonly used fossil fuels. Direct reduction processes, which reduce iron ore to metallic iron without any liquid phase, especially have the possibility to use a high percentage of hydrogen in the reducing gas mixture.
اقرأ أكثر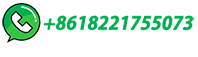
Direct-Reduced Iron
Direct reduction (DR) is defined as any process in which metallic iron is produced by the reduction of iron ore at temperatures below the iron melting point. The product of a DR process is called …
اقرأ أكثر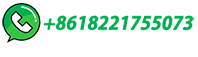
Iron ore reduction using sawdust: Experimental analysis and …
With the 80:20 mass ratio, the iron ore reduction was substantially advanced with the XRD analysis showing presence of predominantly wustite (FeO) and small amounts of metallic iron (Fe) (Fig. 3). With further increase of the biomass weight proportion to 30%, almost complete reduction of the iron ore was achieved at 1200 °C. The XRD analysis ...
اقرأ أكثر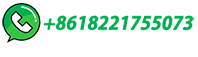
Sustainable iron recovery from iron ore tailings using hydrogen …
The recovery rate of iron initially decreased and then increased. Specifically, the recovery rate of iron declined from 95.26% to 91.86%. The results suggest that with the increase in total gas volume, the reduction time of iron ore decreased, the phase conversion effect of hydrogen-based ore deteriorated, and the sorting index decreased.
اقرأ أكثر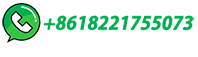
Iron Ore Reduction by Hydrogen Using a Laboratory Scale
The reduction kinetics of hematite iron ore fines to metallic iron by hydrogen using a laboratory fluidized bed reactor were investigated in a temperature range between 873 K and 1073 K, by measuring the weight change of the sample portion during reduction. The fluidization conditions were checked regarding plausibility within the Grace diagram and the measured …
اقرأ أكثر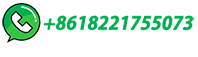
Reducing Iron Oxide with Ammonia: A Sustainable Path to Green …
Here, we introduce a sustainable iron-making process by directly deploying ammonia in iron ore reduction (Figure 1b). An important advantage of this approach is that the green ammonia does not need to be cracked into hydrogen and nitrogen using a precious metal catalyst, e.g., ruthenium, [ 20 ] prior to the reduction process.
اقرأ أكثر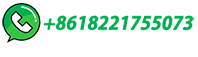
Direct reduction of iron ore pellets by H2 and CO: In-situ
With the aim of reducing CO 2 emissions in basic industries, the sector of iron and steel metallurgy is also faced with the question of how carbon can be replaced in ore reduction. By means of in-situ observation, this study investigates the direct reduction (DR) of individual iron ore pellets under an atmosphere of hydrogen (H 2) and carbon monoxide (CO) and at …
اقرأ أكثر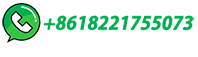
Influence of microstructure and atomic-scale chemistry on the …
However, the iron ore reduction exhibits a relatively stable reduction rate within the reduction degree range of ~0.33 to ~0.7 (Fig. 1 b). This observation indicates that gaseous diffusion is not the key factor controlling the wüstite reduction rate but rather the internal diffusion of oxygen through the solid iron.
اقرأ أكثر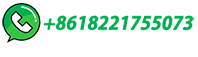
Theoretical Aspects of Direct Reduction Process
In iron ore reduction all of the products (Fe3O4, FeO, and Fe) come under consideration as possible catalysts. Out of these particularly active is solid Fe. The process of reduction of iron ore in CO/CO2 mixtures containing H2 is, hence, to be understood, when metallic Fe is present, as a reaction sequence.
اقرأ أكثر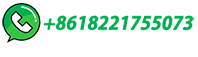
From Ore to Iron with Smelting and Direct Iron …
Source: World Steel Association (worldsteel) The first step in the production of steel or cast iron alloys is the reduction of iron ore—which …
اقرأ أكثر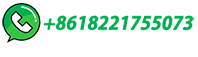
A REVIEW OF IRONMAKING BY DIRECT REDUCTION …
The proposed iron ore reduction process therefore would be a potential to reduce iron directly using biomass with high efficiency and real environmental benefits. View. Show abstract.
اقرأ أكثر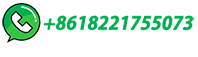
The Iron Ore Challenge for Direct Reduction On Road …
It is abundantly clear that the challenge is by now well recognized along the iron ore and steel value chain, with a variety of co-operation agreements in place between the major iron ore producers and their customers to explore solutions …
اقرأ أكثر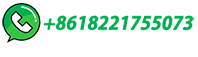
DRI production | International Iron Metallics Association
Direct reduction of iron is the removal of oxygen from iron ore or other iron bearing materials in the solid state, i.e. without melting, as in the blast furnace. The reducing agents are carbon monoxide and hydrogen, coming from …
اقرأ أكثر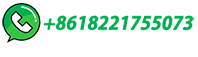
Chemical and electrochemical pathways to low-carbon iron and …
The majority of emissions arise from the iron ore reduction step, which is usually performed in a carbothermic blast furnace (BF) utilizing coal and natural gas (Fig. 1) 6.
اقرأ أكثر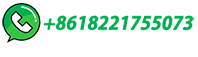
Iron ore reduction by methane partial oxidation in a porous media
Iron ore reduction by the gaseous products of partial combustion of methane in a porous media was experimentally and numerically studied. To achieve this purpose, a porous media burner capable of generating an upstream propagation wave for the rich combustion of natural gas-air mixture was designed and built. Two experimental tests were ...
اقرأ أكثر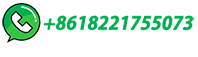
Relationship of particle size, reaction and sticking behavior of iron
During fluidized bed direct reduction, iron ore particles become sticky as metallic iron is formed on the surface, which may cause defluidization of the particles [11].Once defluidization occurs, the reduction process has to be terminated, bringing out a great economic loss [12].The deadly defluidization seriously restricts the development of fluidized bed direct …
اقرأ أكثر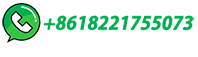
Direct Reduced Iron (DRI)
Direct Reduced Iron (DRI) is the product of the direct reduction of iron ore in the solid state by carbon monoxide and hydrogen derived from natural gas or coal. See more information about the production of DRI.
اقرأ أكثر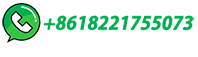
The Optical Spectra of Hydrogen Plasma Smelting Reduction of Iron Ore
In comparison to shaft furnace solid-state direct reduction of iron ore with gaseous hydrogen, they found out that the HPSR with 10% H 2 partial pressure yielded comparable reduction rates. Due to the complex behavior of plasmas, one of the most important perspectives for the future advancement of HPSR is to create a profound process control.
اقرأ أكثر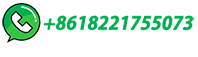
Direct Reduced Iron Fines: Guide for Shipping, Handling and …
There are several processes for direct reduction of iron ore, principally gas-based shaft furnaces (Midrex and ENERGIRON processes) accounting for 76% and coal based rotary kiln furnaces …
اقرأ أكثر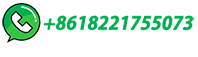
(PDF) i) Direct Reduced Iron: Production
Processes that produce iron by reduction of iron ore (in solid state) below the melting point are generally classified as DR processes. Based on the types of reductant used, DR processes can be ...
اقرأ أكثر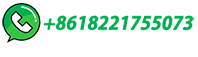
Direct reduction of iron ore pellets by H2-CO mixture: An in-situ
The iron and steel metallurgy industry faces the question of how to replace carbon in iron ore reduction to reduce CO 2 emission in basic industries and achieve the expectation of "double carbon". This study investigates the reduction swelling of individual iron ore pellet under mixed H 2-CO atmospheres and at temperatures of 800–1000 ℃ by in-situ observation.
اقرأ أكثر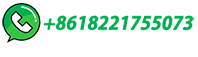
Kinetics of Direct Iron Ore Reduction with CO-H2 Gas Mixtures
is removed from the iron ore by chemical reactions based on 2 and CO from the gas-steam reformer. The reformed gas is typically 72 % H 2 and 17 % CO [4]. Most of the DRI technologies developed so far make use of CO as the major reducing gas. Reduction of iron ore pellets with CO leads to the generation of enormous amount of CO 2
اقرأ أكثر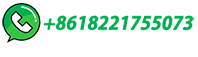
History, developments and processes of direct reduction of …
Iron ore reduction in the blast furnace for the production of liquid hot metal needs coke. The coking plant was rated in the 20th century to be the necessary evil of the blast furnace especially in former years, when the coke plants had environmental problems. Processes for iron ore reduction without the need
اقرأ أكثر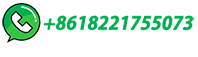
A Review on the Kinetics of Iron Ore Reduction by Hydrogen
Reduction degree as a function of time for iron ore pellet, sinter, and lump ore a t 700, 800, 900, and 1000 °C [44] "modified". Fruehan et al. found that if iron oxides are converted to ...
اقرأ أكثر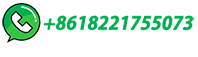
Iron ore reduction predicted by a discrete approach
The various reduction levels of iron oxide were represented by an equilibrium reaction mechanism that includes forward and backward reaction rates according to the phase diagram for iron ore reduction. The proposed treatment of reduction-oxidation reactions is capable of appropriately modelling the thermodynamics as well as the kinetics of iron ...
اقرأ أكثر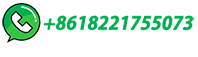
The Direct Reduction of Iron Ore with Hydrogen
The steel industry represents about 7% of the world's anthropogenic CO2 emissions due to the high use of fossil fuels. The CO2-lean direct reduction of iron ore with hydrogen is considered to offer a high potential …
اقرأ أكثر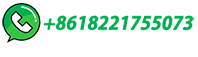
A Review on the Kinetics of Iron Ore Reduction by …
Due to its nature, the kinetics of iron ore reduction by hydrogen can be classified as gas–solid reactions. There are usually three kinetic-controlling mechanisms of diffusion through the gas film layer, diffusion through the ash layer, and the …
اقرأ أكثر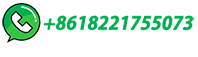
A Review on the Kinetics of Iron Ore Reduction by …
Heikkilä et al. compared the reduction behavior of iron ore pellets, sinter, and lump ore at different temperatures. The lump ore showed the lowest reduction rate at all temperatures due to its low porosity and surface area.
اقرأ أكثر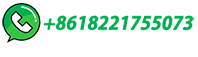