A Comprehensive Guide to the Cement Manufacturing Process
The Manufacturing Process of Cement. Now, let's explore the steps involved in the cement production process in more detail: 1. Mining and Crushing. The process of making cement begins with mining, where raw materials are extracted from quarries. Huge machines called excavators dig the limestone out of the earth.
اقرأ أكثر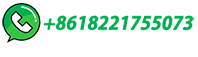
Clinkerization
The overall process of conversion from raw meal to clinker being endothermic demands a theoretical heat of about 380-420 kcal/kg-clinker. However, the rest of the specific heat consumption as tabulated above constitutes heat losses from preheater exhaust gases, clinker, cooler exhaust gases, preheater dust and radiation losses.
اقرأ أكثر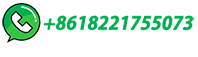
Comprehensive Guide to Cement Kilns: Processes, …
Cement kilns are an essential component of the cement manufacturing process, playing a crucial role in producing the clinker that is ground into cement. These massive, rotating cylindrical vessels are designed to withstand extreme …
اقرأ أكثر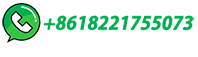
Cement Production Process | Cement Manufacturing Process | AGICO CEMENT
A full cement production process includes the cement crushing process, raw mill process, clinker process, and cement grinding process, cement packing process, and related process. Find more! Skip to content +86 . info@cement-plants. about. blog. contact. EN ES RU. Search. Menu. Menu. Home;
اقرأ أكثر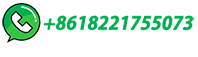
How cement and concrete are made
This results in the production of cement clinker, an intermediate product in the manufacturing process. The cement clinker emerges from the kiln, is cooled, and then finely ground to produce the powder we know as cement. The fuels …
اقرأ أكثر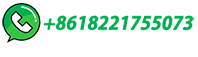
Cement Clinker: Production, Composition, Types, and …
Cement manufacturers create clinkers through a multi-step process that includes ingredient selection, heating, and grinding. Raw Mineral Preparation – The main ingredients in clinker production are limestone and clay.
اقرأ أكثر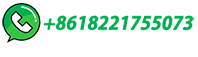
Modelling the cement process and cement clinker quality
Modelling the cement process and cement clinker quality Ho¨kfors, Eriksson and Viggh. iteration procedure continues until it reaches a mass and energy balance. The calculation blocks are placed in the process scheme with Chemapp algorithms wherever chemical equilibrium calcula-
اقرأ أكثر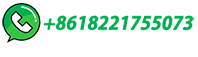
Clinkering Process in Portland Cement Manufacturing
In portland cement manufacturing, the raw materials are changed to clinker in the burning operation. Generally the rotary kiln is used for this purpose and 911 Metallurgist is a trusted resource for practical insights, solutions, and support in mineral processing engineering, helping industry professionals succeed with proven expertise ...
اقرأ أكثر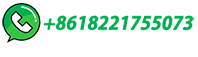
Cement and Clinker Production by Indirect Mechanosynthesis Process
With this process, we manufactured cement and clinker from industrial and laboratory raw mixes, which had to be rectified by adding kaolinite in compliance with the different cement indicators ...
اقرأ أكثر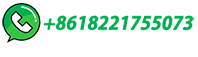
Portland Cement Clinker
The main goal of the clinkering process is to produce the material of designed phase composition, which is called Portland cement clinker. Under the action of high temperature, parallel to the clinker phases formation, underwent the process of sintering and nodulization of material in the rotary kiln.
اقرأ أكثر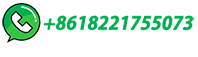
Everything you need to know about Fluxes and Mineralizers in
The production of portland cement clinker from heterogeneous mixtures of raw materials is a complex process in which one must begin with an understanding of the principles underlying the effects of temperature, chemical composition, residence time, and process variations. ... "Mineralizers and Fluxes in Clinkering Process," Cement Research ...
اقرأ أكثر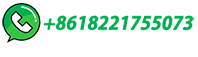
How Cement is Made
The kiln phase is the principal stage of the cement production process. Here, clinker is produced from the raw mix through a series of chemical reactions between calcium and silicon dioxide …
اقرأ أكثر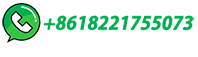
Cement Manufacturing Process: 6 StepsTo Make …
During the cement grinding process, when the clinker is ground to a fine powder with other raw materials, up to 5% gypsum or additional anhydrite is added to control the solidification time of the cement. Many factories use a …
اقرأ أكثر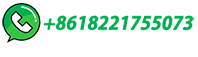
Cement Equipment For Clinker Production
Cement rotary kiln: rotary kiln is the core equipment of the clinker plant that is used for clinker burning. According to the cement manufacturing process, rotary kiln can be divided into two types, dry-process cement rotary …
اقرأ أكثر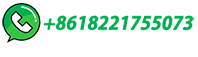
Cement vs. Clinker
Clinker, on the other hand, is the intermediate product formed during the manufacturing process of cement. It is produced by heating limestone, clay, and other materials at high temperatures in a kiln.
اقرأ أكثر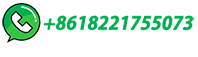
Cement Clinker Calcination in Cement Production …
The cement clinker calcination is an important step in the cement production process. It mainly occurs in cement kiln and can be roughly divided into six reaction stages, namely drying, preheating, chemical decomposition, …
اقرأ أكثر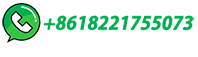
Formation and Techniques for Control of Sulfur Dioxide and …
4 Due to the interaction of raw materials and kiln gases, rotary kiln systems have inherent SO2 removal efficiencies ranging between 40-99% of the sulfur input to the system. The literature suggests that 50-70% of the remaining SO2 will be removed from exhaust gases when passed through an in-line raw mill system.
اقرأ أكثر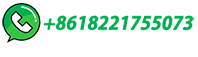
Best ways to cut carbon emissions from the cement industry …
The cement production process. Cement production is energy intensive, requiring 3.3 Gigajoules of thermal energy per ton of clinker - so another source of carbon in the industry is the way plants are powered. Instead of using carbon-intensive fossil fuels, manufacturers could use carbon-neutral biomasses.
اقرأ أكثر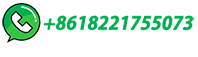
Clinkerization
The process of clinkerization signifies conversion of raw meal into clinker minerals mainly consisting of C4AF (Aluminoferite), C3A (Aluminite), C2S (Belite) and C3S (Alite) phases along with small percentage of free lime CaO, MgO, Alkalies, …
اقرأ أكثر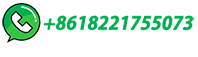
Step-by-Step Guide to the Manufacturing of Cement
Clinker Grinding: The main process in cement grinding units involves grinding the clinker into a fine powder using a cement ball mill or vertical roller mill. This step is crucial as the fineness of the cement determines the rate of hydration and, …
اقرأ أكثر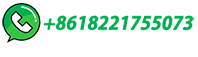
Cement Clinker Manufacturing Process with Reactions
The main raw materials (limestone, clay chalk or basalt) are quarried from natural rocks. They are crushed and transferred to pre-blending storage where other substances (such as sand, iron ore, bauxite, shale, slag, fly ash) are added to get the desired chemical composition.
اقرأ أكثر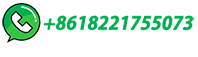
How Is Cement Made? Step-by-Step Guide
Quality control experts test the mixture to ensure it has the correct proportions of each raw material. After passing quality control, this mixture, now called raw meal, is ready to move on to the next step in the cement production …
اقرأ أكثر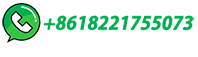
Clinker Reduction
Cement clinker is a key component of concrete, but also a major source of industrial greenhouse gas emissions. This is why substitute agents are already being used today to reduce the clinker content in cement production. Sika supports the process of substitution with its concrete and cement admixtures, while at the same time researching new solutions with a …
اقرأ أكثر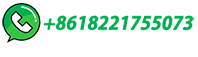
Deep decarbonisation of industry: The cement sector
Process heat overview . Clinker, and clinker substitutes, are the active components that confer cement its binding properties. Producing traditional cement clinker is an extremely energy and CO2 intensive process. In the EU, 90% of clinker is now made via the more energy efficient dry clinker-making process (2).
اقرأ أكثر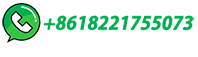
Clinker Production
Minimizing CO 2 emissions during cement and clinker production might be achieved through different strategies such as optimizing the process, reducing the clinker volume in cement, and …
اقرأ أكثر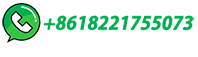
Clinker Grinding Techniques in Cement Manufacturing
Clinker is a critical component in the production of cement and forms the intermediate product during the cement manufacturing process. It can be best described as a nodular material, usually grayish in color, which is produced by sintering limestone and alumino-silicate materials such as clay at high temperatures in a cement kiln.
اقرأ أكثر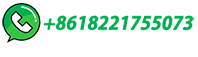
Process characteristics of clinker and cement production
New rate-based model was developed and used to validate full-scale CAP simulations for cement plants. Upcoming work: CAP optimization. CEMCAP framework document: ready for use! …
اقرأ أكثر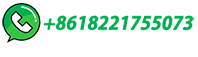
Cement Production Demystified: Step-by-Step Process and …
The production process of cement is not very complex but has many steps to be able to go from raw limestock rocks to a quality cement. The steps are the following [Britannica] : ... which can be used as a partial replacement for clinker in cement production (reduced the clinker to cement ratio). This can help to reduce the amount of energy and ...
اقرأ أكثر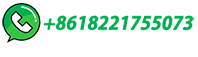
Clinker burning in the cement process of the primaries industry
The pyro-processing stage is generally known as the heart of the cement making process. It is the stage in which most of the operating costs in cement manufacturing appear and is also where most opportunities for process improvement exist. ... For the best outcome in the clinker production process, Endress+Hauser offer an integrated package ...
اقرأ أكثر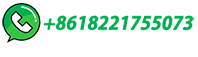
Cement Clinker Quality Control During Clinker Production Process …
In portland cement manufacturing process, the quality of cement clinker directly affects the quality of the finished product cement. The following are several important factors affecting the cement clinker quality. In the process of clinker production, strict control of these factors can ensure the production of high-quality, high-yield clinker. 1.
اقرأ أكثر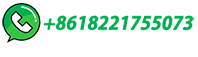