Processing of Magnetite Iron Ores–Comparing …
The iron ore beneficiation plants normally include a series stages of size reduction (in order to achieve the desired liberation degree), increasing iron ore grade (magnetic separation), and ...
اقرأ أكثر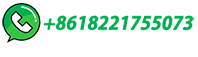
Mineral and Technological Features of Magnetite
Analysis of the current technical solutions for the processing of iron ores showed that the high-grade ores are directly exposed to metallurgical processing; by comparison, low-grade ores, depending on the mineralogical and material composition, are directed to beneficiation including gravitational, magnetic, and flotation processes or their combination. …
اقرأ أكثر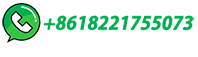
(PDF) Magnetization Roasting of Refractory Iron Ores: …
Magnetization Roasting is considered as an effective and typical method for the beneficiation of refractory iron ores. After magnetization roasting, the weakly magnetic iron minerals,...
اقرأ أكثر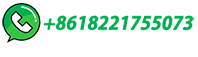
Why We Need Magnetite's High-Grade Iron Ore – and …
The Direct Reduction Process: Cleaner Steelmaking with High-Grade Magnetite. One of the most promising methods for using high-grade magnetite in green steel production is the direct reduction process. In this …
اقرأ أكثر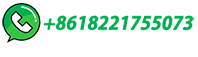
Eco-efficient and cost-effective process design for magnetite iron ore
The majority of steel production is supported by iron ore sourced from high-grade hematite deposits, although a significant fraction comes from magnetite deposits. Compared to direct shipping hematite ores mined from the upper regolith, magnetite deposits require significant beneficiation, which typically involves grinding to a particle size ...
اقرأ أكثر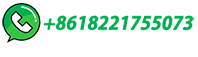
Processing of Magnetite Iron Ores–Comparing …
The iron ore beneficiation plants normally include a series stages of size reduction (in order to achieve the desired liberation degree), increasing iron ore grade (magnetic separation),...
اقرأ أكثر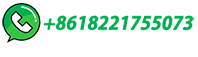
Green Magnetite Will Be the Future of Steelmaking
Approximately 7–9% of global greenhouse gas (GHG) emissions are attributable to steel production. This may be connected to the widely used practice of using a blast furnace (BF) to reduce iron ore chemically based on feeding mixed burdens of lump ore, sinter and pellets with metallurgical coke acting as a fuel, reductant and metallurgical feed.
اقرأ أكثر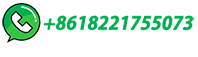
Production of magnetite nanoparticles from Ethiopian iron ore …
Crystallite size is one of the fundamental factors controlling the magnetic property of magnetic nanoparticles. In this study, magnetite nanoparticles were produced from Ethiopian iron ore and the ...
اقرأ أكثر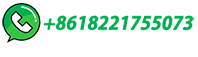
Extraction of Iron from its ores, Iron dressing, …
The ore is Hematite, chemical name is iron III oxide, the chemical formula is Fe 3 O 4, It has a blood red colour, it is more easily reduced, Iron is from 50-60 %, place of deposits is Oasis area (western desert) and western …
اقرأ أكثر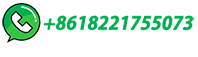
Clean iron production through direct reduction of mineral iron
A promising alternative route for cleaner production of pig iron from iron ore is the gas-based direct reduction of iron ... At temperatures of 600 K–836.7 K, mixed phases of elemental iron, carbon and magnetite (C + Fe + Fe 3 O 4) are formed, whereas at temperatures of 836.7 K–911 K, mixed phases of elemental iron, carbon and wüstite (C ...
اقرأ أكثر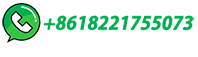
Physical separation of iron ore: magnetic separation
Based on the magnetic susceptibility values in Table 9.1, iron minerals can be divided into two groups, namely strong magnetic minerals, that is, magnetite (72.4% Fe), and weakly magnetic minerals, that is, martite (70.0% Fe), hematite (70.0% Fe), specularite (70.0% Fe), limonite (57.14–59.89% Fe), and siderite (48.2% Fe).While magnetite ores are naturally …
اقرأ أكثر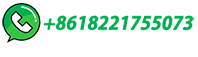
Electrolytic Reduction of Iron Oxides in Molten Salt with a
3), magnetite (Fe 3O 4) and magnetite ore concentrate from the Tapuli deposit in Pajala, Norrbotten, Sweden. The properties of the Tapuli magnetite ore and magnetite ore concentrate were analysed from a mineralogical perspective to evaluate how the raw ore material influences the concentrate and its reduction by the MSE technology.
اقرأ أكثر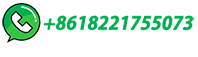
Method for preparing magnetite nanoparticles from low-grade iron ore
the method for preparing magnetite nanoparticles from low-grade iron ore of the present invention it is possible to prepare high-purity magnetite nanoparticles having a purity of 99% or higher by solvent extraction using low-grade iron ore as a starting material, and thus it is possible to reduce the processing cost and the amount of energy used, thus supplying a high-efficiency magnetite ...
اقرأ أكثر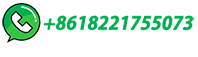
Magnetite
Importantly, magnetite is suitable for processing into iron ore pellets for use in modern steel production and currently accounts for approximately 50% of global iron ore production. The magnetic properties of magnetite enable it to be readily refined into an iron ore concentrate used as high-quality feedstock for the production of premium quality,
اقرأ أكثر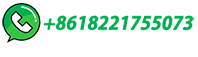
Synthesis of magnetite nanoparticles from iron ore tailings using a
The separation technology provides for production of iron ore concentrate with total iron content of 65.9% and recovers 91.0% of magnetite and 80.5% of hematite from the tailings containing 20.4% ...
اقرأ أكثر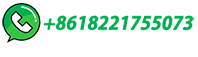
The Efficient Improvement of Original Magnetite in Iron Ore
Magnetization roasting followed by magnetic separation is considered an effective method for recovering iron minerals. As hematite and magnetite are the main concomitant constituents in iron ores, the separation index after the magnetization roasting will be more optimized than with only hematite. In this research, the mechanism of the original magnetite …
اقرأ أكثر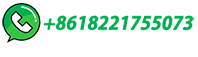
Iron Production
The production of iron from its ore involves a redox reaction carried out in a blast furnace. The furnace is filled at the top with the iron ore oxide most commonly hematite ((Fe_2O_3)) but …
اقرأ أكثر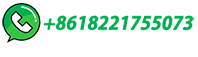
Iron Ore | Essential Raw Material for Steel and Industrial …
- Iron ore, especially hematite and magnetite, contains 50-70% Fe, providing an efficient source of metallic iron for steel production. ... there is a shift towards more sustainable mining practices and the development of more energy-efficient steel production methods. Iron ore mining companies are increasingly adopting technologies that ...
اقرأ أكثر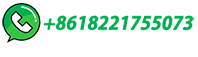
Iron (Fe) Ore | Minerals, Occurrence » Geology Science
Description and properties of common iron ore minerals. Iron ore minerals are rocks or minerals that contain iron in concentrations high enough to be economically extracted. Common iron ore minerals include: Hematite …
اقرأ أكثر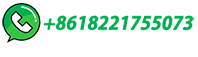
Preparation of high-purity magnetite from iron ore concentrate
Magnetic separation, flotation, and alkali leaching were conducted in the process. The concentrate's Fe grade increased from 65.56% to 72.30% following beneficiation. High …
اقرأ أكثر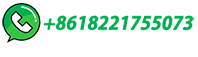
Iron ore: Mineralogy, processing and environmental sustainability
Generally, wet magnetic separation methods are used to produce iron ore concentrate with iron content higher than 65% for use in pelletizing plants and then in steelmaking processes by direct ...
اقرأ أكثر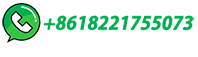
Magnetization Roasting of Low/Lean-Grade Iron ore Resources
Iron ores are naturally occurring, non-renewable, limited, and are vital raw materials for iron and steel-making companies. In China and India, production has expanded significantly in recent years and is predicted to touch 2600 million tonnes (MT) or more in 2030. Approximately 650 million tonnes of scrap per annum (MTPA) can be recycled to meet the iron …
اقرأ أكثر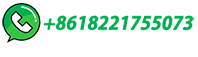
Recovery of magnetite-hematite concentrate from iron ore tailings
The separation technology provides for production of iron ore concentrate with total iron content of 65.9% and recovers 91.0% of magnetite and 80.5% of hematite from the tailings containing 20.4% ...
اقرأ أكثر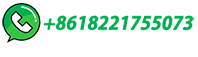
Production of Pig Iron from Magnetite Ore–Coal Composite …
To obtain pig iron from iron ore there are two main reac- tions; one is reduction by carbon and the other carburiza- tion. Both of them are endothermic reactions and therefore to make pig iron …
اقرأ أكثر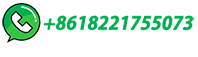
Iron processing | Definition, History, Steps, Uses,
Although the Romans built furnaces with a pit into which slag could be run off, little change in iron-making methods occurred until medieval times. By the 15th century, many bloomeries used low shaft furnaces with water power to drive …
اقرأ أكثر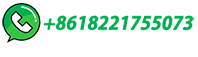
Iron Ore: Extraction Methods, Types & Locations
Pig iron cannot be produced without iron ore and the latter is a major component in the production of steel. 98% of the mined iron ore is used in the steel production; it reveals how crucial steel is in the contemporary world. How Many Types of Iron Ore? Iron ores are classified based on their metallic iron content. They are of the following types.
اقرأ أكثر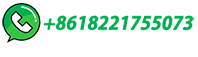
Iron Ore Pelletization: A Critical Review of Processes and
Iron ore pelletization is a critical aspect of the steel manufacturing process, providing a method to utilize fine iron ore particles and beneficiate lower grade ores, which enhances the overall output and efficiency of steel production processes. Pelletization involves converting iron ore fines into compact pellets, which are then used in blast furnaces or direct …
اقرأ أكثر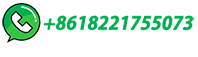
Recovery of magnetite-hematite concentrate from iron ore …
The separation technology provides for production of iron ore concentrate with total iron content of 65.9% and recovers 91.0% of magnetite and 80.5% of hematite from the tailings containing …
اقرأ أكثر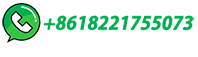
Mechanism of magnetite iron ore concentrate morphology …
Iron ore pellets are one of the significant sources of iron for iron and steel making due to their superior metallurgical performance, low energy consumption, and less emission of environmentally harmful dust and gases during the production process [1], [2], [3].The two primary raw materials for pellet production are hematite and magnetite concentrates.
اقرأ أكثر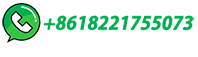