Iron Ore Processing, General
Iron ore handling, which may account for 20–50% of the total delivered cost of raw materials, covers the processes of transportation, storage, feeding, and washing of the ore en route to or during its various stages of treatment in the mill.. Since the physical state of iron ores in situ may range from friable, or even sandy materials, to monolithic deposits with hardness of …
اقرأ أكثر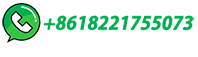
Solved 1. Average size distribution of an iron ore after
Question: 1. Average size distribution of an iron ore after in-pit primary crushing is given below. This ore is to be further crushed at a circuit throughput of 3Mtpy to a size of −30 mm with <10% oversize and <10%−1 mm. There would be two final products: lump (−30+10 mm) and fines (−10 mm). Average W1 of the ore is 14.25kwh/ metric tonne.
اقرأ أكثر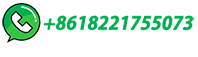
Flow chart extraction of iron crusher
Overview of Iron Extraction Process. Before diving into the flow chart, it's important to understand the broad stages of iron extraction: Mining: Iron ore is extracted from the ground using open-pit or underground mining techniques.; Crushing and Screening: After extraction, the raw iron ore undergoes size reduction through crushing and is screened for further processing.
اقرأ أكثر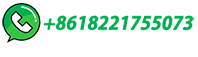
Iron Ore: From Mining to Processing to Dust Control
Iron ore is a rock or mineral from which metallic iron can be extracted economically. It constitutes 5% of the earth's crust. Viable forms of ore contain between 25% and 60% iron. Ore greater than 60% iron is known as natural ore or direct shipping ore, meaning it can be fed directly into iron-making blast furnaces. ...
اقرأ أكثر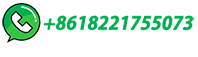
Beneficiation of Iron Ore
Beneficiation of Iron Ore and the treatment of magnetic iron taconites, stage grinding and wet magnetic separation is standard practice.This also applies to iron ores of the non-magnetic type which after a reducing roast are amenable to magnetic separation. All such plants are large tonnage operations treating up to 50,000 tons per day and ultimately requiring …
اقرأ أكثر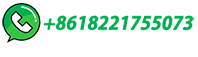
Iron Ore Processing: From Extraction to Manufacturing
Crushing is the initial stage in the iron ore processing journey, where large chunks of ore are broken down into smaller fragments. The primary objective of crushing is to reduce the ore size for subsequent processing and …
اقرأ أكثر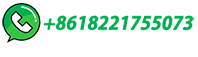
The six main steps of iron ore processing
Ball Mill and Crusher for Iron Ore in Mineral Processing
This article explores the functions, differences, and applications of ball mills and crusher in the iron ore industry. Crusher for Iron Ore Purpose and Functionality. A crusher is the first step in iron ore processing. It reduces large …
اقرأ أكثر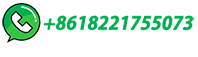
[FREE] If a quantity of iron ore undergoes a crushing process, the
For instance, if you have a 100g piece of iron ore containing 30g of iron and 70g of other materials, crushing it to a smaller size doesn't change the 30g of iron, but if you crush it well, and it now weighs 50g as a result of removing some non-iron material, the percentage of iron becomes 60% (30g iron out of 50g total), which is an increase from the original 30%.
اقرأ أكثر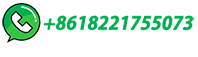
Iron Ore Mine Primary Crushing Plant Construction
Iron Ore Mine Primary Crushing Plant Construction. Welcome to our blog on the construction of iron ore mine primary crushing plants! If you're in the mining industry, you know that a reliable and efficient crushing plant is essential for breaking down large pieces of raw material into smaller, more manageable sizes.
اقرأ أكثر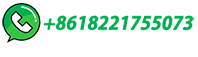
Crushing Iron Ore royalty-free images
Find Crushing Iron Ore stock images in HD and millions of other royalty-free stock photos, illustrations and vectors in the Shutterstock collection. Thousands of new, high-quality pictures added every day.
اقرأ أكثر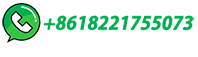
Crushing mechanism analysis of sintered ore and study of …
To improve the crushing effect and reduce the range of particle size distribution after crushing, the crushing mechanism and the particle size distribution pattern after crushing of sintered ore under different roller rotation speeds are analysed in this paper. Based on the discrete element method, the microscopic parameters of sintered ore are calibrated and …
اقرأ أكثر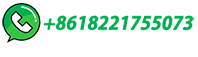
Introduction: Overview of the global iron ore industry
Turning to iron ore exports and imports, the tonnages are summarized in Table 1.1 for 2012 and 2018 (Australian Department of Industry, Science, Energy and Resources, 2021; US Geological Survey, 2020; United National Conference on Trade and Development (UNCTAD), 2021).As shown in Fig. 1.3, China is the largest iron ore importing country and imported about …
اقرأ أكثر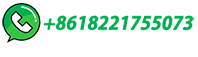
Crushing and separation of the ore of iron
After crushing, the ore undergoes a process called beneficiation, which aims to separate the valuable iron minerals from the gangue minerals. One commonly used method …
اقرأ أكثر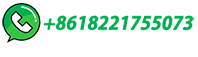
Development of high-strength ceramsite via sintering of iron ore
Over the years, various applications for IOTs have been explored. For instance, B. B. Das produced coarse aggregates based on fly ash (FA) by incorporating iron ore tailings (IOTs) into the FA precursor as an additional component in the mix [7].Lucas Augusto de Castro Bastos investigated the use of iron tailings as paving materials [8].Ranjeet Kumar Singh explored the …
اقرأ أكثر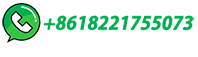
Research into the crushing and grinding processes of iron ore …
Iron ore is generally transported using a traditional method that releases significant amounts of dust into the environment. In contrast, the pipeline transportation of slurry is noticeably a ...
اقرأ أكثر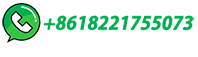
Iron Mining Process
The iron ore is separated from the taconite using magnetism. The remaining rock is waste material and is dumped into tailings basins. The taconite powder with the iron in it is called concentrate. Pellets The concentrate (the wet taconite powder) is rolled with clay inside large rotating cylinders. The cylinders cause the powder to roll into ...
اقرأ أكثر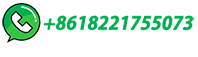
Iron Ore Processing, General
The iron ore processing industry produces usable concentrations of iron-bearing material by removing nonferrous rock (gangue) from low-grade ore. In the United States, predominant iron ore is taconite which is a hard, banded, low-grade ore. Ninety-nine percent of the crude iron ore produced in the United States is taconite.
اقرأ أكثر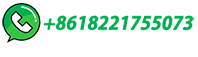
Iron ore mining and dressing
Iron ore processing. After the iron ore has been prepared by crushing and grinding during ore extraction, the ore is actually processed. The aim of this is to reduce the undesirable high proportion of admixtures to a desired minimum in order to increase the iron content. This is done by processes such as flotation or magnetic separation ...
اقرأ أكثر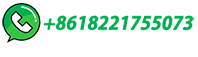
Crushing mechanism analysis of sintered ore and study of …
To improve the crushing effect and reduce the range of particle size distribution after crushing, the crushing mechanism and the particle size distribution pattern after crushing of sintered ore under different roller rotation speeds are analysed in this paper.
اقرأ أكثر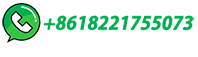
Iron Ore Processing: From Extraction to Manufacturing
The final stage in iron ore processing is ironmaking, where the iron ore is transformed into molten iron through a process called reduction. The most common method of ironmaking is the blast furnace route. In a blast furnace, …
اقرأ أكثر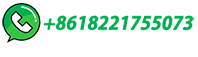
Top 6 Steps Of Iron Ore Processing
Before being crushed, the iron ore must first be broken up to an F 80 grind size. The crushed ore is then sent to a stockpile after being crushed.
اقرأ أكثر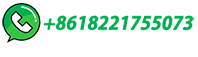
iron ore after crushinh
Jig machine: processing 30 (2)~0.5mm coarse iron ore; Shaking table: separating 2~0.037mm fine iron ore particles; Spiral chute: processing 0.1-0.37mm iron ore with low mud content. 4. Iron ore dewatering equipment. The iron ore mine dewatering operation divides into two parts: concentrate mine dewatering and tailings mine …
اقرأ أكثر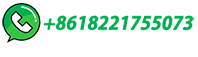
What Is Involved in the Processing of Iron Ore?
After use of some form of crushing equipment, the processing of iron ore will usually involve grinding. Different types of grinding equipment produce everything from a fine dust to small …
اقرأ أكثر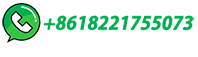
Beneficiation of Iron Ores
Fig 3 Types of processing ores. The wet processing (Fig 4) is normally practiced for low / medium grade (60 % Fe to 63 % Fe) hematite iron ore. The wet process consists of multi-stage crushing followed by different stages of washing in the form of scrubbing and / or screening, and classification etc., but the advantage is only partial removal of adhered alumina and free …
اقرأ أكثر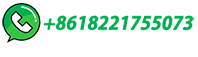
The main stages of the ore crushing process
Iron ore; Tin ore; Copper ore; Polymetallic ore; Gold; Articles; 1. EN +7 (707) 754-17-53. EN. 1. Products. ARP-1C. Advantages; Comparison; ARP-2C; For industries. Ore analysis; Pulp analysis; ... to dmax - the size of the largest pieces after crushing. i = Dmax/dmax. In turn, the crushing process is divided into stages of crushing in a ...
اقرأ أكثر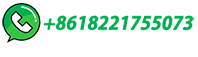
Iron Ore Agglomeration Technologies
Five iron ore agglomeration technologies can be defined: briquetting, nodulization, extrusion, pelletization and sintering. Sintering and pelletization are the most important agglomeration technologies, in this way, in the EU-27, 14 countries operate 34 iron ore sinter plants with 63 iron ore sinter strands, producing in the first decade of the ...
اقرأ أكثر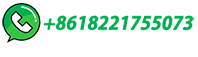
Iron ore analysis
Iron ore. Iron is the fourth most abundant element in the Earth's crust, but economic concentrations are dominated by comparatively rare iron oxide forms; magnetite (Fe 3 O 4), hematite (Fe 2 O 3), goethite (FeOH), limonite …
اقرأ أكثر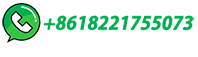
Common Iron Ore Crushing and Screening Process
When dealing with argillaceous iron ore with high water content, or when restricted by terrain conditions, a three-stage open-circuit crushing and rod mill crushing process is sometimes used. That is to relax the particle size of the finely crushed product to 25~30mm, and add a rod mill for fine crushing, which is equivalent to a four-stage ...
اقرأ أكثر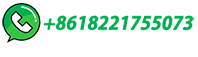
Iron ore mining and dressing
After the iron ore has been prepared by crushing and grinding during ore extraction, the ore is actually processed. The aim of this is to reduce the undesirable high proportion of admixtures to a desired minimum in order to …
اقرأ أكثر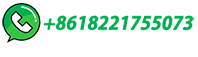
Iron Ore Processing Solution
The first stage: crushing & screening – three stage closed-circuit crushing Large pieces of iron ore are uniformly sent to the jaw crusher or coarse crushing mobile station by the vibrating feeder for coarse crushing; the coarsely crushed iron ore is screened by the vibrating screen and sent to the single-cylinder hydraulic cone crusher for processing Medium crushing: The iron ore material ...
اقرأ أكثر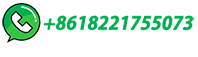