Mastering Ore Recovery: Crushing in Mineral Processing
Crushing in mineral processing is the first step that involves breaking of the large ore materials into smaller sizes by crushing machinery. This process is important because big …
اقرأ أكثر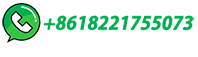
Crushed Iron Ore
Crushed Iron Ore is created by crushing Iron Ore in one of three different crafting stations. The crafting stations come with different ratios, labor cost and time cost. The two lover crafting stations also have a byproduct of …
اقرأ أكثر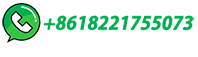
SIZE REDUCTION BY CRUSHING METHODS By
Ore, Copper Ore, Zinc Ore and Manganese Ore. 4.1 The art of crushing: Crushing means different things for different operations and the production goals are not always
اقرأ أكثر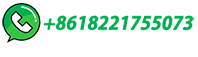
Mechanical characteristics of roll crushing of ore materials based …
The application of high-pressure grinding rolls (HPGR) for ore crushing is considered to be one of the effective ways to save energy and reduce emissions in the ore …
اقرأ أكثر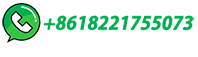
Evaluating the performance of an industrial-scale high pressure
The sorting of bulk ore can discard barren waste before comminution (Li et al., 2018), and dry/wet pre-concentration technologies (Yuan et al., 2021) such as magnetic, electrical, and gravity separation can reject barren rocks before grinding, resulting in additional energy and cost savings (Bamber, 2008).
اقرأ أكثر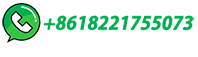
Predicting TFe content and sorting iron ores from hyperspectral …
These objects typically fall within a size range of approximately 20 mm–40 mm. Drawing from these studies, this study mainly focused on sorting small, crushed iron ore with particle sizes ranging from 20 mm to 40 mm. Ensuring that the subsequent test and train samples consisted of iron ore with both low and high TFe content can make the ...
اقرأ أكثر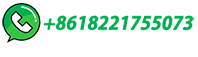
Crusher types and technology in different industries
The crushed material can be recycled for use as aggregate in new construction projects. Aggregate Export. ... These early rock crushing machines were powered by steam engines and were primarily used in mining and ore processing applications. The industrial revolution and advancements in engineering during the 19th century played a significant ...
اقرأ أكثر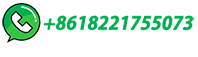
Crushed Ores
Crushed Ores are obtained from crushing various items. If making a Precision Mechanism fails, there is a small chance to receive Crushed Gold Ore, thus making it renewable. 0.4: Removed Crushed Brass Removed Crushed Ore …
اقرأ أكثر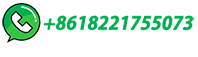
Simulation and optimization of gyratory crusher performance …
Finally, the height of the crushed particle distribution area is enlarged after optimization, shown in Fig. 11 (d), H b ≈ 0.55H f, which means that the effective crushing distance of the ore particles in the crushing chamber is increased, so that the ore particles are better crushed. Furthermore, it can be easily seen that the area of the red ...
اقرأ أكثر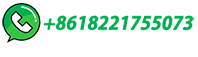
Review on comprehensive utilization of nickel laterite ore
(a) Reaction mechanism of natural gas and laterite nickel ore(He et al., 2024); (b) SEM–EDS Map of nickel laterite ore reduction roasting under optimal reduction conditions(He et al., 2024); (c) XRD patterns of HL oxide ore roasted at 1200 °C (A with NaCl; B without NaCl)(Zhou et al., 2016); (d) SEM images of HL oxide ore with NaCl roasted ...
اقرأ أكثر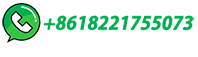
Evaluation of the performance of iron ore waste as potential …
As can be seen in Fig. 8, all the samples met the cohesion test requirement but samples containing iron ore residue have a higher 30 min cohesion value and therefore a constant setting rate than of crushed aggregate. In this result, the lower angularity of iron ore residue than crushed aggregate provides strength by the aggregate interlock.
اقرأ أكثر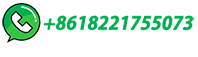
8 Factors That Affect Production Efficiency of Crushers
The hardness of the ore is expressed by the compressive strength of the ore or the Platts hardness coefficient (The compressive strength divided by 100 is called the Platts hardness coefficient). In the process of ore beneficiation, obviously the harder the ore, the greater its compressive strength, so the more difficult …
اقرأ أكثر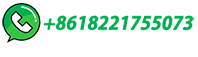
Factors Affecting the Performance of Crushing Plant …
Figure 2. Cause-and-effect diagram over factors affecting plant performance Figure 4 shows the variation in the total amount of ore crushed for the year 2012.
اقرأ أكثر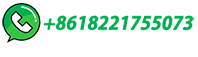
Navigating Chrome Ore Grades and Qualities: South Africa vs
Explore the differences in chrome ore grades from South Africa's Bushveld Complex and Zimbabwe's Great Dyke. Learn about lumpy, ROM, and concentrate, and why Oreways Mining seeks specific chrome qualities for its ferrochrome production. ... It can be directly crushed and sized before being shipped to smelters. ROM ore, on the other hand, is a ...
اقرأ أكثر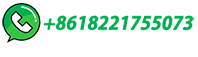
Iron ore pellets for blast furnace
What is iron ore pellet. Iron ore pellets are made by adding a small amount of additives to the fine ore powder (-200 mesh, that is, the ore powder with a particle size of less than 0.074mm accounts for more than 80%, and the …
اقرأ أكثر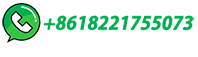
Crushing in Mineral Processing
In mineral processing or metallurgy, the first stage of comminution is crushing. Depending of the type of rock (geometallurgy) to be crushed, there are 2 largely different …
اقرأ أكثر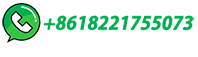
Simulating the Impact of Ore Competence Variability on Process
The Extended Drop Weight Test (ExDWT) improves understanding concerning sources of variation in ore competence through the value chain. This technique measures and describes the variability in ore ...
اقرأ أكثر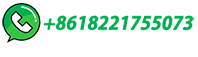
Crushed ore agglomeration and its control for heap leach operations
Crushed ore agglomerates can take two forms: fine particles adhering to coarse particles and fine particles adhering to each other. ... profiles that develop from a particular agglomeration practice are the key parameters which determine the metallurgical performance of an ore. The agglomerate quality tests, stacking test, air and hydraulic ...
اقرأ أكثر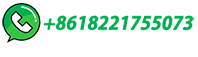
Ore Grinding
In the mineral processing industry, ore grinding is the particle size preparation before the separation of the crushed ore. Except those that process some placers, almost all mineral processing plants have grinding operations, in which materials are crushed by the impact and abrasive action of grinding medium (steel rod, steel ball, gravel, or ...
اقرأ أكثر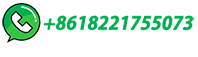
Evaluation of the performance of iron ore waste as potential …
Apaza et al. (2021) investigated the utilization of iron ore residue for micro-surfacing cold asphalt mix and compared its performances with conventional mix. Test results showed that the designed micro-surfacing mix with iron ore waste can meet the requirements for use and the maximum content can reach 20% of total aggregates.
اقرأ أكثر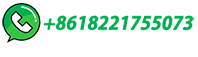
Metallurgical Performance of Ageing Crushed Ore
caved Cu-porphyry ore on metallurgical performance. The impact of oxidation was measured through chemical analyses and flotation tests on the weathered ore. EXPERIMENTAL. A Cu-porphyry ore sample, crushed to passing 10 mesh (1.2mm), was split into ten 7-kg test charges, Figure 1 Ageing column schematic. fifteen 2-kg test charges, and a ...
اقرأ أكثر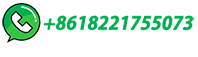
ORE SEPARATION BY SCREENING By
For example, if a sample of a crushed mineral ore ... The grizzlies can be vibrated to improve performance. 7.2 Revolving Screen (Trommel):
اقرأ أكثر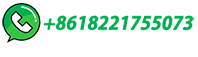
Crushing in Mineral Processing
In mineral processing or metallurgy, the first stage of comminution is crushing.. Depending of the type of rock (geometallurgy) to be crushed, there are 2 largely different techniques at your disposition for crushing rocks. In principle, compression crushing is used on hard and abrasive rocks by placing them between a high wear-resistant plate/surface.
اقرأ أكثر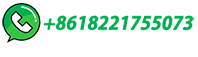
Comparison on micromechanical properties of interfacial transition …
Using recycling iron ore tailings (IOTs) from industrial solid waste as concrete aggregates agrees with the sustainable development of the construction industry and carbon neutrality commitment. As the interfacial transition zone (ITZ) between IOTs and cement paste is significant to concrete performance but rarely studied, the present work is focused on the …
اقرأ أكثر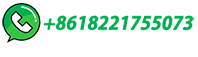
(PDF) ORE SEPARATION BY CLASSIFICATION
Since feature space reduction can result in optimistic esti-mates of classifier performance, the statistical significance of these scores were estimated by computing the empirical distribution of ...
اقرأ أكثر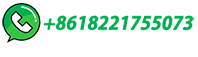
The six main steps of iron ore processing
Screening and diverting fine particles significantly increases the performance of the crusher. 2. Crushing and stock piling This step involves breaking up the iron ore to obtain an F 80 grind size before it can be ground. Once the ore has been crushed, it is diverted to a stockpile. The aim of this step is to ensure a smooth crushing process ...
اقرأ أكثر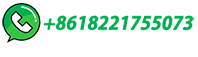
(PDF) ORE SEPARATION BY SCREENING
This goal can be a crushed product with certain size and shape or maximum recovery of metals out of a complex ore. Most value minerals (both metallic and industrial) are priced by their purity.
اقرأ أكثر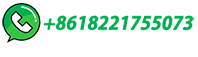
FIELD MONITORING AND PERFORMANCE EVALUATION …
Crushing plants are of great interest in reducing particle size of rocks and ores as milling operations need to consider sustainable development. Since the crushing plants operate …
اقرأ أكثر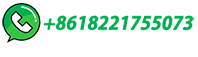
Effect of moisture content on the flowability of crushed ores
original classification proposed by Jenike [2], and it can be seen that this particular ore is easy-flowing if handled at 1% moisture and for instantaneous flow conditions but becomes cohesive at higher moisture levels. Fig. 5. Instantaneous flow function of a particular crushed copper ore (fines minus 1/4") tested at four moisture levels.
اقرأ أكثر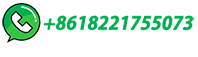
crushed ore cannot be used in crucible or blast furnace #465
Crushed versions of ore are completely unable to be placed in the crucible, and when using any crushed Iron ore in a blast furnace, the furnace accepts the input but does not melt it into pig iron infinitely heating and using fuel. Steps to Reproduce. Use crushed ore in either the crucible or blast furnace. Additional Information
اقرأ أكثر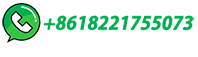