Recovery of Ultra-Fine Iron Ore from Iron Ore Tailings
Journal of Chemistry. Washing of iron ore fines and slime (10% and 25% w/v, slurry concentrations) with two types of surface-active agents (sodium humate (synthesized) and AD 200 (commercial)) at varying concentrations at pH 8 was conducted for ascertaining the efficacy of dispersants in beneficiating the low-grade iron ores.
اقرأ أكثر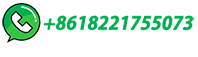
Sequential soil washing techniques using hydrochloric acid and …
In this study, sequential washing techniques using single or dual agents (NaOH and hydrochloric acid) were applied for arsenic-contaminated soils in an abandoned iron-ore mine area. Arsenic-containing iron-ore fines in this area can produce mobile colloids through coagulation and flocculation in natural waters contacting the soils (Pandey et al ...
اقرأ أكثر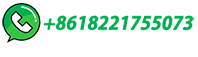
Fine Particle Processing Of Iron Ore Slimes From Wash Plant
constraints spurred the iron ore washing plants to recover the values from their slimy tail pond. The paper enumerates the developments in ecofriendly processing of iron ore slimes by state of art vertical pulsating wet high intensity high gradient magnetic separation. The wash plant tails assayed 46.45%Fe, 18.03%SiO 2, 5.25% Al 2 O
اقرأ أكثر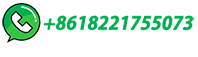
Modeling and Optimisation of Spiral Concentrator for …
At present, iron ore of around +64% Fe is used for production of iron through blast furnace and direct reduction (IBM 2019). To produce +64% Fe from low- and medium-grade ores, crushing and washing are compulsory. During washing of iron ore, to improve the quality of lumps and fines, iron ore slimes are generated.
اقرأ أكثر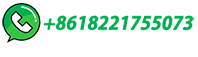
Overview of Ore Washing in the Mineral Processing Industry
Ore washing can prevent the muddy material in the mud-containing mineral raw materials from blocking the crushing and screening equipment. If the raw materials contain soluble useful or harmful components, they should also be washed. The difficulty of washing and removing the sludge from the ore is expressed by the wa…
اقرأ أكثر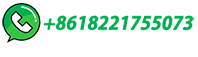
Recovering Iron from Iron Ore Tailings and Preparing Concrete
Iron ore tailings (IOTs) are a form of solid waste produced during the beneficiation process of iron ore concentrate. In this paper, iron recovery from IOTs was studied at different points during a process involving pre-concentration followed by direct reduction and magnetic separation. Then, slag-tailing concrete composite admixtures were prepared from high-silica …
اقرأ أكثر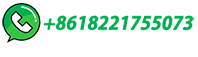
Mark the wrong staement among the following. The iron ore after washing
The iron ore after washing is roasted with a little coasl in excess of air. During roasting A. Moistuyre is removed B. As and S are removed in the form of their volatile oxides C. Any ferrous oide is oxidised to ferric oxide. D. The mass becomes compact and thus makes it sutiable for ready reduction to metallic iron.
اقرأ أكثر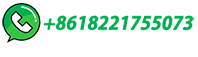
A Review on Removal of Iron Impurities from Quartz Mineral
Iron is one of the most stubborn impurities in quartz minerals, and the iron content partly determines the various applications of quartz. Iron can exist in quartz in the forms of iron minerals, fluid inclusions, and lattice impurities. The removal of iron and the consequent purification of quartz minerals are the key processes to obtaining high-quality quartz. Iron …
اقرأ أكثر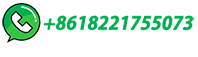
Froth Flotation of Iron Ores
With the depleting reserves of high-grade iron ore in the world, froth flotation has become increasingly important to process intermediate- and low-grade iron ore in an attempt to meet the rapidly growing demand on the international market. In over half a century's practice in the iron ore industry, froth flotation has been established as an efficient method to remove …
اقرأ أكثر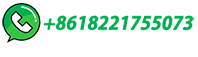
Full article: Preparation and characterisation of environmental
The particle size distribution of iron ore tailings and sludge is listed in Table 2. The maximum size of the 90 wt.% iron ore tailing and 90 wt.% sludge powder are 35.6 μm and 278.4 μm, respectively. The mass percentage of the iron ore tailing and sludge powder with the size of less than 100 μm is 99.9% and 54.8%, respectively.
اقرأ أكثر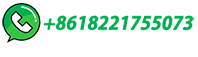
Removal of Silicon, Aluminum and Phosphorus Impurities …
In this paper, the removal processes for silicon (Si), aluminum (Al) and phosphorus (P) impurities from low-grade iron ore, in which hematite (Fe2O3), goethite (FeO(OH)), and quartz (SiO2) are the main mineral constituents, have been presented.
اقرأ أكثر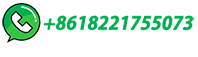
Extent of gangue removal of iron ores treated with the …
In this paper, the removal processes for silicon (Si), aluminum (Al) and phosphorus (P) impurities from low-grade iron ore, in which hematite (Fe2O3), goethite (FeO (OH)), and quartz (SiO2)...
اقرأ أكثر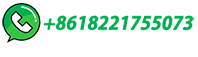
An environment-friendly strategy for comprehensive recovery of Li, Al
Finally, the yield of each element is shown in Fig. 7 c. Compared with the initial content of Li, Fe, Al and Si in the raw ore, the recovery rates of Li, Fe, Al and Si are 78.40 %, 78.60 %, 74.07 % and 89.71 %, respectively, the content analysis of alumina, Al 2 (Al 2.8 Si 1.2)O 9.6 (mullite), lithium phosphate and iron oxide can be seen in ...
اقرأ أكثر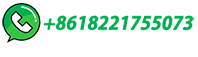
Optimization of an Iron Ore Washing Plant
Closing down of iron ore mines due to environmental constraints spurred the captive iron ore washing plants to workon a custom plant mode and also recover the values from their slimy tails. ... Policy Framework & Sustainable Development for Mining of Mineral and Fossil Energy Resources. 112 S.J.G. Krishna et al. / Procedia Earth and Planetary ...
اقرأ أكثر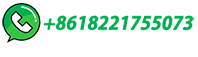
Sustainable iron recovery from iron ore tailings using hydrogen …
The iron and steel industry is a key pillar of both the Chinese and global economies. Steel production relies heavily on iron ore, yet China, a leading steel producer, faces challenges with its domestic iron ore due to low grade, fine particle size, and high impurities [1], [2].This results in low resource utilization and a heavy reliance on imports.
اقرأ أكثر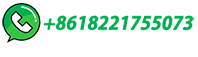
Prospecting, Mining anti Washing the Brown Iron Ores of Alabama
AN increased demand for brown iron ore in the Birmingham district during the past 18 months has caused renewed activity both in prospecting and mining these ores. In recent years the …
اقرأ أكثر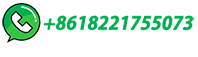
Improving recovery of iron using column flotation of iron ore slimes
The tailing samples used were collected from tailing pond of iron ore washing plant of Kiriburu mines, India. XRD: hematite, goethite and quartz and kaolinite The sample contains 58.24% Fe, with 4.72% SiO 2, 3.47% Al 2 O 3, and had 5.18% LOI. The beneficiation of iron ore tailings by selective flocculation was studied.
اقرأ أكثر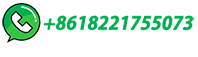
Sulfur Removal and Iron Recovery from High-Pressure Acid
High-pressure acid leach (HPAL) residue from laterite nickel ore is a potentially valuable resource for ironmaking; however, its efficient utilization is hindered by its high sulfur content. In this study, an effective and straightforward method is proposed for sulfur removal from HPAL residue. The process involves sieving and sodium carbonate leaching, enabling …
اقرأ أكثر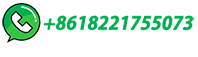
Simplified hydrometallurgical route for the synthesis of silica-free
For instance, magnetic concentration and flotation processes have been combined to promote iron ore enrichment of iron ore and reduce the silica content as much as possible. Such practices have become increasingly complex and do not contribute to reducing the volume of waste (Gyllenram et al., 2022, Muslemani et al., 2021, Sparrow et al., 2022).
اقرأ أكثر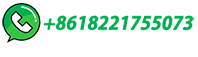
Emission characteristics of dioxins during iron ore Co-sintering …
The main function and advantages of the sintering process are as follows: 1) preparation of fine iron ore powder or fine ore powder into bulk materials with certain strength, 2) removal of volatile components and harmful impurities from raw materials, 3) adjustment of the chemical composition and improve the metallurgical properties of raw materials, 4) expansion …
اقرأ أكثر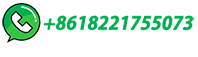
Ore Washing
Wash in Mining Sense •Remove material from surface of ore. •Assumes readily liberated particles of ore with loosely agglomerated gangue •Distinction from separation; Screens, trommels, …
اقرأ أكثر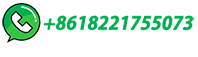
Removal of Silicon, Aluminum and Phosphorus Impurities
In this study, a combination of alkali roasting and hydrothermal treatment is used as a method of gangue (Si, Al, and P) removal from iron ores as a means to upgrade low-grade iron ore (limonite ...
اقرأ أكثر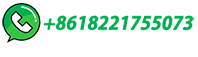
Overview of Ore Washing in the Mineral Processing Industry
④Water Power Ore Washing Screen. The ore washing method that uses water guns to wash on a fixed bar screen is used for easy-to-wash ore. In addition, pay attention to the sludge left from ore washing. Sometimes these sludges also contain tailings of high grade. In view of the current mineral resource situation, they may have good extraction ...
اقرأ أكثر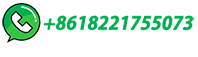
Classifying iron ore with water or dust adhesion combining …
As for water, factors such as rainfall and ore washing during the transition from iron ore extraction to processing may also lead to water adhering to the surface of the iron ore (Furtado et al., 2023, Higuchi et al., 2018, Jing et al., 2023, Pan et al., 2022, Pinto et al., 2021, Sadeghi et al., 2014, Yousefi et al., 2020), which may also ...
اقرأ أكثر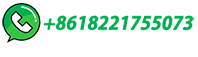
Iron Ore Processing
Resource Recovery and Recycling from Metallurgical Wastes. S. Ramachandra Rao, in Waste Management Series, 2006 9.8 Production of Ceramic Tiles from Iron Ore Tailings. Current practice of washing iron ore before it is processed for extractive metallurgical operation results in three products, coarse ore lumps with sizes in the range 10-80 mm, which are directly charged …
اقرأ أكثر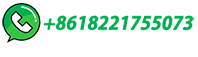
Recovery of iron minerals from Indian iron ore slimes using …
Recovery of iron values from the Barsua iron ore slimes containing 56% Fe, 4.8% SiO 2, 7.2% Al 2 O 3 and 7.0% LOI by the addition of synthetic colloidal magnetite and oleate colloidal coating followed by high gradient magnetic separation technique was investigated. The effects of concentration of colloidal magnetite, pH, and magnetic field strength were studied.
اقرأ أكثر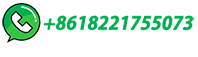
Optimization of an Iron Ore Washing Plant
Closing down of iron ore mines due to environmental constraints spurred the captive iron ore washing plants to workon a custom plant mode and also recover the values from their …
اقرأ أكثر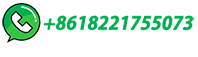
Optimization of an Iron Ore Washing Plant
Closing down of iron ore mines due to environmental constraints spurred the captive iron ore washing plants to workon a custom plant mode and also recover the values from their slimy tails.
اقرأ أكثر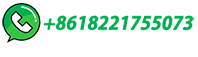
Existing and New Processes for Beneficiation of Indian Iron ores
Most of the iron ore washing plants of India use scrubber and screw classifier for the separation of coarse and fines. Besides that, for classifier fines, hydrocyclones are used for concentration by separating coarse material as most of the gangue constituents are found accumulated in the finer sizes. ... 25.6% SiO 2 and 2.30% Al 2 O 3. The ore ...
اقرأ أكثر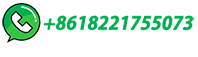
(PDF) An overview of the beneficiation of iron ores via reverse
Prasad et al. (1988) have studied iron ore slimes processed by magnetic separation at the Kiriburu mines in India. A c oncentrate containing 63% Fe and 3.3% Al 2 O 3 with an iron recovery of
اقرأ أكثر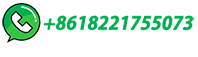