Use of Iron Ore Pellets in Blast Furnace Burden – IspatGuru
BF burden, blast furnace, Hot metal, Iron ore, iron ore pellets, sinter, Use of Iron Ore Pellets in Blast Furnace Burden Pelletizing is a process that involves mixing very finely ground particles of iron ore fines of size less than 200 mesh with additives like bentonite and then shaping them into oval/spherical lumps of 8-20 mm in diameter by a ...
اقرأ أكثر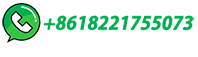
A new insight into iron ore oxidized pellets prepared by steel belt
Iron ore oxidized pellet is a superior furnace burden for the blast furnace process, possessing high iron grades, good strength, and excellent metallurgical properties [].Additionally, compared to the sintering process, the energy consumption of the pelletizing process is approximately 50% lower, with emissions of pollutants such as SO 2, NO x, and particulate …
اقرأ أكثر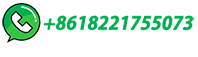
Plasma heated furnace for iron ore pellet induration
PLASMA HEATED FURNACE FOR IRON ORE PELLET INDURATION In the present pelletizing apparatus, the induration of iron ore concentrate pellets is achieved in a tunnel furnace heated by plasma torches, wherein the generation of C02 by the conventional iron ore pelletizing processes is reduced by using electricity powered plasma torches instead of burning natural gas, heavy …
اقرأ أكثر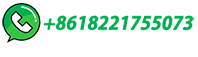
Life cycle energy consumption and greenhouse gas emissions of iron
The iron and steel production is a lengthy and comprehensive process, which includes iron ore processing, coking, sintering, pelletizing, blast furnace (BF) iron making, basic oxygen furnace (BOF) steelmaking, electric arc furnace (EAF) steelmaking, casting, rolling and etc., (Cavaliere, 2016, Ghosh and Chatterjee, 2008).
اقرأ أكثر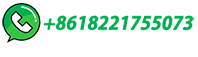
Pelletizing
Iron ore pelletizing are made in two steps: Step 1: the Iron concentrate to be pelleted must have a sufficiently fine particle –size distribution (65-85 % less than 0.045 mm) ... Shaft furnace; For more information please contact us. Logout ...
اقرأ أكثر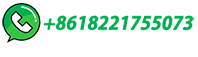
Iron Ore Pelletizing
Iron Ore Pelletizing. As one of the main components of ironmaking equipment such as blast furnaces, iron ore pellets affect the efficiency of these processes. Having a uniform size range …
اقرأ أكثر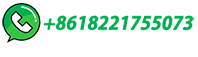
Iron Ore Agglomeration Technologies
Until the 1950s of the last century, the oxidized iron ores that were loaded into the blast furnace had granulometries within 10 and 120 mm. However, the depletion of high-grade iron ore sources has made necessary the utilization of concentration processes with the purpose of enriching the iron ore. Because of these processes, a fine granulometry is produced, and thus …
اقرأ أكثر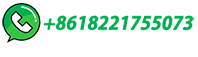
Agglomeration of Iron Ores
Agglomeration of iron ores is the iron ore pretreatment process in which the powdery iron ore that cannot be directly fed into a blast furnace experiences high-temperature solidification by sintering process and pelletizing process or low-temperature solidification by pelletizing process and briquetting process to generate the rich ore material that meets the …
اقرأ أكثر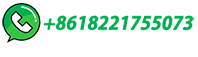
Optimization of Pellet Plant Straight Grate Induration Furnace …
Indian iron ores are suffering from high amounts of alumina and loss on ignition (LOI), which are deleterious constituents in both the pelletizing as well as iron making processes. Iron ore fines utilized in pellet making consist of alumina in the range of 3.20–3.35% and LOI in the range of 3.50–3.70%. Detailed palletization studies have been carried out on high alumina …
اقرأ أكثر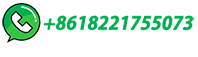
Converting iron ore into iron pellets
Converting iron ore into pellets is an important process that is carried out to prepare iron ore for use in blast furnaces.:Methods of converting iron ore into pellets ... 6- Fluidized bed pelletizing: In this method, iron ore particles are placed in a fluidized bed and pelletizing is carried out under the influence of air or gas flow ...
اقرأ أكثر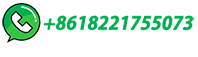
Modern air pollution control for iron ore induration
The iron ore induration or pelletizing process emits particulates, sulfur dioxides (SOx), nitrogen oxides (NOx) and other pollutants depending on trace elements in the orebody and fuel. Typical emission levels for these compounds during induration will be outlined, and corresponding options for pollution control equipment described. Recent pellet plant …
اقرأ أكثر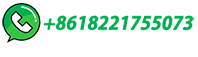
Grate kiln pelletizing plant
Iron ore pelletizing; Feed to blast furnace or DRI plant; Process description. Traveling grate. The traveling grate is comprised of a blanket of plates connected into a chain that carries the pellets similar to a conveyor. The difference is that the plates in the grate chain have holes in them that allows air to pass through it.
اقرأ أكثر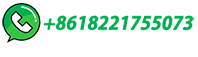
THE POTENTIAL OF PELLETIZING FOR IRON ORE …
THE POTENTIAL OF PELLETIZING FOR IRON ORE PROCESSING The technology of pelletizing iron ore has been used for decades. The basic principles are the same, but there ... furnace converter route was still evident. However, the latest efforts to reduce global CO2 emissions show a trend reversal. From 2017 to 2018 alone, global DRI production
اقرأ أكثر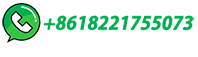
(PDF) Advances in Iron Ore Pelletizing Binders
The iron ore pelletizing process consists of three main steps: 1. Pelletizing feed preparation and mixing: the raw material (iron ore concentrate, additives -anthracite, dolomite-and binders are prepared in terms of particle size and …
اقرأ أكثر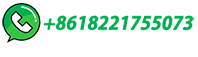
Hazard Identification, Risk Assessment, and Control …
furnaces.[1] The present production capacity of pelletization in ... aim of the study was to identify all the possible hazards at different workplaces of an iron ore pelletizing industry, to ...
اقرأ أكثر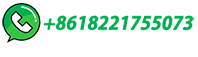
Iron ore pelletization
The ratio in the output from the three main pelletizing technologies changes depending on practical circumstances, such as iron ore reserves, iron ore types, market demand, and required investment. The ratio for grate-kiln pellets has increased to 55.33% in 2011 from 7.21% in 2000, while the ratio for shaft furnace pellets has dropped to 42.05% ...
اقرأ أكثر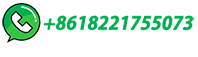
Iron ore pelletizing
Our iron ore pelletizing systems combine the best features of both technologies to provide the most modern plant and to produce pellets at the lowest cost and highest quality. Pellet plants sized from 1.2MTPA to 9MTPA; Engineering and …
اقرأ أكثر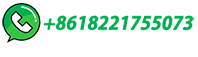
(PDF) Iron ore pelletization
A brief introduction to recent developments in iron ore pelletizing is provided in this chapter, including the world output of fired pellets, pellet production processes, preparation of pellet ...
اقرأ أكثر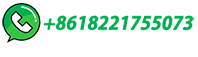
Sintering: A Step Between Mining Iron Ore and Steelmaking
The remaining 2% of domestic iron ore was produced for non-steel end uses. Seven open-pit iron ore mines (each with associated concentration and pelletizing plants), and three iron metallic plants—one direct-reduced iron (DRI) plant and two hot-briquetted iron (HBI) plants— operated during the year to supply steelmaking raw materials.
اقرأ أكثر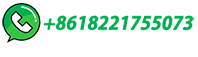
Iron ore pelletization
The ratio in the output from the three main pelletizing technologies changes depending on practical circumstances, such as iron ore reserves, iron ore types, market demand, required investment, etc. The ratio for GK pellets has increased to 77.0% in 2018 from 7.0% in 2000, while the ratio for shaft furnace pellets has dropped to 14.9% in 2018 ...
اقرأ أكثر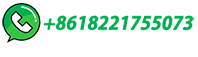
Iron Ore Pelletizing Essential in Meeting Future Steel Needs
As the world leader in tumble growth agglomeration, FEECO provides a variety of services and equipment for iron ore pelletizer plants. As the needs of the steel industry change, one production component looks to be increasingly important in meeting the needs of the modern steel industry: iron ore pelletizing. Iron ore pelletizing, or balling, is the process of transforming fines into …
اقرأ أكثر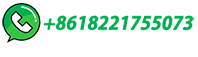
What is Shaft Furnace Iron Ore Pelletizing Technology? How It …
Iron Ore Pelletization Shaft Furnace System ... The future of shaft furnace technology in the iron ore pelletizing industry will likely involve a niche role where it remains viable for specific situations—particularly where low costs are prioritized and the feedstock is primarily magnetite. Despite its limitations, shaft furnace technology ...
اقرأ أكثر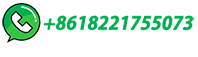
(PDF) IRON ORE PELLETIZING PROCESS
PDF | Iron Ore, Iron Ore Pellets, Direct Reduced Iron )DRI( Pellets, Iron Ore Pellets Market, Pelletizing Process, Sintering, Binder, Induration... | Find, read and cite all the research you need ...
اقرأ أكثر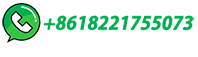
Iron Ore Pelletizing Essential in Meeting Future Steel …
Iron ore pelletizing, or balling, is the process of transforming fines into spherical granules anywhere from 8 – 16mm in size via tumble-growth (agitation) agglomeration using either a disc pelletizer (pan granulator) or rotary drum.
اقرأ أكثر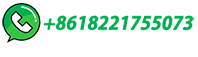
What is Iron Ore Pelletizing? How It Worked? An In-depth Look at …
Iron ore pelletizing is an essential industrial process that transforms powdery iron ore into uniform, robust pellets, serving as a premium feedstock for blast furnaces and direct reduction reactors. This process has witnessed significant advancements since its inception, primarily driven by the escalating requirements of the steel industry, which demands higher …
اقرأ أكثر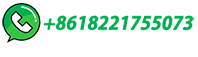
The Iron Pelletizing Process
The iron pelletizing process is often associated with low grade iron ore following a range of liberation techniques to prepare and make suitable for the blast furnace. In summary, pelletizing is achieved by combining the iron ore with water and a …
اقرأ أكثر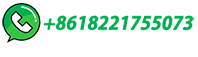
Iron Ore Agglomeration Technologies
Regarding pelletizing technologies, it is possible to mention two that are used at industrial scale: rotary drum and rotary disc. The rotary drum is a large drum-shaped cylinder that is ... Rotary Heating Furnace pellets, or iron ore-coal composite pellets. This kind of pellets does not require high strength as in the other two types, since in ...
اقرأ أكثر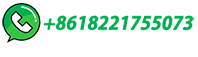
Iron Ore Processing
Iron Ore Processing for the Blast Furnace (Courtesy of the National Steel Pellet Company) ... and ready for the pelletizing process. Pelletizing A pellet plant contains a series of balling drums where the iron ore concentrate is formed into soft pellets, in much the same manner that one rolls a snowball, to make a pellet about ...
اقرأ أكثر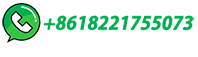
Iron Ore Pelletizing
Iron Ore Pelletizing. As one of the main components of ironmaking equipment such as blast furnaces, iron ore pellets affect the efficiency of these processes. Having a uniform size range and open pores iron ore pellets has a lot of advantages like a high mechanical strength resulting in good transporting possibilities or a good permeability.
اقرأ أكثر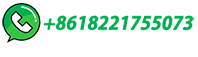
Iron Ore Pelletizing Process: An Overview
In the blast furnace, iron is reduced and melted and the most common product is liquid iron called hot metal. In direct reduction, iron remains in solid state and the product is the so-called direct …
اقرأ أكثر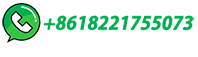